Modular and Off-Site Construction: Risk Questions, Scenarios, and Suggestions
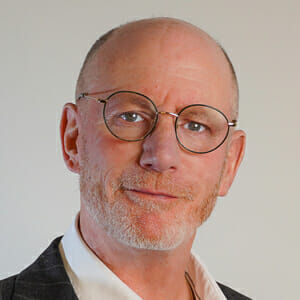
B. Daniel Seltzer, CPCU, is a principal of Seubert & Associates, Inc.
Thanks to our friends at MODLOGIQ, we are proud to announce ourselves as a new member of the Modular Building Institute. Thank you for the warm welcome at World of Modular in Las Vegas last April. We hope to establish long-term, trusting relationships with MBI members, and we look forward to participating in the upcoming expos and the World of Modular in 2024.
We offer the following thoughts as an introduction to Seubert & Associates, Inc.
Question #1: Is your insurance company an adversary or a partner?
My 42 years in the business indicates neither is the correct answer! Carriers are experts at assuming specified, fortuitous, quantifiable risk with conditional promises to pay IF various distinct facts occur, all in exchange for your premium dollars. Who has the advantage on this playing field?
Question #2: Who composes the fine print of the insurance contract, and for the benefit of whom?
The multi-billion-dollar carrier and reinsurers standing behind the contract, or the MBI member reading this article? Who would you bet on, and what tools are at your disposal to improve the rules of the game? Who to turn to, and when?
Question #3: Are you prepared?
When considering risk exposure in your industry, many traditional construction risks are mitigated. A few examples of reduced risk include theft of materials, bodily injury, and enhanced quality. Any new risks? Can you identify exposures created by modular construction? There are a handful. Have you prepared?
Building upon these questions, I invite you to consider the following scenarios.
Scenario #1
To level the playing field, is the best choice of insurance agent one who first obtains copies of your policies, then floods the market with e-mails to hopefully find the lowest rate from the hot underwriter on that given day? Or are chances enhanced by working with a trained risk management professional serving as your broker, who is fiercely independent and understands your exposures to loss at least as well as yourself?
Scenario #2
We are currently experiencing the “hardest market” in over 350 years; insurance rates have increased 19 quarters in a row. This has never happened before, ever! Do you understand why? If you know the dynamics, including your risk profile, you can reduce your Total Cost of Risk.
With the preceding insights in mind, let’s explore suggestions to effectively navigate the complexities of the insurance and risk transfer landscape.
Suggestion #1
Although the “modular” and “off-site” construction business is not new, it is a relative newcomer, and not as mature as the insurance industry. Insurers are conservative by nature and utilize historical data to promulgate rates. When actuaries determine data is not statistically credible, what do you believe is the result? Exactly, lack of competition and unattractive pricing! I believe MBI and its members can do something about this phenomenon.
Shall we discuss?
Suggestion #2
Businesses are glued together by contracts. Try improving your risk profile and how you present yourself to underwriters. This will yield impressive results compared to obtaining bids from hungry insurance salespeople. Arrange for new eyes to review your important contracts and implement best practice processes.
Suggestion #3
Encourage your insurance agent/broker to include you in the negotiating process with underwriters, and I mean directly. Sure, the best risk management professionals can “pitch” your account from an exposure, coverage, and strategic perspective, but no one will have more interest and knowledge of your business operations than yourself. If “prepped” correctly by your broker, you would bring the “special sauce,” which is missing in 95% of insurance submissions in the marketplace. Do not wait for insurers to lower rates. It will not happen until market forces create competition. Currently, reinsurance capacity has been seriously depleted, which restricts competition. Take control!
Real Life Example
Why the insurance advocate you entrust with protecting your assets and shielding your organization from liability is essential to your survival as an entrepreneur.
Most insurance brokers focus on where the commission dollars come from, and how to earn more. The best brokers take their work seriously and are fulfilled when they know their client is correctly insured.
Greater than 65% of the commission dollars for MBI manufacturers and contractors are within General Liability, Workers’ Compensation, and Excess Liability insurance policies – this is important coverage for sure.
May we talk about Property and Inland Marine coverage for a moment? It is rare to meet an insurance professional who, WITH REAL PURPOSE, asks the correct questions to assure their client is situated properly. I am happy to discuss why if you wish. For now, ask yourself two simple questions. First, does your insurance “person” truly understand when, why, how, and to what extent your insurable interest in property is created and when it ceases? See the graphic below which supported a new MBI client’s suspicion of their prior insurance agent not paying attention.
Second, once these questions are answered, does your broker understand and then suggest cost-effective solutions?
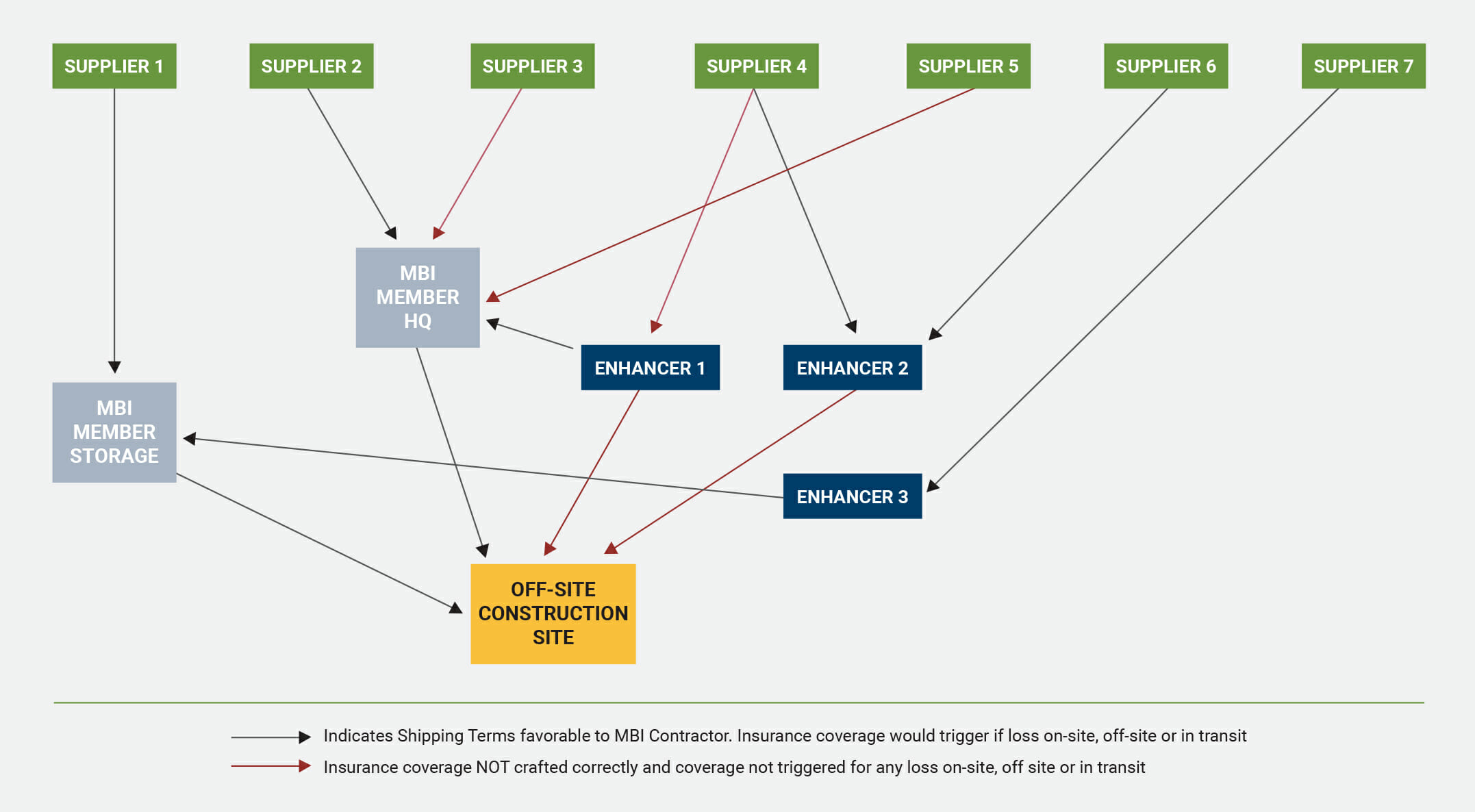
Considering the unique nature of modular projects, MBI members need to carefully address surety considerations to ensure successful outcomes.
1. Surety Selection
Selecting a quality surety professional is of utmost importance. When researching a firm, consider their years of experience and amount of bonds written, current
relationships with underwriters, and the memberships they hold to various professional associations, as well as their overall knowledge of your unique industry. By partnering with a reputable consultant, you can ensure reliable performance that maximizes your bonding capacity.
2. Design Elements
Failures during the design stage will trigger delays and increase costs. If the contractor is responsible for designing the project, delays will cause margins to shrink, eat into working capital, and impact the balance sheet, which is integral to surety underwriting decisions.
3. Supplier Risk
Contractor must know:
- Can the manufacturer meet the timeline?
- What happens if the manufacturer cannot meet the schedule or ceases business operations?
- Can the contractor replace the manufacturer, or will the contractor need to return to the design/engineering stage with a new manufacturer?
4. Transportation
Increased costs result from shipping delays and damages, which can trigger liquidated damages or actual damages clauses. Related to damage delay clauses, contract language must be reviewed. Surety underwriters want to make sure the contractor can meet the timelines.
5. Construction Defects
Modular build quality can suffer with the wrong employees or misused automation equipment. Contractors should ensure the right labor is in place, understand local legislation, and always keep quality at the forefront. To help with the underwriting process, modular contractors should be able to answer questions regarding their experience with the modular building supplier and the process to prequalify the supplier.
6. State and Local Building Codes
Modular contractors should be aware of varying state and local building codes. Surety underwriters ensure contractors are knowledgeable about these codes. If a contractor is moving into a new territory, surety underwriters will remind contractors that building code knowledge is key.
7. Prevailing Wage Issues
In some states, contractors are responsible for unpaid prevailing wages and unpaid penalties, even if a subcontractor or supplier completed the work. The contractor must assess its contractual obligation to determine if a modular builder will fall under a subcontractor, manufacturer, or supplier classification.
8. Labor
The difference in complexity between a single-story modular building and a high-rise or mixed-use development modular building can be exponential. Construction labor availability continues to be a major challenge, and the lack of experience assembling these buildings can make it more difficult for contractors looking to enter the modular building market. Surety underwriters will ensure the right labor is in place to complete the project within its parameters.
More from Modular Advantage
Oregon’s Prevailing Wage Proposal: A Wake-Up Call for Modular Construction
In early February, 2024, the Massachusetts Board of Building Regulations and Standards (BBRS) released its proposed 10th Edition building codes. This draft included several amendments targeting modular construction that would have created an extremely difficult environment for the entire modular industry and could have eliminated the industry entirely in the state.
Behind the Design of Bethany Senior Terraces, NYC’s First Modular Passive House Senior Housing Project
As more developers seek to meet new regulations for energy efficiency, the team at Murray Engineering has set a new record. With the Bethany Senior Terraces project, Murray Engineering has helped to develop NYC’s first modular structure that fully encompasses passive house principles — introducing a new era of energy efficiency in the energy-conscious city that never sleeps.
How LAMOD is Using Modular to Address Inefficiency, Sustainability, and the Future of Construction
As developers, designers, and contractors seek to understand the evolving needs of the modular industry, no one is as well-versed in the benefits of going modular as Mārcis Kreičmanis. As the co-founder and CBDO of LAMOD in Riga, Latvia, Mārcis has made it his ultimate goal to address the inefficiencies of traditional construction.
From Furniture Builder to ‘Activist Architect’: Stuart Emmons’ Unique Journey
Stuart Emmons was fascinated by buildings at a young age. He remembers building sand cities with his brother during trips to the Jersey shore. His father gave him his first drawing table at the age of ten. Today, he is an experienced architect who received his FAIA in June 2025. The road he took is unique, to say the least.
Forge Craft Architecture + Design: Codes, Contracts, and Intellectual Property
Founding Principal and Director of Modular Practice for Forge Craft Architecture + Design, Rommel Sulit, discusses the implications of codes, contracts, and intellectual property on
modular construction.
Eisa Lee, the “Bilingual” Architect
Now as the founder of XL
Architecture and Modular Design in Ontario, Canada, she applies not just her education as a traditional architect but an entire holistic view on modular design. It’s this expansive view that guides her work on being a true partner that bridges the gap between architects and modular factories as they collaborate on the design process.
Tamarack Grove Engineering: Designing for the Modular Sector
The role of a structural engineer is crucial to the success of a modular project, from initial analysis to construction administration. Tamarack Grove offers structural engineering services — project analysis, plan creation, design creation, and construction administration — for commercial, manufacturing, facilities, public services, and modular. Modular is only one market sector the company serves but it is an increasingly popular one.
Engineer Masters the Art of Listening to His Customers
Since founding Modular Structural Consultants, LLC. in 2014, Yurianto has established a steady following of modular and container-based construction clients, primarily manufacturers. His services often include providing engineering calculations, reviewing drawings, and engineering certification
Inside College Road: Engineering the Modules of One of the World’s Tallest Modular Buildings
College Road is a groundbreaking modular residential development in East Croydon, South London by offsite developer and contractor, Tide, its modular company Vision Volumetric (VV), and engineered by MJH Structural Engineers.
Design for Flow: The Overlooked Power of DfMA in Modular Construction
Unlocking higher throughput, lower costs, and fewer redesigns by aligning Lean production flow with design for manufacturing and assembly.