Fabricating the Tesla Model S of the Modular Industry

Chris Waters, the Director of Business Development at Z Modular, talked with us about how the Chicago-based company came into being and how it’s innovating in the modular construction industry.
Steel manufacturing expertise
Zekelman Industries has been around for over century, and for most of its history it has focused on manufacturing various steel products. Z Modular was inspired by the invention of a specific type of steel connection system — what’s now called VectorBloc®. The Zekelman team saw the potential to diversify into modular construction using this connection system, and formed its Z Modular division in 2016.
In addition to steel’s non-combustibility, Waters also notes that the material “allows much greater precision than wood, and Z Modular’s system has tight tolerances to 1/16th of an inch both vertically and horizontally.”
Steel also enables the construction of taller buildings. “Wood frame modular structures can typically go to between four and six stories. Combining modular construction with the conventional construction of a podium, then it’s possible to reach seven stories in some cases,” Waters says. “With Z Modular’s steel system, we can build up to 20+ stories.”
A major advantage of the VectorBloc system is that Z Modular can construct steel structures without needing welders to work outdoors on partially-constructed buildings.
“Traditionally, welders go up on scaffolding for skyscrapers, stadiums, arenas, and other large steel-framed structures with blowtorches in their hands. Onsite welding is an enormous expense, and we’ve taken that out of the equation.”
VectorBloc and other technology
“The patented VectorBloc is unique in that it’s a vertical tension bolted system. In other words, via the in-plant welding process, the HSS [hollow structural sections] members are attached on all corners and intersections of each module to form a 3D cage or chassis system,” Waters explains. The modules are then built out in the plant and transported to the project site.
“With the bolted system, the installation process is quick, effective, and results in secure and precise stacking — no going out of plumb after a few stories — without the need for costly and time-consuming on-site welding.”
Zekelman has long experience in steel manufacturing with robotics and automation. They saw the opportunity to apply that know-how and technology to Z Modular’s construction processes, and currently 25% to 30% of their in-plant fabrication process uses automation or robotics — a percentage Waters says will continue to grow.
“Z Modular is still in its infancy — young and evolving. Our initial facility was smaller and more manually driven, though it proved to be an excellent R&D [research and development] center for us. It’s been ‘The Little Engine That Could’ and it certainly got us started and continues to operate,” Waters says. “But with production advancements being identified, we realized it wouldn’t be an ideal space for long-term growth. Now, we have three more modular manufacturing facilities, which are large and equipped with a high level of technology and automation.”
Waters says that things that took hours to do manually can now be done in minutes, by using robotics and automation. Other technologies also help to increase efficiency for the company. “The wall in-fill panels are produced using steel stud forming machines, and decking systems are simplified using CNC machines. All of these advancements help to drive speed, efficiencies, and quality to our modular build process — and we’re just getting started.”
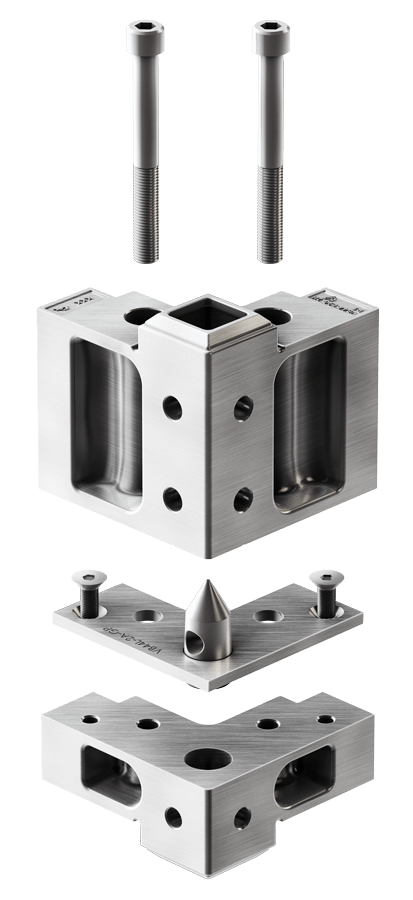
“The patented VectorBloc is unique in that it’s a vertical tension bolted system. In other words, via the in-plant welding process, the HSS [hollow structural sections] members are attached on all corners and intersections of each module to form a 3D cage or chassis system."
- Chris Waters, director of business development, Z Modular
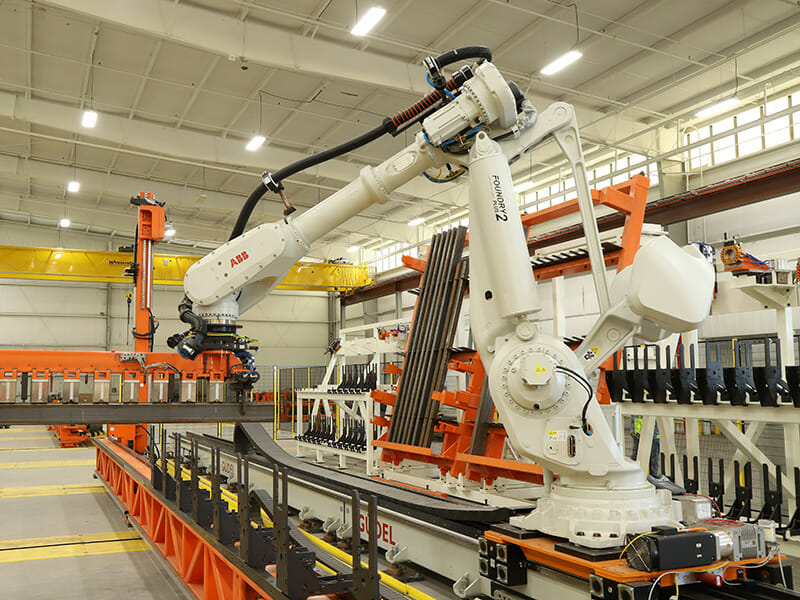
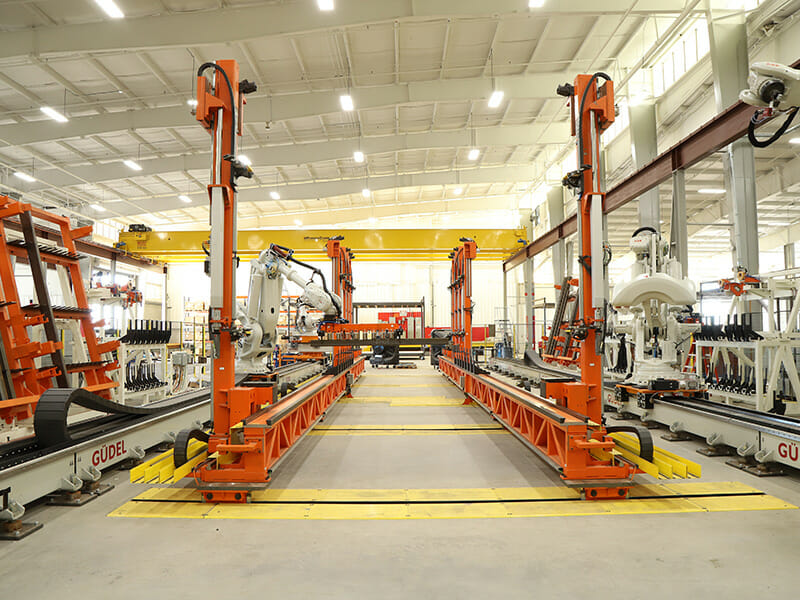
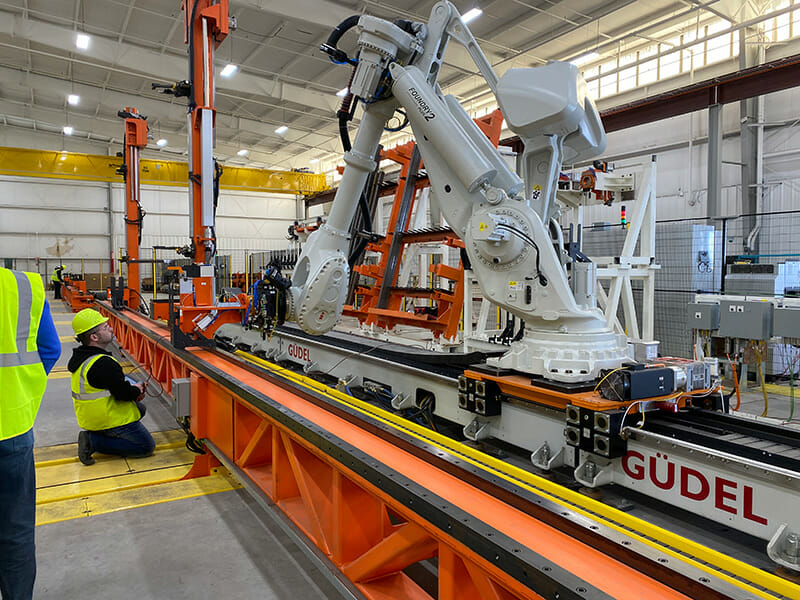
Standardization and the Z Modular Ecosystem
In an effort to make every project as efficient and cost effective as possible, Z Modular takes a ‘product line’ approach to construction, building consistency and standardization into everything they do. In addition to standardizing individual modules, they’ve also “developed pre-designed/pre-engineered multifamily unit layouts and further advanced and expanded that to entire building structure layouts.”
Although some may worry that this product line approach is limiting, Waters mentions that “although the layouts may be standardized, buildings can have different interior finishes and different exteriors — much like a Tesla Model S that is available in different colors. The benefits of standardization far outweigh the perceived drawbacks of any degree of uniformity.”
The company is witnessing the benefits of the product line approach — “removing uncertainty around cost, schedule, labor, quality, and supply chain” — while acting in the role of an integrated self-developer on their own projects. What the company calls its ‘ecosystem’ involves an integrated process, managing a construction project from beginning to end. “Integrating the off-site and on-site scopes of a modular construction project has traditionally proven to be extremely difficult,” Waters explains. “We’ve taken steps to vertically integrate our development-design-build process. From initial development planning, through design, supply chain, off-site fabrication, on-site installation and construction services, all the way to the certificate of occupancy.”
As the company continues to grow and evolve, Waters says, “We may entertain introducing this vertically integrated approach to larger third-party developers.”
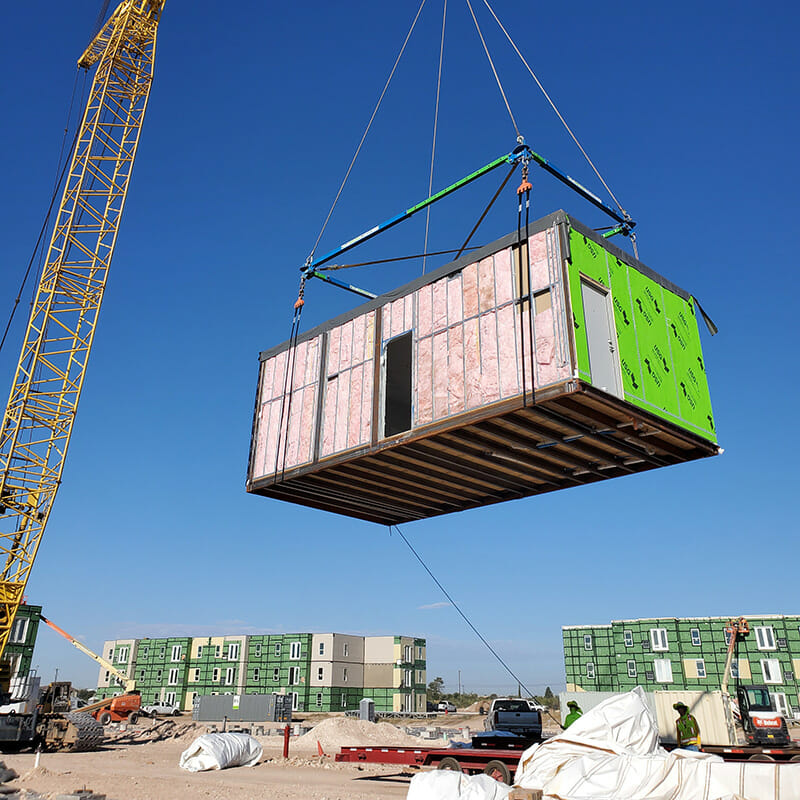
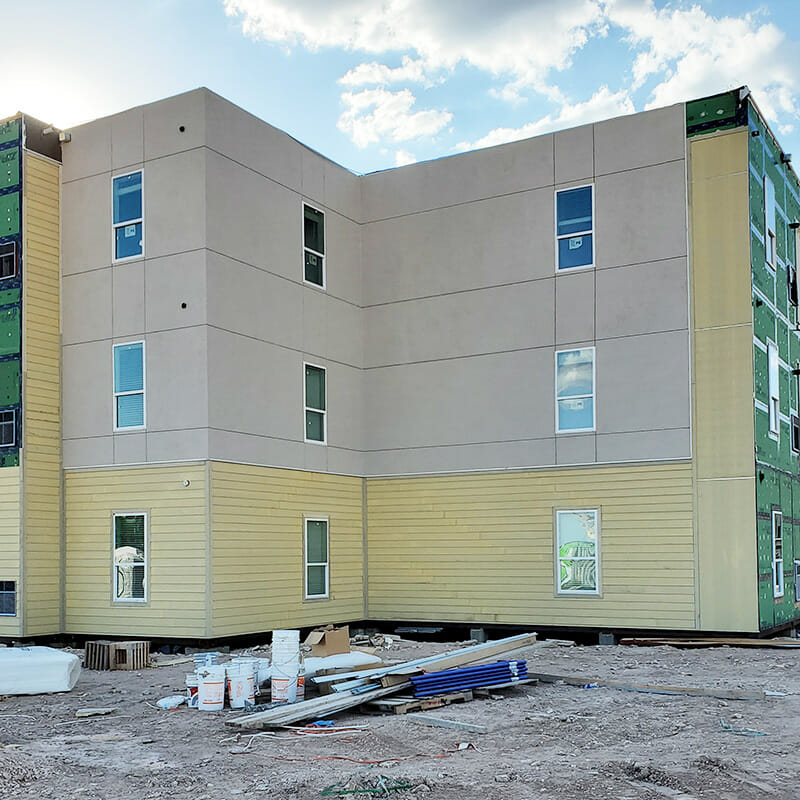
Projects and productivity
Z Modular is currently fabricating and installing 342 apartment units consisting of 684 modules for a nine-building multi-family development in Midland, Texas. They expect the first phase be ready to open early next year. “We’re using our product line approach to include the pre-designed/pre-engineered structures and we’re also controlling the entire on-site portion of the project.” They’re also working on a 180-apartment, 268-module complex in Phoenix, Arizona and they’re about 25% of the way through the installation process on that project.
“The modular industry is currently about 5% of the construction industry in North America. I think that in the next five to ten years, that’s going to become 10%. It won’t be just one or two companies driving that growth. There need to be several of us who are producing a high volume of product in high-output facilities,” Waters says. “There used to be very little technology in construction, but it’s increasing daily. In the modular industry, that means greater productivity and the potential to become a viable mainstream construction alternative. We’ll continue to do our part to drive industry growth.”
About the Author: Zena Ryder is a freelance writer, specializing in writing about construction and for construction companies. You can find her at Zena, Freelance Writer or on LinkedIn.
More from Modular Advantage
Oregon’s Prevailing Wage Proposal: A Wake-Up Call for Modular Construction
In early February, 2024, the Massachusetts Board of Building Regulations and Standards (BBRS) released its proposed 10th Edition building codes. This draft included several amendments targeting modular construction that would have created an extremely difficult environment for the entire modular industry and could have eliminated the industry entirely in the state.
Behind the Design of Bethany Senior Terraces, NYC’s First Modular Passive House Senior Housing Project
As more developers seek to meet new regulations for energy efficiency, the team at Murray Engineering has set a new record. With the Bethany Senior Terraces project, Murray Engineering has helped to develop NYC’s first modular structure that fully encompasses passive house principles — introducing a new era of energy efficiency in the energy-conscious city that never sleeps.
How LAMOD is Using Modular to Address Inefficiency, Sustainability, and the Future of Construction
As developers, designers, and contractors seek to understand the evolving needs of the modular industry, no one is as well-versed in the benefits of going modular as Mārcis Kreičmanis. As the co-founder and CBDO of LAMOD in Riga, Latvia, Mārcis has made it his ultimate goal to address the inefficiencies of traditional construction.
From Furniture Builder to ‘Activist Architect’: Stuart Emmons’ Unique Journey
Stuart Emmons was fascinated by buildings at a young age. He remembers building sand cities with his brother during trips to the Jersey shore. His father gave him his first drawing table at the age of ten. Today, he is an experienced architect who received his FAIA in June 2025. The road he took is unique, to say the least.
Forge Craft Architecture + Design: Codes, Contracts, and Intellectual Property
Founding Principal and Director of Modular Practice for Forge Craft Architecture + Design, Rommel Sulit, discusses the implications of codes, contracts, and intellectual property on
modular construction.
Eisa Lee, the “Bilingual” Architect
Now as the founder of XL
Architecture and Modular Design in Ontario, Canada, she applies not just her education as a traditional architect but an entire holistic view on modular design. It’s this expansive view that guides her work on being a true partner that bridges the gap between architects and modular factories as they collaborate on the design process.
Tamarack Grove Engineering: Designing for the Modular Sector
The role of a structural engineer is crucial to the success of a modular project, from initial analysis to construction administration. Tamarack Grove offers structural engineering services — project analysis, plan creation, design creation, and construction administration — for commercial, manufacturing, facilities, public services, and modular. Modular is only one market sector the company serves but it is an increasingly popular one.
Engineer Masters the Art of Listening to His Customers
Since founding Modular Structural Consultants, LLC. in 2014, Yurianto has established a steady following of modular and container-based construction clients, primarily manufacturers. His services often include providing engineering calculations, reviewing drawings, and engineering certification
Inside College Road: Engineering the Modules of One of the World’s Tallest Modular Buildings
College Road is a groundbreaking modular residential development in East Croydon, South London by offsite developer and contractor, Tide, its modular company Vision Volumetric (VV), and engineered by MJH Structural Engineers.
Design for Flow: The Overlooked Power of DfMA in Modular Construction
Unlocking higher throughput, lower costs, and fewer redesigns by aligning Lean production flow with design for manufacturing and assembly.