How Air Caster Technology Has Helped Improve Modular Building Manufacturing
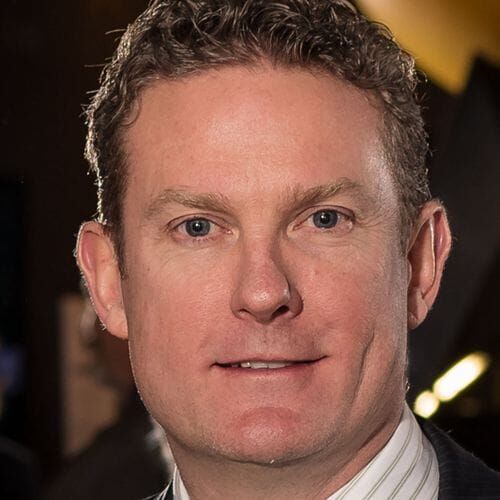
John Massenburg is the President and CEO of AeroGo, Inc.
By manufacturing houses and doing it repetitively, Fading West, a Colorado-based firm, has kept costs down and produced houses more quickly. To accomplish this goal, the company designed a manufacturing facility that can turn around hundreds of modular units, using a breakthrough process that utilizes the adoption of air casters, a low-profile material handling system inspired by hovercraft technology. Traditional systems, like cranes and forklifts, lack the capacity for larger modules, while rail systems are too inflexible and immobile.
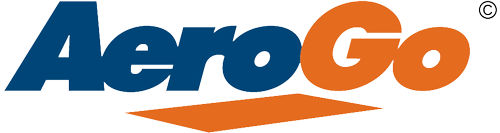
At Fading West, the company uses an unconventional U-shaped production line with nine stations down one row, one in the middle, and nine more stations up the other row. As a result, Fading West doubled its throughput and minimized travel and other forms of waste with consistently positive results.
Transforming the Construction Industry
Modular housing construction firm Fading West Development is anything but fading away. Indeed, the Buena Vista, Colorado-based company, named after an album from American rock band Switchfoot, has seen its success skyrocket in housing construction since its inception. That’s due to its clever and innovative solution to a massive and growing problem: building modular homes, apartments, and other value-engineered residential products in a factory setting to address the nationwide crisis in housing affordability. “I came here to Fading West to ask how we can revolutionize the construction industry to create more affordable housing and get it into the marketplace,” says Sean Brown, Fading West’s vice president of factory operations.
Revolutionize it they did. The Colorado Sun newspaper described Fading West as “a solution to the housing crisis.” Time Magazine even recognized Fading West as one of the 100 Most Influential Companies of 2022—ranking it alongside Amazon and Pfizer.
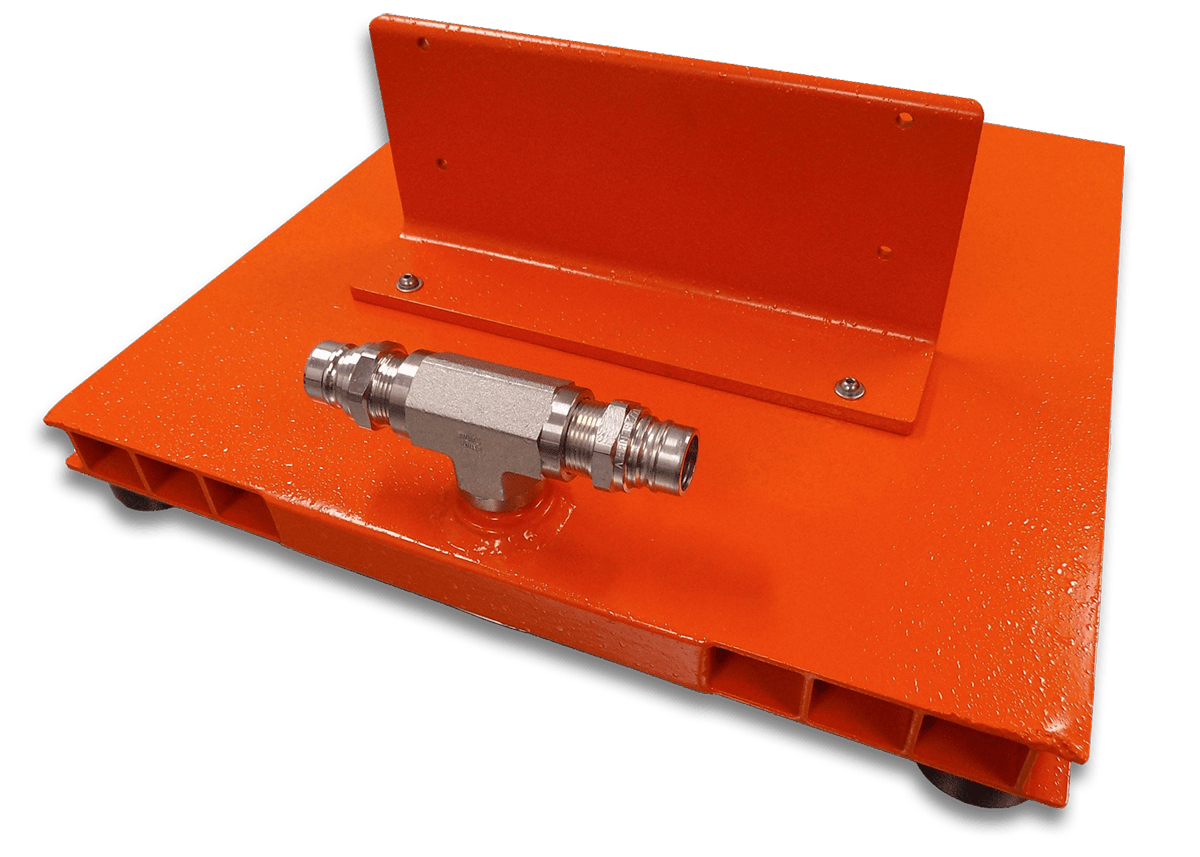
Typical load module for the modular industry allows for quick bolting to the structure through the pre-drilled holes.
What accounts for its stellar success? Efficiency. “By manufacturing houses and doing it in a repetitive fashion, we can keep costs down and we can get the number of houses out quicker,” Eric Schaefer, vice president of sales and strategic partnerships, told the Sun. The result is the company can build a modular three-bedroom home up to five times faster than a traditional stick-built house, with construction costs 15-30 percent lower and market costs at least 25 percent less expensive than comparable stick-built homes.
But what drives that efficiency? The answer might be surprising.
Turning Housing Structures into Hovercraft
The main obstacle for Fading West was designing a manufacturing facility that could turn around hundreds of these modular units, sometimes called “boxes,” quickly and efficiently. Since the company built its 110,000-square-foot factory in Buena Vista in 2021, it had an opportunity to design the perfect manufacturing process from the ground up.
Unfortunately, traditional material handling methods proved intractable in meeting its desired goals. Either they wouldn’t work in the way Fading West wanted, or they wouldn’t work at all. For example, cranes and forklifts lacked the capacity for larger modules, while rail systems were too inflexible and immobile. Fading West didn’t want a straight-line manufacturing process because that would require too large a facility and place incoming and outgoing areas on opposite ends of the facility, necessitating two staging areas. It also would force unnecessary travel for workers to monitor the process or move equipment or resources.
The breakthrough came with the adoption of air casters, a low-profile material handling system inspired by hovercraft technology. By inflating a series of donut-shaped bags with compressed air, the massive modules can hover above the ground, allowing for easy, nearly frictionless maneuverability. “In a 38-foot-long-house, we use six air casters,” says Brown. “With 40 psi, we lift the house up and, with four people, one at every corner, we just push the house across the stages. It is not difficult to move entire houses very smoothly.”
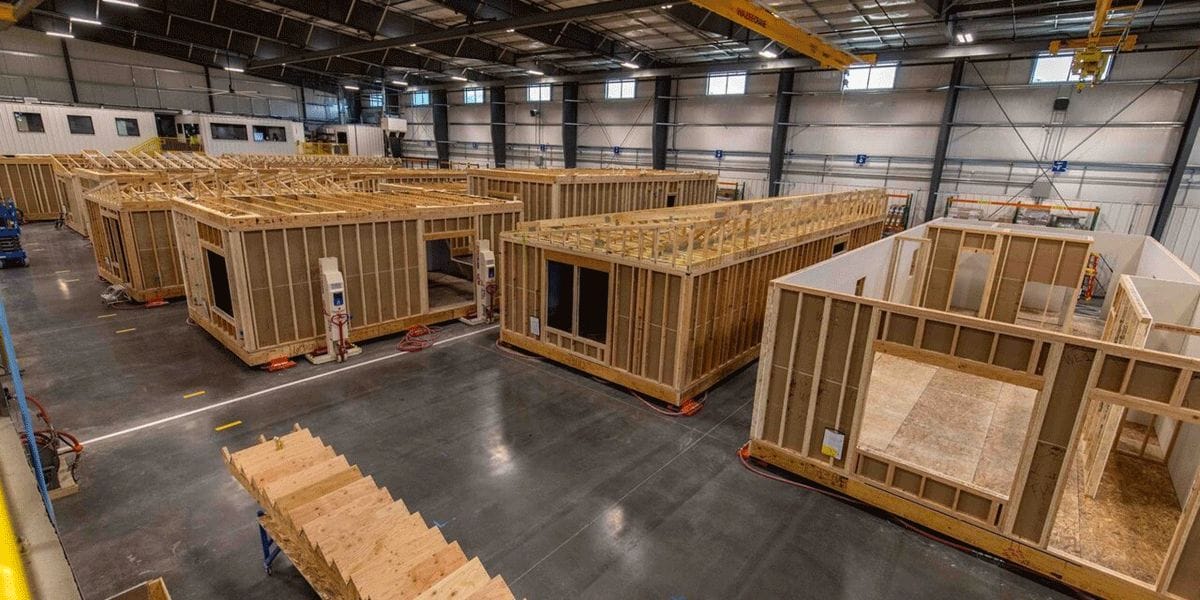
Fading West’s production line can be moved safely and efficiently while floating on air.
U-shaped? You Bet
Better yet, the air casters made it possible to create an unconventional U-shaped production line with nine stations down one row, one in the middle, and nine more stations up the other row. That way, Fading West could double throughput, minimize travel and other forms of waste, and move structures in and out through the same opening. “We can move the entire factory through all 19 stations in the line in under 30 minutes,” says Brown. It enabled Fading West to build the assembly process around a central mezzanine holding tooling and other resources, with elevated offices offering complete visibility over the whole manufacturing line, all at once.
Notably, air casters also mean flexibility, not just in terms of movement but also in terms of change. For example, one structure might be 56-feet-long and another 76-feet-long. Air casters allow the company to easily accommodate a variety of shapes and sizes of boxes and then make changes on the fly. Even better, if Fading West needs to pause production on one unit to handle one-off issues, it can simply float the box to the side and allow the remainder of the production line to continue moving uninterrupted. When ready, employees can seamlessly float the unit back into production.
Solving Real-world Problems While Floating on Air
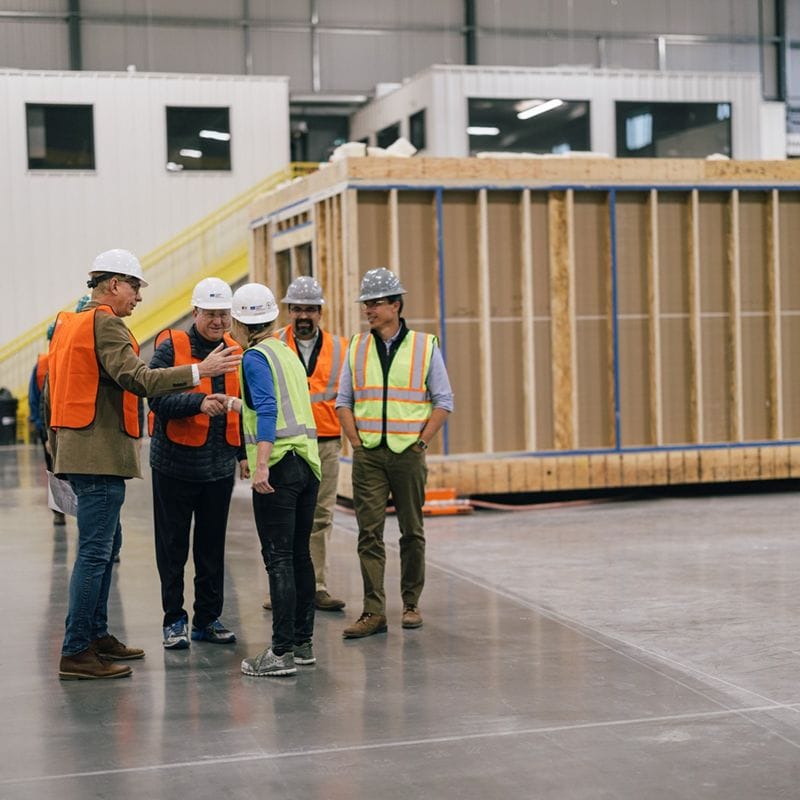
The team at Fading West discusses their efficient production line.
Tackling housing affordability is an ambitious goal, but with its ingenious manufacturing setup, Fading West has found the formula to produce high-quality housing quickly and affordably. Air casters play a quiet but critical role in this formula for success. With their ease of use, low cost, and unbeatable flexibility, Fading West designed a factory from the ground up that could maximize output and adaptability without disruption while minimizing waste. Ultimately, using air casters means Fading West can produce over 700 modular homes and apartments annually.
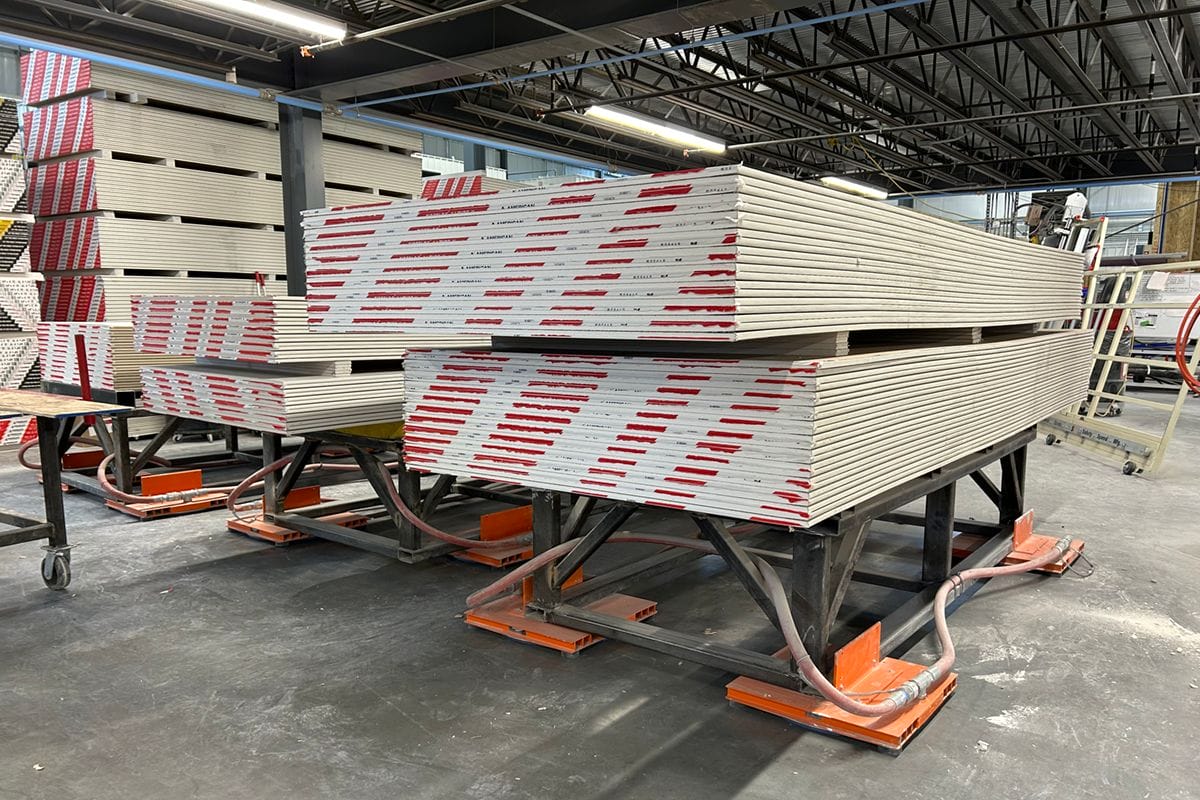
Moving building materials across the shop floor with air bearings.
It’s not just air casters themselves that matter; it’s also the company that provides them. “AeroGo was the only partner that could meet all of our needs,” says Brown. “I wish they could have provided everything in this plant. AeroGo is the only one who delivered what was promised and on time.”
AeroGo has made an impression—and not just on factory workers. “The AeroGo product is so nice, so unique, it’s commented on by every single person that walks through the factory,” says Brown. Playing a part in making housing affordable again and impressing passers-by? That’s just the everyday reality of AeroGo air casters making otherwise impossible moves happen.
Facilitating Growth with Air Caster Technology
Competition in the construction industry is fierce. Historically, two out of these three customer demands—economy, speed, and quality—were adequate. In today’s world, everyone wants all three and then some. Using modern air caster technology in the modular building sector is one way to help meet the fast-moving, high-demand expectations of the industry and its expected growth through 2024 and beyond.
More from Modular Advantage
AI, Faster Sets, and Automation: The Future of Modular is at World of Modular
While the modular building industry has long known that it can be an effective solution to increase affordable housing, the word is slowly spreading to more mainstream audiences. Three presentations at this year’s World of Modular in Las Vegas hope to provide insight and direction for those seeking a real solution to the crisis.
An Insider’s Guide to the 2025 World of Modular
The Modular Building Institute is bringing its global World of Modular (WOM) event back to Las Vegas, and with it comes some of the industry’s best opportunities for networking, business development, and education. Over the course of the conference’s four days, there will be numerous opportunities for attendees to connect, learn, and leverage event resources to get the most out of the conference.
Affordable Housing Now: The Industry’s Best Bring New Solutions to World of Modular
While the modular building industry has long known that it can be an effective solution to increase affordable housing, the word is slowly spreading to more mainstream audiences. Three presentations at this year’s World of Modular in Las Vegas hope to provide insight and direction for those seeking a real solution to the crisis.
Opportunities for Innovation in Modular Offsite Construction
Modular Offsite Construction has already shattered the myth that it only produces uninspired, box-like designs. Architectural innovations in module geometry, configurations, materials, and products make it possible to create visually stunning buildings without sacrificing functionality or efficiency.
Safe Modular Construction with Aerofilm Air Caster Transport
In collaboration with Aerofilm Systems, Heijmans developed innovative skids using air caster technology for moving modules easily and safely. These pallets are equipped with an auto-flow system, making operation extremely simple.
Miles, Modules, and Memes: Building a Modular Network One Flight at a Time
At the end of the day, social media is just another tool for building connections, and like any other tool, needs to be used skillfully to work properly. Use social media thoughtfully, and it will open doors to real opportunities and relationships you didn’t even see coming.
Falcon Structures: Thinking Inside the Box
Some of Falcon’s latest projects include creating container solutions for New York’s Central Park and an East Coast professional baseball team. More and more, Falcon is shipping out container bathrooms and locker rooms to improve traditionally difficult work environments, like those in oil and gas or construction.
UrbanBloc—From Passion to Industry Leader
UrbanBloc specializes in three main categories or markets – what they call “Phase 0” projects, amenities, and urban infill. Clients are often attracted to shipping containers because from a real estate perspective they are considered an asset. Having the flexibility to move and transport these assets allows owners to respond to different circumstances in a fluid manner that they can’t get with standard construction.
The Hospitality Game-Changer
“Hospitality is about more than just providing a service – it’s about delivering an experience,” says Anthony Halsch, CEO of ROXBOX. “And that’s where containers thrive. They allow us to create spaces that are unique, efficient, and sustainable.”
Container Conversions Counts on Simplicity to Provide Critical Solutions
Container Conversions has fabricated and developed thousands of containers for varied projects, including rental refrigeration options, offices, kitchens, temporary workplace housing, and mobile health clinics.