Demand Booms for Modular Cleanrooms: G-CON Delivers
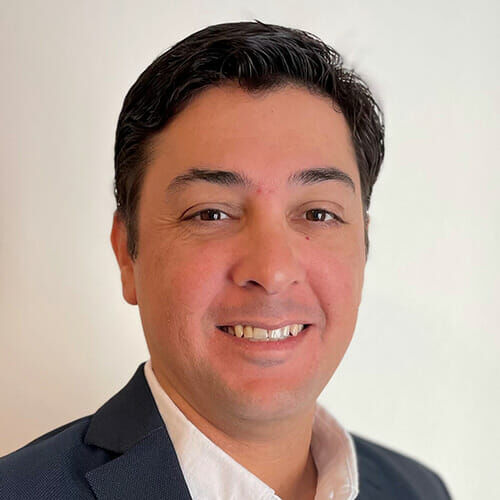
José Negrón is a process architect at G-CON, a manufacturer of prefabricated modular cleanrooms.
José Negrón is a process architect at G-CON, a manufacturer of prefabricated modular cleanrooms, which the company calls PODS. His role involves a combination of engineering and architecture. At the beginning of a project, his goal is to fully understand all the steps of the client’s production process, “starting from how they get raw materials into their warehouse; how they check the quality of the materials; every step of their production line; the flow of people and materials through the process; all the way to the finished product going out the door.” With that understanding, Negrón can design a POD layout that best serves the client’s processes and equipment.
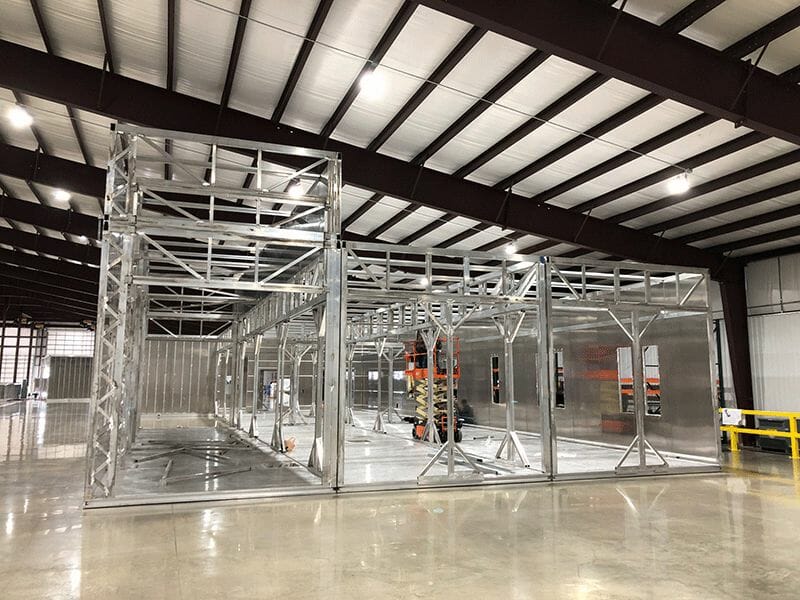
The PODs structures are made by welding aluminum members. Some extrusions are patented aluminum shapes that provide higher load bearing capacity than typical extrusions.
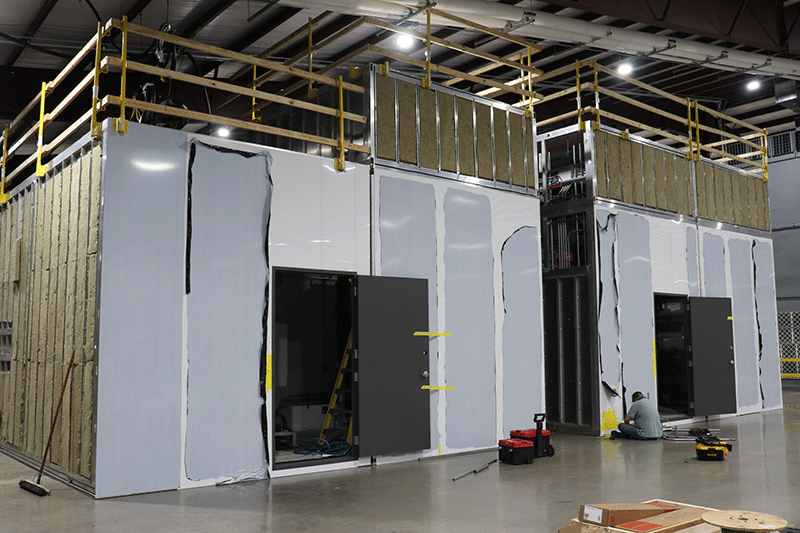
The PODs are fit-out at the factory with the necessary architectural components, in addition to the mechanical, electrical, automation and fire protection systems.
Product Design
Cleanrooms often have smaller rooms adjacent to them, called airlocks. Airlocks are used for people to gown-up, or for materials to go in or out. These actions take place in the airlocks so the proper environmental conditions can be maintained inside the cleanroom. Depending on the process, some airlocks are bi-directional, and some are uni-directional.
The superstructure of each cleanroom POD is made of aluminum, which is strong, light, and corrosion-resistant, all significant advantages over steel and wood construction. G-CON builds each POD frame in their fabrication shop. “The PODs are then combined with pre-assembled architectural and mechanical systems,” Negrón says.
“Fresh outside air is pre-conditioned with a make-up air unit to remove particulates and to get the temperature and humidity within a certain range,” Negrón explains. “Within each POD, there’s a dedicated HVAC system that receives the pre-treated air and pushes it through a number of filters. The final HEPA [High Efficiency Particulate Air] filters are in the cleanroom ceiling.”
Once the air flows into the cleanroom and reaches the floor, low wall return chases remove it from the room. “Any particulate matter that might be in the air goes down to the floor and out through the low wall returns,” Negrón adds. This airflow ensures no particulates accumulate in the corners of the cleanrooms. Coving where the walls meet the floor and ceiling also help achieve this.
Strict Requirements
In the pharmaceutical industry G-CON serves, there are different regulatory requirements for various aspects of a client’s processes. For example, air cleanliness and room classification requirements will vary depending on a client’s manufacturing processes.
In addition, many clients have very specific, rigorous cleaning protocols for every surface of the cleanroom, including the floor, walls, and ceiling. The materials for the interior surfaces must be able to withstand the cleaning chemicals used and the cleaning frequency.
In many cases, G-CON’s clients need to be able to prove to regulatory agencies that their products — such as vaccines — have been manufactured within strict environmental parameters. This means they must collect data on air temperature, relative humidity, air pressure, and other factors. “The data needs to be digitally collected, saved, and protected in such a way that nobody can tamper with it,” Negrón explains. “So, if someone from the regulatory agency asks for the data regarding a specific batch of vaccines manufactured at a certain time on a certain date, all that data is available.”
Modular Manufacturing Advantages
Building in a controlled, indoor environment means that it’s much more feasible to keep the product clean during construction. “Before shipping, we have a list of tests we perform on each POD in the factory. After they’re tested, the PODs are prepared and shrink-wrapped for shipping and delivery,” Negrón says. Once the cleanroom PODs are installed at the client’s facility, G-CON cleans them again. “For commissioning, we test the POD systems once more.” The client then does the final sanitization prior to operation.
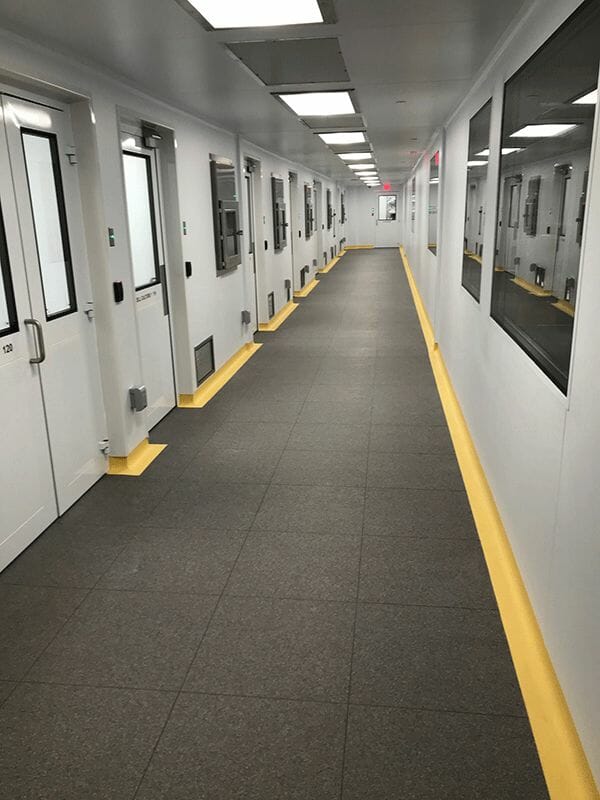
SubPODs are joined together with clean corridors that lead to airlocks, pass-through boxes and other material transfer elements.
Negrón says that more and more clients are turning to prefabricated modular cleanrooms “because of the high quality, cost certainty, predictable schedules, and the ability to deliver projects much faster than traditional construction.”
Another advantage of POD cleanrooms is that they can be used temporarily and then re-located. Clients can use the cleanrooms for as long as they need them and then re-deploy them for another use or sell them. With traditional stick-built cleanrooms, the building expenses are sunk costs because the cleanrooms can’t be moved or re-sold as independent units if they’re no longer needed. Also, a small manufacturer can begin operating with one cleanroom POD and add more as the company grows and requires additional capacity — because each POD is completely self-contained.
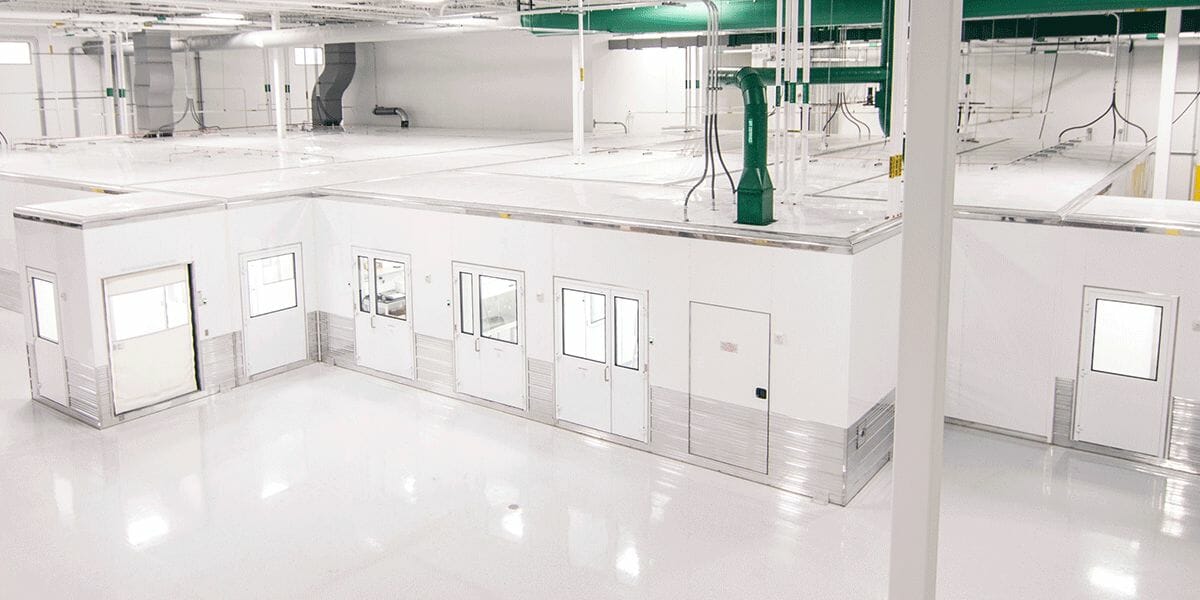
Depending on the client’s process, subPODs can be joined together to form a POD cluster. Projects vary from 1 to 14 plus subPODs. Interconnecting the PODs allows clients to have great layout flexibility.
Greater Demand and Increasing Standardization
The demand for cleanrooms has been very high over the past couple of years. “When COVID hit, some clients put projects on hold. But we were also inundated with new requests for cleanrooms, to support the global COVID response, including vaccine manufacturing,” Negrón says.
This increased demand has resulted in rapid growth for G-CON, including greater manufacturing footprint, capacity, and head count. At the same time, G-CON is moving towards more standardization of its POD systems to further reduce the time and cost for delivering cleanroom facilities. The company recently released a catalog of standardized POD designs. These standard models can address the needs of cell and gene therapy companies, or can handle fill-finish. (Fill-finish is the final step of filling, labeling, and packaging vials of medications before they’re distributed.) The idea is that the standardized PODs will provide enough variety and flexibility for clients to mix and match, while also providing the speed advantages of standardization. “Standard PODs can be ready for delivery in three months, whereas if a client requires custom POD designs, it might take six months to a year to deliver the PODs, depending on the project size,” Negrón says.
World of Modular Presentation
The main focus of Negrón’s World of Modular presentation is to show how G-CON delivers projects faster than regular construction methods, helping companies take drugs and therapies to market faster, saving patients’ lives. Cleanrooms must adhere to strict standards imposed by regulatory bodies such as the FDA, and Negrón will talk about how the manufacturing process for cleanrooms differs from ordinary modular prefabrication.
About the Author: Zena Ryder is a freelance writer, specializing in writing about construction and for construction companies. You can find her at Zena, Freelance Writer or on LinkedIn.
More from Modular Advantage
Oregon’s Prevailing Wage Proposal: A Wake-Up Call for Modular Construction
In early February, 2024, the Massachusetts Board of Building Regulations and Standards (BBRS) released its proposed 10th Edition building codes. This draft included several amendments targeting modular construction that would have created an extremely difficult environment for the entire modular industry and could have eliminated the industry entirely in the state.
Behind the Design of Bethany Senior Terraces, NYC’s First Modular Passive House Senior Housing Project
As more developers seek to meet new regulations for energy efficiency, the team at Murray Engineering has set a new record. With the Bethany Senior Terraces project, Murray Engineering has helped to develop NYC’s first modular structure that fully encompasses passive house principles — introducing a new era of energy efficiency in the energy-conscious city that never sleeps.
How LAMOD is Using Modular to Address Inefficiency, Sustainability, and the Future of Construction
As developers, designers, and contractors seek to understand the evolving needs of the modular industry, no one is as well-versed in the benefits of going modular as Mārcis Kreičmanis. As the co-founder and CBDO of LAMOD in Riga, Latvia, Mārcis has made it his ultimate goal to address the inefficiencies of traditional construction.
From Furniture Builder to ‘Activist Architect’: Stuart Emmons’ Unique Journey
Stuart Emmons was fascinated by buildings at a young age. He remembers building sand cities with his brother during trips to the Jersey shore. His father gave him his first drawing table at the age of ten. Today, he is an experienced architect who received his FAIA in June 2025. The road he took is unique, to say the least.
Forge Craft Architecture + Design: Codes, Contracts, and Intellectual Property
Founding Principal and Director of Modular Practice for Forge Craft Architecture + Design, Rommel Sulit, discusses the implications of codes, contracts, and intellectual property on
modular construction.
Eisa Lee, the “Bilingual” Architect
Now as the founder of XL
Architecture and Modular Design in Ontario, Canada, she applies not just her education as a traditional architect but an entire holistic view on modular design. It’s this expansive view that guides her work on being a true partner that bridges the gap between architects and modular factories as they collaborate on the design process.
Tamarack Grove Engineering: Designing for the Modular Sector
The role of a structural engineer is crucial to the success of a modular project, from initial analysis to construction administration. Tamarack Grove offers structural engineering services — project analysis, plan creation, design creation, and construction administration — for commercial, manufacturing, facilities, public services, and modular. Modular is only one market sector the company serves but it is an increasingly popular one.
Engineer Masters the Art of Listening to His Customers
Since founding Modular Structural Consultants, LLC. in 2014, Yurianto has established a steady following of modular and container-based construction clients, primarily manufacturers. His services often include providing engineering calculations, reviewing drawings, and engineering certification
Inside College Road: Engineering the Modules of One of the World’s Tallest Modular Buildings
College Road is a groundbreaking modular residential development in East Croydon, South London by offsite developer and contractor, Tide, its modular company Vision Volumetric (VV), and engineered by MJH Structural Engineers.
Design for Flow: The Overlooked Power of DfMA in Modular Construction
Unlocking higher throughput, lower costs, and fewer redesigns by aligning Lean production flow with design for manufacturing and assembly.