Offsight’s Digital Certification Program Can Accelerate Modular Industry Growth
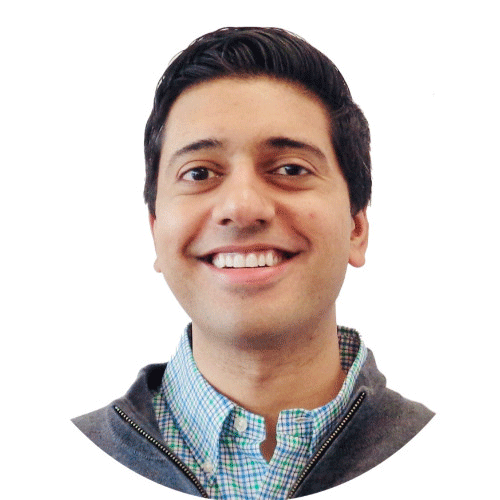
Vikas Murali is the CEO & Co-Founder at Offsight
When it comes to modular and offsite construction the benefits and advantages are widely known and accepted. Industry analysts have forecasted that the traditional construction value chain is ripe for disruption and a $256 Billion annual profit pool can be accessed by new offsite and modular businesses.
Analysis by McKinsey & Company already confirms that modular techniques accelerate construction timelines by 20 to 50 percent and can reduce overall costs by 20 percent. The benefits of modular construction over traditional methods are obvious and include faster project delivery, reduced overall project cost, and far greater overall project quality excellence. However, in the same analysis the authors directly address the key factors that must be addressed to accelerate modular adoption:
“The benefits of modular buildings come from the industrialization of key construction tasks. Modular companies aim to standardize, streamline, and automate big parts of the value chain, allowing buildings to be treated like products rather than projects. To get that right, modular players need best-in-class manufacturing capabilities, including sophisticated digital design platforms and lean, efficient production lines.”
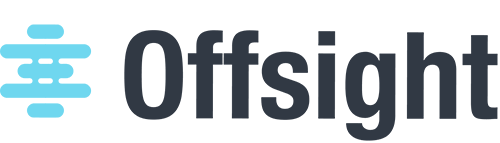
In other words, simply moving work from a traditional job site into a factory doesn’t ensure that the true benefits of modular and offsite construction including speed, cost savings, and quality excellence are achieved. In order to truly realize the return on investment of offsite construction, companies must run a highly efficient manufacturing and production process. Investing in digitization and training your workforce to capitalize on the move to modular will be the key to truly harnessing the full potential and value add of offsite construction.
Going Digital, Getting Certified & Capturing The Full ROI of Modular Construction
At Offsight, we’ve built a solution specifically for the modular, offsite, and prefab industry. Our platform is robust enough to manage all forms of building project manufacturing over the full scope of prefab and modular product lines, from fully volumetric modules and bath pods to panels, trusses, and floor cassettes.
By developing a solution specific to the needs of the industry, we meticulously considered each aspect of managing a modular and prefab project at the factory level and built a full feature set to address the entire scope of factory operations. This includes Production & Quality Tracking, Reporting & Auditing, Advanced Analytics & Insights, Labor Tracking & Timesheets and Materials & Inventory Management.
To achieve the full potential from Offsight, our customers needed to drive adoption internally through educating their workforce and developing internal champions to learn our platform and train others. After witnessing our most successful modular customers deploy and expand our solution to their other factories successfully, Offsight was able to track progress and quality across several major commercial projects in parallel. We incorporated these insights into a digital certification and training program curated to foster shared knowledge among industry leaders within our customer base.
Related Listening:
The Value-Add of Offsite Construction Project Management Software w/ Offsight
Vikas Murali, CEO of Offsight, discusses the advantages that offsite factory owners and manufacturers can realize through the use of customized project management software. Vikas also talks about the development and capabilities of his company's Offsight software platform, as well as about how his background in enterprise-level software development—combined with the modular and offsite industry experience of his key staff—has led to Offsight's growth as an industry software solution.
To achieve the full potential from Offsight, our customers needed to drive adoption internally through educating their workforce and developing internal champions to learn our platform and train others. After witnessing our most successful modular customers deploy and expand our solution to their other factories successfully, Offsight was able to track progress and quality across several major commercial projects in parallel. We incorporated these insights into a digital certification and training program curated to foster shared knowledge among industry leaders within our customer base.
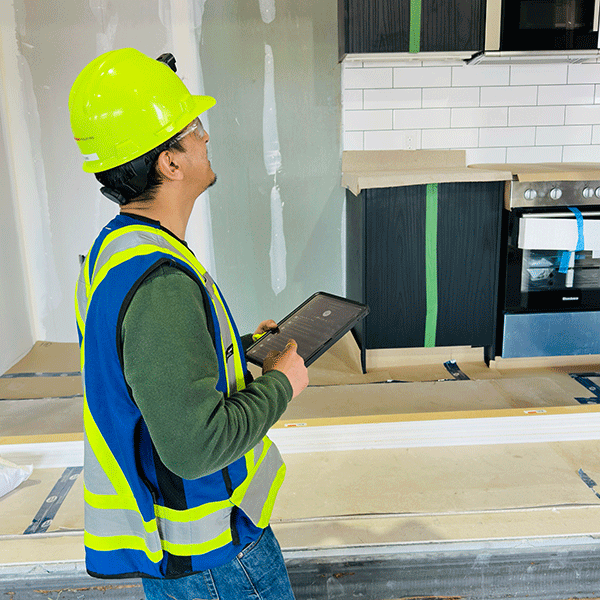
Commercial modular builder Z Modular utilizes Offsight to manage projects across multiple factories in the U.S. and Canada.
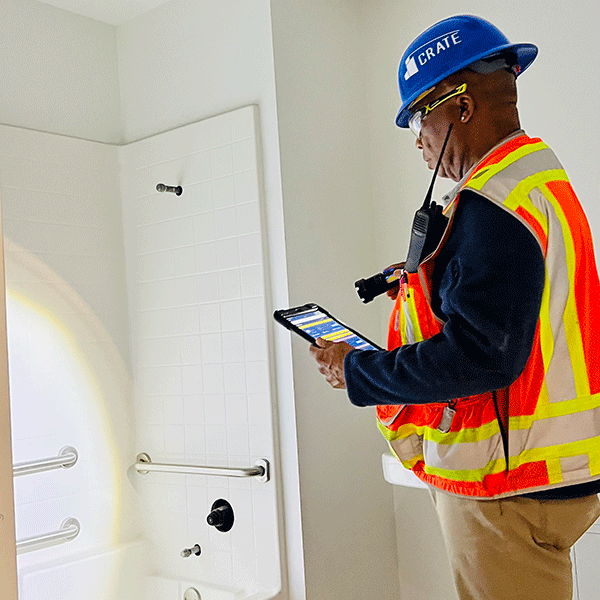
Multifamily residential builder CRATE Modular, leverages Offsight to manage full factory operations and production.
Therefore, we launched the Offsight Certification Program in January 2024. Our program is designed to equip production managers, quality inspectors, plant managers, and operators with a deeper understanding of how technology and digitization can be a game-changer in driving process improvements and productivity benefits, which will ultimately allow our customers to capture the full value of modular and offsite construction.
As Offsight Solutions Engineering Manager, Jason Dixon states: “Before joining Offsight, I held quality manager and operations roles at modular manufacturing companies. It was my responsibility to implement Offsight across our workforce of 50+ operators and managers. My biggest takeaway was the importance of training a technical lead responsible for learning how Offsight works and the value it can provide the factory. Our Offsight Certification Program will enable our clients to better train and recognize these internal leads and drive technological changes throughout the company.”
Our program consists of two major certifications that help operators, managers, and inspectors apply digitization to all aspects of factory operations. The Offsight Factory Operations Project Management Certification trains modular industry leaders in leveraging Offsight’s production, quality, analytics, and material and labor tracking capabilities to manage overall prefab project progress, collaborate with other project stakeholders, and accurately manage project costs. The Offsight Digital Quality Building Inspections Certification is designed to help quality personnel, managers and accredited building inspectors leverage digitization to manage complex code conformance and tracking, including mandatory and State-regulated reporting and auditing.
Through both programs, modular professionals learn how digitization can be a game-changer in driving modular construction adoption and delivering on the innate benefits the process offers.
As Offsight customer, Keizah Coye, Plant Project Manager at CRATE Modular, states: “As a production leader, I interact with Offsight daily. It’s a very robust solution that helps manage all factory operations and provides crucial visibility to our management. Their Certification and training program is exactly what production leaders in the modular, offsite, and prefab industry, like myself, need to quickly get up to speed on how Offsight’s technology can be utilized to meet our major operations and project goals and scale our business.”
At Offsight, our vision is to be the leading provider of digital tools and products that empower companies to unlock the complete potential of modular and offsite construction. We invite you to join us on this journey and hope that we can partner with you to help push the industry forward.
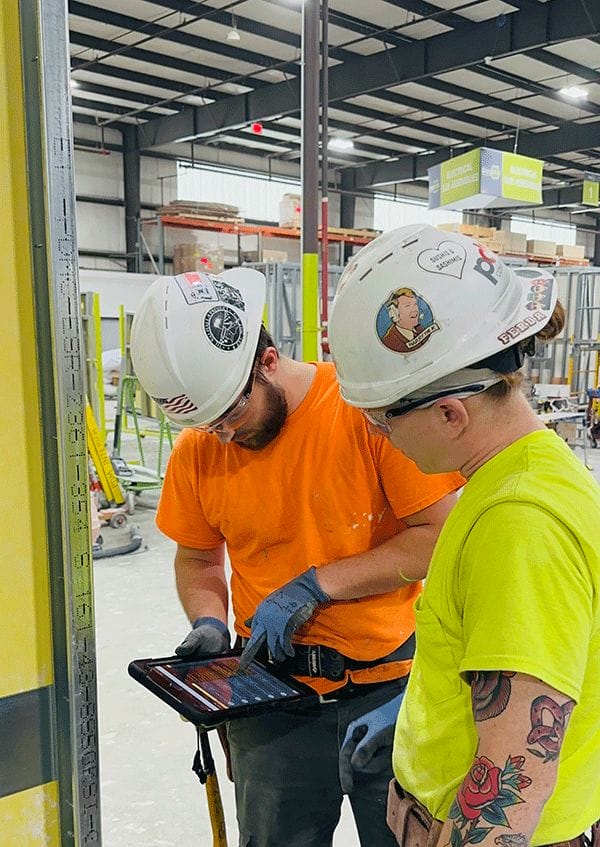
Specialty contractor PDM Constructors manages production across thousands of modular bath pods for major healthcare projects, through Offsight.
More from Modular Advantage
Oregon’s Prevailing Wage Proposal: A Wake-Up Call for Modular Construction
Should House Bill 2688A become law, building projects would increase in price, face longer completion timelines, and produce significantly more waste. The bill also incentivizes contract awards to out of state businesses who would not reinvest their earnings into the local Oregon economy.
Behind the Design of Bethany Senior Terraces, NYC’s First Modular Passive House Senior Housing Project
As more developers seek to meet new regulations for energy efficiency, the team at Murray Engineering has set a new record. With the Bethany Senior Terraces project, Murray Engineering has helped to develop NYC’s first modular structure that fully encompasses passive house principles — introducing a new era of energy efficiency in the energy-conscious city that never sleeps.
How LAMOD is Using Modular to Address Inefficiency, Sustainability, and the Future of Construction
As developers, designers, and contractors seek to understand the evolving needs of the modular industry, no one is as well-versed in the benefits of going modular as Mārcis Kreičmanis. As the co-founder and CBDO of LAMOD in Riga, Latvia, Mārcis has made it his ultimate goal to address the inefficiencies of traditional construction.
From Furniture Builder to ‘Activist Architect’: Stuart Emmons’ Unique Journey
Stuart Emmons was fascinated by buildings at a young age. He remembers building sand cities with his brother during trips to the Jersey shore. His father gave him his first drawing table at the age of ten. Today, he is an experienced architect who received his FAIA in June 2025. The road he took is unique, to say the least.
Forge Craft Architecture + Design: Codes, Contracts, and Intellectual Property
Founding Principal and Director of Modular Practice for Forge Craft Architecture + Design, Rommel Sulit, discusses the implications of codes, contracts, and intellectual property on
modular construction.
Eisa Lee, the “Bilingual” Architect
Now as the founder of XL
Architecture and Modular Design in Ontario, Canada, she applies not just her education as a traditional architect but an entire holistic view on modular design. It’s this expansive view that guides her work on being a true partner that bridges the gap between architects and modular factories as they collaborate on the design process.
Tamarack Grove Engineering: Designing for the Modular Sector
The role of a structural engineer is crucial to the success of a modular project, from initial analysis to construction administration. Tamarack Grove offers structural engineering services — project analysis, plan creation, design creation, and construction administration — for commercial, manufacturing, facilities, public services, and modular. Modular is only one market sector the company serves but it is an increasingly popular one.
Engineer Masters the Art of Listening to His Customers
Since founding Modular Structural Consultants, LLC. in 2014, Yurianto has established a steady following of modular and container-based construction clients, primarily manufacturers. His services often include providing engineering calculations, reviewing drawings, and engineering certification
Inside College Road: Engineering the Modules of One of the World’s Tallest Modular Buildings
College Road is a groundbreaking modular residential development in East Croydon, South London by offsite developer and contractor, Tide, its modular company Vision Volumetric (VV), and engineered by MJH Structural Engineers.
Design for Flow: The Overlooked Power of DfMA in Modular Construction
Unlocking higher throughput, lower costs, and fewer redesigns by aligning Lean production flow with design for manufacturing and assembly.