DORÇE Navigates Mountainous Terrain, Dangerous Weather to Help Rebuild Türkiye
DORÇE Prefabricated and Construction has been around for over 40 years, focusing on bringing modular constructions to the world at large. The company has worked tirelessly to design and manufacture over hundreds of projects in 60 countries. But all the experience in the world could not match the company’s sudden need for manufacturing speed, as they rushed to fabricate over 40,000 modules in the wake of the 2023 7.8-magnitude and 7.5-magnitude earthquakes that hit Eastern Türkiye.
The February 6 earthquakes in 2023 were enormous, killing thousands of people and wiping out a large number of cities, leaving many citizens without homes. As a result, DORÇE moved quickly, obtaining a government bid to help create housing and multipurpose structures—both temporary and permanent—for earthquake victims and laborers hired for reconstruction efforts.
In a matter of days, DORÇE’s manufacturing facilities in Ankara worked around the clock to build these 22 square meter modules and 90 square meter light gauge steel (LGS) houses to deliver across mountainous regions and areas that were still emerging from the destruction.
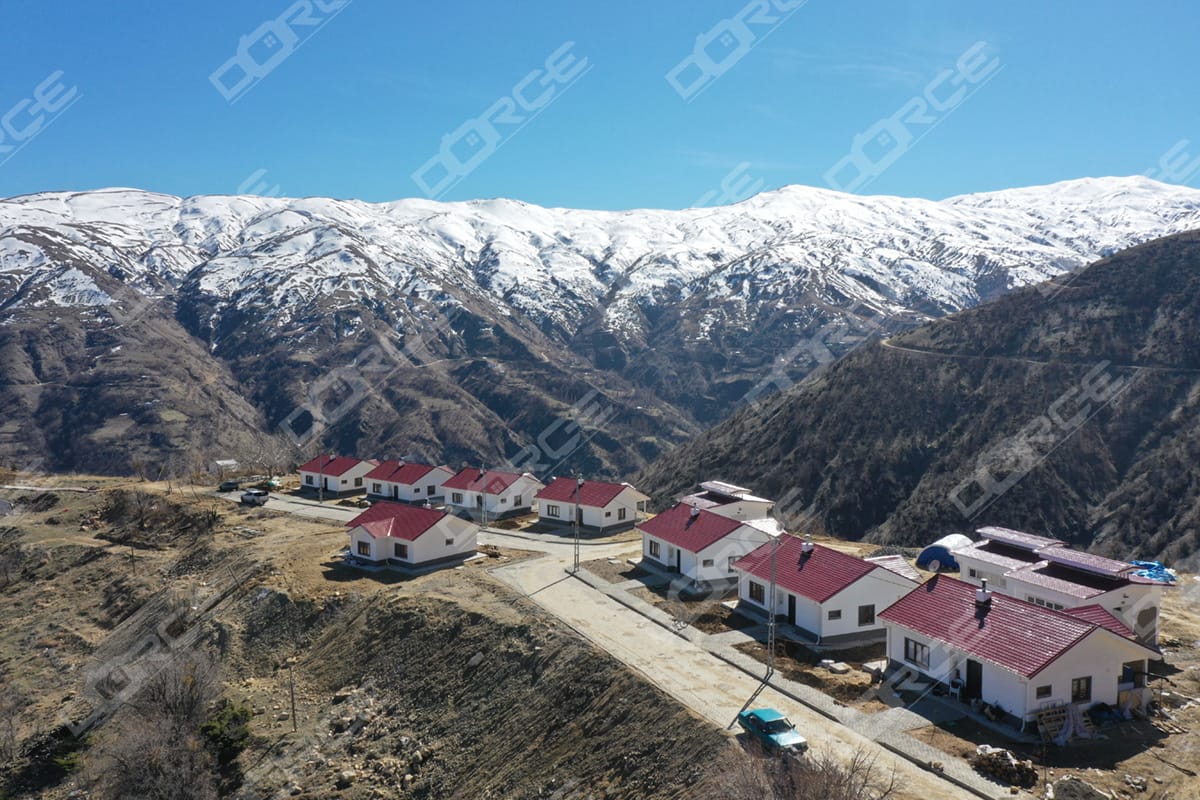
Mobilizing to Manufacture After February 6
DORÇE won the government bid to participate in rebuilding efforts almost immediately after the earthquake, thanks to their experience and expertise as a modular manufacturing company globally in more than 60 countries.
“Our expertise area is focused on mass production or large-scale projects,” said Deputy General Manager Geldimurat Annageldiyev. “We call it CLQ, centralized labor quarters for the oil, gas and mining sector starting from 5,000 up to 120,000 laborers. We provide turnkey solutions for the oil, gas, and mining sector.”
Through the "Village Houses and Barns Project,” DORÇE worked with Turkish housing and disaster management leadership to design structures that could be quickly built and able to withstand both seismic and climate changes. Given the immediate need for housing, DORÇE’s team worked in conjunction with a network of other authorities and subcontractors to collaborate and install these prefab housing units as quickly as possible.
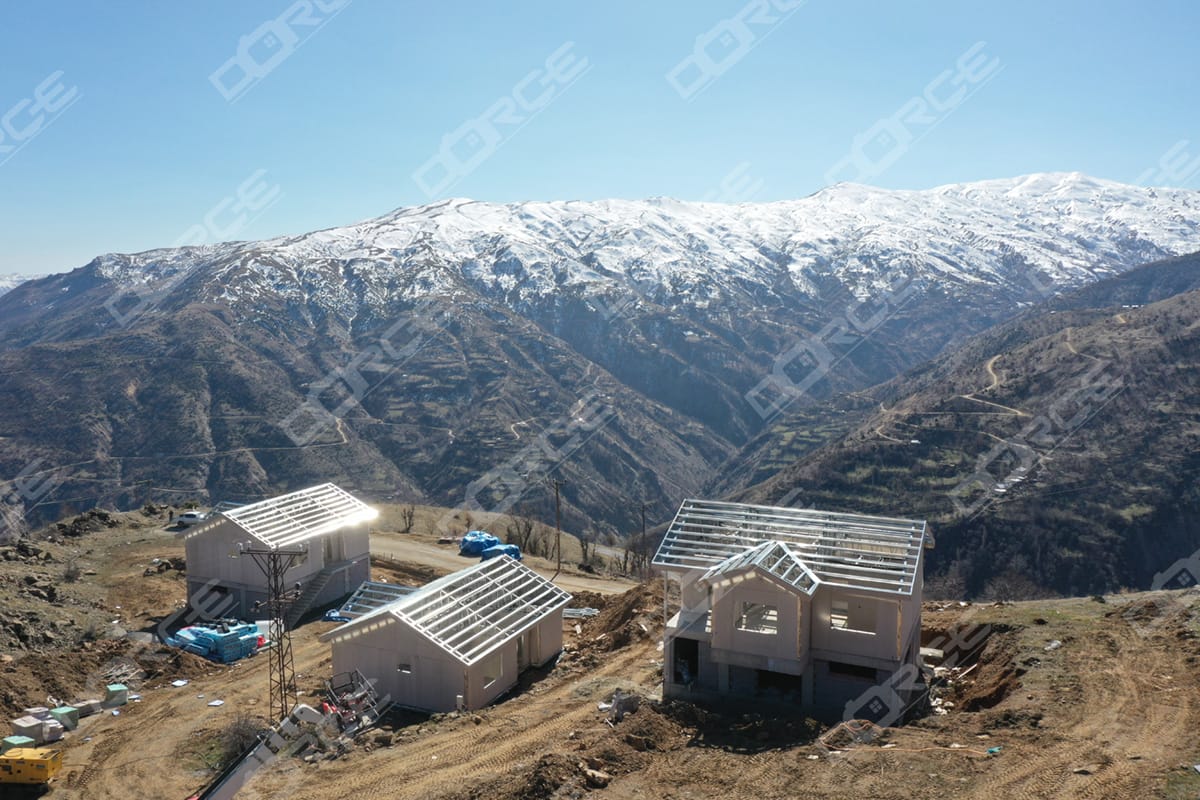
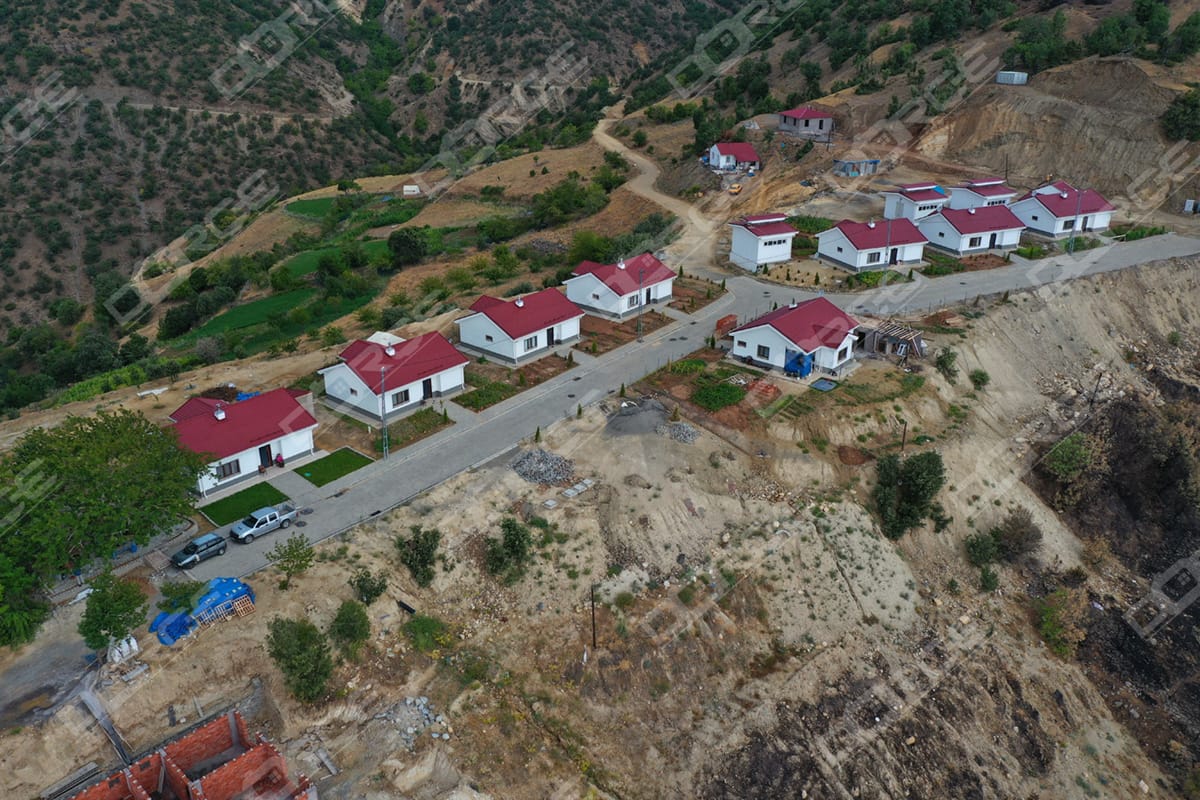
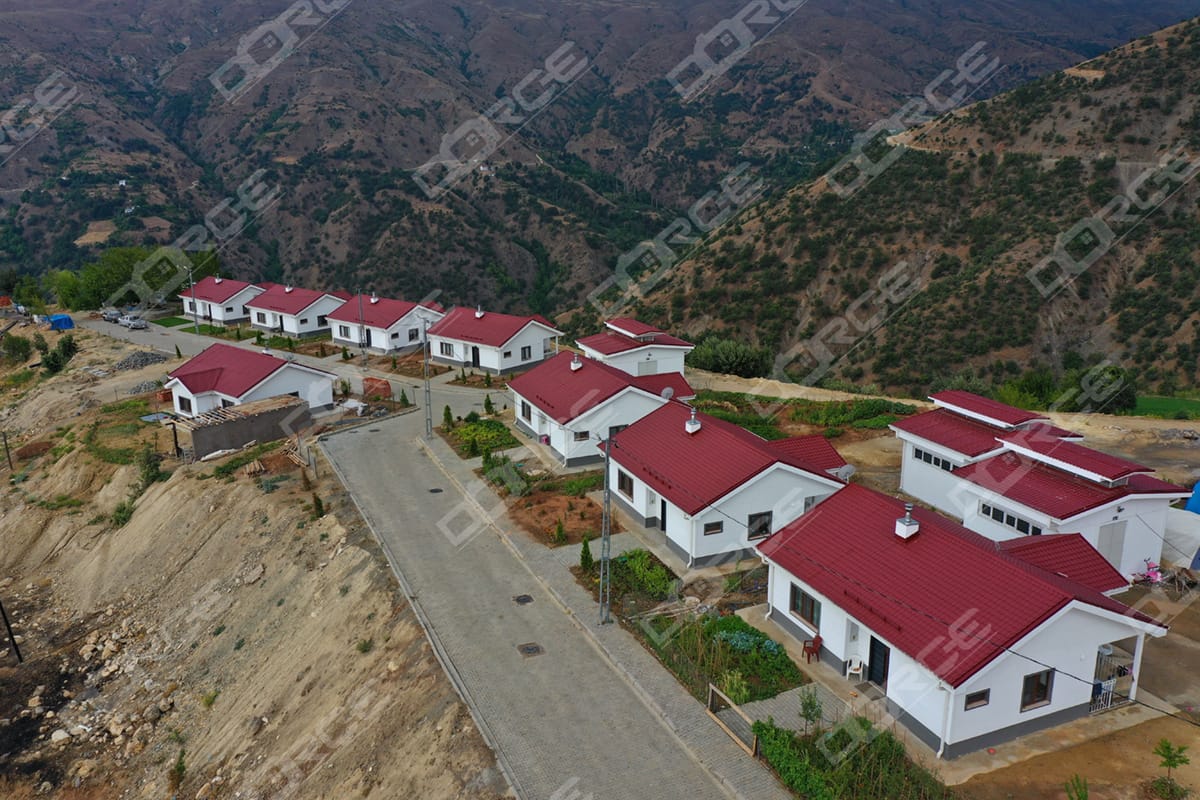
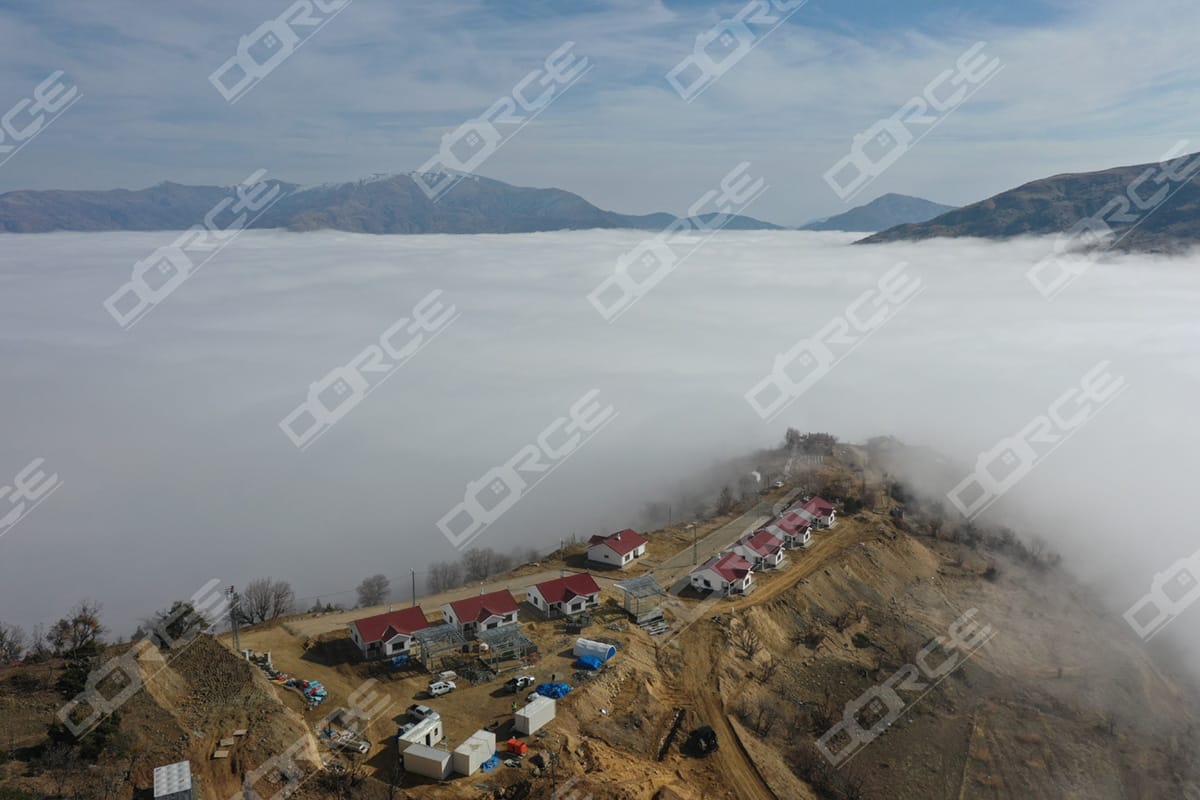
They were responsible for developing the superstructure, said Geldimurat, meaning DORÇE had to work extremely fast to deliver both a design and a physical module. DORÇE put together a design in three days, and immediately sent it off to the factory. The government tapped other companies to help with soil investigation, site service, and installation.
“They awarded contracts to local companies for two reasons,” said Geldimurat. “First of all, they are locals, and they can immediately start actions at the site. And second and most important, to support them because as they are locals, they were the most affected from the disaster area.”
As soon as they were given the go ahead to start, DORÇE’s plant and team stopped all ongoing projects to pivot over to fabrication and delivery. Staff at the manufacturing plant in Ankara were scheduled to work around the clock, requiring back-to-back shift scheduling—three shifts a day, for 24 hours a day, seven days a week.
Related Reading:
Turkish Manufacturer Has Long History of Responding to Disasters
DORCE has a rich history of responding to disasters in the area, almost from its inception in the early 1980s. Due to its proximity to one of the most active earthquake zones in the world, they have invested a lot of time into the design and production of earthquake-resistant modular structures.
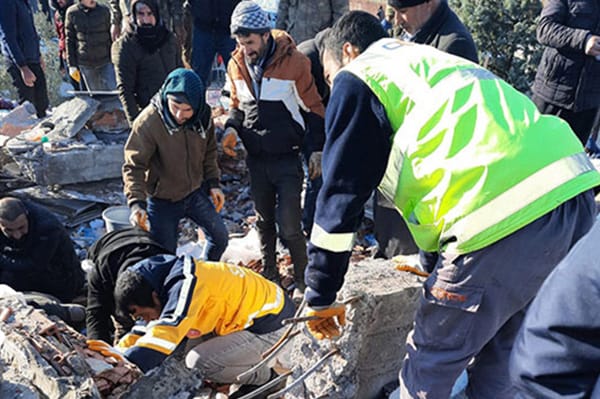
Designing for Quick Delivery and Installation
Given the truncated schedule to prioritize the delivery of modules, DORÇE focused heavily on prefabrication elements that would help avoid any additional installation challenges. For example, each module featured light gauge steel for the frame and the roof; integrated utility pipes to minimize mechanical, electrical, and plumbing work (MEP) work on-site; and traditional drywall.
Even with these weight and time constraints, the modules still had to be as fully furnished as possible for immediate move-in for earthquake victims who were staying in shelters.
According to Business Development Specialist İlyas Gasilov, the design was optimized to maximize factory-based (off-site) manufacturing. To minimize on-site mechanical work, all wall panels were prefabricated with integrated utility pipes. Additionally, considering weather and logistical constraints, the utility lines were also designed to be installed in the suspended ceiling. The in-wall utilities were prefabricated at the factory, and these two manufacturing processes were seamlessly integrated on-site.
Typically, DORÇE has anywhere from 10 to 15 types of mockups for clients to see in person at the factory. The company also made couple of available for the government to inspect and review prior to delivery.
With the light gauge steel and other design elements, DORÇE was able to deliver two plug-and-play modules per truck across high altitude roads quickly to east Türkiye. The first modules arrived on site about ten days after the earthquake. At the peak of the project, DORÇE was manufacturing upwards of 375 modules per day.
“We had up to 180 trucks delivering [modules] from our factory on a daily basis,” said Geldimurat. “I've been in many countries and have visited many factories. So, can you imagine producing 375 modules daily? It's an amazing figure.”
In about four to five months, the company was able to fulfill its original government contract, delivering up to 45,000 modules in all affected cities and around 3,000 permanent village houses across 76 locations in six to seven cities. These modules were used to create 22-square-meter temporary housing units, 90-square-meter permanent housing units, and multipurpose buildings for government and commercial use.
Overall, DORÇE helped communities get back up on their feet by providing buildings for banking, government, temporary housing for NGOs, and more.
Delivering Modules to Eastern Türkiye
As the damage was so widespread across Türkiye, DORÇE delivered modules across mountainous regions and high-altitude areas over 10 hours away from the factory in Ankara.
High winds, winter weather, and overall seismic climatic conditions contributed to the overall construction difficulties and design considerations.
“In normal circumstances when we deliver a product to any location in any part of the world, including Türkiye, of course we take into consideration the earthquake zone, wind load, snow load, and more,” said Geldimurat. “But for this particular earthquake area, even the weather forecast was changing quickly.”
They were also facing infrastructure challenges, as roads needed to be cleared of earthquake debris for delivery. Additionally, major utilities and power systems were affected, which made obtaining on-site power for assembly difficult as well. Once the modules were delivered, assembly was carefully done, as crane and lifting operations were minimized due to strong winds. However, the lightweight design helped with assembly, as the loads were already reduced.
According to İlyas, there were also safety risks that needed to be addressed with regards to concrete pouring because of the locations. In order to mitigate these risks, both standard mixers and “highly maneuverable concrete carriers” were used when building the foundations for these modules.
Unprecedented Disasters Lead to Unprecedented Results for DORÇE
Geldimurat has seen a lot in his 22 years working in modular construction, and particularly with DORÇE. But even with the amount and size of projects he’s worked on, nothing can really compare to the tireless efforts the company put in to manufacture all these modules for earthquake victims, he said. Everyone at DORÇE worked hard to design, manufacture, and deliver these modules—in some cases, even in spite of the personal losses they faced due to the earthquake.
“There are too many projects that have been great accomplishments for all of us,” he said. “But with the earthquake in Turkey, it's not just technical or capacity achievement, you're bringing people a solution. You're bringing people a solution for where to live, where to continue their lives.”
The company is continuing to work with the government in the areas that have been affected, as people continue to acclimate to their new lives more than a year and a half later.
“We are talking about 10 cities affected, and some cities or some districts were completely destroyed,” he said. “But overall, we can say in spite of all of these difficulties, life continues…There are hundreds of thousands of constructions underway, both conventional and different modern methods of construction (MMC). Our main focus was to be there exactly just after the earthquake, and we did that successfully.”
About the Author: Karen P. Rivera is a freelance writer and editor with a passion for storytelling. She is a former United Nations-based reporter, with experience covering international breaking news, venture capital, emerging healthcare tech, and the video game industry.
More From Modular Advantage
Oregon’s Prevailing Wage Proposal: A Wake-Up Call for Modular Construction
In early February, 2024, the Massachusetts Board of Building Regulations and Standards (BBRS) released its proposed 10th Edition building codes. This draft included several amendments targeting modular construction that would have created an extremely difficult environment for the entire modular industry and could have eliminated the industry entirely in the state.
Behind the Design of Bethany Senior Terraces, NYC’s First Modular Passive House Senior Housing Project
As more developers seek to meet new regulations for energy efficiency, the team at Murray Engineering has set a new record. With the Bethany Senior Terraces project, Murray Engineering has helped to develop NYC’s first modular structure that fully encompasses passive house principles — introducing a new era of energy efficiency in the energy-conscious city that never sleeps.
How LAMOD is Using Modular to Address Inefficiency, Sustainability, and the Future of Construction
As developers, designers, and contractors seek to understand the evolving needs of the modular industry, no one is as well-versed in the benefits of going modular as Mārcis Kreičmanis. As the co-founder and CBDO of LAMOD in Riga, Latvia, Mārcis has made it his ultimate goal to address the inefficiencies of traditional construction.
From Furniture Builder to ‘Activist Architect’: Stuart Emmons’ Unique Journey
Stuart Emmons was fascinated by buildings at a young age. He remembers building sand cities with his brother during trips to the Jersey shore. His father gave him his first drawing table at the age of ten. Today, he is an experienced architect who received his FAIA in June 2025. The road he took is unique, to say the least.
Forge Craft Architecture + Design: Codes, Contracts, and Intellectual Property
Founding Principal and Director of Modular Practice for Forge Craft Architecture + Design, Rommel Sulit, discusses the implications of codes, contracts, and intellectual property on
modular construction.
Eisa Lee, the “Bilingual” Architect
Now as the founder of XL
Architecture and Modular Design in Ontario, Canada, she applies not just her education as a traditional architect but an entire holistic view on modular design. It’s this expansive view that guides her work on being a true partner that bridges the gap between architects and modular factories as they collaborate on the design process.
Tamarack Grove Engineering: Designing for the Modular Sector
The role of a structural engineer is crucial to the success of a modular project, from initial analysis to construction administration. Tamarack Grove offers structural engineering services — project analysis, plan creation, design creation, and construction administration — for commercial, manufacturing, facilities, public services, and modular. Modular is only one market sector the company serves but it is an increasingly popular one.
Engineer Masters the Art of Listening to His Customers
Since founding Modular Structural Consultants, LLC. in 2014, Yurianto has established a steady following of modular and container-based construction clients, primarily manufacturers. His services often include providing engineering calculations, reviewing drawings, and engineering certification
Inside College Road: Engineering the Modules of One of the World’s Tallest Modular Buildings
College Road is a groundbreaking modular residential development in East Croydon, South London by offsite developer and contractor, Tide, its modular company Vision Volumetric (VV), and engineered by MJH Structural Engineers.
Design for Flow: The Overlooked Power of DfMA in Modular Construction
Unlocking higher throughput, lower costs, and fewer redesigns by aligning Lean production flow with design for manufacturing and assembly.