Modular Building Poised for Takeoff Globally
A report from Anirban Basu, chairman & CEO of Sage Policy Group and Chief Economist of the Modular Building Institute
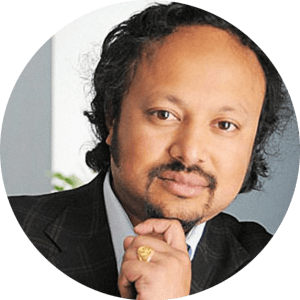
Anirban Basu is chairman & CEO of Sage Policy Group and Chief Economist of the Modular Building Institute
Limited Market Penetration to Date
Approximately two-and-a-half years ago, COVID undid the global economy. A period of progress associated with the development of just-in-time worldwide supply chains, diminished global poverty, rampant innovation, and a dearth of nation versus nation military conflict ended. It has been replaced by a period of disrupted supply, elevated inflation, food and energy crises, a brutal war in Eastern Europe, and rising geopolitical tensions between the world’s two leading superpowers, America and China.
Just-in-time has become “don’t hold your breath” as materials and worker shortages have conspired with elevated transportation costs to raise the price of virtually any manufactured good amidst lingering equipment and related shortages. Many Americans have left the labor force. Others insist on working from the comfort of their homes. This has further exacerbated supply, resulting not only in delays, but also in less consistent customer services. All of this has implications for modular building, and those implications are generally positive.
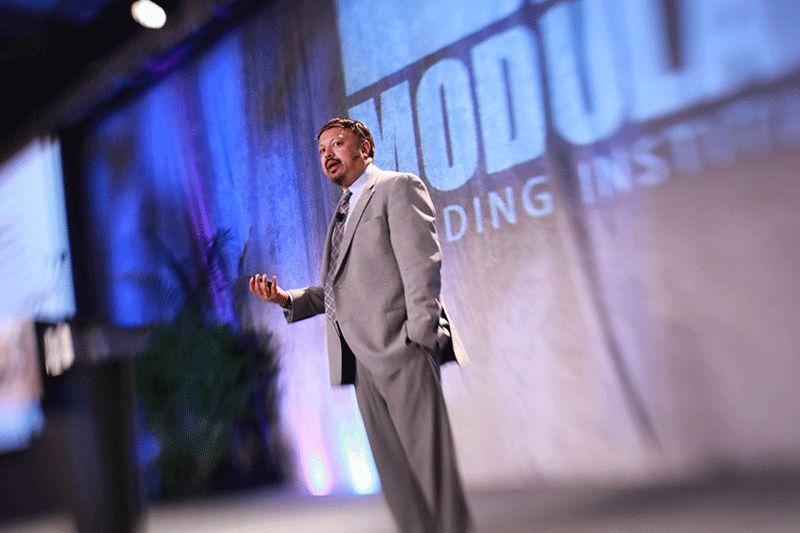
Anirban Basu speaks at the 2022 World of Modular conference and tradeshow.
That modular building hasn’t already gained more market share is a source of bewilderment to many. Though the technology has been around for more than 70 years, modular building in the U.S. has never gained as solid a foothold as it has in other societies. In Scandinavia, known for its commitment to efficiency and common sense, nearly half of all housing is manufactured and assembled off-site. In Japan, known for its scientific management of societal requirements, roughly 15 percent of housing is fabricated in a facility and transported to the project-site.
In the U.S., however, the technology remains far more niche, with only 3 percent of housing built in this fashion. Recent data from the Modular Building Institute indicate that modular construction still comprises only about 5 percent of commercial construction. As the balance of this article will indicate, modular building is about to takeoff globally and in America.
Workforce Considerations
The stereotypes are true – younger workers really are striving for work-life balance. A recent study conducted by PwC found that work-life balance is important for 95 percent of Millennials. This is far higher than recorded among prior generations. Many factors are at work, including the fact that 42 percent of workers stay connected at work even while on vacation. According to a Deloitte survey, Millennials and Gen Zers also measure success differently. Rather than focusing on owning tangible assets, many of these younger workers prioritize work-life balance when evaluating career opportunities.
These dynamics represent a significant opportunity for modular building. Traditional construction typically transpires during fixed hours. Because people often work in teams, they must be at jobsites at specified times. Opportunities to offer flexible hours are limited, particularly at a time when there is a general shortage of construction workers.
Moreover, those who work outdoors are subject to the vicissitudes of weather. Many workers are likely to prefer controlled settings. That is precisely what modular building offers. Because tasks are more easily separable (e.g., assembly line activities), opportunities for worker flexibility are greater.
Considerations of Climate
The world is presently amid an awkward transition from traditional fossil fuels to alternative energy like wind and solar power. That transition helps explain the elevated energy prices that Americans and others presently encounter. Obviously, the raging conflict between Russia and Ukraine hasn’t helped.
While some believe that the U.S. should recommit to fossil fuels, others remain concerned about global warming and increasingly violent weather. In short, the transition to alternative energy is likely to continue. In the meantime, energy prices are likely to remain higher than normal, even after the conflict in Eastern Europe ends.
Policymakers remain committed to climate. As of this writing, the U.S. Senate just passed a $700 billion package that embodies nearly $370 billion for climate related programs and initiatives. One of the bill’s primary goals is to reduce carbon emissions. The construction industry, with its reliance on heavy equipment and vehicles, is one of the largest producers of CO2 emissions. A United Nations Environmental Program report indicates that the industry produces “38 percent of total global energy related emissions”. To reach the 50 percent reduction in CO2 emissions goal by 2030, the global construction industry would have to cut emissions by 6 percent each year.
In this regard, modular building offers massive advantages. For instance, academics from the University of Cambridge and Edinburgh Napier University found that carbon dioxide emissions from homebuilding could be slashed by up to 45 percent with a modular construction system.
What this really tells us is that onsite builds produce massive amounts of carbon. The Urban Developer points out that onsite builds are “constructed using materials, components, and products. All this material has to be extracted from the ground, transported to a facility to be processed, transported again to be fabricated into a product, transported to site, and craned into place.” These processes inevitably result in the emission of greenhouse gases, including from fuel used for deliveries, heat used to reshape raw materials, and releases from manufacturing processes. Offsite prefabrication, by contrast, allows for more efficient processes, particularly if it is conducted close to a development site. Additionally, equipment used to assemble modules tends to be more energy efficient than equivalent machinery used onsite.
Negrón says that more and more clients are turning to prefabricated modular cleanrooms “because of the high quality, cost certainty, predictable schedules, and the ability to deliver projects much faster than traditional construction.”
Another advantage of POD cleanrooms is that they can be used temporarily and then re-located. Clients can use the cleanrooms for as long as they need them and then re-deploy them for another use or sell them. With traditional stick-built cleanrooms, the building expenses are sunk costs because the cleanrooms can’t be moved or re-sold as independent units if they’re no longer needed. Also, a small manufacturer can begin operating with one cleanroom POD and add more as the company grows and requires additional capacity — because each POD is completely self-contained.
A Response to the Devastation of War
Rebuilding Ukraine will take in the range of $600 billion. It is conceivable that war will continue to be a part of the landscape even as rebuilding commences. Modular construction represents a logical way to rebuild a society that faces the potential to rebuild often and expeditiously. Some industry insiders are pointing to the rebuilding of Ukraine to highlight the industry’s capabilities, flexibility, and contributions to a resilient built environment.
This is not merely theoretical. The Governor George Pataki Leadership Center, headed by the former New York governor, has worked to build and deliver modular housing units to Ukraine to help with the ongoing conflict. Media reports indicate that 18 units were delivered to the Kyiv region to house specialists working to clear debris and search for survivors.
Looking Ahead
Modular building is poised to experience substantial increases in market share over the next few years. That will support a cleaner, greener global environment, provide safer workplaces for employees, and help to more rapidly rebuild battered societies.
More from Modular Advantage
AI, Faster Sets, and Automation: The Future of Modular is at World of Modular
While the modular building industry has long known that it can be an effective solution to increase affordable housing, the word is slowly spreading to more mainstream audiences. Three presentations at this year’s World of Modular in Las Vegas hope to provide insight and direction for those seeking a real solution to the crisis.
An Insider’s Guide to the 2025 World of Modular
The Modular Building Institute is bringing its global World of Modular (WOM) event back to Las Vegas, and with it comes some of the industry’s best opportunities for networking, business development, and education. Over the course of the conference’s four days, there will be numerous opportunities for attendees to connect, learn, and leverage event resources to get the most out of the conference.
Affordable Housing Now: The Industry’s Best Bring New Solutions to World of Modular
While the modular building industry has long known that it can be an effective solution to increase affordable housing, the word is slowly spreading to more mainstream audiences. Three presentations at this year’s World of Modular in Las Vegas hope to provide insight and direction for those seeking a real solution to the crisis.
Opportunities for Innovation in Modular Offsite Construction
Modular Offsite Construction has already shattered the myth that it only produces uninspired, box-like designs. Architectural innovations in module geometry, configurations, materials, and products make it possible to create visually stunning buildings without sacrificing functionality or efficiency.
Safe Modular Construction with Aerofilm Air Caster Transport
In collaboration with Aerofilm Systems, Heijmans developed innovative skids using air caster technology for moving modules easily and safely. These pallets are equipped with an auto-flow system, making operation extremely simple.
Miles, Modules, and Memes: Building a Modular Network One Flight at a Time
At the end of the day, social media is just another tool for building connections, and like any other tool, needs to be used skillfully to work properly. Use social media thoughtfully, and it will open doors to real opportunities and relationships you didn’t even see coming.
Falcon Structures: Thinking Inside the Box
Some of Falcon’s latest projects include creating container solutions for New York’s Central Park and an East Coast professional baseball team. More and more, Falcon is shipping out container bathrooms and locker rooms to improve traditionally difficult work environments, like those in oil and gas or construction.
UrbanBloc—From Passion to Industry Leader
UrbanBloc specializes in three main categories or markets – what they call “Phase 0” projects, amenities, and urban infill. Clients are often attracted to shipping containers because from a real estate perspective they are considered an asset. Having the flexibility to move and transport these assets allows owners to respond to different circumstances in a fluid manner that they can’t get with standard construction.
The Hospitality Game-Changer
“Hospitality is about more than just providing a service – it’s about delivering an experience,” says Anthony Halsch, CEO of ROXBOX. “And that’s where containers thrive. They allow us to create spaces that are unique, efficient, and sustainable.”
Container Conversions Counts on Simplicity to Provide Critical Solutions
Container Conversions has fabricated and developed thousands of containers for varied projects, including rental refrigeration options, offices, kitchens, temporary workplace housing, and mobile health clinics.