Falcon Structures: Thinking Inside the Box
Stephen Shang, CEO and co-founder of Falcon Structures, has a background in technology and venture capital deals. But in 2002, when the dotcom bubble burst, he decided he wanted to build a “real business.” He left San Francisco, created a new business, and never looked back.
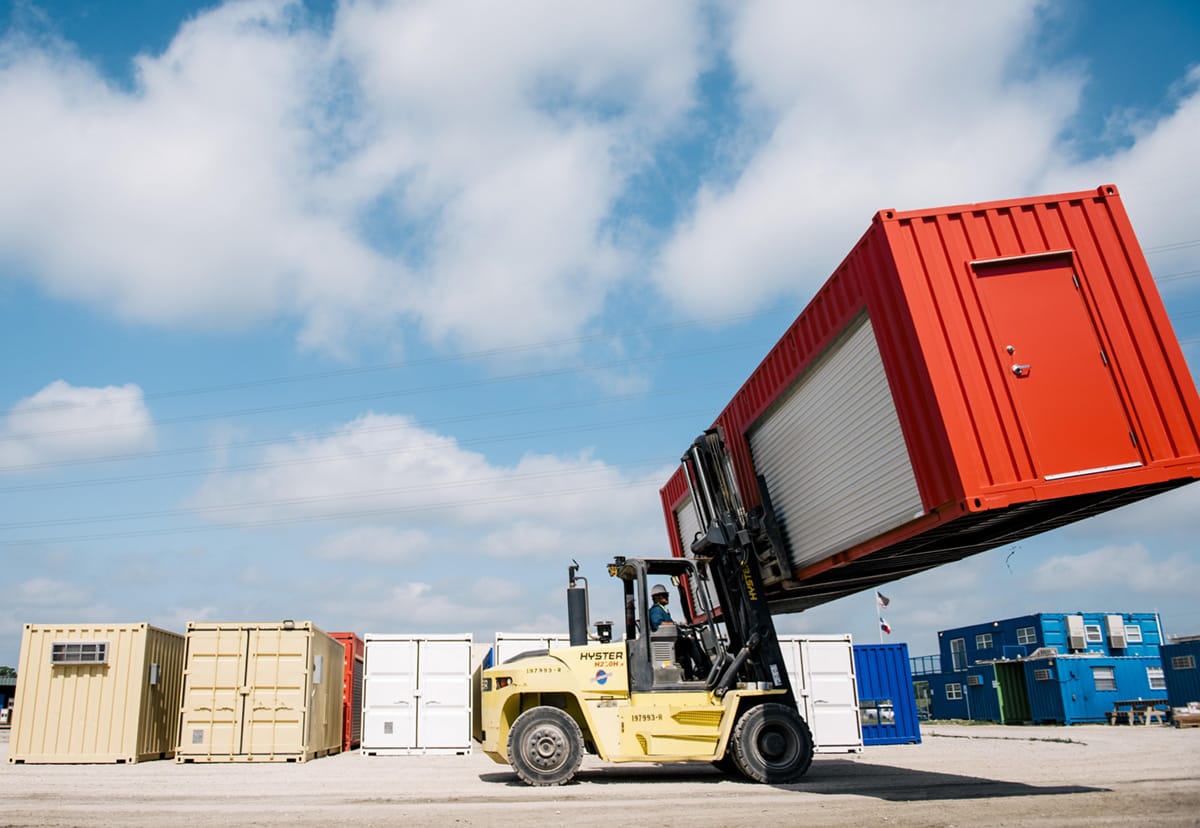
When Stephen Shang and Brian Dieringer launched Falcon Storage in 2003, the idea was straightforward: buy shipping containers, rent them out for storage, and keep things simple. But simplicity didn’t last long. By 2005, Falcon was turning ordinary steel containers into a wide variety of structures—and their vision had grown far beyond storage.
The company’s early projects were simple and functional with little engineering or design. Falcon basically added air conditioning and insulation to 20-foot or 40-foot containers.
“The market really loved that product, and they still do love that product,” says Shang, who serves as the company’s spokesperson. “But over the years we’ve seen that by starting with a structurally sound box, you could do all kinds of crazy things.”
One of the earliest and largest projects the company undertook was the creation of a 700-container simulated city in New Mexico for the Department of Defense.
“We applied a lot of the lessons learned from that project to industry,” Shang says.
A major focus for Falcon Structures today is employee advocacy. They noticed a pattern emerge, with their containers being deployed to some of the toughest, most unforgiving workplaces imaginable. A construction crew braving the scorching desert heat needed a field office to stay productive and cool. Factory workers handling toxic materials required a safe, functional locker room with showers to wash away the day. Laborers in remote areas needed more than a sweltering porta potty – they needed climate-controlled bathrooms that offered dignity and comfort.
“Companies are starting to pick up on this trend that to get and retain these workers – who are instrumental to our economy – you have to take better care of them. So, a lot of our product line is about taking care of employees.”
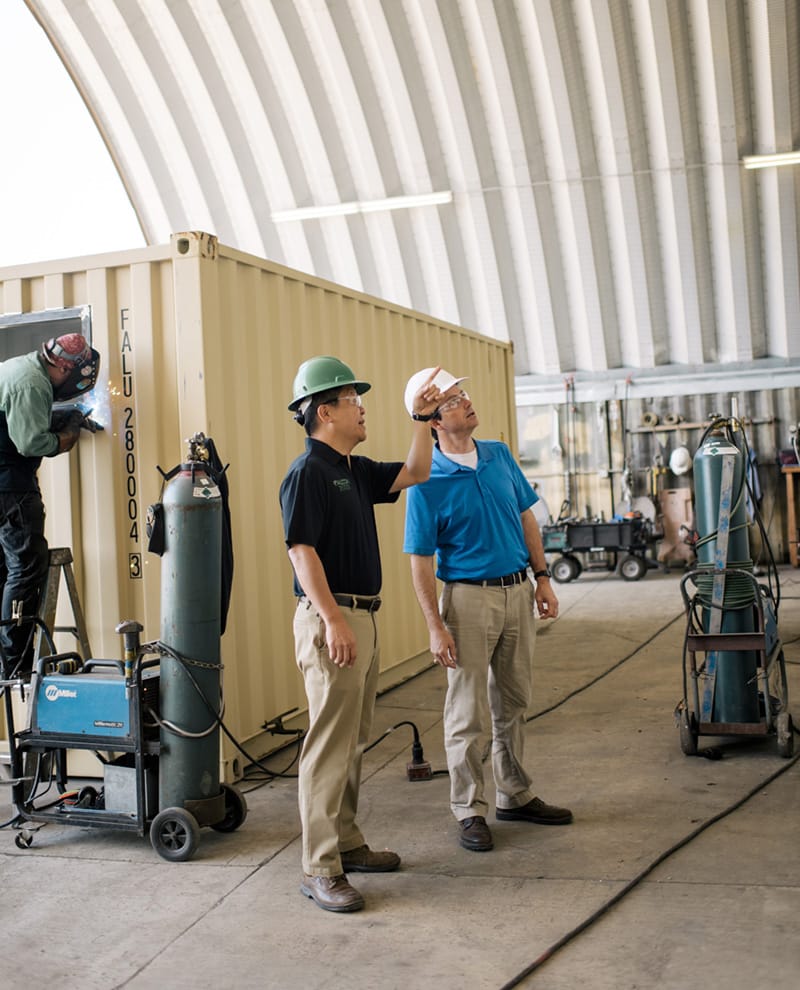
Stephen Shang and Brian Dieringer co-founded Falcon Structures together in 2003.
Creativity Flourishes within Constraints
Modified containers are extremely sturdy, quick to build and set up, and economical. When a business needs a quick, deployable structure, they make a lot of sense Starting with a box rather than starting from scratch has advantages for Falcon as well. An 8-foot-wide, 40-foot-long, and 9.5-foot-tall box places constraints upon the design—which Shang says is a good thing.
“We like to think inside the box,” Shang jokes. “When you start with a strong, sturdy frame, it forces you to innovate and maximize every inch of space. That’s where the magic happens—taking constraints and turning them into creative solutions.”
Geographically, Falcon serves companies everywhere in the U.S.—from the East Coast to the West Coast, from Alaska to the Caribbean, as well as Mexico and Africa.
“It’s a shipping container. It’s designed to travel the world,” says Shang.
Falcon’s modified containers can be as simple as a 20-foot office space, about 160 square feet, that sells for under $20,000.
Clients can customize the repurposed containers by selecting among options from Falcon’s design library to add to the basic model, including different brands of HVAC systems, upgraded floors, or multiple windows. It’s a delicate balance, Shang shared, toeing the line of being a manufacturer with clean processes in a construction-like environment.
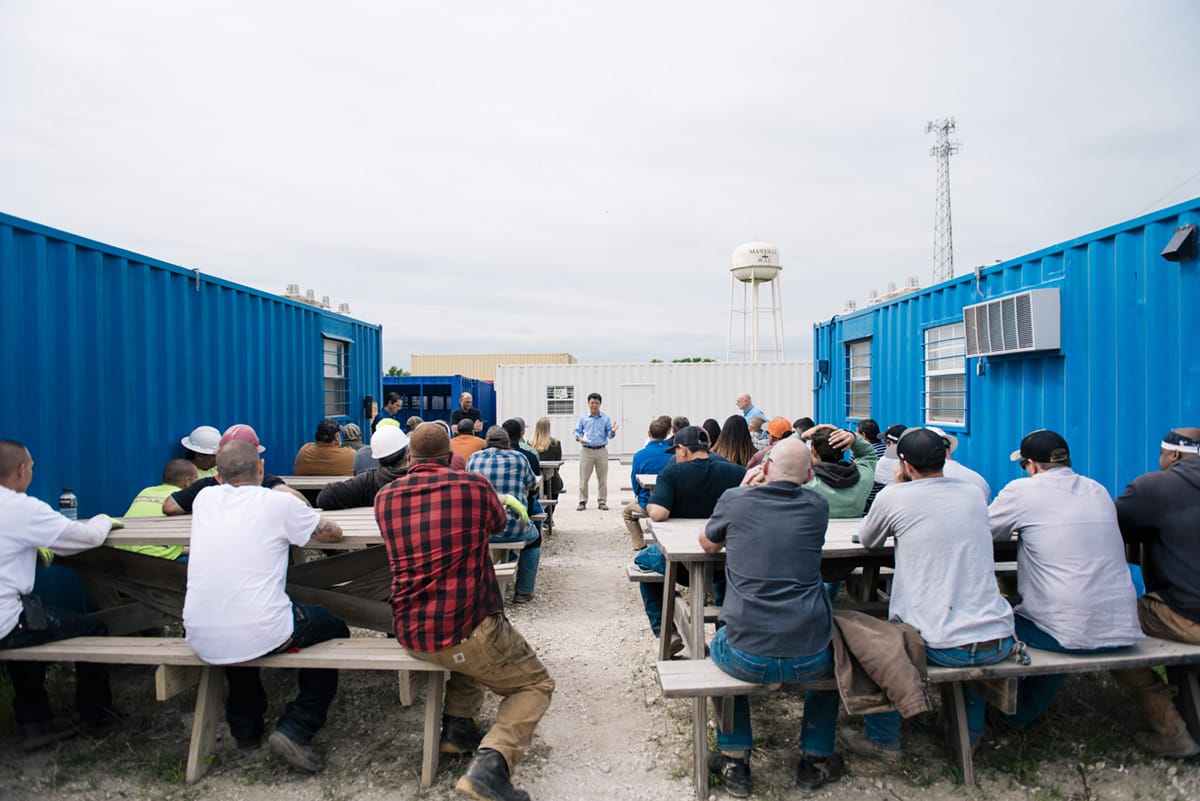
Falcon’s culture of one team across production and office workers is highly important to the company.
“Or it’s like Burger King,” Shang says. “We’ve made it so you can have it your way. That’s where the secret sauce is.”
As the company evolved, it built containers for a wide variety of different uses—equipment enclosures, offices, vertical farms, food and beverage units, disaster recovery, storage space, manufacturing space, changing/shower areas for workers dealing with toxic materials, bathrooms, and sleeping/living quarters for remote site operations.
The team thinks they’ve only scratched the surface.
“Modified containers fulfill an important niche in the modular industry,” Shang says. “There’s great market potential and a lot of excitement around them.”
Some of Falcon’s latest projects include creating container solutions for New York’s Central Park and an East Coast professional baseball team. More and more, Falcon is shipping out container bathrooms and locker rooms to improve traditionally difficult work environments, like those in oil and gas or construction.
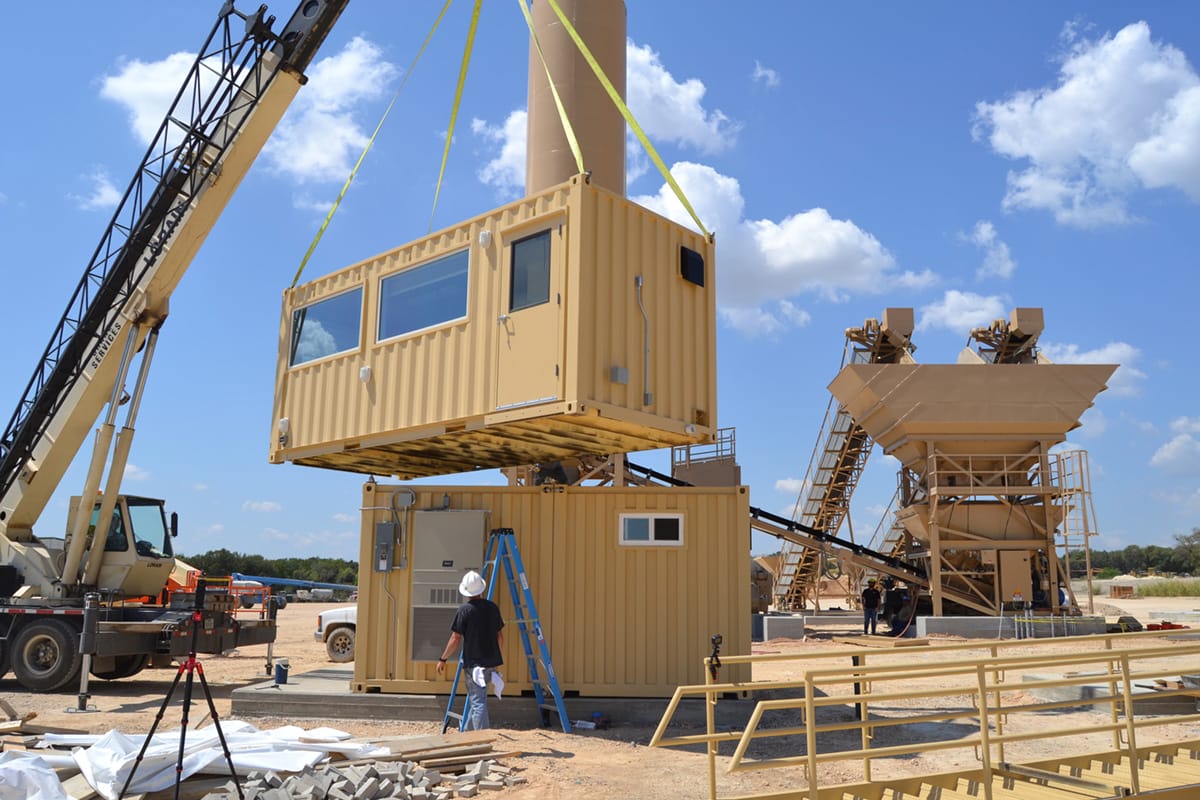
Modified shipping containers thrive in industrial, rugged environments, like this two-story observation workspace for an aggregate company.
Vision to Reality: How Falcon Delivers Custom Containers
Falcon’s process begins with a floor plan from their library of designs. Their team guides the customer through modification options for a customized solution, then provides a quote. Once the customer signs off on that piece, the design team creates shop drawings that include everything that will go into the container and specify how it will be laid out.
“We want to make sure we get this right on paper before we start swinging hammers,” Shang says. “There’s no undo button once we start on it in the factory.”
Then production begins. The container goes through phases like carpentry, insulation, electrical, and mechanical. Once the container is finished, it goes through a thorough quality control process before shipping off to its final destination.
The entire process typically takes six to eight weeks.
The State of the Industry
“The container industry is still in its teenage years,” Shang says with a grin. “We’re just getting started, and the only limit is our imagination. Every project pushes boundaries and proves what’s possible inside the walls of a box.”
Initially, there were no building codes for containers. But in 2021, thanks to efforts of the Modular Building Institute (MBI), shipping containers are now included in the building codes. However, many code issues and regulation concerning using them as building products still need to be resolved. Shang says it will happen through collaboration. Through his work with MBI, he interacts with the International Code Council, working alongside building code officials to rewrite or edit building codes.
“Codes ensure that we can build safe structures that are suitable for public use,” says Shang, who will become MBI’s President of the Board in 2025. “Getting everyone on the same page and educating the industry is critical.”
Shang says having codes for building containers accomplished two things. “One, it has taken out fly-by-night companies who don’t want to follow the rules. And two, it has given the people in the industry who take it seriously guidelines for building safely.”
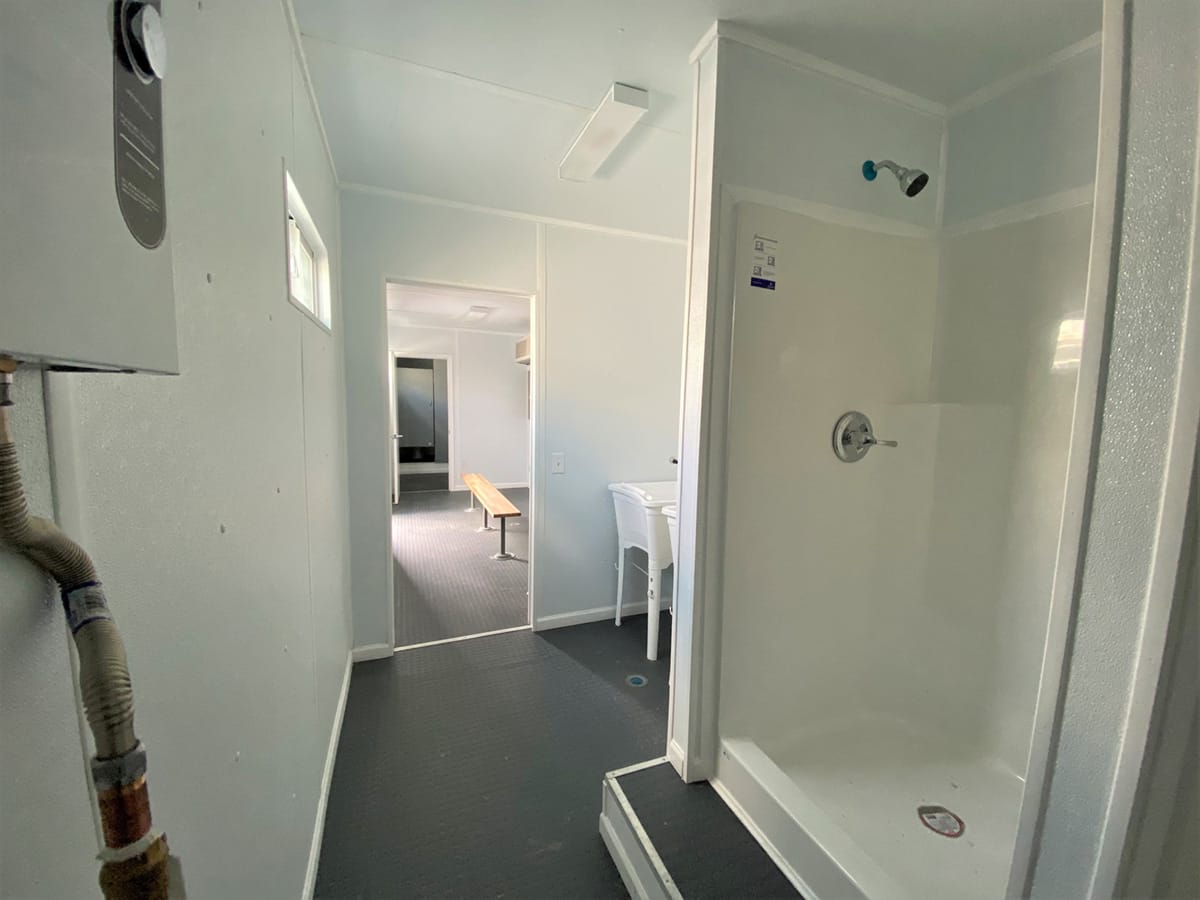
Outfitted with full plumbing, containers with showers and toilets provide climate-controlled locker rooms for blue-collar workers where traditional construction isn’t feasible.
Approximately 17 million shipping containers are in circulation today in ports worldwide. An estimated 11 million are currently unused and just sitting around. But not all of them are acceptable for repurposing. A common misconception is that containers are free or very cheap—that ports practically give them away.
Falcon purchases some containers directly from factories in Asia. One-trip containers (brand new containers that arrive in the U.S., are unloaded, and purchased) are by far the most common type used for repurposed containers. The steel components can be traced, plus buyers know what cargo was stored in it. Other containers come from leasing companies or port depots.
“We’ve developed a very sophisticated supply chain over the last 20 years,” Shang says. “Getting the container is the easy part of the whole process.”
Purpose-Driven Challenges
Starting out, the main challenge for the two co-founders was to build a product that was “just right.” Now that the company has been modifying containers for more than 20 years and has nearly 80 employees, its challenge has changed. Now the focus is on creating a company culture that ensures all employees care about the customer and do great work.
“Creating a culture of excellence is really hard to do, and you can lose it in an instant,” Shang says.
He believes transparency and communications are critical to creating that culture. Every morning, Falcon kicks off the day with a five-minute huddle—a fast-paced, no-frills check-in where teams share their top priority. It’s like a daily team rally, ensuring every department stays aligned and energized. This culture of communication isn’t just about efficiency; it’s the heartbeat of Falcon’s success.
“It creates that culture, that cohesion, that allows us to communicate freely with one another,” Shang says.
Take the company Christmas party, for example. It used to be held at a swanky downtown Austin restaurant, but attendance from the production crew was sparse. The solution? Bring the celebration home. Today, the party unfolds right in Falcon’s production area, transformed with festive decorations and brimming with camaraderie. From an annual (and sometimes contentious) egg toss challenge to team games, the event is now a true reflection of Falcon’s culture: inclusive, fun, and all about connection. Nearly 95% of employees join in, proving that sometimes, the best memories are made close to where the magic happens.
“Fostering a culture of excellence and genuinely supporting our employees has been one of our most rewarding challenges,” Shang says. “To me, it’s the ultimate measure of a company’s success.”
About the Author: Shari Held is an Indianapolis-based freelance writer who has been covering the construction industry for more than 20 years.
More from Modular Advantage
Oregon’s Prevailing Wage Proposal: A Wake-Up Call for Modular Construction
In early February, 2024, the Massachusetts Board of Building Regulations and Standards (BBRS) released its proposed 10th Edition building codes. This draft included several amendments targeting modular construction that would have created an extremely difficult environment for the entire modular industry and could have eliminated the industry entirely in the state.
Behind the Design of Bethany Senior Terraces, NYC’s First Modular Passive House Senior Housing Project
As more developers seek to meet new regulations for energy efficiency, the team at Murray Engineering has set a new record. With the Bethany Senior Terraces project, Murray Engineering has helped to develop NYC’s first modular structure that fully encompasses passive house principles — introducing a new era of energy efficiency in the energy-conscious city that never sleeps.
How LAMOD is Using Modular to Address Inefficiency, Sustainability, and the Future of Construction
As developers, designers, and contractors seek to understand the evolving needs of the modular industry, no one is as well-versed in the benefits of going modular as Mārcis Kreičmanis. As the co-founder and CBDO of LAMOD in Riga, Latvia, Mārcis has made it his ultimate goal to address the inefficiencies of traditional construction.
From Furniture Builder to ‘Activist Architect’: Stuart Emmons’ Unique Journey
Stuart Emmons was fascinated by buildings at a young age. He remembers building sand cities with his brother during trips to the Jersey shore. His father gave him his first drawing table at the age of ten. Today, he is an experienced architect who received his FAIA in June 2025. The road he took is unique, to say the least.
Forge Craft Architecture + Design: Codes, Contracts, and Intellectual Property
Founding Principal and Director of Modular Practice for Forge Craft Architecture + Design, Rommel Sulit, discusses the implications of codes, contracts, and intellectual property on
modular construction.
Eisa Lee, the “Bilingual” Architect
Now as the founder of XL
Architecture and Modular Design in Ontario, Canada, she applies not just her education as a traditional architect but an entire holistic view on modular design. It’s this expansive view that guides her work on being a true partner that bridges the gap between architects and modular factories as they collaborate on the design process.
Tamarack Grove Engineering: Designing for the Modular Sector
The role of a structural engineer is crucial to the success of a modular project, from initial analysis to construction administration. Tamarack Grove offers structural engineering services — project analysis, plan creation, design creation, and construction administration — for commercial, manufacturing, facilities, public services, and modular. Modular is only one market sector the company serves but it is an increasingly popular one.
Engineer Masters the Art of Listening to His Customers
Since founding Modular Structural Consultants, LLC. in 2014, Yurianto has established a steady following of modular and container-based construction clients, primarily manufacturers. His services often include providing engineering calculations, reviewing drawings, and engineering certification
Inside College Road: Engineering the Modules of One of the World’s Tallest Modular Buildings
College Road is a groundbreaking modular residential development in East Croydon, South London by offsite developer and contractor, Tide, its modular company Vision Volumetric (VV), and engineered by MJH Structural Engineers.
Design for Flow: The Overlooked Power of DfMA in Modular Construction
Unlocking higher throughput, lower costs, and fewer redesigns by aligning Lean production flow with design for manufacturing and assembly.