Rebuilding Hope: How Modular Housing Restored Lives in the Aftermath of the Lahaina Wildfires
In the early hours of August 8, 2023, a brush fire near Lahaina, Hawaii, sparked under the dry, volatile conditions of Hawaii’s peak fire season.
Fueled by severe drought and high winds from Hurricane Dora’s distant passage, the fire rapidly spread across Maui, catching residents off guard. Within hours, Lahaina—a historic coastal town home to over 12,000 people—was overwhelmed.
Downed power lines severed communications, road closures blocked escape routes, and depleted water systems left firefighters with insufficient resources to battle the blaze. By the next day, much of Lahaina had been reduced to ashes. Nearly 12,000 residents were displaced, 102 lives were lost, and more than 2,200 homes were destroyed, compounding the island’s existing housing challenges. Amidst the devastation stood the charred but resilient 150-year-old Banyan Tree, a poignant symbol of hope for the community.
In response to this unprecedented disaster—one of the deadliest fires in modern U.S. history—state and federal governments launched a coordinated recovery effort. Part of that effort involved a coalition of MBI members who worked together with the state of Hawaii to create over 100 permanent modular houses for displaced residents of Lahaina. Remarkably, these modular homes were built, barged to Maui, and set within weeks of the project kickoff, again proving the speed and efficiency of modular construction.
Learn how modular construction benefitted the residents of Lahaina—and how the industry can help respond to future disasters—in this detailed case study.
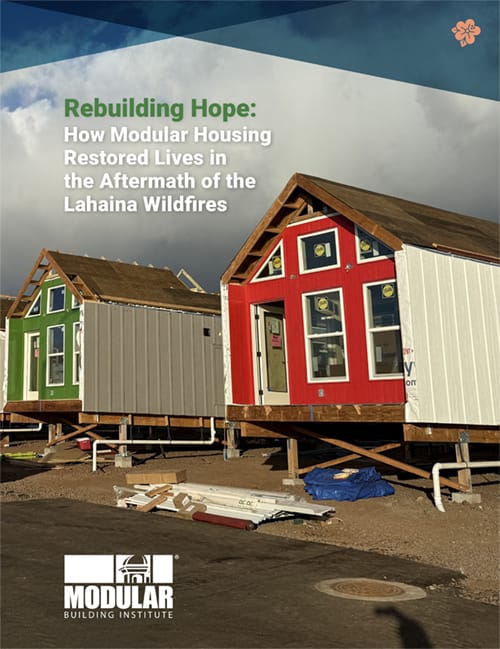
“They didn’t understand modular construction," said Jon Hannah-Spacagna, MBI's Director of Government Affairs, "so I began working with them to provide the basics—explaining that modular construction is built to the same building codes as site-built structures, its capabilities, and how to write a modular-specific Request for Proposal.”
Understanding the Stafford Act
The Robert T. Stafford Disaster Relief and Emergency Assistance Act, which was enacted in 1988 to provide federal assistance for disasters. The act enables financial and physical assistance, coordinates government-wide relief efforts, and allows federal agencies to provide disaster aid. However, the Stafford Act also includes a clause that enables states like Hawaii to decline traditional HUD trailers in favor of alternative housing solutions.
“The Hawaiian people not only wanted housing that was long-lasting, but they also wanted housing that looks like it belongs on the island and fits the environment," said Hannah-Spacagna. "These homes will be fixtures on the island for years to come, unlike in the continental U.S., where temporary housing can be easily removed after serving its purpose.”
From Factory to Maui: A Modular Housing Solution
Fading West and Guerdon were two of three contractors to build modular homes for Lahaina’s recovery. Together, they built over 100 units. These included one-bedroom, two-bedroom, and three-bedroom homes, ranging from 490 to 980 square feet, all built on temporary foundations for future relocation.
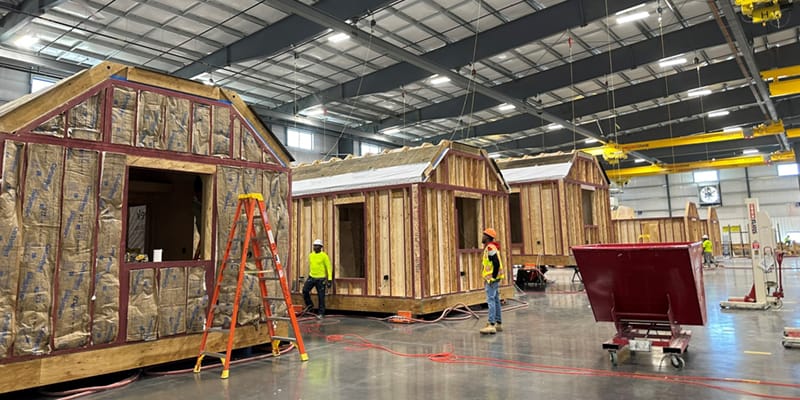
“Our factory is 110,000 square feet, set up like a Toyota lean car factory with two workstations,” explained Eric Schaefer, Chief Business Development Officer of Fading West. “Twenty houses are in the factory at any given time at different levels of completion, moving to a new station every four hours. It takes about seven or eight days to finish a house.”
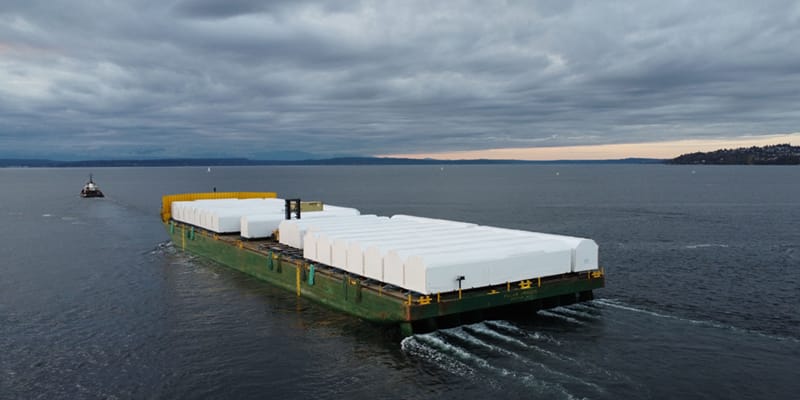
“Materials arrived at the factory, and within 14 calendar days, we had units on a barge headed to Maui,” said Tommy Rakes, CEO of Guerdon.“It was an incredible pace.”
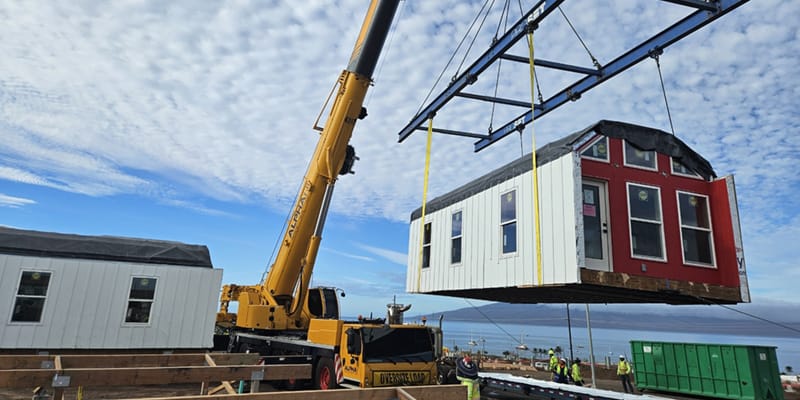
“In a lot of ways, this project is a great example of the extreme benefits of modular construction because of the pre-existing conditions before the fires,” . explained Scott Bridger, Principal at ProSet Modular.“The nature of the acute [housing needs] in Lahaina was just begging for modular in a lot of ways.”
The Case for Modular as a Long-Term Housing Solution
Hawaii’s unique geographic challenges as an island underscore the need for innovative solutions, but the larger question remains: Why not apply this approach everywhere? Hannah-Spacagna elaborates, “If a modular home could be built for the same cost or less than a HUD trailer—$180,000—you could have a structure built to the regular building codes of the area. That makes it suitable for long-term use, addressing both the affordable housing crisis and homelessness. Maui is the perfect example to show that this is possible.”
Schaefer echoed this, urging decision-makers to consider the financial and functional advantages of modular housing over traditional disaster relief options. “If a project like this costs $200 million, but the purchased housing is only going to last for three years before they’re thrown out—you do the math, right?” he said. “But, if the housing is well-built and to an international code with the same level of quality as a stick-built home, it could be repurposed and even sold after it has filled a community’s need post-disaster, allowing [the government] to make its money back.”
“If FEMA had a library of pre-approved modular plans, we could start production within 7 to 10 days of a natural disaster,” said Rakes. “These homes could be shipped anywhere in the continental U.S. in 3 to 5 days, installed, and occupied within a day. In under three weeks, displaced victims could have permanent homes.”
By embracing modular construction as both a short-term and long-term solution, Lahaina’s recovery provides a transformative blueprint for disaster relief and housing innovation. It’s a model that not only responds to crises but also proactively addresses the larger issue of housing affordability—a challenge that communities across the country and around the world continue to face.
Download the Complete Disaster Recovery & Rebuilding Case Study
Overall, this project proved that when innovation, efficiency, and empathy come together, the impossible becomes achievable. Lahaina’s recovery serves as a beacon for how modular housing can redefine what it means to rebuild—not just with speed, but with purpose.
To learn more about this project, the roles and contributions of its stakeholders, and the possibilities of modular construction to help with future disaster recovery and rebuilding efforts, download the complete case study below.
Explore More Modular Building Case Studies
Parkhurst Elementary School Classroom Additions
The Parkhurst Elementary School in Winchester, MA, has recently undergone an expansion of 13,074 square feet. Due to renovations at the neighboring Lynch School, students were temporarily relocated to Parkhurst. Modular construction was chosen as the preferred method to accommodate the influx of students and prepare for the start of the 2023-2024 school year.
VBC Chooses MAESTRO SMART 9 HP
Volumetric Building Companies (VBC), a global leader in the construction sector with a focus on building the future through volumetric modular techniques, choose the Maestro Smart 9 Heat Pump as their ideal comfort solution to heat and cool their modular housing project in Philadelphia, PA, consisting of 60 modular housing units.
16’ x 37’ Welded Substation Enclosure
Instead of sourcing a new transformer, which would have taken over 100 weeks and cost several million dollars, Raytheon Technologies turned to Panel Built Inc. for a modular solution. Panel Built designed a 16’ x 37’ prefabricated enclosure that could be delivered to Guam in two pieces. Once it was put together, it was lowered over the transformer.
Temporary Visitors Center at Antietam National Battlefield Park
Antietam National Battlefield Park, a revered site listed on the U.S. National Register of Historic Places, presented unique challenges demanding meticulous preservation efforts. The paramount goal was to ensure minimal disruption to the sacred grounds surrounding the new modular building.
Wraptite Airtightness Protection for Northampton School for Boys
The Wraptite external air barrier system from the A. Proctor Group has been chosen for its high-performance, airtight insulation for a Department for Education (DfE) funded project of the offsite construction of Northampton School for Boys Multi-Academy Trust.
University Temporary Modular Student Housing— Ettrick, VA
Modular Genius, Inc. designed and built three temporary modular dormitory complexes featuring 134 dorm rooms, totaling 49,632 sq. ft. All three modular dorms feature a shared laundry room, kitchen and lounge area, showers, and restrooms for residents.
Hage’s Badehotel — Case Study — Denmark
For this project, Forta PRO delivered 72 buildings, 144 modules, with 5,200 m2 of gross modular area. With final onsite completion in June 2023, it provides exceptional long-stay accommodation in a stunning and serene environment.
355 Sango Court Case Study
The logic-intensive preconstruction method demanded of automated modular brought extra benefits to the Sango Court project. Autovol had worked side by side with preconstruction innovator Prefab Logic to create a digital twin modeling approach and a sprint process as advanced as the Autovol factory.
Enhancing Building Performance with Wraptite
The Wraptite external air barrier system from A. Proctor Group was installed in combination with the innovative, unique pre-panelized and fully load-bearing Hadley Frame offsite system, which is ideal for developments of low to medium rise structures.