Maximizing Modular Design and Construction to Create Affordable Housing
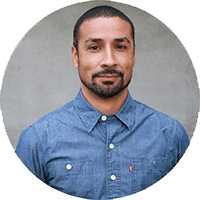
About the Author: Nick Gomez of Lowney Architecture has more than 15 years of experience working on multi-family housing and modular projects for nonprofit and for-profit clients. As the Oakland, Calif.-based firm’s Multi-family Studio Director, Nick has managed award-winning projects from design development through construction administration.
Volumetric modular design and construction can save time and money and create affordable, healthy housing. However, there are many ways this delivery method can go awry. By starting with the assumption that every building design is modular and then seeking to eliminate it, a project will employ the best delivery method for its circumstances. Lowney Architects completed its first modular multifamily project in San Francisco in 2013 and has since worked on over 60 multifamily and hotel projects totaling over 5,300 unit/keys. Clients include the factories themselves, market rate developers and LITC financed developers sponsoring affordable and supportive housing projects. Modular projects open up a world of possibilities, but also have pitfalls. Following are ways to optimize projects with buildings constructed offsite and how common pitfalls can be avoided.
Site selection is key.
Modular buildings are built with volumetric boxes that are craned onto the site-built foundations. Site access and staging areas are critical to identify, at least provisionally, upfront. There should be few, if any, aerial obstructions to make craning the boxes easier as the site’s geometry can limit the viability of this delivery method.
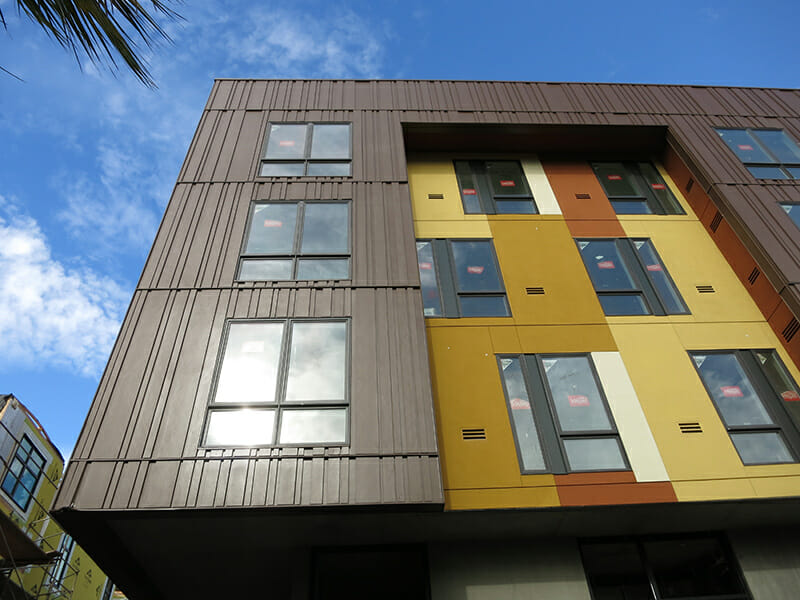
Pie shaped or irregularly shaped sites do not lend themselves to efficient layout of rectangular boxes. These sites should be eliminated; flat, rectilinear, sites that have dimensions close to multiples of the intended box sizes (up to 15’-10 x72’) are preferred. Zoning designation is also a critical factor in site selection. Most modular buildings are one foot taller per floor than their site-built alternative. Often modular buildings will not fit within the site’s zoning envelope because the zoning codes did not anticipate modular construction (check allowable building height first!). The lesson here is, don’t force it. Some sites are just not suitable for modular construction.
Keep every project modular possible for as long as possible.
It is far easier to “demodularize” a project than to redesign a site-built project to conform to the requirements of a factory. Become familiar with factory-built construction and understand the opportunities and limitations before designing. Keep a building organization simple, such as double-loaded corridors with walls that track across corridors in plan. Repetition is important but should not limit design. Always be clear about and evaluate what is the factory scope and what is the site scope; never confuse the two and constantly seek clarity as the design process unfolds. Try to work with SMEP engineers who have experience with modular and consult with them. Review exterior façade articulation and modular box stacking. Pay attention to vertical shaft layouts and exterior exhaust runs. Importantly, reach out to your preferred factory for input on constructability, module layout, and their scope in the overall project.
Design decisions are front-loaded in modular projects.
The good news is that this reduces the likelihood of change orders. The bad news is that this design process is vastly different from conventional site-built projects and can confound unsuspecting clients (and their teams). All decisions that the factory will act on - from structural issues to window locations to interior finishes and equipment - must be procured by the factory and installed in the module sometimes before a foundation is poured. Thus, the importance of “design freeze,” so that the factory can efficiently manufacture its modules.
Modular projects cost more to design than site-built projects, even though they cost less to build.
This is not only a result of the front-loaded design decisions process, but because modular projects typically require two building permits and, therefore, two drawing sets to get approved. The modular drawing set is approved by the state, the site scope is approved by the local municipality. Again, be clear on who is providing what (factory or GC) and who is reviewing what (state or city). This must be explicit in the drawings. Always have one team of professionals working on both drawing sets. Never have two teams working on the two separate drawing sets as this will result in confusion and items not getting fully coordinated. It is often beneficial to hold a brief explanatory seminar with novice city officials to help them understand what is modular design and construction, and more importantly, what their scope of review is. Cities, at times, can overstep their review scope, which delays projects and, in some instances, adds cost.
Modular is beautiful. But you must make it so.
Just because a building is manufactured in a factory does not determine it appearance. A modular building can assume the trappings of any architectural style if you respect factory optimization. The Mayfair mixed-use project in Albany, California pushes the limits of this last axiom. The City required the project to conform to its approved guidelines, which required a high degree of architectural expression that included building reveals, a “super portal”, and a muscular façade articulation. The result was done with a high degree of structural, factory and client coordination.
If the conditions are right, modular can be right.
Always seek to disprove the viability of modular against its site-built option. The further along in the design and construction process you go, the more expensive it is to change the project delivery approach.
It is becoming increasingly clear that the archaic construction approach deployed to solve today’s housing crisis is not up to the task. There are better ways to build affordable, decent housing. Modular is one way to do so.
Nick Gomez has over 15 years of experience working on multi-family housing and modular projects for both nonprofit and for-profit clients. As Director of Lowney Architecture’s Multi-family Studio, Nick has managed award-winning projects from design development through construction administration. To evaluate modular solutions for your project, Nick can be reached at nick@lowneyarch.com or 510.269.1107.
This article was first published in the Modular Advantage - November/December 2020 Edition.
More from Modular Advantage
AI, Faster Sets, and Automation: The Future of Modular is at World of Modular
While the modular building industry has long known that it can be an effective solution to increase affordable housing, the word is slowly spreading to more mainstream audiences. Three presentations at this year’s World of Modular in Las Vegas hope to provide insight and direction for those seeking a real solution to the crisis.
An Insider’s Guide to the 2025 World of Modular
The Modular Building Institute is bringing its global World of Modular (WOM) event back to Las Vegas, and with it comes some of the industry’s best opportunities for networking, business development, and education. Over the course of the conference’s four days, there will be numerous opportunities for attendees to connect, learn, and leverage event resources to get the most out of the conference.
Affordable Housing Now: The Industry’s Best Bring New Solutions to World of Modular
While the modular building industry has long known that it can be an effective solution to increase affordable housing, the word is slowly spreading to more mainstream audiences. Three presentations at this year’s World of Modular in Las Vegas hope to provide insight and direction for those seeking a real solution to the crisis.
Opportunities for Innovation in Modular Offsite Construction
Modular Offsite Construction has already shattered the myth that it only produces uninspired, box-like designs. Architectural innovations in module geometry, configurations, materials, and products make it possible to create visually stunning buildings without sacrificing functionality or efficiency.
Safe Modular Construction with Aerofilm Air Caster Transport
In collaboration with Aerofilm Systems, Heijmans developed innovative skids using air caster technology for moving modules easily and safely. These pallets are equipped with an auto-flow system, making operation extremely simple.
Miles, Modules, and Memes: Building a Modular Network One Flight at a Time
At the end of the day, social media is just another tool for building connections, and like any other tool, needs to be used skillfully to work properly. Use social media thoughtfully, and it will open doors to real opportunities and relationships you didn’t even see coming.
Falcon Structures: Thinking Inside the Box
Some of Falcon’s latest projects include creating container solutions for New York’s Central Park and an East Coast professional baseball team. More and more, Falcon is shipping out container bathrooms and locker rooms to improve traditionally difficult work environments, like those in oil and gas or construction.
UrbanBloc—From Passion to Industry Leader
UrbanBloc specializes in three main categories or markets – what they call “Phase 0” projects, amenities, and urban infill. Clients are often attracted to shipping containers because from a real estate perspective they are considered an asset. Having the flexibility to move and transport these assets allows owners to respond to different circumstances in a fluid manner that they can’t get with standard construction.
The Hospitality Game-Changer
“Hospitality is about more than just providing a service – it’s about delivering an experience,” says Anthony Halsch, CEO of ROXBOX. “And that’s where containers thrive. They allow us to create spaces that are unique, efficient, and sustainable.”
Container Conversions Counts on Simplicity to Provide Critical Solutions
Container Conversions has fabricated and developed thousands of containers for varied projects, including rental refrigeration options, offices, kitchens, temporary workplace housing, and mobile health clinics.