Revisiting Yellowstone Canyon Village—a Groundbreaking Modular Construction Feat—Ten Years On
The oldest national park in the world was in need of a big lodging revamp in the late 2000s.
Before 2014, any of the 3.5 million annual visitors to Yellowstone who wanted to experience an overnight stay in the remote altitude of Canyon Village had little choice but to stay in an outdated motel-style cabin. These 200 cabins, providing a total of 410 rooms, were initially built in 1957 to meet the uptick in visitorship (then around 1.7 million annually) as part of the “Mission 66” plan.
About 57 years later, Xanterra Travel Collection®, Yellowstone’s main park concessionaire, was tapped to tackle the conundrum of revitalizing lodging in this remote, elevated area prone to extreme climatic conditions. In fact, they embarked on one of the largest hospitality construction projects for the National Park Service—and they did it in record time with modular.
In collaboration with Guerdon, LLC, a modular design and manufacturing firm based out of Boise, Idaho, Xanterra replaced the 410 rooms in Canyon Village across five multistory lodges in just two years. Thanks to modular design, Guerdon was able to marry the rustic, natura beauty of Yellowstone with the resilient, sustainable requirements necessary to maintain this one-of-a-kind property.
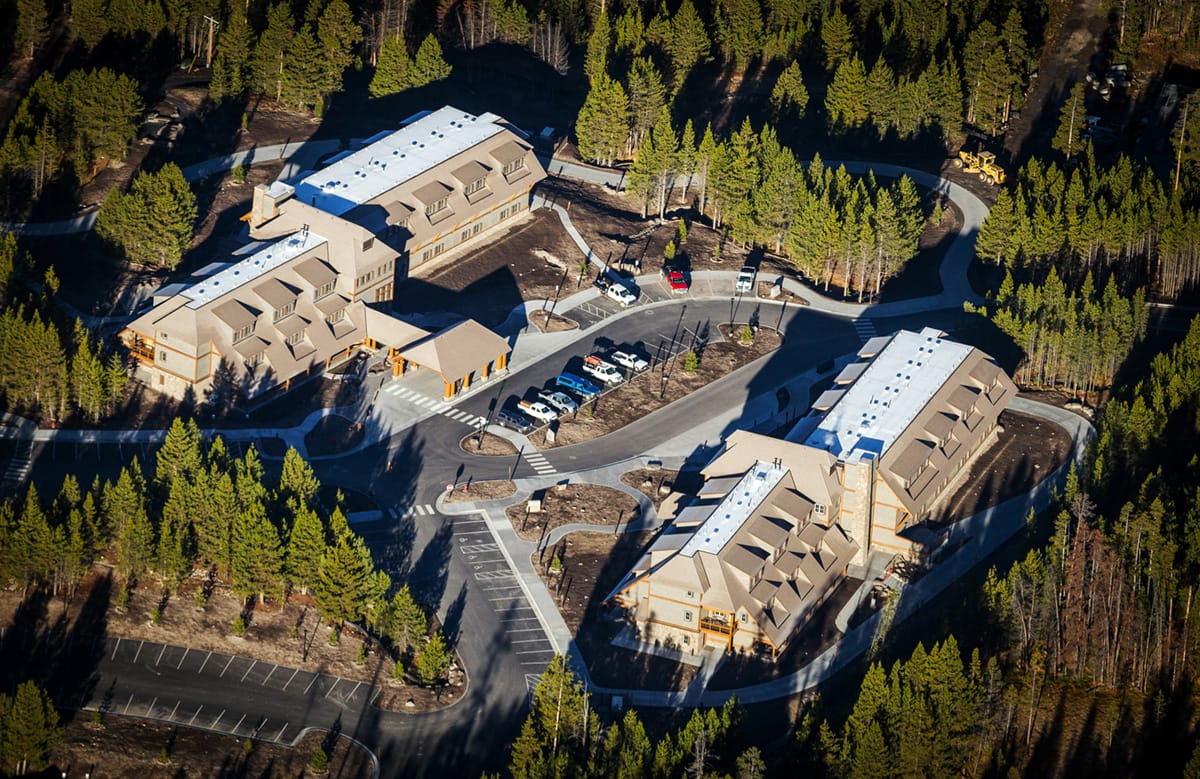
An aerial view of the completed Yellowstone Canyon Lodge, manufactured by Guerdon.
Poised For Sustainability Gains Due to Elevation Needs
Mike Keller, Xanterra’s Vice President/General Manager, had seen the growing need to upgrade the lodging availability in Canyon Village over his longstanding tenure at Yellowstone.
“[Mission 66] was intended for five years, and it ended up lasting close to 70 years,” he said. “So the long overdue need to build just modern visitor-friendly, visitor-useful services was just glaring in the Canyon Village. Canyon’s at the highest elevation in Yellowstone and tends to have some of the most significant snowfall in the park.”
Canyon Village, standing just under 8,000 feet above sea level, initially featured buildings that resembled “literal box cars, flat roofed, portable cabins that looked way out of place,” said Keller.
So, when Xanterra envisioned the replacement lodges, a lot of the design centered on implementing resiliency and sustainability into these structures. Each building was created with unique MEP systems and external facades to:
- Minimize the impact of snow load and accumulation with high-pitched roofing.
- Maintain structural integrity regarding temperature fluctuations from extreme weather conditions and seismic activity.
- Remove frozen water threats with sloped pipes to draw out excess water from main and safety lines before winter closure.
- Meet LEED certification requirements.
- Ease any annual winter drain down processes for park staff.
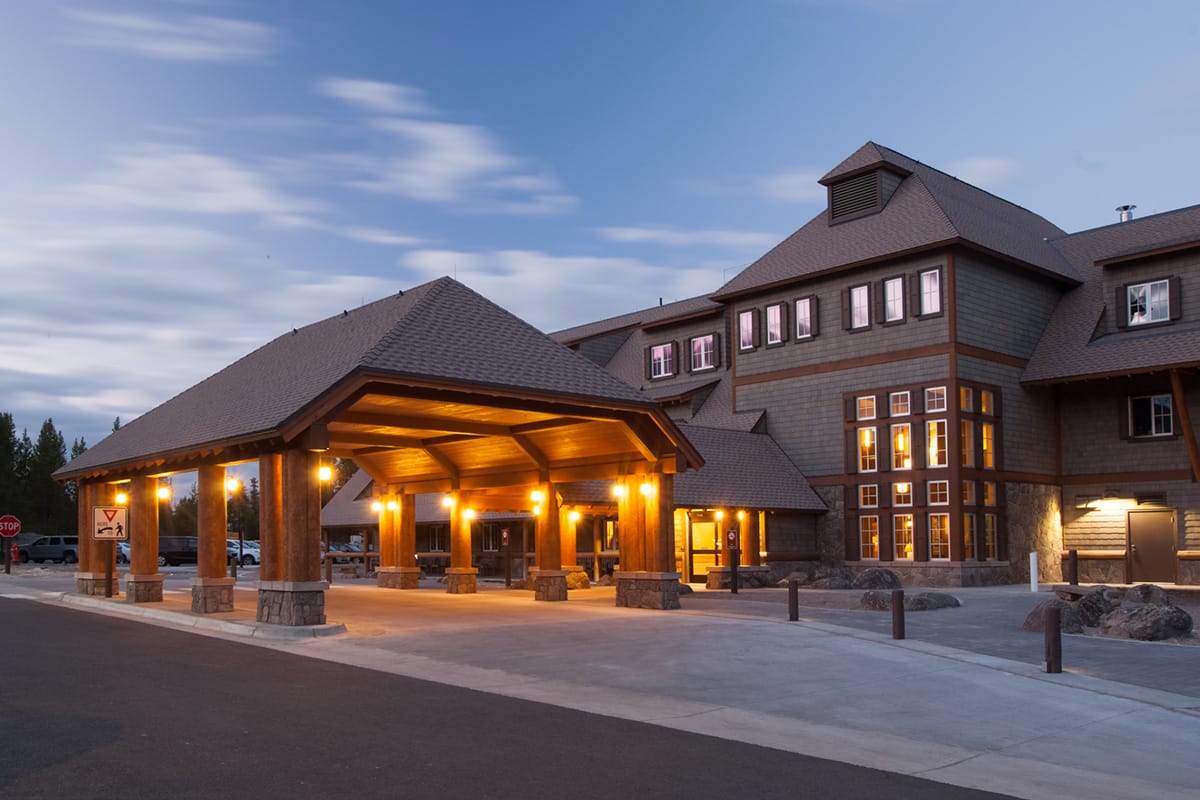
Moving from the “Drawing Board” to Practical Implementation
As part of Guerdon’s Business Development Department, Director of Design & Product Development Mitch Hovaldt was faced with the creative challenges of meeting all of Xanterra’s requirements for the lodges at Canyon Village. The obstacles were stacked as high as Canyon’s elevation level, as Hovaldt remembers from 2013.
“I got a call from somebody that said, ‘Hey look, we have this project, we’re challenged with time. It’s in Yellowstone. What can we do to get the product on the ground?’” he said. Over the course of a year, he reviewed the site plan for the five buildings for Guerdon’s engineering department, creating the initial massing, layouts, and processes before working in tandem with the factory design team.
Guerdon’s Design Manager Chad Hart, then a senior modular designer, was brought onto the project in 2014. He focused on the factory production details to make sure that manufacturing could match the architectural, structural, and MEP expectations given by Xanterra.
Each module measured about 13 feet 8 inches wide, with a typical length of 54 feet, which was easily within Guerdon’s fabrication capability. Together, Hart and Keller’s teams pored over the blueprints, inserting material types, module sizes, and even small details like tile work.
“We went into each room type and actually drew in every single piece of trim board that they needed,” said Hart. “Every outlet, every light fixture, all of the tile work we had all designed into our Revit model all figured out so that we could help our production group build the thing more efficiently.”
On top of the internal finishes, the roof designs pushed Guerdon to rethink fabrication practices to meet the environmental demands at Yellowstone.
High-Pitched Roofs and Fabrication Challenges for the Winter Drain Down
The upper-level unit types required complex thinking and creative workarounds, according to Hovaldt. The initial design featured a “cape-style roof,” with sharp angles typically not found in modular cube designs, challenging Guerdon’s design team to ensure that everything aligned correctly.
Additionally, Xanterra was “purchasing truss packages that were going to overbuild on top of the modules that we were delivering, we had to have a highly coordinated design package with that upper-level floor,” said Hovaldt “We had dormers that poked out from that, and they were window dormers within the suites as well.”
“We spent a lot of time developing the upper-level units to make sure that all the wall and ceiling assemblies were correct,” he said. “While our factory has established processes for building walls and ceilings, we added an extra component to accommodate the angled wall needed for the roof system. This added a little bit more complexity to our plant’s operations, but it was necessary to achieve the design.”
Hovaldt and his team also installed a vapor barrier component that also worked to reinforce structural integrity in the face of said extreme climate conditions like heavy snow loads.
“We also had a poly wrap that we had to put behind the drywall for the vapor barrier according to specifications. That was a little bit outside of our realm that we were comfortable with at that time, but we managed to make all that work.”
In addition to the fabrication work, the sloped piping and radiant heat elements required Hart and his team to design ceilings and corridors with ample spacing to help Canyon Village in their annual winterization efforts.
Subtly sloped piping along with strategically placed valves that together utilize gravity to clear the water during the annual winterization were crucial design functions, said Xanterra’s Director of Sustainability Dylan Hoffman.
“The less time that we have to spend on the individual winterization of each of these buildings, the more time we can focus on other crucial aspects in preparing these facilities for a long, cold winter,” he said. “It was a major focus for us and something that has worked well.”
Even with all these design anomalies in play, the main challenge that was on everyone’s mind was: How quickly could these modules be transported and crane installed?
Transporting Modules in the Off Season Helped Avoid Traffic Pressure
One part of the unusual construction restraints for Canyon Village had to do with one simple variable: time. Yellowstone’s most active months of the year are during summer, or from May to October. Canyon Village is nestled away about an hour northeast of Old Faithful, and is only accessible by two main roads. After October, the two main roads are closed for the winter.
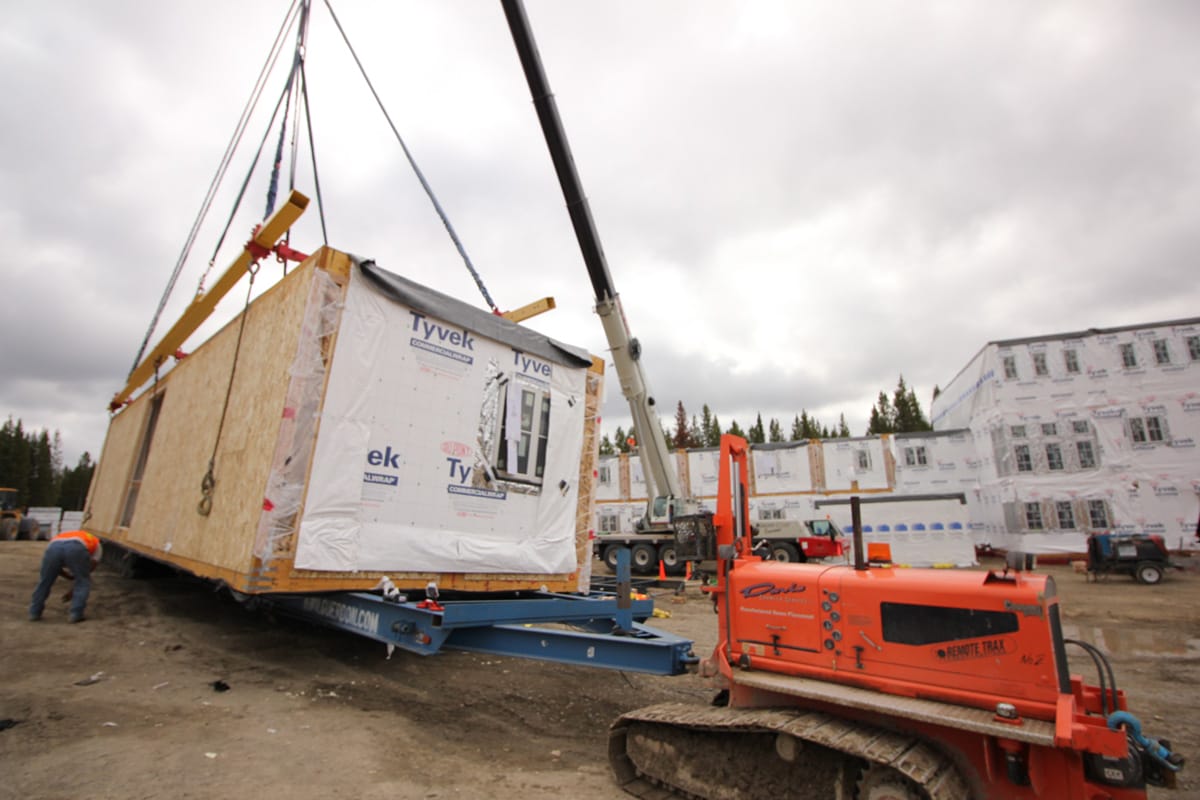
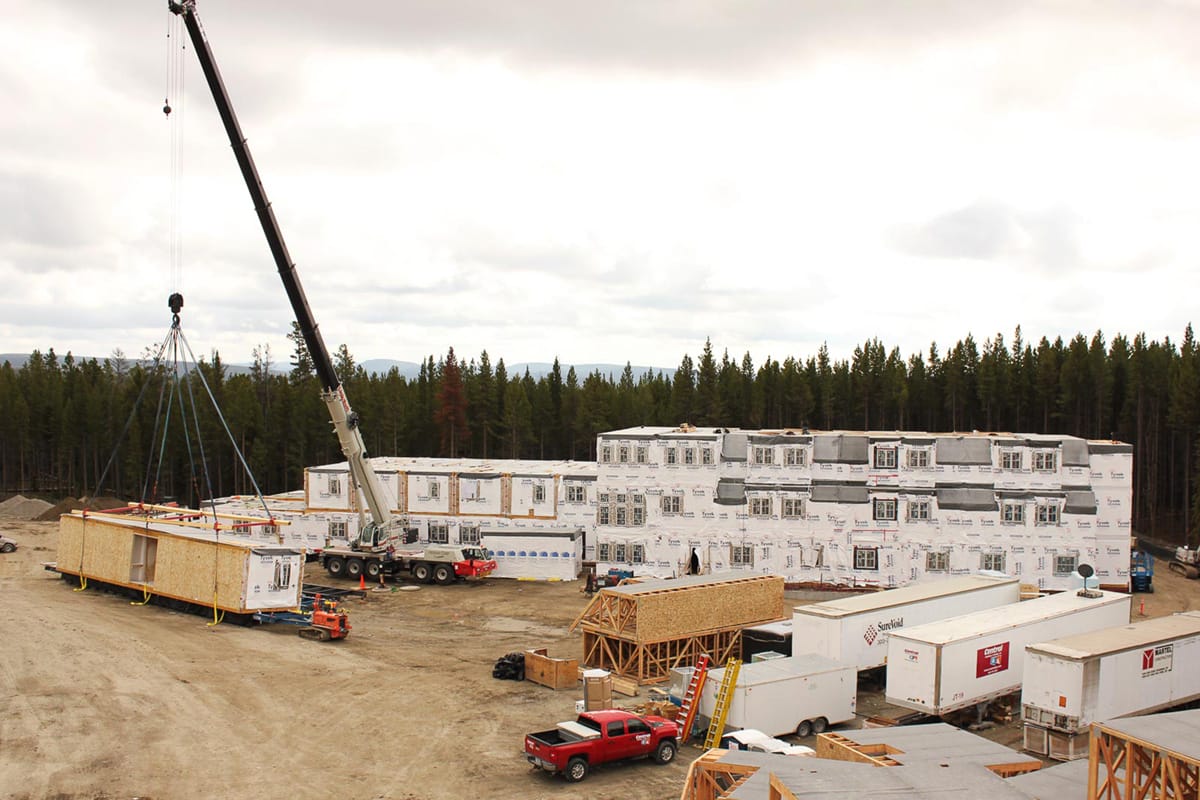
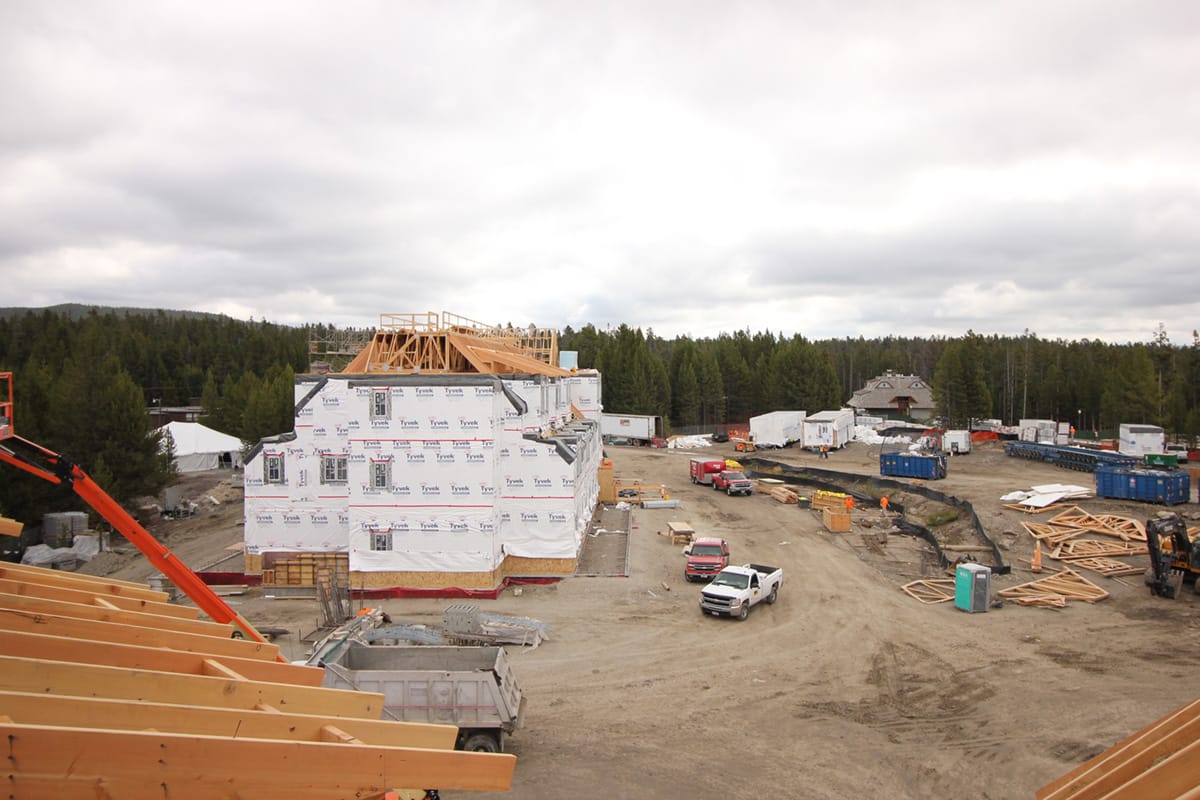
Guerdon and the modular set crew faced numerous challenges due to weather, park visitors, and the site's remote location.
With such a short building period, it made the most sense for Xanterra to pursue modular. Yellowstone’s high visitor traffic also required some odd transportation scheduling, as traffic from the West Yellowstone entrance determined the times when trucks could unload modules.
In July of 2014, Guerdon started shipping the first modules out to Yellowstone, moving them in in two stages—from Boise to the West Yellowstone entrance, and then West Yellowstone to Canyon Village.
However, often carriers would be coming in after park hours and throughout the shoulder seasons, said Hoffman. Module transportation was targeted for those shoulder seasons before the park opened and closed in earnest. Before the park opened for the main season, plows would come in from March 25 to about April 5 to clear the snow. During the fall, the roads would be maintained from November 1st to Thanksgiving post-closing. In both those time frames, trucks could come in and offload modules without dealing with visitor traffic.
It took a bit of administrative and logistics juggling to make the double staging happen, because giant flatbeds were queued up to enter via the west entrance and eventually staged into the park.
“It was really a trick to try to minimize the impact both with employees but also just general park travel,” said Hoffman.
Mike Keller also echoed the logistics difficulties, noting that “while we were open in some of those early weeks and late weeks, they would do drives, but late at night, early in the morning when traffic was minimal or not on the road. You’d have flagging vehicles, you’d have pilot cars, all the things you would expect on narrow mountain roads,” he said.
Digging Snow Tunnels, Cranes Swinging Modules On Site
As the roofing system also pushed Guerdon to their creative limits, installing all the modules onsite with these sharply angled ceilings provided one aspect of unusual site work. There was also the issue of the impending weather hampering installation.
Guerdon’s design team had experience with extreme cold conditions, but the sudden closure and drop in construction reinforced the value of weather tight modules and the building was fully dried in before the snow came in, according to Mitch. In the fall of 2014, three buildings had been shipped and crane installed, with all of them fully dried in prior to any snow fall.
Internal installations and construction work continued throughout the winter.
At one point, “tunnels were being dug through the snow to get [into] the buildings because the snow was so deep” for crews working on the inside of the craned building, said Hovaldt.
Once spring of 2015 came around, construction continued, and the final two buildings were shipped and crane installed.
Finding The Right Pine Trim and More For LEED Certification
Another major piece of the production puzzle was related to LEED certification. Xanterra’s contract with the National Park Service stipulated the use of specific recyclable materials and local procurement requirements. According to Hoffman, Xanterra was also aiming for a LEED Silver certification with the Canyon Village project. For example, choosing to go modular helped meet LEED certification by significantly diverting about 85 percent of construction waste.
“With the LEED version that we were using at the time, the 2009 version, there were credits around regional materials,” he said. “For anything that’s sourced within a 500-mile radius, you could get credits for that or for using certified wood. So, if you’re using a FSC or SFI certified wood throughout the process, you can get points based on the percentage that you’re using. The same goes for things like materials containing recycled content.”
Guerdon worked with vendors to obtain materials like blue pine beetlekill wood for the finishes, recycled glass countertops, low-to-no-VOC paints, and carpets made of recycled materials. The challenge, according to Hovaldt, was trying to find them within the designated radius of the project site.
The work behind obtaining LEED certification was found in the everyday details in the modules, such as LED lighting, low-flow rate shower heads, gallon per minute toilet flushes, smart switches, high performance windows, and more. All these small things helped Canyon Village manage resources more effectively, said Dylan.
The pre-planning paid off, as four of the Canyon Village buildings have a LEED Gold certification, with the fifth obtaining LEED Silver.
The Statistics Behind the Success of Canyon Village
After the lodges opened up in 2016, the number of annual visitors coming to Yellowstone increased from 3.5 to about 4.5 million, and the numbers keep rising. The construction of Canyon Village lodges remains to this day the largest sustainable building project in the history of the National Park Service.
“It’s one of the first modular projects to go into a national forest in the entire country,” said Hart. “That’s a pretty big deal.”
All five buildings continue to perform admirably, with little to no weather effects or repairs needed to adjust day-to-day operations.
“These buildings are durable. They have lasted, they have weathered fine,” said Keller. “They’ve held up the elements and the challenges of our seasonality here in the park, and this project was very well constructed, and it’s continuing to show and benefit itself that way.”
The Canyon Village project also stands out as one of the top five best projects for Chad Hart and Mitch Horvaldt at Guerdon. Xanterra’s Mike Keller and Dylan Hoffman also look back fondly at the construction of Canyon Village as one of their top three.
About the Author: Karen P. Rivera is a freelance writer and editor with a passion for storytelling. She is a former United Nations-based reporter, with experience covering international breaking news, venture capital, emerging healthcare tech, and the video game industry.
More from Modular Advantage
AI, Faster Sets, and Automation: The Future of Modular is at World of Modular
While the modular building industry has long known that it can be an effective solution to increase affordable housing, the word is slowly spreading to more mainstream audiences. Three presentations at this year’s World of Modular in Las Vegas hope to provide insight and direction for those seeking a real solution to the crisis.
An Insider’s Guide to the 2025 World of Modular
The Modular Building Institute is bringing its global World of Modular (WOM) event back to Las Vegas, and with it comes some of the industry’s best opportunities for networking, business development, and education. Over the course of the conference’s four days, there will be numerous opportunities for attendees to connect, learn, and leverage event resources to get the most out of the conference.
Affordable Housing Now: The Industry’s Best Bring New Solutions to World of Modular
While the modular building industry has long known that it can be an effective solution to increase affordable housing, the word is slowly spreading to more mainstream audiences. Three presentations at this year’s World of Modular in Las Vegas hope to provide insight and direction for those seeking a real solution to the crisis.
Opportunities for Innovation in Modular Offsite Construction
Modular Offsite Construction has already shattered the myth that it only produces uninspired, box-like designs. Architectural innovations in module geometry, configurations, materials, and products make it possible to create visually stunning buildings without sacrificing functionality or efficiency.
Safe Modular Construction with Aerofilm Air Caster Transport
In collaboration with Aerofilm Systems, Heijmans developed innovative skids using air caster technology for moving modules easily and safely. These pallets are equipped with an auto-flow system, making operation extremely simple.
Miles, Modules, and Memes: Building a Modular Network One Flight at a Time
At the end of the day, social media is just another tool for building connections, and like any other tool, needs to be used skillfully to work properly. Use social media thoughtfully, and it will open doors to real opportunities and relationships you didn’t even see coming.
Falcon Structures: Thinking Inside the Box
Some of Falcon’s latest projects include creating container solutions for New York’s Central Park and an East Coast professional baseball team. More and more, Falcon is shipping out container bathrooms and locker rooms to improve traditionally difficult work environments, like those in oil and gas or construction.
UrbanBloc—From Passion to Industry Leader
UrbanBloc specializes in three main categories or markets – what they call “Phase 0” projects, amenities, and urban infill. Clients are often attracted to shipping containers because from a real estate perspective they are considered an asset. Having the flexibility to move and transport these assets allows owners to respond to different circumstances in a fluid manner that they can’t get with standard construction.
The Hospitality Game-Changer
“Hospitality is about more than just providing a service – it’s about delivering an experience,” says Anthony Halsch, CEO of ROXBOX. “And that’s where containers thrive. They allow us to create spaces that are unique, efficient, and sustainable.”
Container Conversions Counts on Simplicity to Provide Critical Solutions
Container Conversions has fabricated and developed thousands of containers for varied projects, including rental refrigeration options, offices, kitchens, temporary workplace housing, and mobile health clinics.