CES Group’s Stuart Cameron Will Convince You the Moon Is Achievable with Modularized MEP
Give Stuart Cameron five minutes and he’ll tell you why you need to consider modularized Mechanical, Electrical, and Plumbing assemblies to develop new real estate. Give him an hour—preferably at a panel at World of Modular—and you’ll wonder how you even made it this far without knowing about the values of modular MEP.
But first, ask yourself, what does a prefabricated MEP assembly even do, and why should you care?
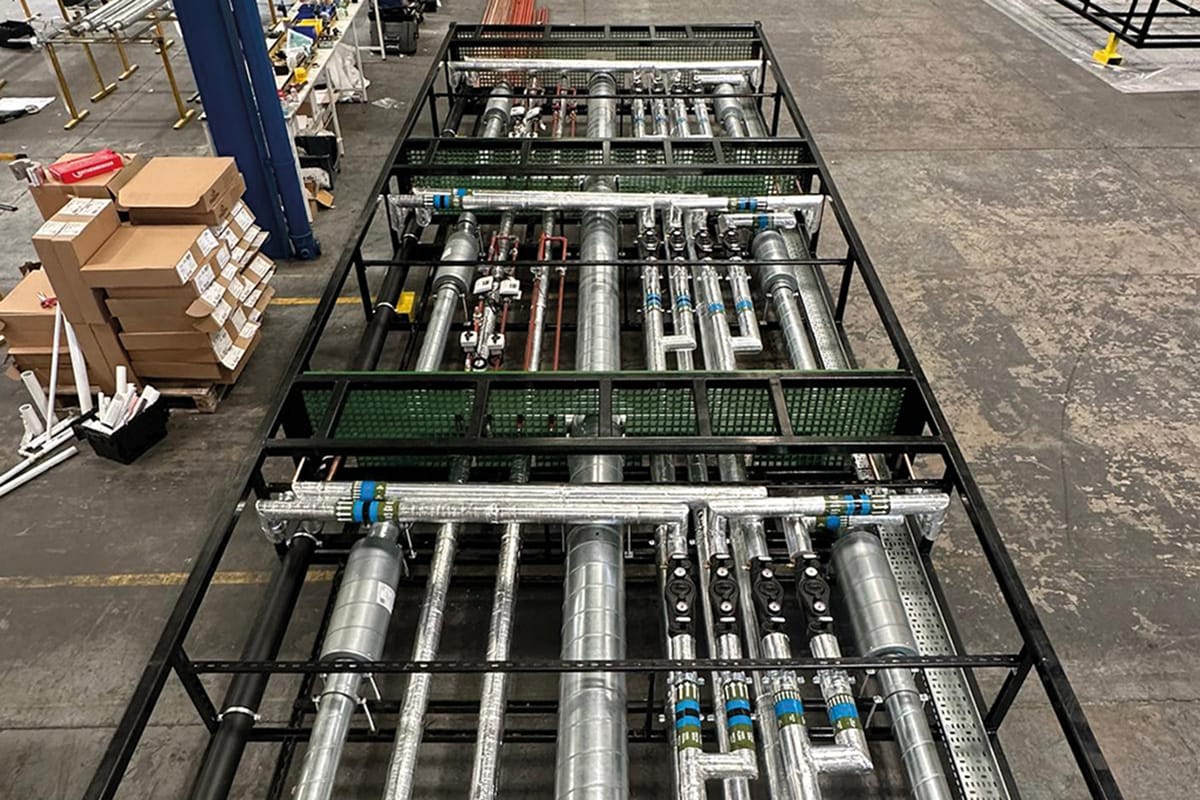
This modular MEP assembly is housed within risers for simple placement and installation.
The answer is that it’s just common sense, according to the Director and MMC lead of CES Group. Cameron, a native of the United Kingdom, started his own consulting practice in 2017 specializing in MEP, sustainability, decarbonization, and commissioning in modular assemblies, and eventually joined forces with CES in North America to expand their efforts worldwide.
CES Group works all around the world, aiming to provide its services in all countries and regions that can benefit from its values and vision. The firm currently has offices in Europe, the United Kingdom, and North America respectively. They’ve worked in countries on the African continent, the Middle East, designing and consulting on prefabricated MEP systems and assemblies as part of larger projects for small island locations outside of places such as Scotland and Japan, and even some places as far north as the Arctic Circle.
Making the Move to Offsite Modular Construction
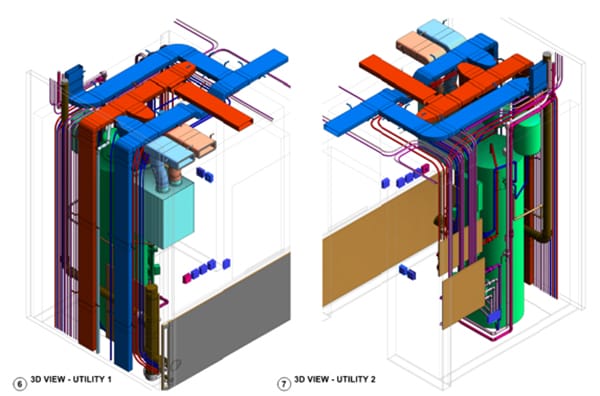
3-D view of modular MEP sub-assemblies for housing units.
While most people think of construction as a gradually layered process, MEP assemblies—such as the modular ones—tend to provide all-in-one installs, like a car factory. A modular MEP product helps developers, architects, and fellow modular manufacturers reach their goals through early integration and planning. MEP assemblies address all the unseen things like electrical, heating, and plumbing when looking at a finalized building. The very nature of MEP assemblies are crucial to any initial prospectus.
“When you think about a car getting built on a factory line, you don’t see somebody get into that car, install the airbag, the gear stick, the speedometer, the steering wheel, and the radio all separately, right?” asks Cameron. “You see them install a completed assembly of the dash, which includes all of that product in one.”
As modular continues to reinvent the construction industry, MEP assemblies are the next step in evolution for those who prioritize efficiency, overhead cost, and build time.
“I would say the problem with the construction industry at the minute is that it’s a bit like an oil tanker, incredibly difficult to change direction,” he said. “And I think that’s what they’ve got to be prepared for is, ‘let’s prepare to innovate and do something a little bit different.’ I think people like to stick with what they know because they feel safe.”
Cameron looks to leaders in the automotive and aerospace industries as inspiration for pushing others into newer arenas of thought and experimentation, especially with MEP. CES Group’s worldwide reach helps developers by saving overhead costs, meeting sustainability goals, and shortening deadlines with prefabricated mechanical, electrical, and plumbing assemblies.
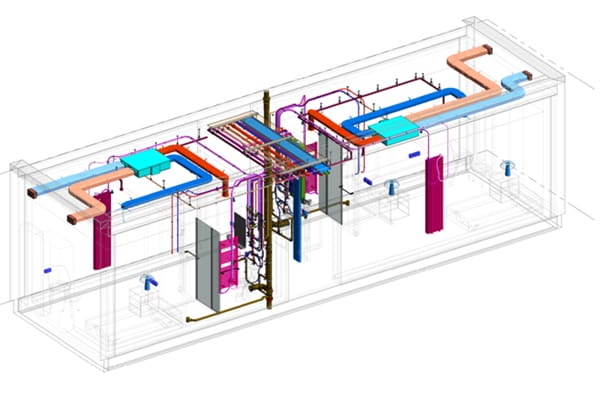
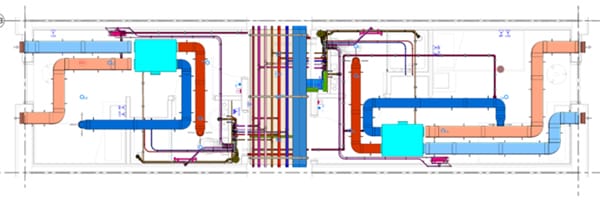
3-D and 2-D views of modular MEP sub-assemblies for hotel units.
Speeding Up Construction with Modular MEP Assemblies
A lot of onsite construction depends on moving pieces and refined schedules to ensure ideal working conditions for the next tradesperson to come in. Modular MEP moves a good portion of the work from onsite to a factory floor where everyone can work, troubleshoot, and test their portions of the MEP module or assemblage. All of this improves the speed and ensures the delivery of a timely product.“
I believe MEP is probably the most important part of any building, but of course, an architect would disagree, and so would a structural engineer and so would an interior designer,” said Cameron. “99.9 percent of the time you never see the MEP because it’s hidden behind walls or hidden above ceilings and it’s very much out of sight, out of mind. So the efficiency comes where it can be standardized and be the same everywhere. And the reason for that is that there’s no kind of variation on the factory line or the offsite line.
”Most MEP modules will share many characteristics, as is the nature of all modular and services installations. Cameron says that about 85 to 95 percent of any standard assembly will probably be standardized. That leaves about 15 to five percent of differentiation for building codes, regional, and geographical standards, and other small layout choices.
But aside from standardization efforts, how do modular MEP assemblies improve sustainability, reduce emissions, and benefit the end user?
‘Everything Always Comes Down to the Cost’
Developers stand to gain from the get-go with MEP assemblies, according to Cameron.“
When you build a building, you’ve generally got some form of funding or loan to pay that can cost in the millions. And with any loan, there comes interest—as we well know in the current economic climate—and that interest accrues and sometimes it compounds and [can] potentially cost a fortune,” he said.
“So if a building takes two years to build, you are paying interest for two years, and then you’re paying it off only after two years because you’re starting to sell apartments...Even just speeding up the program with MEP Modularization, there’s the potential that you could finish that building in 12 months.”
These are big amounts of capital left on the table if developers choose to ignore MEP innovations early on in the design process. According to Cameron, one such project was delayed and overwrought with additional costs due to a poorly sized heat rejection plant room. The small size of the room made it difficult for the equipment to work or operate under warranty, on top of doing the basic work of maintaining the cooling and heating of a large property.
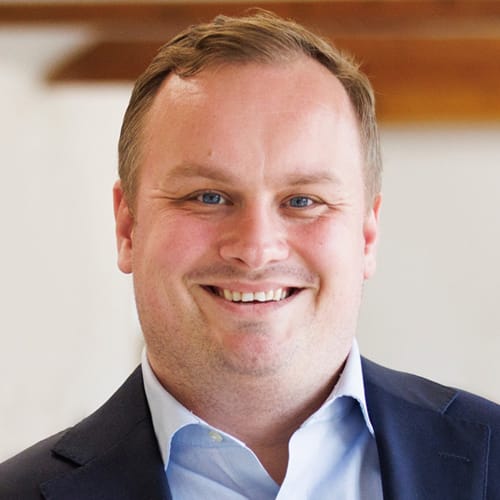
Talking Modular MEP at the 2024 World of Modular
Stuart Cameron, Director and MMC Lead, CES Group
For anyone keen on learning about MEP, Cameron will be speaking at the World of Modular in March with his discussion panel all about modular MEP and what CES Group is doing to advance not only the conversation but the industry at large. His goals are far-reaching, hoping that everyone will find the panel to be informative and inspiring.
"Basically, I’d like the audience to be as wide as possible,” he said. “[But] sometimes it’s really nice also to have students in attendance, they think of things that we don’t think of and provoke a discussion through questions and answers. There’s always opportunities to grow, to learn, to innovate, and we like that to be a kind of circular discussion.”
Shortening the time to completion is definitely important, but needs are shifting in the residential and building industry. Sustainability has become the clarion call for all developers, designers, manufacturers, and architects to rally behind. And for Cameron, MEP is no different.
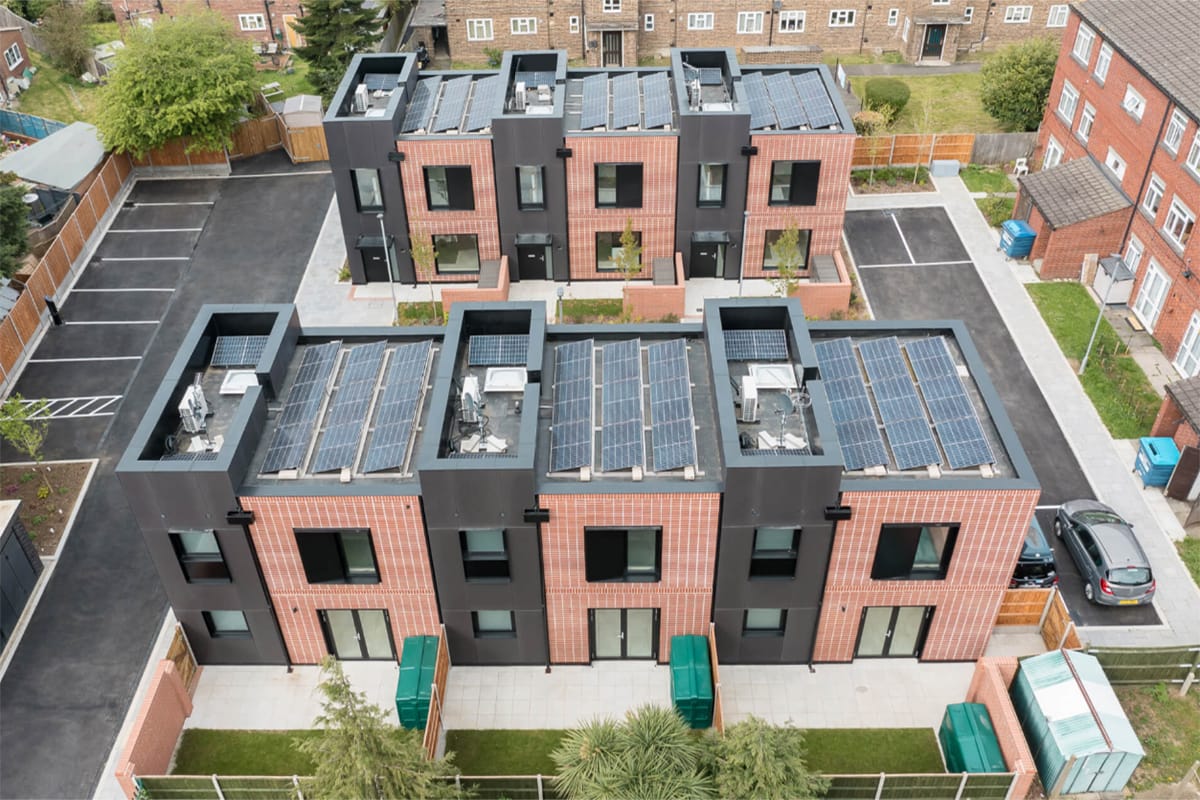
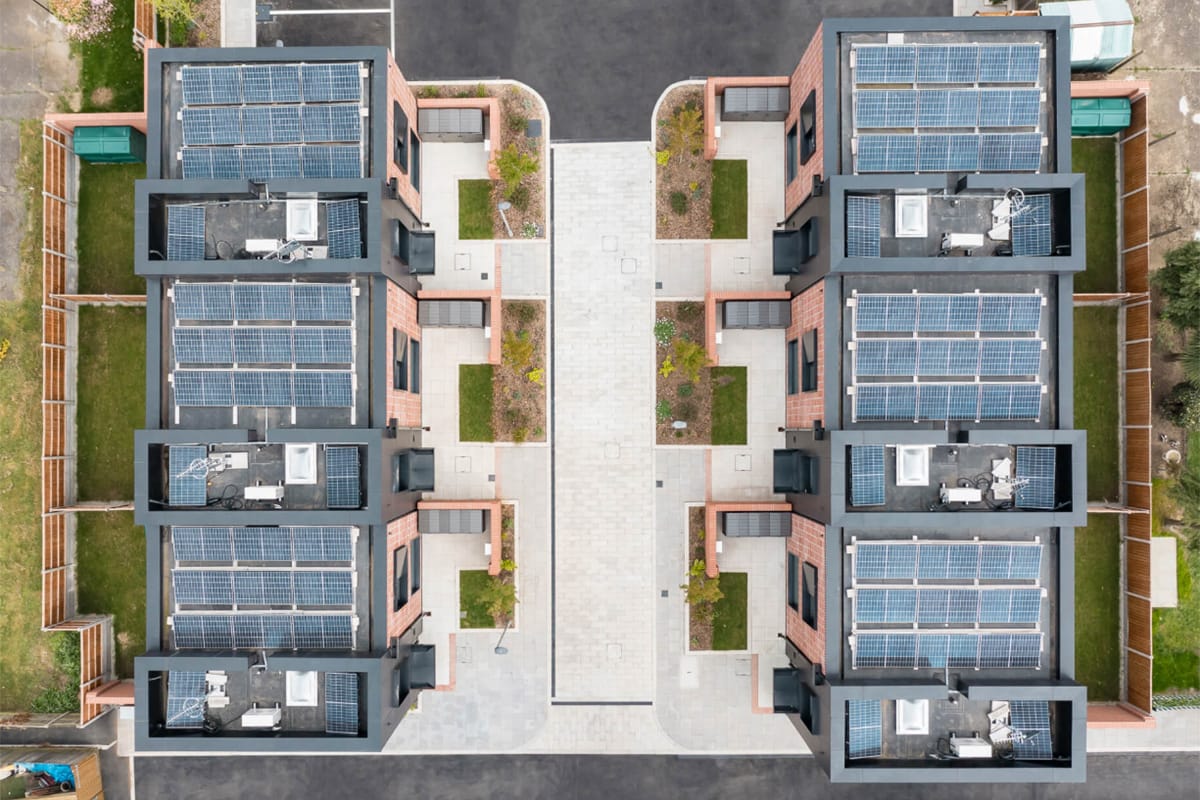
Meeting Sustainability Goals and More With Modular MEP
The other part about modular MEP and assemblies is that they can also help answer some more pressing needs for existing buildings. Decarbonization and retrofitting of existing buildings is part of Cameron’s work, as CES Group helps towns, cities, and local governments with their affordable housing needs. Currently, they are providing services to the Regional Municipality of Peel, a part of the Greater Toronto Area in Southern Ontario, Canada.
Cameron says that so far they’ve been asked to review everything “from gas fired boilers, to building fabric [like cladding, insulation and other structural materials], and glazing.” However, with retrofitting, some might be inclined to simply ask for solar photovoltaic panels and call it a day. Cameron says that does not tackle any of the building’s original inefficiencies.
“Putting PV panels on buildings that aren’t very efficient is like feeding a starving person caviar,” he said. “You need to deal with the root cause of the issue before looking at nice to haves.”On top of retrofitting existing buildings, speeding up projects, and saving money, modularized MEP assemblies have caused ripple effects in other places, including:
- a reduction in onsite traffic (less tradespeople on the site, less parking infrastructure issues).
- a reduction in noise pollution.• combined reduction in emissions.
- better safety and health standards, as workers can do floor-level assembly in a factory as opposed to scaffolding or incomplete structures.
“We need to be performing better,” said Cameron. “We need to have better building fabric, and it’s a lot easier to incorporate better performing fabric on a modular build than on a traditional one.”
Benefits for the End User
There are many growing boons to the use of MEP in modular construction, even when the structure is finished and ready for use, says Cameron. He notes one such project located on the Fair Isle, north of Scotland that features modular MEP assemblies built with hotel guests and facilities management in mind. A lot of care was taken to not only ship the fully built assemblies but to set up as quickly as possible on the small island.
One highlight, according to Cameron, is that all control panels and maintenance access points are installed outside of every hotel room. So if something breaks, no guests will have to move, as the main access points are all adjacent in the hallway, retaining business while making repairs or updates.
The Growth of MEP...and CES
Cameron's session at World of Modular is just one part of CES Group’s plans for 2024. Currently, the company is consulting on large decarbonizing projects in North America and Europe. They’re also working with a worldwide retailer with 20,000 locations to “reduce their fitout times from 18 weeks to something a lot shorter.” And there’s the “gigaprojects” in the Middle East, where they are also providing some consulting to innovate alongside other architects and developers.
Even with all these locations in the portfolio for 2024, Cameron is aiming for structures in other far-flung lands—namely, the moon or Mars.
“I would love to do something in the space industry, modular, MEP modular, whatever it is, for buildings on another planet,” he said. “That would complete it for me.”
But he’ll settle for South America and Antarctica first.
About the Author: Karen P. Rivera is a freelance writer and editor with a passion for storytelling. She is a former United Nations-based reporter, with experience covering international breaking news, venture capital, emerging healthcare tech, and the video game industry.
More from Modular Advantage
AI, Faster Sets, and Automation: The Future of Modular is at World of Modular
While the modular building industry has long known that it can be an effective solution to increase affordable housing, the word is slowly spreading to more mainstream audiences. Three presentations at this year’s World of Modular in Las Vegas hope to provide insight and direction for those seeking a real solution to the crisis.
An Insider’s Guide to the 2025 World of Modular
The Modular Building Institute is bringing its global World of Modular (WOM) event back to Las Vegas, and with it comes some of the industry’s best opportunities for networking, business development, and education. Over the course of the conference’s four days, there will be numerous opportunities for attendees to connect, learn, and leverage event resources to get the most out of the conference.
Affordable Housing Now: The Industry’s Best Bring New Solutions to World of Modular
While the modular building industry has long known that it can be an effective solution to increase affordable housing, the word is slowly spreading to more mainstream audiences. Three presentations at this year’s World of Modular in Las Vegas hope to provide insight and direction for those seeking a real solution to the crisis.
Opportunities for Innovation in Modular Offsite Construction
Modular Offsite Construction has already shattered the myth that it only produces uninspired, box-like designs. Architectural innovations in module geometry, configurations, materials, and products make it possible to create visually stunning buildings without sacrificing functionality or efficiency.
Safe Modular Construction with Aerofilm Air Caster Transport
In collaboration with Aerofilm Systems, Heijmans developed innovative skids using air caster technology for moving modules easily and safely. These pallets are equipped with an auto-flow system, making operation extremely simple.
Miles, Modules, and Memes: Building a Modular Network One Flight at a Time
At the end of the day, social media is just another tool for building connections, and like any other tool, needs to be used skillfully to work properly. Use social media thoughtfully, and it will open doors to real opportunities and relationships you didn’t even see coming.
Falcon Structures: Thinking Inside the Box
Some of Falcon’s latest projects include creating container solutions for New York’s Central Park and an East Coast professional baseball team. More and more, Falcon is shipping out container bathrooms and locker rooms to improve traditionally difficult work environments, like those in oil and gas or construction.
UrbanBloc—From Passion to Industry Leader
UrbanBloc specializes in three main categories or markets – what they call “Phase 0” projects, amenities, and urban infill. Clients are often attracted to shipping containers because from a real estate perspective they are considered an asset. Having the flexibility to move and transport these assets allows owners to respond to different circumstances in a fluid manner that they can’t get with standard construction.
The Hospitality Game-Changer
“Hospitality is about more than just providing a service – it’s about delivering an experience,” says Anthony Halsch, CEO of ROXBOX. “And that’s where containers thrive. They allow us to create spaces that are unique, efficient, and sustainable.”
Container Conversions Counts on Simplicity to Provide Critical Solutions
Container Conversions has fabricated and developed thousands of containers for varied projects, including rental refrigeration options, offices, kitchens, temporary workplace housing, and mobile health clinics.