From a Basement Office to a Team of Modular Experts
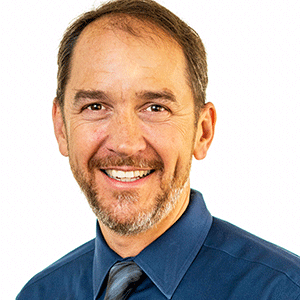
Dean Dalvit is the founding principal at EVstudio
Starting from his basement office 17 years ago, Dean Dalvit leveraged his professional training in both architecture and engineering to develop EVstudio into a fully integrated architecture and engineering firm. Now with over 120 staff members in four offices, including two in Colorado, one in Boise Idaho, and one in Austin Texas, the firm is a regional design powerhouse.
“We’re organized around having what we call our horizontals,” Dalvit said, “which are our design disciplines: architecture, structural engineering, mechanical/electrical/plumbing, and civil engineering. And then each of those horizontals support our vertical design studios, which are based on market or project type,” he added.
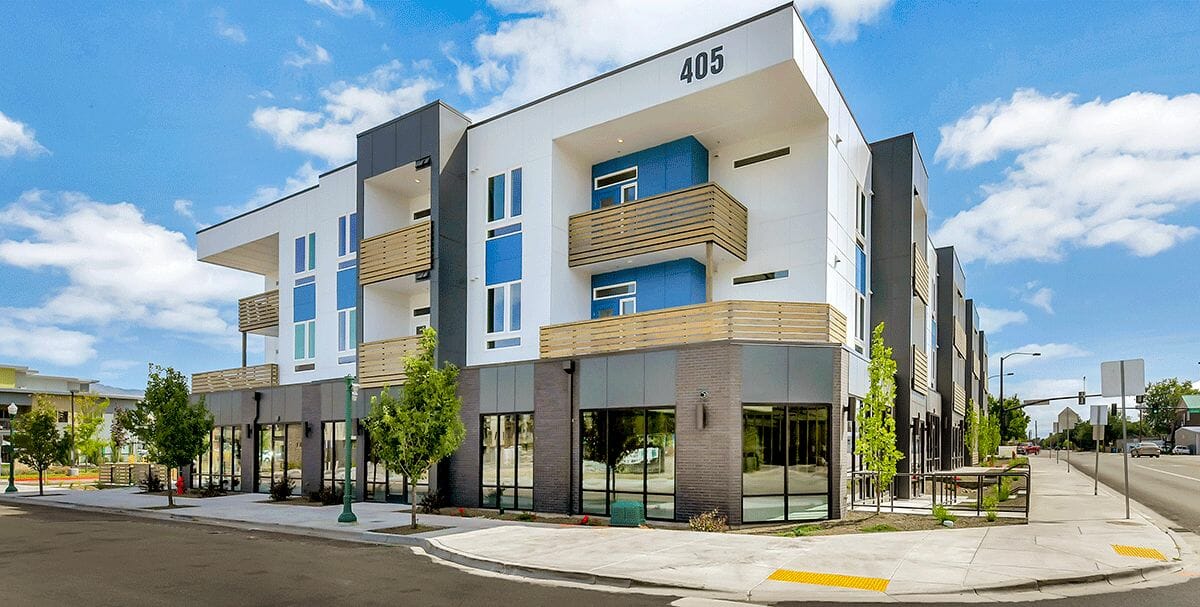
A mixed-use modular housing development designed by EVstudio.
A Multidisciplinary Approach
“The modular offsite construction project type actually found EVstudio because of our company’s integrated multidisciplinary approach,” Dalvit said, which led the company to develop a focused design studio around that project type.
Over the years the company has accepted projects from small field inspections to multi-hundred-unit residential projects, as well as some unique project types. “One of our clients is Roxbox,” he noted, “who does projects like popup beer taprooms in shipping containers. So we can work outside of the realm of typical traditional building projects. But that’s probably only 10% or less of what we do. The other 90% are typical housing projects that you would expect to see in apartments and townhomes,” he added.
Regardless of the project type, Dalvit said the company focuses heavily on the quality of design and documentation because it’s so critical to all the stakeholders on the project.
“We track key performance metrics on our projects that ensure that not only are we providing a level of service that’s going to keep the client happy,” he noted, “but actually better designs and documents that are really well coordinated. They’re clear for all the stakeholders from plans reviewers to inspectors, and the factory to the general contractor. The focus needs to be on the greater team involved in a modular project because every one of these stakeholders have different needs from our documents.”
A team of over 120 employees doesn’t typically come together overnight, and Dalvit’s team is no exception. Starting with a focus on architecture, he added a structural engineer when he couldn’t keep up with the workload. Then the civil engineering team came together, and then the MEP department.
“Once each of those departments were formed, stabilized, and growing on their own, that’s when we started focusing on project types and the studios naturally emerged,” Dalvit said. “And when we create studios, that’s really when a team’s skills and experience become leverageable. A studio focuses on specific project types.”
“The studios create thought leaders and specialists in a way that was not possible previously, when everyone needed to work on everything,” Dalvit said. “When you get people functioning as specialists, you have an exponential growth curve there in terms of skills and experience that we can bring to the market in ways that we couldn’t really do in the early days,” he noted.
“Before studios, when we got a new project, whoever was available at the time would take it on. And while that was interesting, it wasn’t scalable because nobody could really dig in deep and become a real specialist in any one market the way that we can now,” he added.
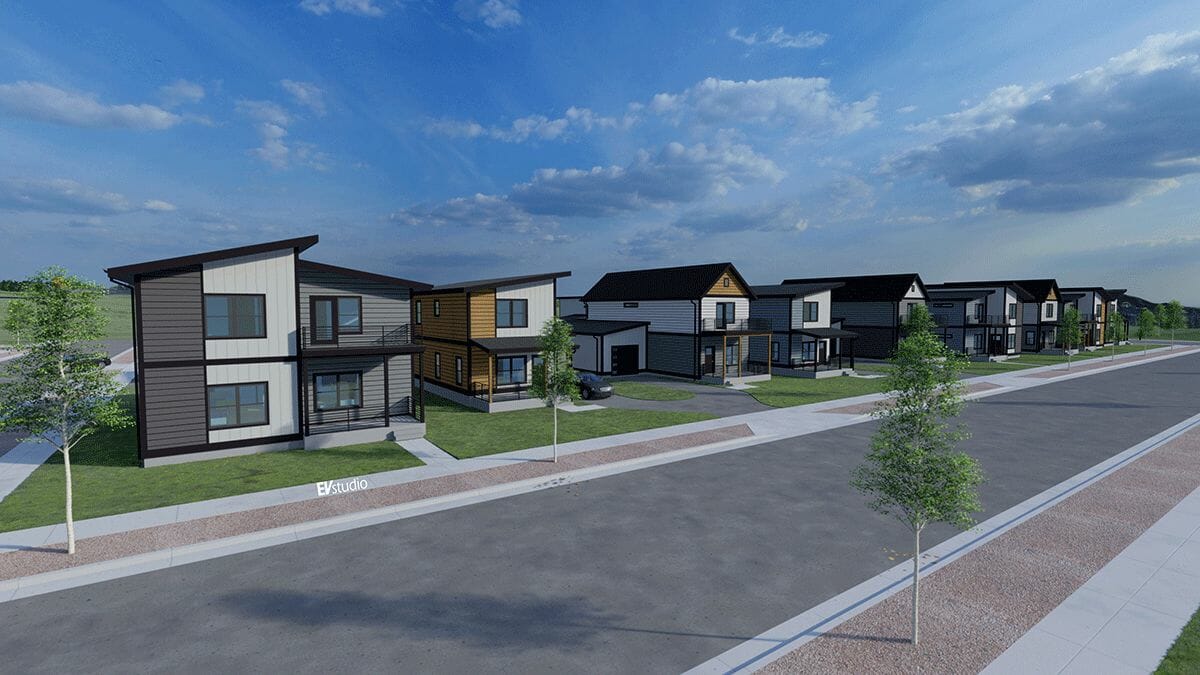
EVstudio rendering of Poncha Springs streetscape.
Embracing Challenges with All Stakeholders
EVstudio’s breadth of expertise has definitely been an advantage in dealing with the challenges of the last few years, as well. “There isn’t a project that exists that doesn’t have its challenges. That’s why we all are in business. Our job is to anticipate challenges and work through them,” Dalvit said.
In the years following the pandemic, projects were suddenly derailed by supply chain and schedule issues, labor challenges, and any number of other factors. “Our approach has been to just buckle down and lock arms with our clients, the factories, and the contractors that are all working for the common goal, and work through those struggles together,” Dalvit said.
“You often find that an issue that comes up on a project is not a singular issue. It’s not just a design solution that will get you out of it. It’s going to be a design solution that’s connected with means and methods that the factory or the GC has to sort through that probably also ties to a procurement decision that the factory must contend with.”
“Every issue that comes up potentially affects every stakeholder,” he said. “Scheduling issues affect the GC, the financing people, the owner, and the factory. When something goes on hold, it is painful for everyone involved,” he added.
Creating a Smoother Process
“Getting EVstudio involved early in the process can help to create a smoother process,” Dalvit said. “Any type of offsite construction, whether panelized or fully modular, must be designed from the start to be factory built,” he noted. “You also want to do your site analysis considering offsite construction to optimize the building footprint.”
“Pivoting to offsite construction later in the project is possible and can happen,” he said. “Though in my professional experience, it always results in a significant redesign, if not a complete do-over from scratch. If you’re not designing for offsite construction, there are just far too many variables that are not going to be considered and are too difficult to unwind or unravel,” he said.
“As the building designer, EVstudio facilitates communication between stakeholders,” Dalvit said. “Our communication style and our platform are open because
there are so many stakeholders. We have regular meetings not just with the owner, but the factory and the general contractor have important seats at the table as well,” he noted.
That level of assistance is necessary in modular construction in a way that’s different from stick-built construction. “Architects and engineers are trained not to get into means and methods,” he noted. “That’s the builder’s job, traditionally, but a modular designer must consider how assemblies go together.” “I can confidently say the biggest challenge to designing for off-site construction is actually the mindset. It’s just a very different way of thinking than most designers
are trained academically and professionally. In many ways, we’re expected to take on the contractor’s role and determine the means and methods of constructing every assembly or component,” he said.
As an example, he mentioned setting one module on top of another and connecting plumbing fittings. “Some actual person has to physically stick their hand up between two joists straddling a wall and make a plumbing connection with a three-inch diameter 90-degree elbow. And most designers are never expected to ever concern themselves with that,” he noted. “We don’t have that luxury to ignore that. When it’s left to figure out in the field, that’s when bad things happen,” he added.
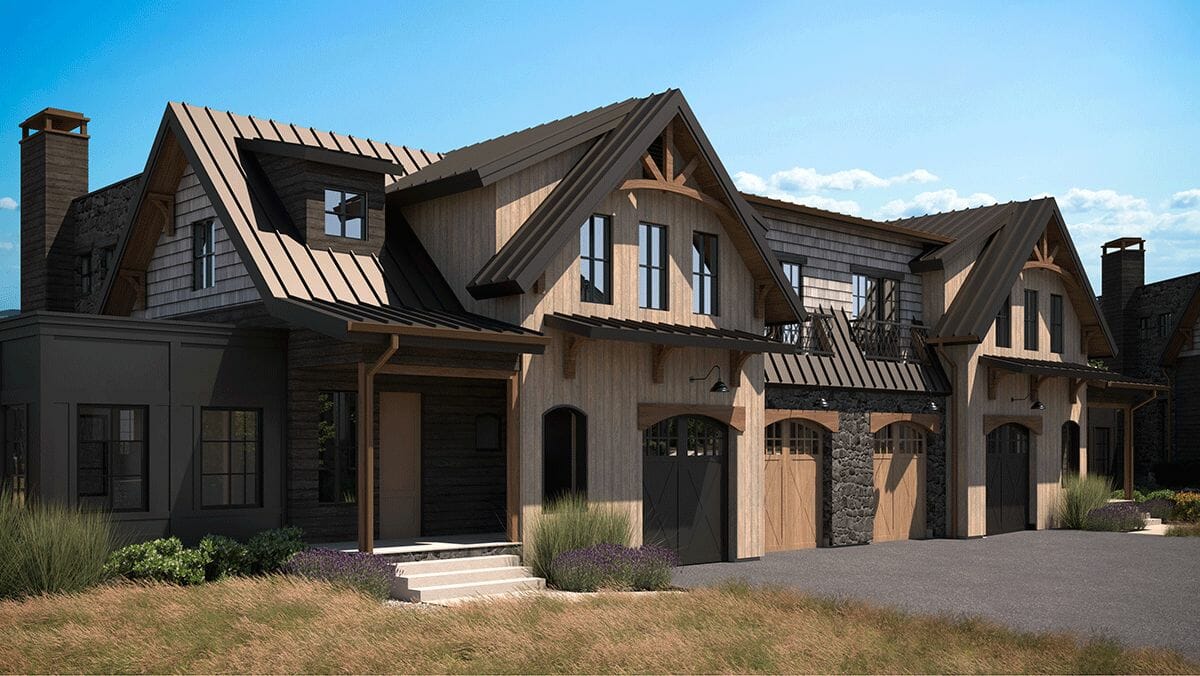
Big Sky Yellowtail, designed by EVstudio.
Best Practices for Modular Construction
That mindset, in fact, is one of Dalvit’s five best practices for modular designers. “Start with the right mindset and be willing to get into the weeds on means and methods with factories, general contractors, and most importantly, the scope delineation between the two. If a designer doesn’t have that mindset and doesn’t care about scope delineation, the project is doomed from the get-go,” he said.
Next on his list is learning how factories actually work and visiting factories to see for yourself and learn. “Think like a factory manager, take tours of the factory that you’re working with. Take tours of any factory for that matter and as many factories as you possibly can take tours of,” he said. “Understand what the limitations are, the real-life limitations of a factory, what their tooling is, and how they build their assemblies,” he added.
His third idea is a riff on the previous idea, and that’s a deep understanding and development of standard assemblies and sticking to them. “That’s really hard for architects to do. Architects like to deviate and change, break the rules. But in offsite construction, rules are there for a reason. While they might be able to be broken, try not to. Make sure you stick to the standard assemblies and things go a lot more smoothly for the factory,” he added. “There’s still plenty of opportunity for great design.”
His fourth best practice is to advocate for each of the stakeholders on the team. “It really is a team and should not be a silo of designers versus factory versus general contractor versus owner. But rather a group of people all working towards the common goal,” he said. “Help others understand the importance of coordinating your scope with theirs and their scope with others because they may not be fully aware of the downstream implications of what they’re considering or perhaps not considering,” he noted.
Finally, be honest with yourself and if modular is not for you don’t pretend that it is. If you do, you’re not going to be adding value to the client or the stakeholder team. “I’ve been on enough teams now where you’ve had folks on the team that their heart wasn’t into it. They wanted to do the project like any other traditional site-built project, and it just makes trouble for everyone else on the team,” Dalvit noted.
“A list of best practices is a solid tool for future growth, which EVstudio is embracing,” Dalvit said. “With modular construction representing such a tiny fraction of all construction, there is abundant room for growth,” he noted. “Open sourcing of information would help the modular industry as a whole to gain market share by cooperating rather than competing.”
“A rated fire assembly is not a strategic advantage for a factory. It’s just a way you might do things,” Dalvit said. “So I would strongly stress that the industry would better itself dramatically by developing a set of universal standards that would enable developers and owners to consider modular and not have to necessarily feel like they’re limiting themselves to one specific choice before they’ve really had an opportunity to vet the construction method as a whole.”
Though EVstudio is the building designer and you might think their involvement in projects would end with the certificate of occupancy, it doesn’t. “Our involvement really never ends,” Dalvit said.
“There’s always a post CO assessment evaluation, something might come up that the owner might call us about that we’ll step in and assist with in any way that we can, whether it’s a warranty issue with the factory or general contractor, or just a maintenance item,” he added. “We are stewards of our projects and clients long after the construction is completed.”
About the Author: Steve Hansen is a Colorado-based writer with a focus on the built environment—architecture, construction, renewable energy, and transportation. He can be reached on LinkedIn.
More from Modular Advantage
Oregon’s Prevailing Wage Proposal: A Wake-Up Call for Modular Construction
In early February, 2024, the Massachusetts Board of Building Regulations and Standards (BBRS) released its proposed 10th Edition building codes. This draft included several amendments targeting modular construction that would have created an extremely difficult environment for the entire modular industry and could have eliminated the industry entirely in the state.
Behind the Design of Bethany Senior Terraces, NYC’s First Modular Passive House Senior Housing Project
As more developers seek to meet new regulations for energy efficiency, the team at Murray Engineering has set a new record. With the Bethany Senior Terraces project, Murray Engineering has helped to develop NYC’s first modular structure that fully encompasses passive house principles — introducing a new era of energy efficiency in the energy-conscious city that never sleeps.
How LAMOD is Using Modular to Address Inefficiency, Sustainability, and the Future of Construction
As developers, designers, and contractors seek to understand the evolving needs of the modular industry, no one is as well-versed in the benefits of going modular as Mārcis Kreičmanis. As the co-founder and CBDO of LAMOD in Riga, Latvia, Mārcis has made it his ultimate goal to address the inefficiencies of traditional construction.
From Furniture Builder to ‘Activist Architect’: Stuart Emmons’ Unique Journey
Stuart Emmons was fascinated by buildings at a young age. He remembers building sand cities with his brother during trips to the Jersey shore. His father gave him his first drawing table at the age of ten. Today, he is an experienced architect who received his FAIA in June 2025. The road he took is unique, to say the least.
Forge Craft Architecture + Design: Codes, Contracts, and Intellectual Property
Founding Principal and Director of Modular Practice for Forge Craft Architecture + Design, Rommel Sulit, discusses the implications of codes, contracts, and intellectual property on
modular construction.
Eisa Lee, the “Bilingual” Architect
Now as the founder of XL
Architecture and Modular Design in Ontario, Canada, she applies not just her education as a traditional architect but an entire holistic view on modular design. It’s this expansive view that guides her work on being a true partner that bridges the gap between architects and modular factories as they collaborate on the design process.
Tamarack Grove Engineering: Designing for the Modular Sector
The role of a structural engineer is crucial to the success of a modular project, from initial analysis to construction administration. Tamarack Grove offers structural engineering services — project analysis, plan creation, design creation, and construction administration — for commercial, manufacturing, facilities, public services, and modular. Modular is only one market sector the company serves but it is an increasingly popular one.
Engineer Masters the Art of Listening to His Customers
Since founding Modular Structural Consultants, LLC. in 2014, Yurianto has established a steady following of modular and container-based construction clients, primarily manufacturers. His services often include providing engineering calculations, reviewing drawings, and engineering certification
Inside College Road: Engineering the Modules of One of the World’s Tallest Modular Buildings
College Road is a groundbreaking modular residential development in East Croydon, South London by offsite developer and contractor, Tide, its modular company Vision Volumetric (VV), and engineered by MJH Structural Engineers.
Design for Flow: The Overlooked Power of DfMA in Modular Construction
Unlocking higher throughput, lower costs, and fewer redesigns by aligning Lean production flow with design for manufacturing and assembly.