ReMo Homes: Building Futuristic Homes for the Present
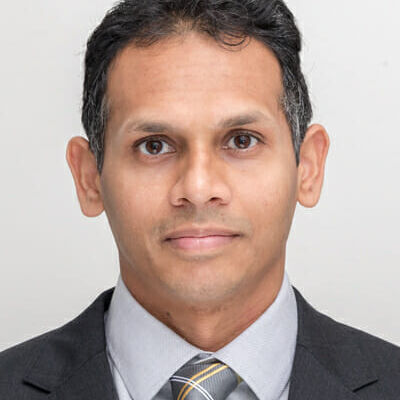
Vamsi Kumar Kotla is the co-founder of ReMo Homes.
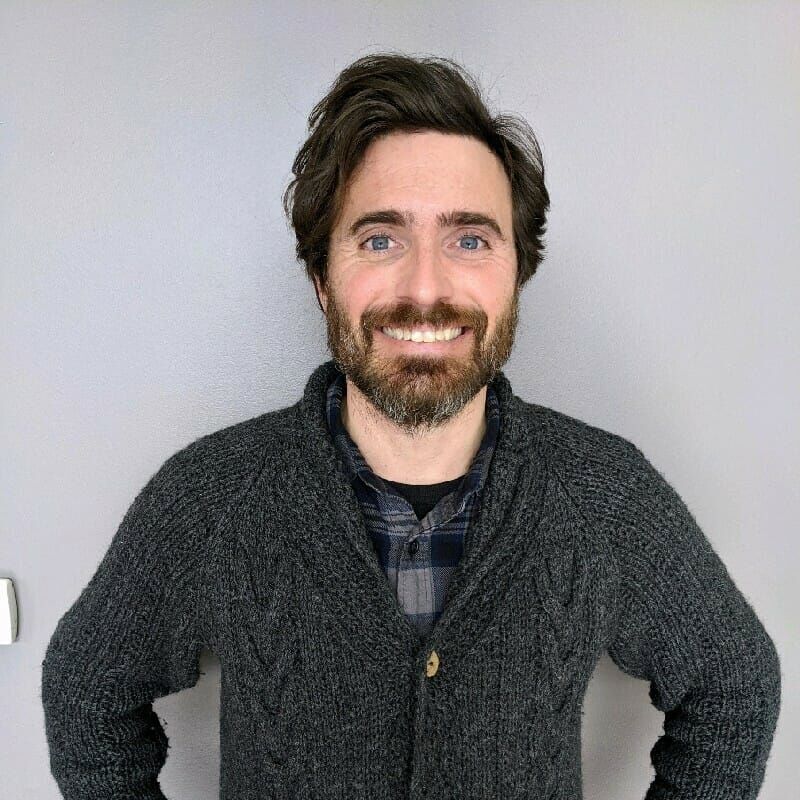
Ryan Blowers is the co-founder of ReMo Homes.
What if your home could predict your mood when you got home based on how you shut your car door? Let’s say you’ve had a bad day and need to relax. You open your front door to find tranquil music playing and the smell of lavender in the air. Your home knows what food is in your fridge and what’s more, it knows what you like to eat when you’re in this mood and suggests that you make that meal.
What if your home had automatic temperature control and humidity monitoring? And we’re not talking about a Ring Doorbell – we’re talking about sensors inside the walls of your home that could also tell you the difference between the temperature inside and outside so you can verify your thermal insulation and double as sensors for a security system.
What if your home could notify you of an issue, like a leak, in your home before it became a problem? Or, what If your home could detect where you spend most of your time and adjust to accommodate your habits and maximize energy efficiencies? What if your home could improve your mental health and wellness with lighting that mimics daylight and features technology that can bring more in?
There’s a new home on the market that can do all of this and more, signaling that we have arrived in the future. ReMo Homes is not just building homes, but homes that aim to solve the biggest problems in the world today: climate change and affordable housing. Vamsi Kumar Kotla and Ryan Blowers co-founded ReMo Homes at the beginning of 2022.
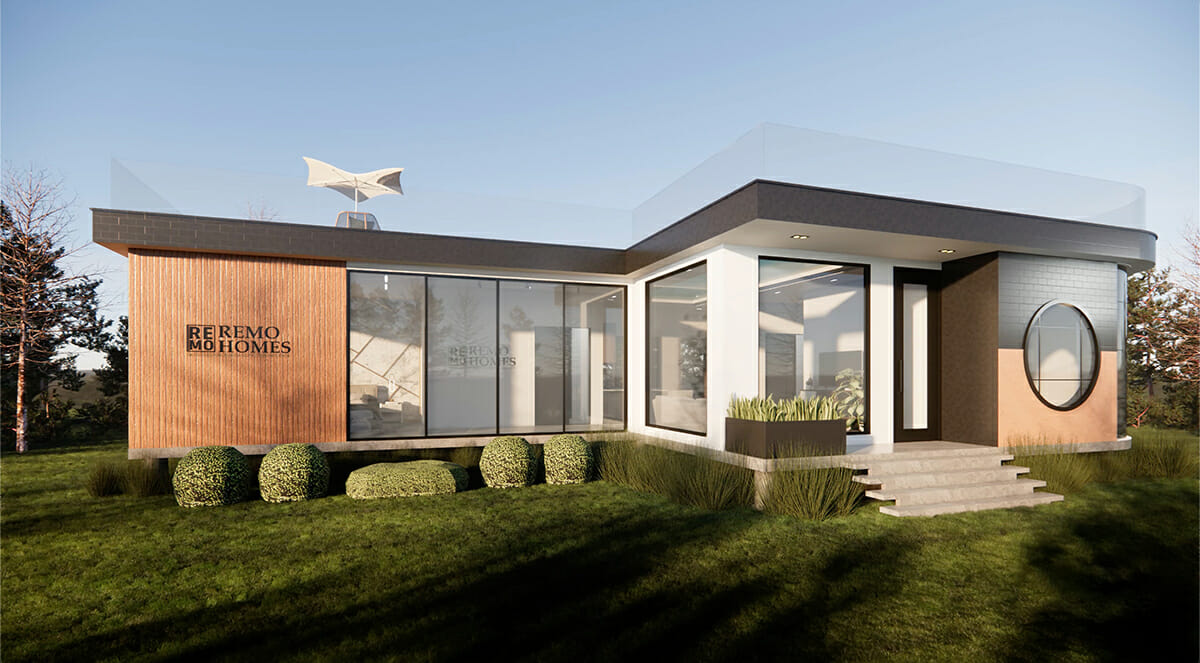
3-D rendering of ReMo Homes’ SupreMo model. For the complete interactive version, visit https://remo.homes.
It Started by Asking “Why?”
Kotla started in the commercial construction industry back in 2004 and then he married into a family that has been constructing single and multi-family homes for over four decades. But his background in computer science left him questioning the lack of innovation in the industry. “Why can’t we use modern systems and modern methods?” he would repeatedly ask his father-in-law. The innovative ideas Kotla brought to the table were constantly met with pushback from subcontractors and unapproving banks.
However, during the COVID-19 pandemic, everything changed. When Kotla was trying to upgrade his home, he lost marketable bids and new homes were still considered 50-year tear-downs. “There must be a better way,” he thought. With the pandemic challenging the status quo, he saw an opportunity to finally bring his ideas to life and teamed up with Ryan Blowers, a US Navy Veteran and ex-SpaceX Project Leader. Blowers was also just as frustrated with traditional construction. At the beginning of 2022, they began formalizing a company, building a team, putting
together a prototype, and building. ReMo Homes was born.
[ r ee m oh ]
The name “ReMo Homes” marries the together the two main concepts behind their unique home construction method. “Re” accounts for the way ReMo Homes reduce home footprints, uses recyclable materials, offers the reuse components of the home in the future, and can reconfigure the space of the home to fit different needs at any time. “Mo” accounts for the modular construction of the homes.
Kotla was inspired by the automotive, aerospace, and smartphone industries to mass produce single-family homes, eyeing their cutting-edge technology, diagnostics, and human-centered design seeing an opportunity to apply it to the housing industry which has been largely undisrupted for decades.
“The materials and building codes have changed, but the construction methods have largely remained the same for over 100 years. Guys are still swinging hammers and hand-painting walls. The residential construction industry has been resisting industrialization,” says Kotla. “However, we are here not to ‘disturb,’ but rather ‘enhance’ with cooperation from various stakeholders such as policymakers, developers, and traditional construction industry players.”
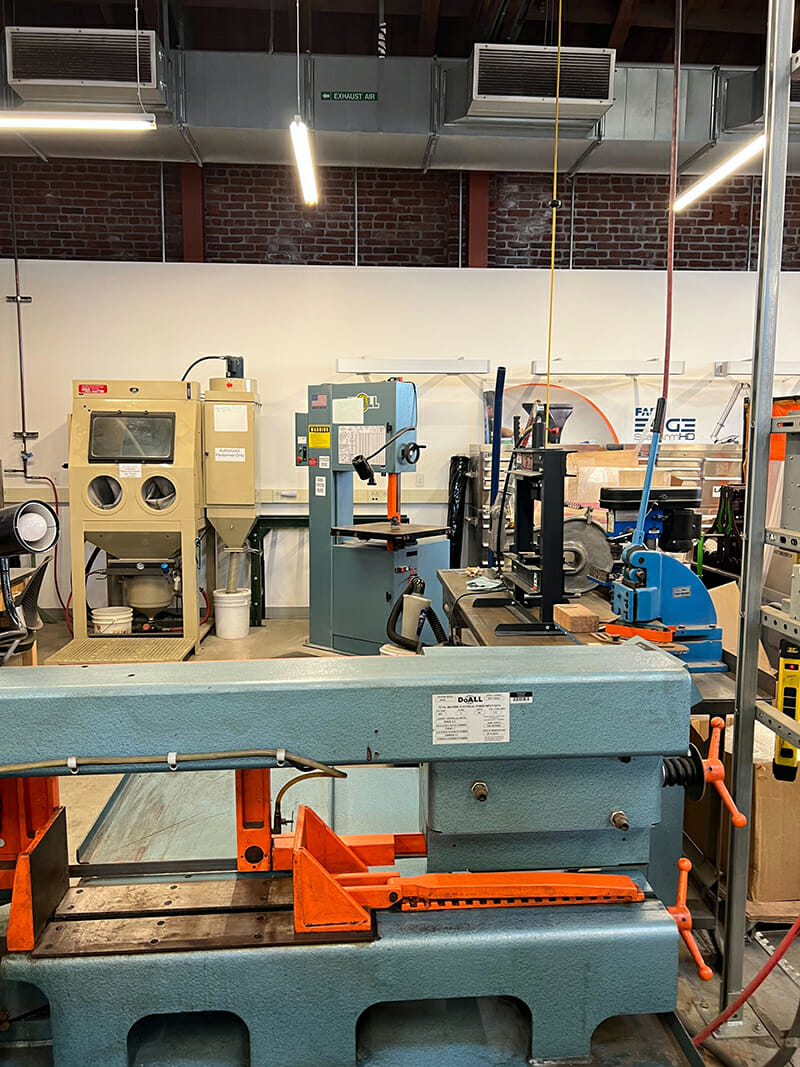
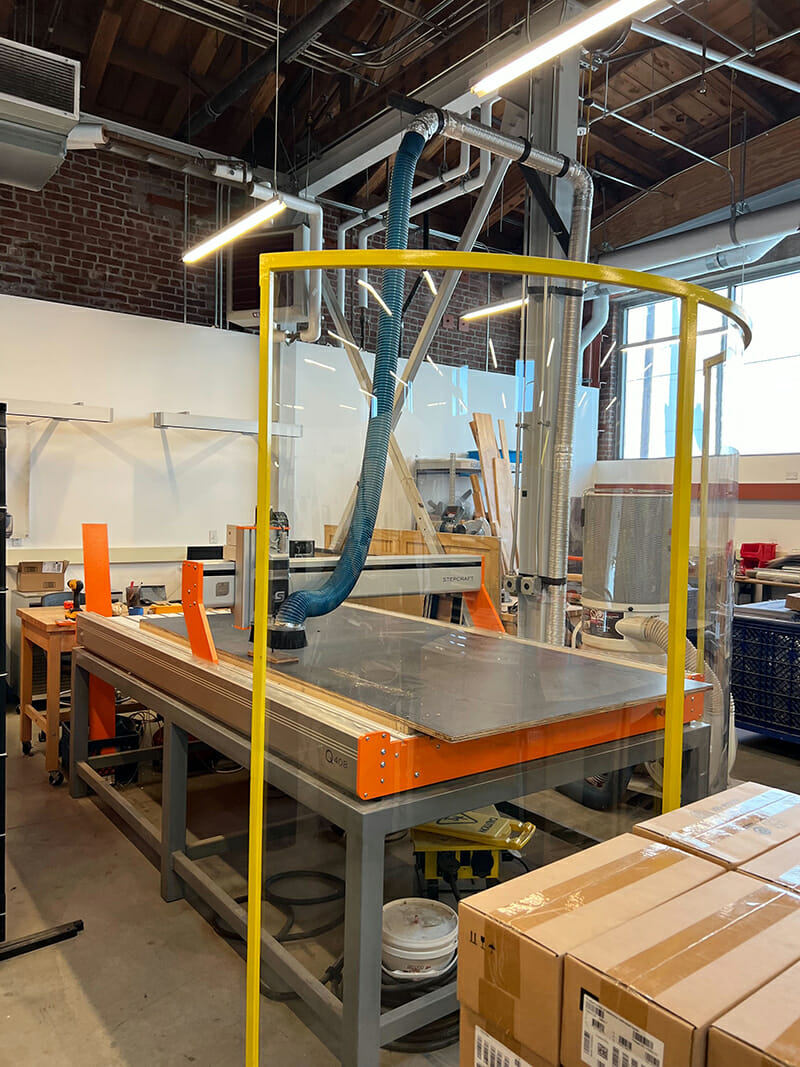
A peek inside the ReMo prototyping lab.
Holistically Built Homes on a Mission
To build homes that address both climate change and the affordable housing crisis Kotla and Blowers are taking holistic approach. Over the years housing has gotten more and more out of reach for most people, especially around desirable areas with well-paying jobs. The COVID-19 Pandemic only furthered this issue, all against the backdrop of a climate crisis.
ReMo Homes’ solution lies in standardizing home models and manufacturing them on an assembly line in a factory to utilize the benefits of modular construction to make housing more affordable and environmentally friendly. Housing’s combined contribution to GDP averages 15-18% and it is wildly harmful to the environment, responsible for 40% of overall global CO2 emissions. “There is no excuse to be building on site,” says Kotla. Kotla and Blowers ask us to consider this scenario:
You order a Tesla Model 3, and the parts of the car are brought to your front yard and assembled there. “Wouldn’t that be absurd?” they ask.
“There is no good reason that a home, mostly filled with empty space and doesn’t have nearly as a complex of a supply chain or gadgetry as a [car] and be costing $500 per square foot to build in California [for example],” says Kotla. “Something doesn’t add up.” Kotla and Blowers’ goals with ReMo Homes are to make the home-building process more streamlined and cost-effective, with more predictable timelines and utilize higher-quality materials to build a futuristic home for the here and now.
We have smart cars and smartphones, and we think we have smart homes too. But Kotla says there’s no such thing as a “smart home” today. “Today’s ‘home innovation’ comes after the build of the home and where some sensors are added in and it’s called a ‘smart home,’” says Kotla.
A True Smart Home
The ReMo Homes prototype adds innovation to their homes before the walls are closed in a factory with efficiency. “A true ‘smart home’ is not sticking a [Google] Nest on the wall and calling it a ‘smart home,” states Kotla.
The innovation Kotla’s referring to goes far beyond a Google Nest, with features like automatic full-spectrum lighting that mimics daylight. “Temperature control and air quality monitoring that can tell you the difference in temperature between the inside and the outside so you can verify your thermal insulation – Your walls should be able to tell you all of that,” says Blowers. “If you think about it in one section of a wall, it’s a little easier to digest, but then you imagine it connected like a network, and you have a virtual home that you can experiment with your living habits and it allows you to learn more about what type of home you actually need,” he says.
Blowers point out that with a truly smart home, you can begin to answer questions like, “Where are you spending most of your time?” You would be able to detect issues in the home before they become big problems, saving time, money, and potential waste.
Kotla refers back to the Tesla analogy, offering that when there’s an issue with the home you would be able to call someone to remotely run diagnostics on the home to pinpoint the exact issue. You would also be able to learn about your home’s inefficiencies such as temperature variations and, for example, something as simple as when a float in your toilet isn’t functioning properly and it’s causing your water to be constantly running.
A Human-Centered Home
“We want to productize the whole home,” says Blowers. The idea is that you’ll have a build of materials and the ability to order a new backsplash that fits like a puzzle piece into your kitchen or change out a water facet – or any of the other components of your home without spending hours in a variety of hardware and home improvement stores overwhelmed by choice paralysis. “There is no reason to have so many options for housing. There should be some method to this madness,” says Kotla. Further, if you need to modify an entire section of the home you could add mods with ease.
“This is the modern home,” says Blowers. “We are giving you the home that you can build right now with all these amazing technologies that actually exist right now. This isn’t the future home; this is the home for right now.” And, with all of ReMo Homes’ components and the way the home is engineered, it’s also adaptable for the future. “This is not a concept home,” adds Kotla. “It’s all about human-centered design.” With people spending so much of their time in their homes these days, Kotla believes that it’s important for our homes to work better for us.
“There’s so much opportunity to incorporate mental wellness just with the lighting alone,” says Blowers. “People spend a lot of time in their houses, especially now working remotely. Taking all of these things into consideration and being able to facilitate an environment that we already know is better for the human condition, we have the opportunity to stimulate a little happiness. That’s what it’s all about,” explains Blowers.
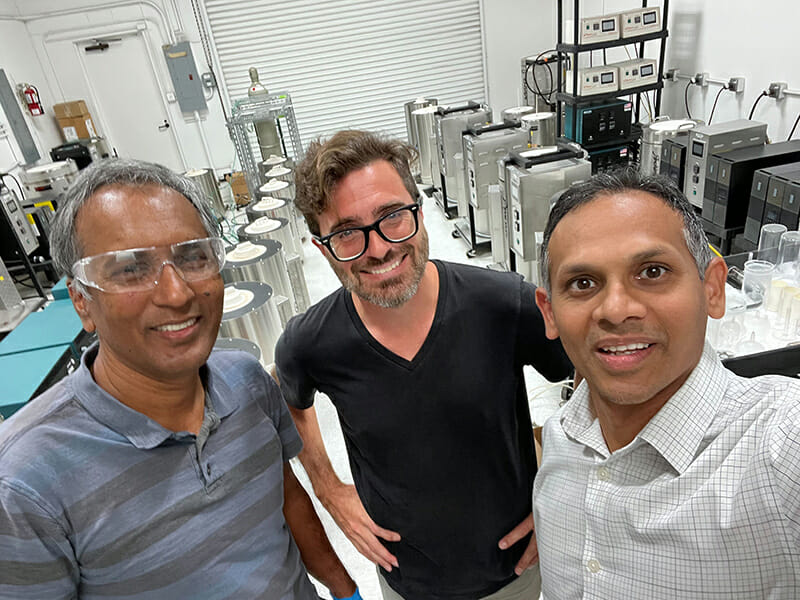
Bringing semiconductor and aerospace manufacturing processes to buildings manufacturing.
Photo courtesy: United Semiconductors LLC
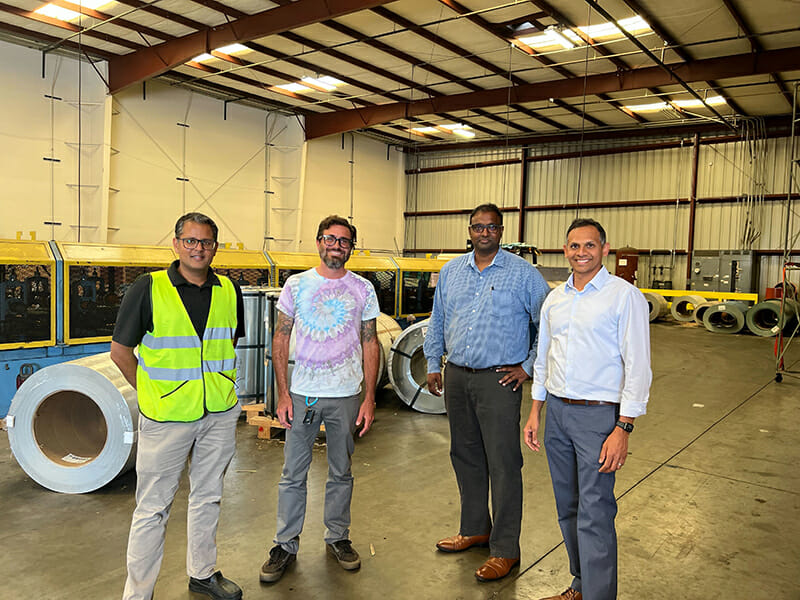
The ReMo team at our light gauge steel prefab facility.
Working Backwards to Propel the Housing Industry Forward
For the research and development of ReMo Homes’ first model, they worked backward from all the problems they were trying to solve. “Working backward is what’s missing in the market,” says Kotla. They started with an average home price people could afford, thought about how they could build a home with efficient use of the land it would occupy, considered the available commodity materials, and identified the most common building look of a home with a focus on the walls.
“We dissected the wall and put it back together piece by piece and incorporated modern available tech. Since then, we’ve just been running different ‘recipes’ with temperature sensors, internal vs. external, humidity sensors, IR sensors, and methods of pest control. All those sensors will be repurposed for the security systems. We want to find the most available, off-the-shelf components that we had access to and put it to the test to see if it meets our vision of what the ‘smart wall’ can be,” explains Blowers.
Smart Walls at the Core
The term “smart wall” is one that they coined as they worked through the research and development process. Once they settle on different materials, they will incorporate all of the sensors internal to the wall itself. “The wall is the core of the home, and it is the home of the technology,” says Blowers.
Kotla notes that for ReMo Homes it’s more so little ‘r’ capital ‘D.’ “What that means is, being a startup with limited resources we want to also be mindful of spending too much time on capital. We are turning to a well of people who have done decades of research as well as corporates to see if we can commercialize R&D that’s gathering dust,” he explains. “Then in the future, we can incorporate new products, and [this well of people] can support a line,” adds Blowers.
ReMo Homes has multiple prototyping centers across California. They have one in Pomona that they share with one of their architects, one in downtown Los Angeles that they are using as an existing prototyping center for their product, and one of their own in Gardena. One is dedicated to designing, another is dedicated to testing smart sensors, and the third is dedicated to testing materials. Kotla and Blowers have been having active conversations with one of the biggest modular factories in the world and one of the biggest robotics companies in Germany for their input as they continue to develop their line. By next year, they want to have their model built to full scale, take it to shows, and open up a small-batch production facility to fill orders they already have for several hundred homes.
They’re currently working on incorporating assembly stations for components like roofing, plumbing, and external and internal finishes. Then by 2024, they’d like to have a semi-automated assembly line with robots. “We want automation, but we want it to be right,” says Blowers.
When completed, the homes will ship in modules and be installed by local GCs at their destinations in compliance with all local codes and standards. Because ReMo Homes are unlike any other, Kotla and Blowers would like to be able to certify local GCs in installing their homes and receive validation and verification from them.
Homes That Can Do It All
Before the COVID-19 Pandemic, the home was the place you came back to after being out in the world during the day. Kotla points out that home is everything now. “[Home] is where you live, but also where you work, study, and entertain. Because of that, we feel that this is the time for more human-centered design,” he says. This is why he is constantly asking questions like, “Can we make reconfigurable walls?” and “Can we design this space better, not just for sleeping and living, but also for working, studying, and entertaining?”
People now expect more from their homes. Blowers envisions homeowners being able to come home and activate different modes, and even be able to detect your mood and what you might need on any given day by something as simple as how you shut your car door when you get home. “If the home detects you’ve had a bad day, it could cue it to start playing tranquil music and diffusing lavender into the air, as an example. It’s important to note that all this information that the house would know about its inhabitants would be protected, anonymous user data. This is your home, and it should work as a tool for you,” says Blowers.
“Your environment can stimulate moods. Let’s use that for what we know about productivity, what we know about relaxing, and what we know about the human condition overall,” Blowers goes on to say. “Your home really should be like a ‘spa.’”
“We call home a ‘sacred space’ because back in the day, life’s big moments would happen outside of it, but we’re spending more and more time inside our homes and life’s big moments are primarily happening within them,” adds Kotla. “Let’s reinvent and adapt homes to this new reality.”
Undeniable Advantages
There’s no denying the advantages of a ReMo Home that will make it attractive to end-users including its price, short build times, undeniable quality of its materials, true home automation, standardized practices, and the ability to easily upgrade your home to name a few.
Currently, ReMo Homes are made of steel, glass, and composites with eco-friendly foam insulation. As the R&D of the home evolves, the materials could change to offer an even higher quality end product. Kotla and Blowers also want to offer a full ecosystem of furniture, lighting, accessories, and more designed specifically for ReMo Homes and they are currently exploring partnerships with major home retailers. Blowers hopes to even be able to offer a whole section of re-mods so that a homeowner can easily adjust the size and space of their home to fit their unique needs at any time.
"We are turning to a well of people who have done decades of research as well as corporates to see if we can commercialize R&D that's gathering dust.”
Call ReMo Home
If you’re interested in owning a ReMo Home, you can reach out directly to Kotla and Blowers and join the waitlist. They share that biggest challenge in bringing the home to market is conveying the vision to architects. “It’s been challenging to convey the vision to architects and overcome skepticism,” says Blowers. “We’ve found some really amazing architects once we got onto the trail and learned how to approach them and what exactly we’re asking for.”
Over the next three to five years, Kotla and Blowers hope to educate stakeholders, policymakers, and think tanks aside from incorporating production automation. “We want to incorporate automation in our production process and all of that, but what’s equally important is to get buy-in,” explains Kotla. For this reason, we have been working on co-hosting ReBuild 2022, an invite-only leadership conclave to discuss the innovation and regulatory changes needed to scale the offsite modular industry. They are particularly inspired by Sweden where almost 84% of all residential construction takes place in a factory off site.
It’s their hope that ordering one of their homes will be as easy as ordering the latest iPhone with homes that are truly designed to be human-centered and sustainable.
About the Author: Meg Dowaliby is a copywriter, storyteller, and brand evangelist. You can connect with her at https://www.linkedin.com/in/meg-dowaliby/.
More from Modular Advantage
AI, Faster Sets, and Automation: The Future of Modular is at World of Modular
While the modular building industry has long known that it can be an effective solution to increase affordable housing, the word is slowly spreading to more mainstream audiences. Three presentations at this year’s World of Modular in Las Vegas hope to provide insight and direction for those seeking a real solution to the crisis.
An Insider’s Guide to the 2025 World of Modular
The Modular Building Institute is bringing its global World of Modular (WOM) event back to Las Vegas, and with it comes some of the industry’s best opportunities for networking, business development, and education. Over the course of the conference’s four days, there will be numerous opportunities for attendees to connect, learn, and leverage event resources to get the most out of the conference.
Affordable Housing Now: The Industry’s Best Bring New Solutions to World of Modular
While the modular building industry has long known that it can be an effective solution to increase affordable housing, the word is slowly spreading to more mainstream audiences. Three presentations at this year’s World of Modular in Las Vegas hope to provide insight and direction for those seeking a real solution to the crisis.
Opportunities for Innovation in Modular Offsite Construction
Modular Offsite Construction has already shattered the myth that it only produces uninspired, box-like designs. Architectural innovations in module geometry, configurations, materials, and products make it possible to create visually stunning buildings without sacrificing functionality or efficiency.
Safe Modular Construction with Aerofilm Air Caster Transport
In collaboration with Aerofilm Systems, Heijmans developed innovative skids using air caster technology for moving modules easily and safely. These pallets are equipped with an auto-flow system, making operation extremely simple.
Miles, Modules, and Memes: Building a Modular Network One Flight at a Time
At the end of the day, social media is just another tool for building connections, and like any other tool, needs to be used skillfully to work properly. Use social media thoughtfully, and it will open doors to real opportunities and relationships you didn’t even see coming.
Falcon Structures: Thinking Inside the Box
Some of Falcon’s latest projects include creating container solutions for New York’s Central Park and an East Coast professional baseball team. More and more, Falcon is shipping out container bathrooms and locker rooms to improve traditionally difficult work environments, like those in oil and gas or construction.
UrbanBloc—From Passion to Industry Leader
UrbanBloc specializes in three main categories or markets – what they call “Phase 0” projects, amenities, and urban infill. Clients are often attracted to shipping containers because from a real estate perspective they are considered an asset. Having the flexibility to move and transport these assets allows owners to respond to different circumstances in a fluid manner that they can’t get with standard construction.
The Hospitality Game-Changer
“Hospitality is about more than just providing a service – it’s about delivering an experience,” says Anthony Halsch, CEO of ROXBOX. “And that’s where containers thrive. They allow us to create spaces that are unique, efficient, and sustainable.”
Container Conversions Counts on Simplicity to Provide Critical Solutions
Container Conversions has fabricated and developed thousands of containers for varied projects, including rental refrigeration options, offices, kitchens, temporary workplace housing, and mobile health clinics.