Digitalizing Your Products for Seamless Integration into Offsite Projects
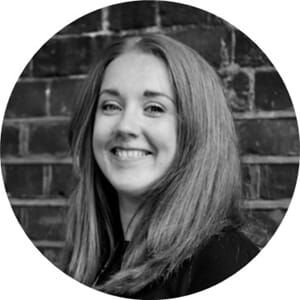
Charlotte Garrett is the Head of Industry Strategy at KOPE.
Buildings are too often designed without the method or the products we intend to use in mind. We continue to apply offsite construction products to projects using traditional methodologies despite their inherent differences, leading to significant inefficiencies and low productivity.
Redesigning projects, to later accommodate offsite solutions, is expensive and risky, wasting creativity and opportunities for efficiency. This is largely due to a lack of visibility and accessibility to the right information about offsite products.
The construction industry must adapt to new ways of working.
Prefabrication and Offsite Construction Play an Important Role in Industrializing Construction
At the core of this transformation is the move towards productization which involves bringing products to the forefront of design.
We need to improve collaboration through transparency and accessibility of structured and standardized product information to create project consistency and predictability. By moving beyond prefabrication and embracing productization we will be able to create standard components that are packaged up and ready to be deployed in not just one project, but many projects.
Digitalizing Products can Enable Better Collaboration and Communication between Stakeholders
Converting standardized product information and processes into digital formats can enable accurate automation of configuring and placement of each component into a design model.
We need to move away from generic, descriptive design processes in traditional Design and Build Contracts. Designing with known manufacturing capabilities and limitations upfront. (A wall panel supplier may have standard panel sizes or may offer flexibility within maximum and minimum panel sizes). Access to this information allows designs to be validated early on, saving time, reducing rework and accelerating project delivery. Testing all components needed to construct building elements to be scheduled, costed and coordinated before committing to design freeze and manufacture.
KOPE enables products to carry information on product data, drawing templates, links to other products and systems, and the rules on how they should be configured and arranged in projects. We need to get rid of moments where decisions are translated either from one skill set to another and from one file type to another. The data that informs you, should also be the data that gets passed along to the next link in the chain.
KOPE plays a crucial role as an enabler in offsite construction, providing certainty to design decisions by offering a single access point for all manufacturer’s product information. Our platform integrates offsite processes and products, facilitating convergence between design and manufacturing.
It’s all about scalability and the applicability of the right data, to support decisions across design, construction, and procurement.
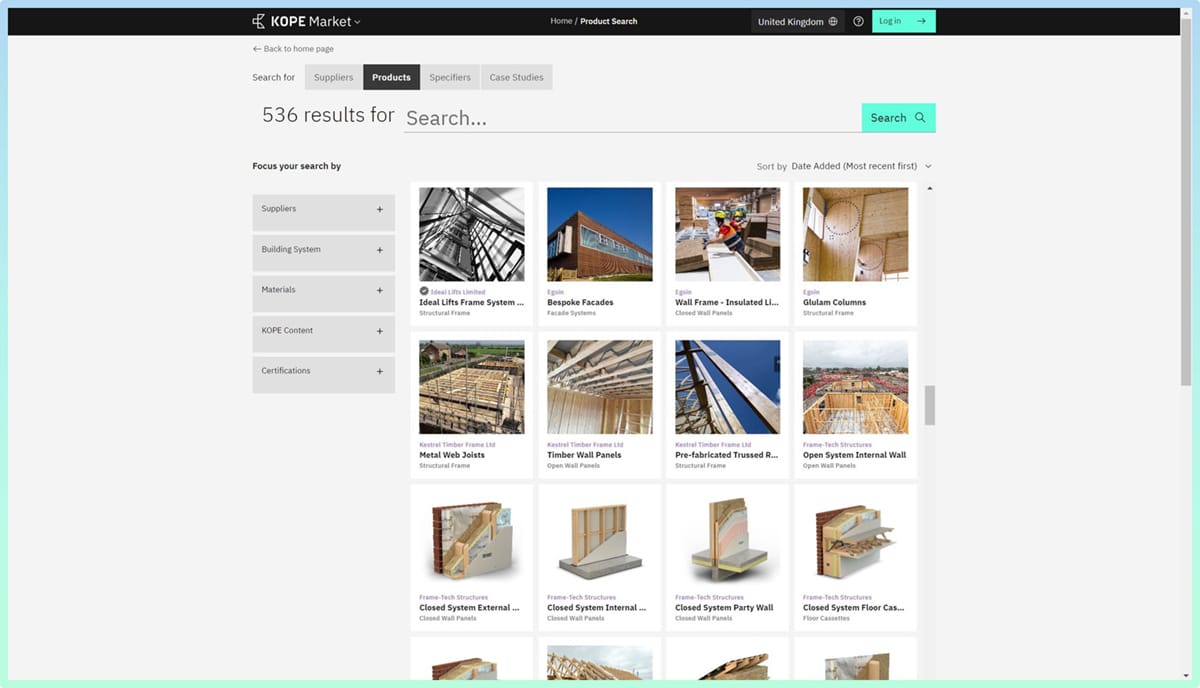
KOPE Market is a free and searchable database for offsite construction.
KOPE is a product configurator that allows you to seamlessly apply prefabricated products to your projects by automatically configuring and placing multiple products within design models. It enables suppliers to maintain and update product libraries, digitalizing all of the supplier-defined attributes and repeatable processes. This enables suppliers to have control over the application of their products into any project, ensuring compliance and consistent application to scale and gain value from efficiencies.
To compliment our configurator, we have KOPE Market, a free and searchable database for offsite construction, allowing organizations to explore and connect with suppliers and their products. It allows you to understand the capabilities of products and systems that can benefit projects, facilitating comparison and integrations into your supply chain for later application into the project.
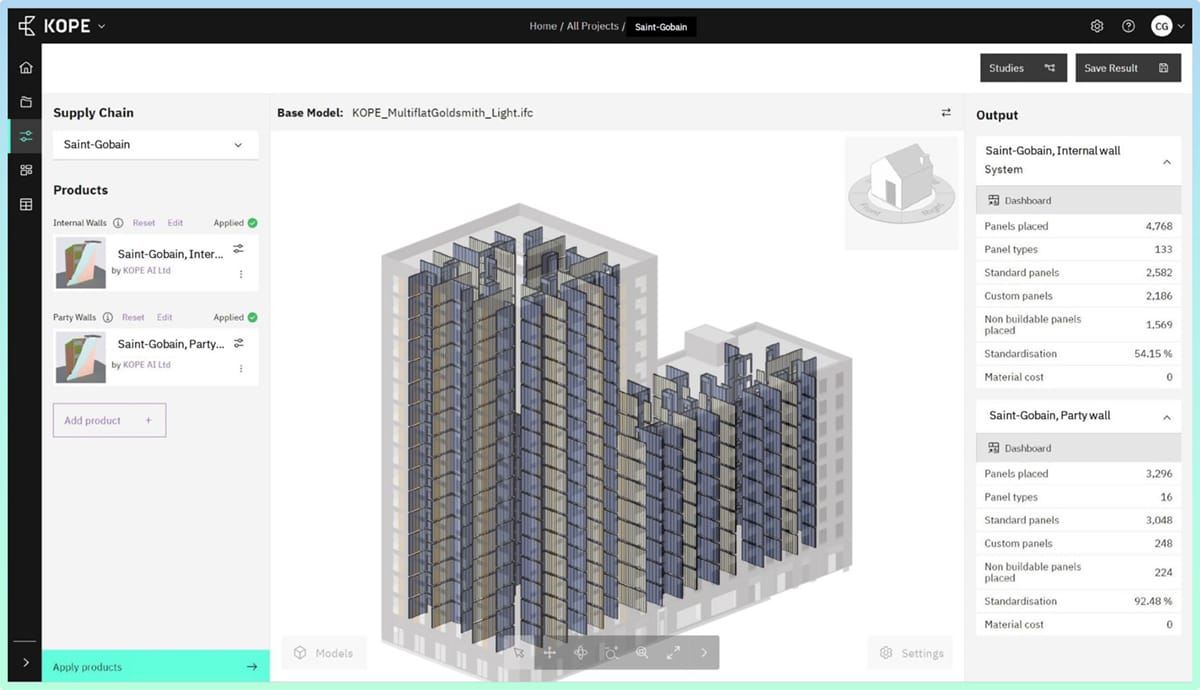
Case Study
The Challenge
Saint-Gobain approached KOPE, looking to improve the efficiency around processing project tenders for one of their prefabricated solutions.
Saint-Gobain traditionally operated by supplying system components into the construction sector which skilled labour assemble at a job site. This is relatively flexible but not efficient. New offsite solutions developed by Saint-Gobain enhance productivity and reduce waste but require early design engagement. Developing a quick, compliant and auditable platform to quantify a project’s suitability for costing and assessing feasibility is vital.
Saint-Gobain’s goal is to apply their solutions with greater speed and accuracy to their customer’s projects and to assess the levels of standardization of each project, by minimizing the number of bespoke components being manufactured. Building bespoke components was not only inefficient but also expensive, prompting a need to prioritize projects with the capability to apply significant standardization potential. They also sought to automate the generation of schedules and layout drawings for each building level within the project design model.
Our Approach
After onboarding Saint-Gobain’s product to KOPE, the digitalized asset captured all the product data and logic on how to integrate it into the project design, quantifying, and generating schedules and drawings to return a tender. Delving into their decision-making logic when applying their products to projects we were able to quickly digitalize the product’s data and logic to then automate their processes.
With KOPE’s platform, Saint-Gobain was able to seamlessly integrate its solutions into project models in minutes. KOPE identified all relevant building elements from within the IFC model, and translated all monolithic walls into precise manufacturable components, as defined by the solutions capabilities and rules around the application.
Following that, KOPE generated a set of layout drawings and basic outputs such as product-level quantities, and a 3d model, enhancing productivity and streamlining workflows around feasibility assessment. Its system-level understanding validated product placement, enabling assessment of design impacts on standardization levels.
‘’In order to apply offsite solutions to achieve their full potential, solutions need to be considered and integrated into project design much earlier than we do today. Developing a digital platform to allow this to be done very quickly and produce key measures and indicators which are system-specific and compliant is vital. KOPE allows solution data we have to be applied.‘’
— Tom Cox. Construction Solution Director, Saint-Gobain UK
The Results
By embedding manufacturers’ decision-making logic within digital assets, KOPE ensured that Saint-Gobain solutions behave as intended, guaranteeing adherence to standards. This gives users confidence when integrating the products into the design files, knowing they are manufacturable and meet expectations around efficiency in cost, program, and function.
Saint-Gobain is now able to achieve consistency in key metrics and performance indicators across customer projects. This standardization streamlined workflows minimized errors, enhanced productivity, and reduced waste. KOPE drastically reduced the time required to integrate products into design files, facilitating quicker and more accurate validation of design approaches.
KOPE is currently deploying the Saint-Gobain solution on a number of live projects, we will soon be sharing updates on the results.
More from Modular Advantage
Oregon’s Prevailing Wage Proposal: A Wake-Up Call for Modular Construction
In early February, 2024, the Massachusetts Board of Building Regulations and Standards (BBRS) released its proposed 10th Edition building codes. This draft included several amendments targeting modular construction that would have created an extremely difficult environment for the entire modular industry and could have eliminated the industry entirely in the state.
Behind the Design of Bethany Senior Terraces, NYC’s First Modular Passive House Senior Housing Project
As more developers seek to meet new regulations for energy efficiency, the team at Murray Engineering has set a new record. With the Bethany Senior Terraces project, Murray Engineering has helped to develop NYC’s first modular structure that fully encompasses passive house principles — introducing a new era of energy efficiency in the energy-conscious city that never sleeps.
How LAMOD is Using Modular to Address Inefficiency, Sustainability, and the Future of Construction
As developers, designers, and contractors seek to understand the evolving needs of the modular industry, no one is as well-versed in the benefits of going modular as Mārcis Kreičmanis. As the co-founder and CBDO of LAMOD in Riga, Latvia, Mārcis has made it his ultimate goal to address the inefficiencies of traditional construction.
From Furniture Builder to ‘Activist Architect’: Stuart Emmons’ Unique Journey
Stuart Emmons was fascinated by buildings at a young age. He remembers building sand cities with his brother during trips to the Jersey shore. His father gave him his first drawing table at the age of ten. Today, he is an experienced architect who received his FAIA in June 2025. The road he took is unique, to say the least.
Forge Craft Architecture + Design: Codes, Contracts, and Intellectual Property
Founding Principal and Director of Modular Practice for Forge Craft Architecture + Design, Rommel Sulit, discusses the implications of codes, contracts, and intellectual property on
modular construction.
Eisa Lee, the “Bilingual” Architect
Now as the founder of XL
Architecture and Modular Design in Ontario, Canada, she applies not just her education as a traditional architect but an entire holistic view on modular design. It’s this expansive view that guides her work on being a true partner that bridges the gap between architects and modular factories as they collaborate on the design process.
Tamarack Grove Engineering: Designing for the Modular Sector
The role of a structural engineer is crucial to the success of a modular project, from initial analysis to construction administration. Tamarack Grove offers structural engineering services — project analysis, plan creation, design creation, and construction administration — for commercial, manufacturing, facilities, public services, and modular. Modular is only one market sector the company serves but it is an increasingly popular one.
Engineer Masters the Art of Listening to His Customers
Since founding Modular Structural Consultants, LLC. in 2014, Yurianto has established a steady following of modular and container-based construction clients, primarily manufacturers. His services often include providing engineering calculations, reviewing drawings, and engineering certification
Inside College Road: Engineering the Modules of One of the World’s Tallest Modular Buildings
College Road is a groundbreaking modular residential development in East Croydon, South London by offsite developer and contractor, Tide, its modular company Vision Volumetric (VV), and engineered by MJH Structural Engineers.
Design for Flow: The Overlooked Power of DfMA in Modular Construction
Unlocking higher throughput, lower costs, and fewer redesigns by aligning Lean production flow with design for manufacturing and assembly.