The Mountains, Hills, and Valleys of Material Prices
A new report from Anirban Basu, chairman & CEO of Sage Policy Group and Chief Economist of the Modular Building Institute
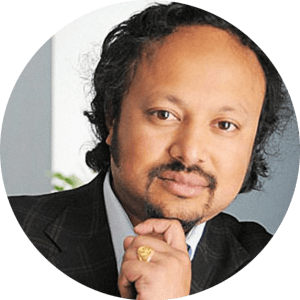
Anirban Basu is chairman & CEO of Sage Policy Group and Chief Economist of the Modular Building Institute
What Goes Up Must Come Down, Eventually
It all started with a global pandemic. With governments urging people to stay at home and the global economy entering a sharp downturn, many economic activities were interrupted. This was particularly true in the context of supply chains as workers generally could not supply effort remotely in manufacturing and distribution contexts and were told to physically isolate as their factories idled.
The pandemic followed decades of moving to just-in-time inventory practices. With factories temporarily shuttered and inventories quickly depleted, the supply of various items was constrained. Then the economy reopened, albeit in fits and starts. Demand for various items surged as consumers looked to spend massive accumulation of savings as vaccinations become more commonplace.
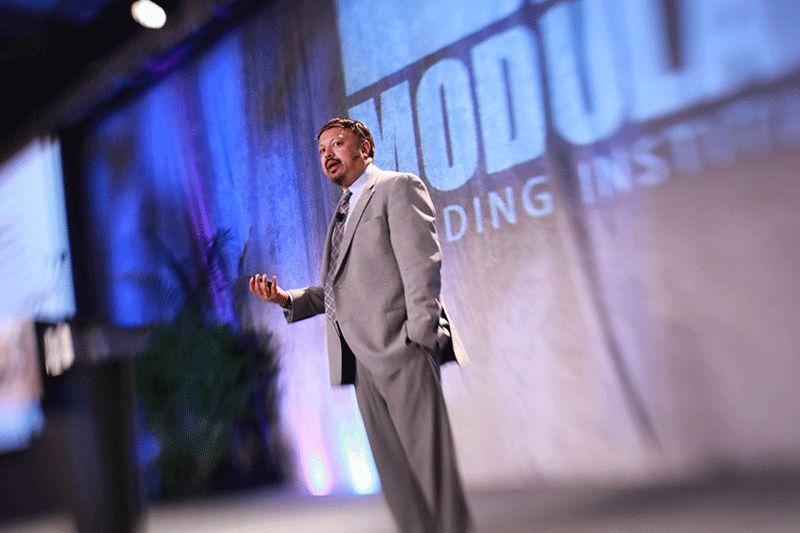
Anirban Basu speaks at MBI's annual World of Modular conference and tradeshow.
The result was inevitable. With demand ratcheting higher and supply chains and inventories atrophied, prices took off. This was especially problematic for those working in goods-producing segments, like modular construction. Investors sought to deploy capital in large amounts thanks to absurdly low costs of capital as central banks around the world injected liquidity into financial systems. While it helped certain forms of economic activity that the cost to borrow funds was low, the same factor rendered it difficult to generate income. Interest rates were too low from the perspective of portfolio returns. Investors responded by investing in a variety of assets, including real estate. The consequence was an uptick in demand for construction materials as properties were repositioned in the marketplace or built from scratch.
Alas, the supply of materials was simply inadequate, producing massive increases in the prices of softwood lumber, steel, and other inputs to construction. Many of these commodity prices slumped early during the pandemic, only to ramp up immediately thereafter. For instance, according to data from the Bureau of Labor Statistics (BLS), steel prices fell slightly in 2020. With most of the world shut down, demand for steel was predictably low.
That did not last. Inflation burst forth during spring 2021, with construction materials prices at the heart of dramatic price increases. By April 2021, steel prices were 125 percent higher than they were the month prior to the pandemic. By August, prices were nearly twice the pre-pandemic levels. Steel prices finally peaked in November 2021, settling at 235.7 percent above the pre-pandemic level.
The story of softwood lumber was roughly as dramatic. If the price of steel was equivalent in dramatic intensity to the hit TV series Game of Thrones, softwood lumber was metaphorically aligned with at least the show Succession. Softwood lumber, another key input in modular building, experienced a price in exceeding 150 percent between February 2020 and May 2021.
While it is simple to handwave and attribute virtually all causal effects to pandemic induced phenomena, there has been more at work. For example, prior to global contagion there were budding trade wars around the world, including many between friends.
Early during the Trump Administration, America imposed significant tariffs on Canadian softwood lumber. By mid-2018, Random Lengths, a publication focused on the lumber market, pointed out that the “cost of 1,000 board feet of western Canadian lumber is up nearly 80 percent over the past 12 months...” There was also a burgeoning trade war with China, Brexit, and other forms of deglobalization that pushed prices higher. Many trade disputes have continued into the Biden Administration.
Even the price of concrete has ballooned. Its price has increased more than 31 percent over the past three years. As indicated by the National Association of Home Builders, the rise in prices in recent months was attributable at least in part to the closure of a large limestone quarry in Mexico. Moreover, the report states that the shortages in concrete are not limited to the U.S. since many nations are wrestling with a lack of key inputs, including cement. A recent Washington Post article pointed out that concrete “is the most ubiquitous human-made substance on earth...” That same article pointed out that, “Cement prices are surging on both sides of the Atlantic as producers passed on higher energy and pollution-compliance costs to customers and then kept hiking prices even as their gas and electricity bills receded.” In America, cement prices have been increasing at a 15 percent annual rate.
That said, even a deadly pandemic and trade wars fail to fully explain the massive inflation that modular builders and others have experienced in recent years. Transportation costs have also risen massively on occasion. The Baltic Dry Index, an economic indicator that tracks shipping costs of raw materials, rose from around $400 per container in February 2020 to $2,178 a bit more than a year later. Prices continued to rise, passing $5,500 by October 2021.
The Cass Freight Index, an indicator supplying crucial insight into North American’s shipping industry, was 17 percent higher in May 2021 compared to the month before the shutdown. The rise in shipping costs was attributable to numerous factors, including a shortage of truck drivers. Data from the BLS indicate that the number of job openings in the Transportation, Warehousing, and Utilities subcategory, which encompasses truck drivers, was up 51.2 over the same period.
While many of these prices have fallen recently, including several construction materials prices, there are still indications of supply chain disruption. Mechanical contractors, for instance, often point to lengthy lead times for switchgear and generators. According to a CNBC survey from December 2022, only 32 percent of logistics managers indicated that supply chains had returned to what they deem normal compared to more than 60 percent who find that abnormalities persist. Nearly one in three respondents indicate that supply chains will not return to pre-pandemic normalcy until 2025 or perhaps never.
A report from Nashville, a hotbed of construction activity, highlights these lingering challenges. Shortages of key materials and equipment have forced contractors to come with novel ways to conduct work. For instance, Nashville Electric Service has dug up old unused power transformers to use in current projects while they wait for new equipment to arrive.
Looking Ahead
While there remain a handful of construction input categories that continue to be associated with significant supply shortages and rapidly rising prices, such instances have become increasingly rare. During a recent 12-month period, materials prices in the aggregate declined, though much of that decline was driven by dips in energy prices. With the global economy poised for further weakness and recession highly likely in America at some point over the next 12 months, there could be additional downward pressure on input prices during the year ahead even as more infrastructure projects break ground.
More from Modular Advantage
AI, Faster Sets, and Automation: The Future of Modular is at World of Modular
While the modular building industry has long known that it can be an effective solution to increase affordable housing, the word is slowly spreading to more mainstream audiences. Three presentations at this year’s World of Modular in Las Vegas hope to provide insight and direction for those seeking a real solution to the crisis.
An Insider’s Guide to the 2025 World of Modular
The Modular Building Institute is bringing its global World of Modular (WOM) event back to Las Vegas, and with it comes some of the industry’s best opportunities for networking, business development, and education. Over the course of the conference’s four days, there will be numerous opportunities for attendees to connect, learn, and leverage event resources to get the most out of the conference.
Affordable Housing Now: The Industry’s Best Bring New Solutions to World of Modular
While the modular building industry has long known that it can be an effective solution to increase affordable housing, the word is slowly spreading to more mainstream audiences. Three presentations at this year’s World of Modular in Las Vegas hope to provide insight and direction for those seeking a real solution to the crisis.
Opportunities for Innovation in Modular Offsite Construction
Modular Offsite Construction has already shattered the myth that it only produces uninspired, box-like designs. Architectural innovations in module geometry, configurations, materials, and products make it possible to create visually stunning buildings without sacrificing functionality or efficiency.
Safe Modular Construction with Aerofilm Air Caster Transport
In collaboration with Aerofilm Systems, Heijmans developed innovative skids using air caster technology for moving modules easily and safely. These pallets are equipped with an auto-flow system, making operation extremely simple.
Miles, Modules, and Memes: Building a Modular Network One Flight at a Time
At the end of the day, social media is just another tool for building connections, and like any other tool, needs to be used skillfully to work properly. Use social media thoughtfully, and it will open doors to real opportunities and relationships you didn’t even see coming.
Falcon Structures: Thinking Inside the Box
Some of Falcon’s latest projects include creating container solutions for New York’s Central Park and an East Coast professional baseball team. More and more, Falcon is shipping out container bathrooms and locker rooms to improve traditionally difficult work environments, like those in oil and gas or construction.
UrbanBloc—From Passion to Industry Leader
UrbanBloc specializes in three main categories or markets – what they call “Phase 0” projects, amenities, and urban infill. Clients are often attracted to shipping containers because from a real estate perspective they are considered an asset. Having the flexibility to move and transport these assets allows owners to respond to different circumstances in a fluid manner that they can’t get with standard construction.
The Hospitality Game-Changer
“Hospitality is about more than just providing a service – it’s about delivering an experience,” says Anthony Halsch, CEO of ROXBOX. “And that’s where containers thrive. They allow us to create spaces that are unique, efficient, and sustainable.”
Container Conversions Counts on Simplicity to Provide Critical Solutions
Container Conversions has fabricated and developed thousands of containers for varied projects, including rental refrigeration options, offices, kitchens, temporary workplace housing, and mobile health clinics.