Seizing the Modular Construction Opportunity
An executive summary from the CSA Group
Canada’s fast growing housing shortage has received significant attention recently. The need to build more facilities like hospitals and long-term care homes to prepare for an aging population is also looming. Could the potential of modular construction help accelerate the pace of building?
Currently, 4.3 million more homes are needed to help alleviate affordability and access issues, particularly for people with low incomes, students, and those who are unsheltered. Changing demographics mean that Canada will also require 199,000 new beds in long-term care facilities by 2035. But with an estimated 700,000 workers in the skilled trades expected to retire by 2028 and construction costs having risen by 51 per cent in recent years, new approaches are needed to meet this increasing demand.
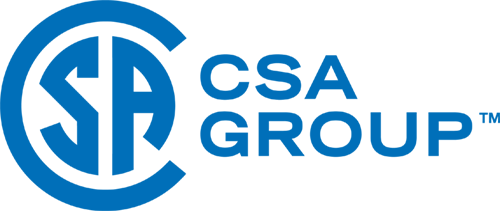
The CSA Public Policy Centre’s new report, Seizing the Modular Construction Opportunity, highlights how innovative modular methods can help to bring various building forms—from single unit housing to complex high-rises—online more quickly. Owing to efficient manufacturing practices and controlled factory environments, modular can achieve completion rates that are 25% to 50% faster than conventional construction approaches.
Under the right circumstances, modular also has the potential to realize substantial cost-savings—upwards of 20%. And as Canada works towards greater circularity in the construction sector, modular’s standardized components allow for greater reuse and recycling which offer further opportunities to meet national sustainability goals. Though modular construction has seen strong growth in recent years—increasing from 2.14% of all construction starts in North America in 2018 to 6.0% in 2022—there are still several challenges hindering greater uptake in Canada.
The most fundamental barrier to modular construction is that it is poorly understood. From developers to tradespeople and key professionals like architects, engineers, and financiers, there is a general lack of awareness and technical know-how when it comes to designing, financing, and building modular projects.
Secondly, Authorities Having Jurisdiction (AHJs)—for example, the municipalities that oversee product safety, issue permits, and undertake inspections, or the provinces that approve changes to building codes—have limited experience with modular projects. This too often results in longer review and approval times, defeating the speed advantages offered by modular methods.
Thirdly, inconsistencies and gaps in building codes across jurisdictions make for a complex regulatory environment—particularly challenging when modular units are frequently manufactured in one province and transported to another for assembly. Building codes are also mostly silent on standards around transport, placement, and lifting of modules, which are important and unique aspects of factory-made buildings.
Finally, the way the public sector procures and finances construction projects is often at odds with how modular construction works. For example, large public projects like hospitals or schools usually come with highly prescribed architectural and engineering specifications that are more difficult for modular manufacturers to meet, given their set factory limitations. And while customization is possible to fit desired criteria, this can limit the potential cost savings that could otherwise have been achieved.
On the financing side, because as much as 80% of a modular project is completed in a factory, manufacturers require a much larger payment upfront to obtain needed materials and build modules concurrently. However, current practices among both private and public lenders rarely align with this approach, severely limiting the availability of financing options for modular projects.
If modular construction is to help Canada meet its unmet and growing infrastructure needs more quickly, cost effectively, and sustainably, governments at all levels must take action to enable an environment in which its potential can be maximized.
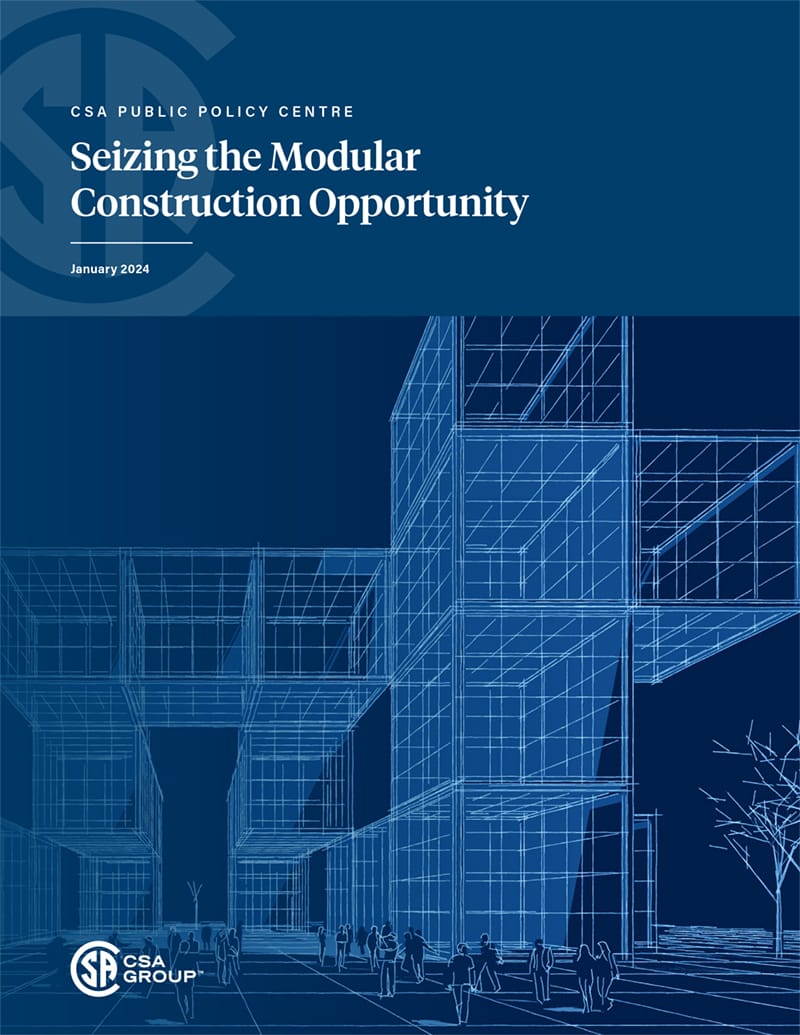
Download the complete version of the CSA Public Policy Centre’s new report, Seizing the Modular Construction Opportunity.
As a first step, provinces and territories can issue guidance materials and training to educate AHJs on modular methods and help clarify processes and responsibilities around certification, inspections, and approvals. This would allow projects to move forward more quickly and safely. Encouragingly, Ontario and British Columbia have already developed such materials.
Building code changes that enable modular construction are also needed. For example, the main standard used to certify modules off-site (CSA A277) is enforced to varying degrees across provinces in Canada, and its classification as an ‘administrative document’ within Canada’s National Building Code also creates uncertainty for local inspectors. While the most comprehensive solution would be consistent and harmonized recognition of CSA A277, an initial step would be to enhance education about the standard at the municipal level. Further, the recognition of CSA Z250—which addresses transport, lifting and placement of modules—in the National Building Code as well as codes at the provincial/territorial level could also support needed innovation in the building sector.
Next, governments at all levels should review their procurement practices to ensure bidding processes are more accessible to modular manufacturers and involve them earlier in the design and planning phases. More collaborative or integrated procurement approaches than the traditional ‘design-bid-build’ approach could help to secure greater cost-certainty and quality of construction, without compromising on the essential requirements of a given project.
Another critical action the federal and provincial governments could pursue is revision to the financing criteria for housing developments to better align with the reality of modular’s front-loaded project costs. The federal government in particular has set aside billions of dollars for affordable housing development through the National Housing Strategy. This could be made more accessible to modular builders who have unique advantages in rapidly producing buildings with efficient floor plans.
Finally, more research and evidence are needed to inform policymakers, regulators, and private developers of modular’s functions, merits, and limitations. Though evidence from other countries is demonstrating important benefits, decision-makers in the public and private realm are more likely to be persuaded by Canadian experience.
Modular construction presents real opportunities to help Canada meet key infrastructure demands—especially in the housing sector—more quickly, sustainably, and cost-effectively. However, this can only be achieved with broader awareness and understanding of modular methods, greater regulatory consistency and guidance, and more compatible procurement and financing practices—all underpinned by an expanding evidence base. All levels of government have important roles to play in enabling this future and ensuring the full potential of modular construction is seized.
More from Modular Advantage
How Rebel Concept Harnesses AI as a Design Tool to Improve the DFMA Process
“The complexity of projects and the size of project are so large, and the technology is so complicated that AI would do it so much faster than we are,” says Kris Droszcz, CEO at Rebel Concept. “Everybody’s struggling to control the manufacturing processes according to the design. And I think that’s what AI will do.”
One Answer from AI Can Provide Innumerable Opportunities, says Stack Modular’s Jim Dunn
The Stack AI Engine is not fully functional yet, but it offers an unlimited number of productivity benefits. Currently, the company is using AI for cost estimates, most recently for a project out in California.
GrayWolf: Building the Future of Modular Data Centers to Power the AI Revolution
The growth of artificial intelligence (AI) and cloud-based applications has created an urgent need for data centers capable of managing massive amounts of data. As businesses across industries increasingly rely on digital infrastructure to power their AI tools, the demand for data centers has skyrocketed.
Artificial Intelligence: Yes, it is a Construction Game-Changer
Much like other sectors of the economy, AI is reshaping construction, revolutionizing how projects are planned and executed across the country. While it is obvious that AI cannot do certain things by itself, like laying bricks, paving roads, or shingling roofs, its impact stands to be both massive and positive.
The Potential and Possibilities of AI for Offsite
AI is everywhere. Many industries have incorporated AI into business as usual with new organizational structures and new dependencies to be more efficient and to automate repetitive tasks. Offsite construction will not be immune to AI’s ubiquity. The technology offers unique benefits to the offsite building process.
Moving from AI Hype to an AI Advantage
Learning about AI will help you see past the overinflated hype and identify the opportunities specific to your own business. Learning about AI is like peeling an onion – each layer reveals something new, and occasionally it might make your eyes water. But in the end, you’ll have all the ingredients you need to cook up some real innovation in your organization.
The Blueprint for Smart and Ethical AI Integration in Your Business
The journey toward smart and ethical AI integration involves crafting a strategic vision that aligns AI’s transformative potential with your organizational goals. True success with AI is measured by its capacity to enhance human capabilities, foster sustainable growth, and generate value for all stakeholders while actively avoiding ethical pitfalls and harmful risks.
Five Factors for Success When Shifting Your Business to Modular
As labor, competitive and cost factors push more contractors and developers to embrace the opportunity to go modular as a first choice and not a last resort, it’s become clear that adopting this new model requires more than just a willingness to make it happen. Here are five factors to consider as your company moves to a modular construction model:
UniCool-Edge: Optimized Cooling Solutions for Modular and Edge Data Centers
In an industry where efficiency, scalability, and security are crucial, the UniCool-Edge™ system is a revolutionary solution for modular data center manufacturers. By offering external mounting for maximum space utilization, energy-efficient cooling, and pre-commissioned reliability, UniCool-Edge helps manufacturers stay ahead in the rapidly evolving AI-driven data center market. As edge data centers continue to expand, solutions like UniCool-Edge will play a vital role in supporting the next generation of modular data centers and their data center infrastructure.
Building Skills in a Virtual World: Immersive Training for the Modern Workforce
As both the hardware and software for developing and deploying XR applications continue to become more affordable, the investment in this technology as a training tool is increasingly appealing. XR also offers several other benefits, including performing potentially hazardous tasks in a safe environment and acquiring new skills without the immediate need for physical materials.