Modular Bathroom Case Study: Holiday Inn, Dublin Airport
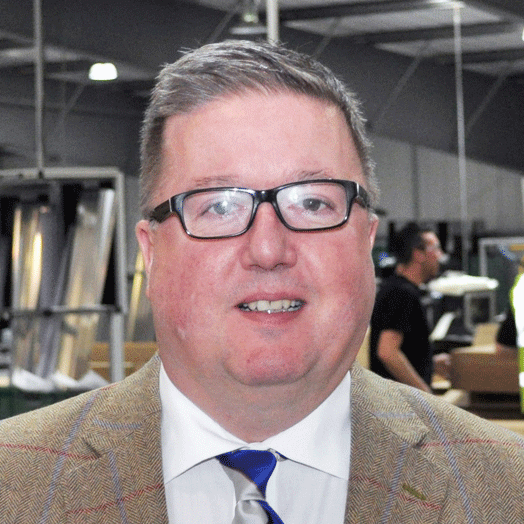
David Osborne is the CEO of Roman Showers Ltd, the largest shower enclosure manufacturer in the UK and Europe, based in the north east of England. Roman has developed specialist capabilities to manufacture anti-slip solid surface shower pans and to fabricate solid surface vanity tops which integrate with the showering space. Roman exports around the world to 63 countries currently and is constantly developing systems for modular manufacturers and international hotel groups.
Roman, Europe and the UK’s largest shower enclosure designer and manufacturer, offers designer showering solutions for the bathroom within the hospitality and residential markets; are firmly embedded with key international hotel groups, architects and designers worldwide; and currently operate in over 60 international markets. All products are made in Britain on a 400,000 square feet manufacturing operation in County Durham. Roman is a capability driven manufacturer with all design in-house; an enclosure factory; a solid surface moulding facility; and a Corian fabrication plant.
Overview
As the leading company who designs and manufactures numerous elements of the bathroom which are all designed from the ground up to integrate together, Roman were contracted by Irish bathroom pod manufacturer, Castle Modular, to supply shower enclosures, anti-slip solid surface shower trays and integrated Corian vanity units for the prestigious IHG Dublin Airport Holiday Inn.
The project involved the supply of 400 bathroom pods by Castle Modular to the main contractor Stewart Construction. The ability to source from an accredited IHG manufacturer who had the skill sets to bring these items together with the necessary CE Marking accreditations, declarations of performance and industry leading service backed guarantees was fundamental to the
purchasing decision.
Product Specification
All products supplied adhered to IHG’s Holiday Inn brand standards. Roman liaise closely with the IHG Group to develop concepts together across a number of their brands.
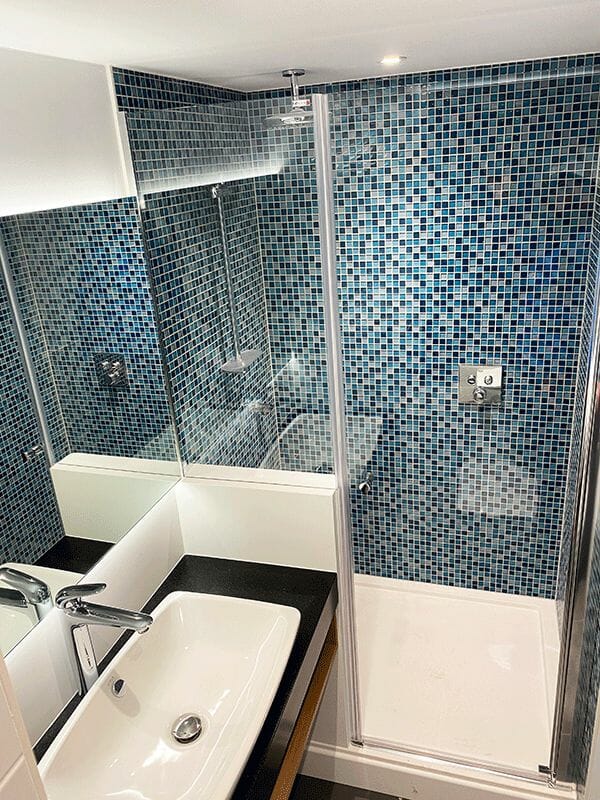
An inside look at Roman's newly-installed modular bathroom pods at under-construction IHG Dublin Airport Holiday Inn.
Related Listening:
The Evolution and Future of Modular Showers w/ Roman Ltd.
In this episode, David Osborne, CEO of UK-based Roman Ltd., speaks about the growth of the international modular shower industry, how modular showers themselves have evolved, and the trends that will define the industry over the next few years.
The unique Holiday Inn design involved the fabrication of a nib wall which integrated with the tray and vanity unit. The bespoke glass panel affixed to the wall allowed for a bright, fresh, open looking enclosure when combined with the frameless toughened glass pivot door.
The design brief also called for a bottle shelf to be included which was seamlessly formed onto the solid surface wall.
Integral to the design was the modular way in which all items were constructed to create a water tight contemporary shower enclosure for the guest to safely enjoy. Critically the products are also easy to clean and maintain. Roman designed and developed a unique leg riser kit for the shower tray with six robust adjustable feet to allow for ease of levelling which also offered a rigid platform on which to stand.
Due to the nature of bathroom pod construction methods, sufficient space was allowed beneath the shower tray to accommodate the drain and waste pipe. For ongoing maintenance, a solid surface facial plate was fixed to the front of the tray to enable quick and easy access to the fast flow waste.
In line with IHG Brand standards, Roman manufactured a solid surface shower tray in a matte white finish which has a DIN Class C anti-slip rating. This unique material cannot wear and offers a stunning permanent anti-slip surface.
Result
Working in tandem with Castle Modular’s construction, design and commercial teams, 400 stunning bathroom pods were supplied on time and on budget in what will be one of IHG’s largest new-build hotels in Europe.
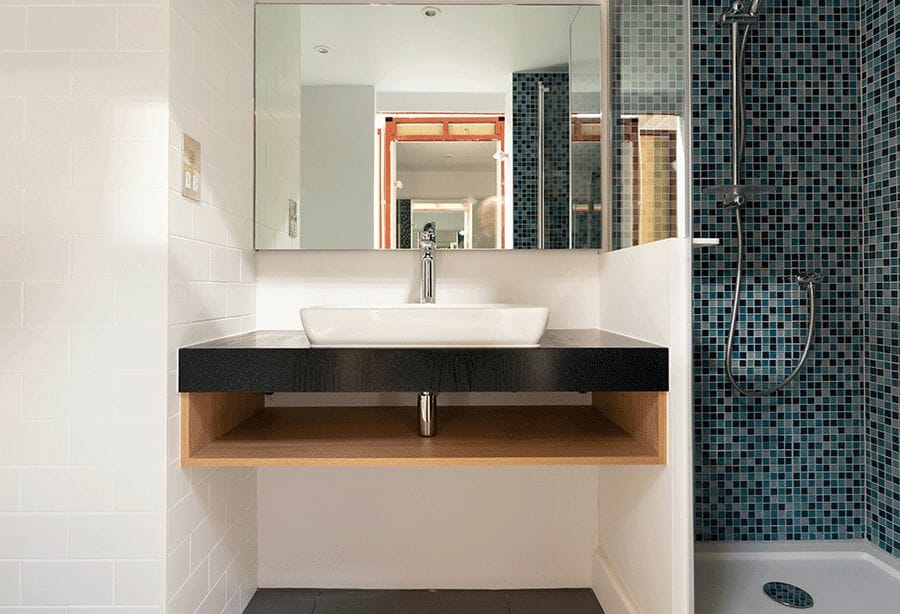
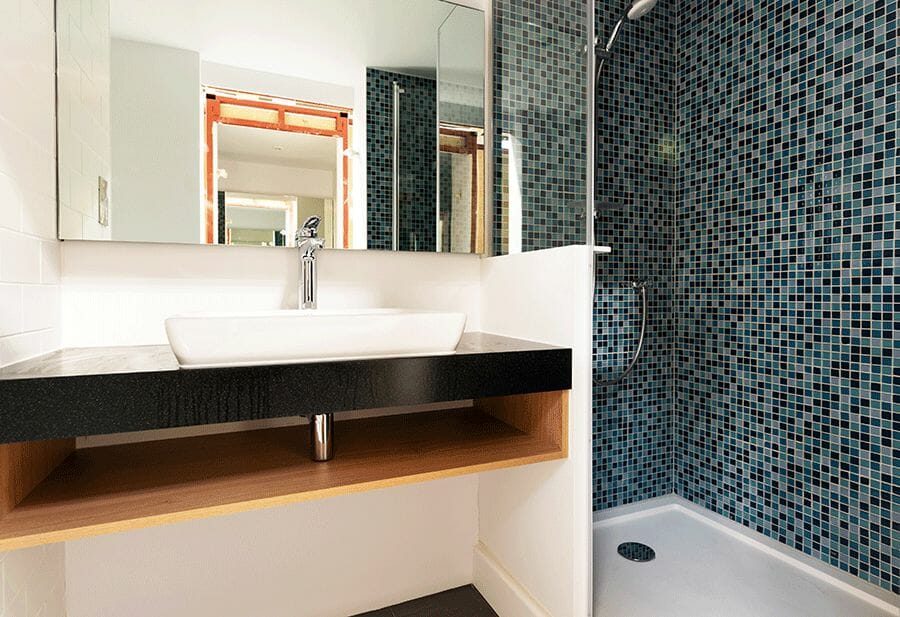
More from Modular Advantage
Oregon’s Prevailing Wage Proposal: A Wake-Up Call for Modular Construction
In early February, 2024, the Massachusetts Board of Building Regulations and Standards (BBRS) released its proposed 10th Edition building codes. This draft included several amendments targeting modular construction that would have created an extremely difficult environment for the entire modular industry and could have eliminated the industry entirely in the state.
Behind the Design of Bethany Senior Terraces, NYC’s First Modular Passive House Senior Housing Project
As more developers seek to meet new regulations for energy efficiency, the team at Murray Engineering has set a new record. With the Bethany Senior Terraces project, Murray Engineering has helped to develop NYC’s first modular structure that fully encompasses passive house principles — introducing a new era of energy efficiency in the energy-conscious city that never sleeps.
How LAMOD is Using Modular to Address Inefficiency, Sustainability, and the Future of Construction
As developers, designers, and contractors seek to understand the evolving needs of the modular industry, no one is as well-versed in the benefits of going modular as Mārcis Kreičmanis. As the co-founder and CBDO of LAMOD in Riga, Latvia, Mārcis has made it his ultimate goal to address the inefficiencies of traditional construction.
From Furniture Builder to ‘Activist Architect’: Stuart Emmons’ Unique Journey
Stuart Emmons was fascinated by buildings at a young age. He remembers building sand cities with his brother during trips to the Jersey shore. His father gave him his first drawing table at the age of ten. Today, he is an experienced architect who received his FAIA in June 2025. The road he took is unique, to say the least.
Forge Craft Architecture + Design: Codes, Contracts, and Intellectual Property
Founding Principal and Director of Modular Practice for Forge Craft Architecture + Design, Rommel Sulit, discusses the implications of codes, contracts, and intellectual property on
modular construction.
Eisa Lee, the “Bilingual” Architect
Now as the founder of XL
Architecture and Modular Design in Ontario, Canada, she applies not just her education as a traditional architect but an entire holistic view on modular design. It’s this expansive view that guides her work on being a true partner that bridges the gap between architects and modular factories as they collaborate on the design process.
Tamarack Grove Engineering: Designing for the Modular Sector
The role of a structural engineer is crucial to the success of a modular project, from initial analysis to construction administration. Tamarack Grove offers structural engineering services — project analysis, plan creation, design creation, and construction administration — for commercial, manufacturing, facilities, public services, and modular. Modular is only one market sector the company serves but it is an increasingly popular one.
Engineer Masters the Art of Listening to His Customers
Since founding Modular Structural Consultants, LLC. in 2014, Yurianto has established a steady following of modular and container-based construction clients, primarily manufacturers. His services often include providing engineering calculations, reviewing drawings, and engineering certification
Inside College Road: Engineering the Modules of One of the World’s Tallest Modular Buildings
College Road is a groundbreaking modular residential development in East Croydon, South London by offsite developer and contractor, Tide, its modular company Vision Volumetric (VV), and engineered by MJH Structural Engineers.
Design for Flow: The Overlooked Power of DfMA in Modular Construction
Unlocking higher throughput, lower costs, and fewer redesigns by aligning Lean production flow with design for manufacturing and assembly.