Revelution Containers and S. I. Container Builds: On a Mission to Revelutionize Housing
When Rory Rubin and Pamela Bardhi met, it turned out to be a “match made in heaven.”
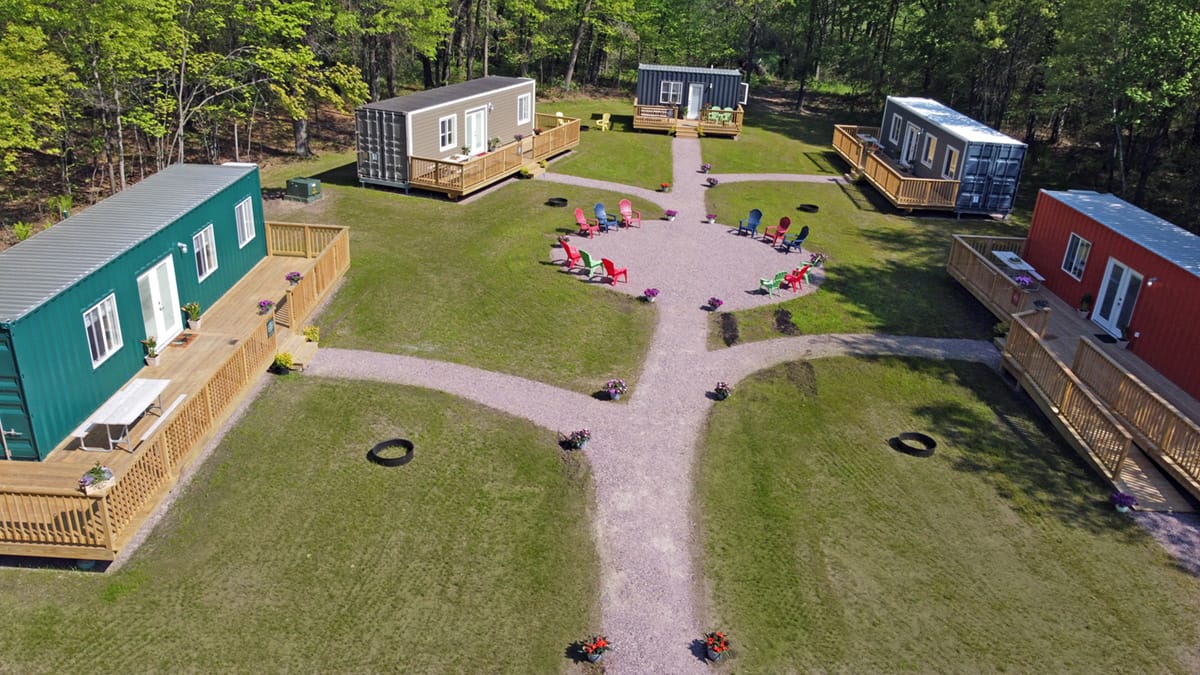
Rory Rubin founded S.I. Container Builds six years ago to manufacture affordable housing made from shipping containers in partnership with other organizations. The company serves B2B clients, such as developers, non-profit groups and other commercial groups.
“You always want to focus on what you’re good at and not do everything,” says Rubin, founder and CEO, of S.I. Container Builds in Chicago, Ill. “Pam was the missing link for us.”
Pam Bardhi, real estate developer and founder of Revelution Containers in Boston, Mass., has been a real estate developer for almost 11 years—mainly in traditional construction. She was fascinated with the idea of developing projects featuring accessory dwelling units (ADUs)—smaller, independent living spaces on the same lot as a single-family home to help homeowners unlock wealth in their backyard.
For their first project together, Bardhi purchased an ADU from S. I. Container Builds to place in her own backyard so she could understand the process and the build itself.
The two businesswomen began working together and found that more than their skillsets meshed. Their missions were also in sync.
“It’s a two-fold mission,” Bardhi says. “One is to create ADUs and help homeowners unlock wealth in their backyards. The other piece of the mission is creating sustainable and intentional communities utilizing shipping containers.”
Why Repurpose Shipping Containers?
“We have a duty to recycle and repurpose things we’ve created before we start from scratch,” Rubin says. “If shipping containers are not used for transport, they go into a container graveyard, never to be used again. Plus, steel containers have the structural integrity that will outlast stick-built homes.”
Their built-out 40-foot containers weigh approximately 18,000 pounds. Once it’s bolted to the foundation, it’s practically indestructible and will withstand hurricanes, tornadoes, fires and other natural disasters.”
Rubin purchases quality, one-trip containers from reputable brokers all over the country. One-trip containers are loaded with cargo overseas, unloaded in the U.S., and then sold to builders like Rubin.
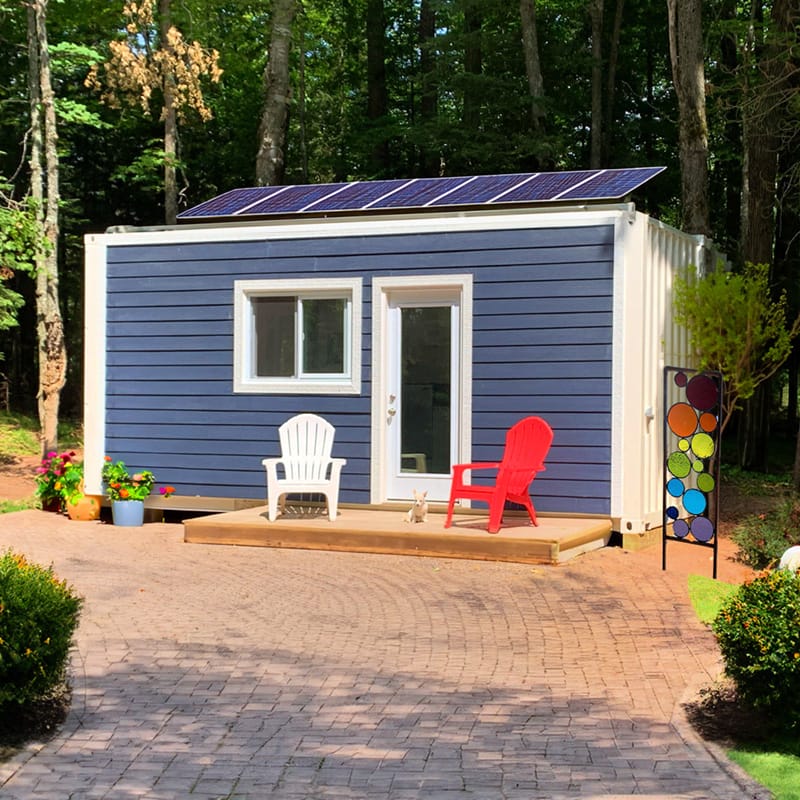
Shipping containers are perfect for ADUs. Given their rectangular shape, they fit on nearly any size or shape lot. Utilizing piers for support, they can be built in places that typically couldn’t be built on before. Then, there’s the fact that they are mobile. They can easily be shipped by truck, train or ship.
There are a million uses for ADUs—in-law suites or extended family home, guest house, pool house, a workshop, personal office or a rental unit. They can be built to accommodate whatever the homeowner needs.
“I see this as a wonderful steppingstone in the continuum of care as we age and want to keep our families close together,” says Rubin, who has a background as a clinical social worker. “Wouldn’t it be wonderful if your parents’ first line of support was in your backyard while they’re still independent?”
ADUs are affordable. But Rubin cautions that if a quote sounds too good, don’t jump on it without doing your research. There’s much misinformation on the internet. She advises working with reputable, experienced companies that buy one-trip containers and build to code.
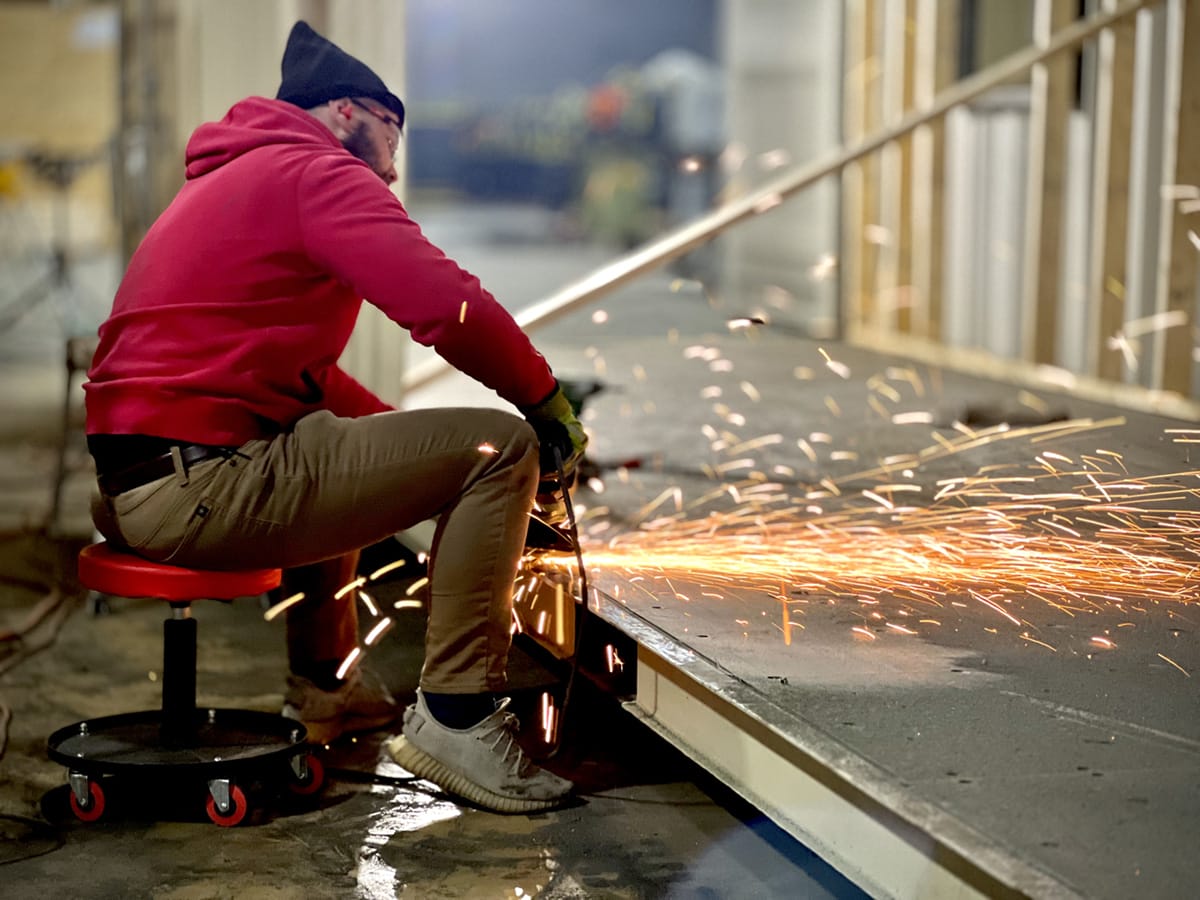
Build time is approximately eight to 12 weeks once plans are permitted. Once the containers are built, they are shipped to their destination where S.I. Container Builds works with local set crews to put them together and finish them on site.
“The expansion of ADUs is a core focus of what we’re building,” Bardhi says.
One of the largest obstacles to homeowners purchasing ADUs is financial accessibility. Homeowners can’t make money from a rental property if they can’t afford to build it. Bardhi partnered with CMG Financial, who will offer homeowners ADU loans—conventional loans that essentially serve as a second mortgage so they can get ADUs for a 95% loan to value ratio. If they have sufficient equity in their property, no down payment is required.
Scratching the Surface
While using shipping containers for housing and other uses is common in other countries, it’s relatively new to the U.S. “Globally, they are building really
great things such as a beautiful multi-story hotel in London,” Rubin says.
The upscale Stow-Away Hotel is built from 26 repurposed shipping containers and is billed as “swanky” and “chic.”
“We’re getting there,” Rubin says. “We’re understanding how to use shipping containers like Legos, how to stack them, how to engineer them correctly. If you can think of it, we can build it.”
Bardhi adds: “Containers are made to be stacked—think of how they cross the ocean in the first place”.
Meanwhile, the U.S. is scratching the surface. “There’s a lot more to come, which is super exciting for us,” Bardhi says.
Developing White Heather Farm
Bardhi and Rubin are currently partnering on the White Heather Farm project, a multi-million dollar, multi-unit sustainable, intentional community in Bridgewater, Mass., just 35 minutes outside Boston.
“The first project was smaller,” Rubin says. “I knew the steps and the process and everything was straightforward. With this new project, we’re entering a whole new scale of building.”
The plan calls for renovating the existing farmhouse and transforming the barn into a community clubhouse. The development, a blend of townhouses and ADUs, will be three-bedroom, two-bath units, roughly 1,964 square feet each, and have a simple, timeless, modern farmhouse look. The farm has an apple orchard and greenhouses, a community garden and a farm stand where homeowners can sell their produce are also planned.
The units will feature water filtration systems, battery energy storage and solar panels for energy savings. Options for upgrades are available.
“What I’m creating is a community that is essentially going to be self-sustaining,” Bardhi says. “A new way of conscious living with sustainability and intentionality.”
If no special permitting is required, Bardhi anticipates the project can be completed in 18 months. But the planning process is complex, requires patience, and is dependent upon others.
Bardhi has shared her vision with local agents and homeowners. The reaction has been tremendously positive. She’s been told the project will sell out—and fast.
Facing Challenges
“The building is actually the easiest part,” Rubin says. “We know what we’re doing and we can build it fairly quickly. It’s all the other layers that are involved before you can get to the build that are challenging. That’s what we’re learning through it all.”
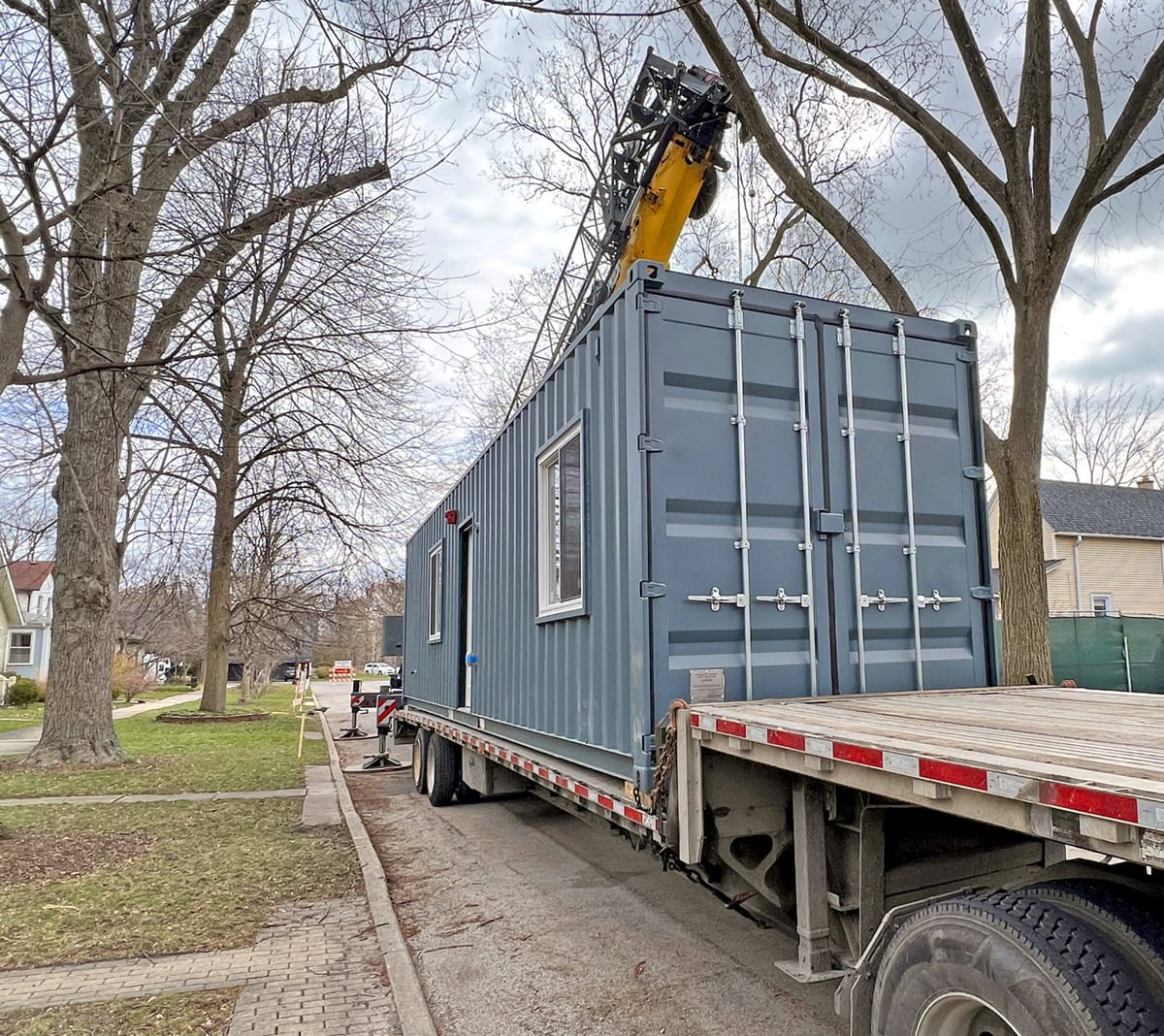
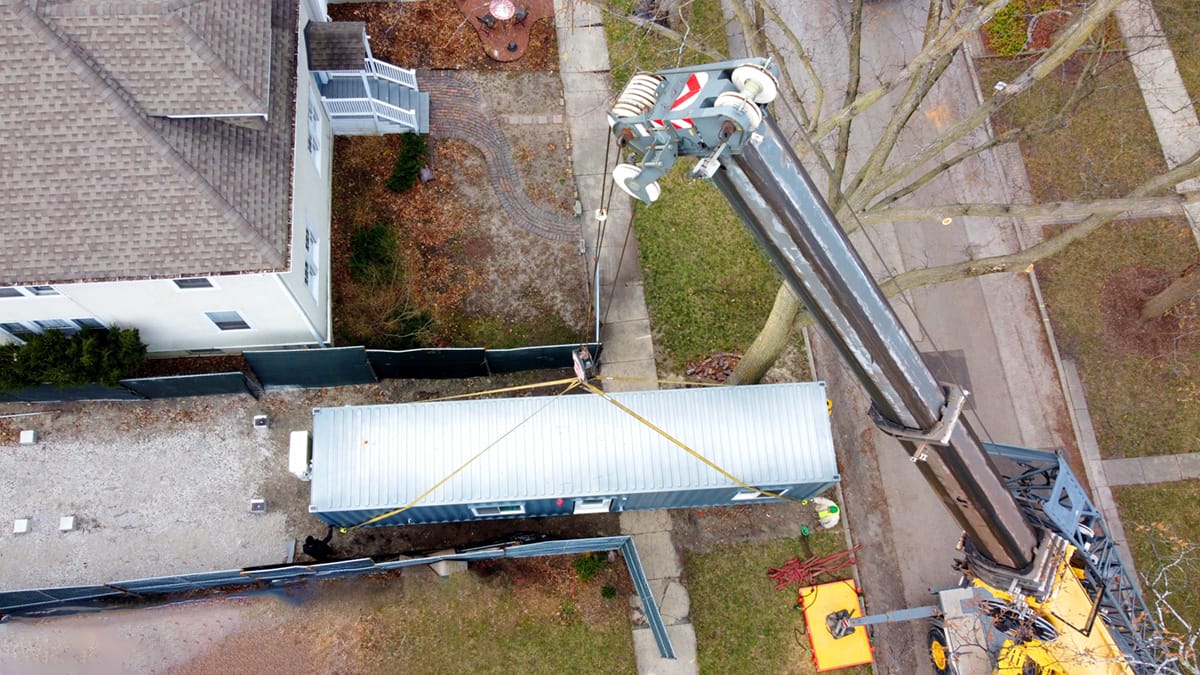
Development isn’t easy. If you don’t have a particular skillset the project requires, you must partner with those who do at different points during the project.
For example, the professionals involved in the White Heather Farm project include the architect, civil engineer, structural engineer, attorney to handle permitting, real estate agent, developer, construction crew—plus the architects, engineers and building team at S.I. Container Builds.
Unexpected bumps in the road such as changes in a by-law or building code can throw everyone’s schedule off.
The four main challenges are zoning, infrastructure, ensuring the project meets all the building codes, and finding the funding to finance the project. For example, Bardhi’s financers will cover 70% of the vertical construction, but she must raise capital separately for the infrastructure.
Bardhi also has to ensure the community that shipping container buildings are going to blend in with the fabric of the existing neighborhood.
“Every time I talk to people about container buildings, I get one of two reactions,” Bardhi says. “One, ‘Oh my god, that’s cool!’ Or, ‘Heck no, that’s not going into my neighborhood.”
This is because of the misnomer that containers are simply rusty old boxes. Both Bardhi and Rubin are on a mission to change that thought. Fortunately, most reactions are positive.
“It’s going to get easier because Pam hopes to repeat this process over and over again,” Rubin says. “All the things that are pain points now won’t be pain points next time. Every project is a lesson.”
Looking Ahead
What’s ahead for Bardhi and Rubin? They plan to build more shipping container eco communities similar to single-family subdivisions, and mixed-use buildings in urban settings. They also want to expand the footprint of ADUs across the nation.
“Revolutionizing housing in America,” Bardhi says, “that’s really our mission. And from there we want to continue to build these sustainable and intentionally conscious communities.”
Rubin is a licensed builder in all 50 states, so there’s no geographical limit to where they can build U.S. communities.
Currently Rubin is planning a home for Habitat for Humanity and an amenity building at Chicago’s famous Navy Pier. Also, S.I. Container Builds is partnering with Shelter Inc., with a grant from DCFS to build a group home (6,400 square feet or the equivalent of 20 containers) for girls who have been trafficked in Illinois.
Bardhi also works with Habitat for Humanity with the mission to expand accessible housing.
“This is all super exciting,” Bardhi says. “Learning new things is fun, right? There’s going to be a lot more container developments coming.”
Rubin could not agree more.
About the Author: Shari Held is an Indianapolis-based freelance writer who has been covering the construction industry for more than 20 years.
More from Modular Advantage
Behind the Design of Bethany Senior Terraces, NYC’s First Modular Passive House Senior Housing Project
As more developers seek to meet new regulations for energy efficiency, the team at Murray Engineering has set a new record. With the Bethany Senior Terraces project, Murray Engineering has helped to develop NYC’s first modular structure that fully encompasses passive house principles — introducing a new era of energy efficiency in the energy-conscious city that never sleeps.
How LAMOD is Using Modular to Address Inefficiency, Sustainability, and the Future of Construction
As developers, designers, and contractors seek to understand the evolving needs of the modular industry, no one is as well-versed in the benefits of going modular as Mārcis Kreičmanis. As the co-founder and CBDO of LAMOD in Riga, Latvia, Mārcis has made it his ultimate goal to address the inefficiencies of traditional construction.
From Furniture Builder to ‘Activist Architect’: Stuart Emmons’ Unique Journey
Stuart Emmons was fascinated by buildings at a young age. He remembers building sand cities with his brother during trips to the Jersey shore. His father gave him his first drawing table at the age of ten. Today, he is an experienced architect who received his FAIA in June 2025. The road he took is unique, to say the least.
Forge Craft Architecture + Design: Codes, Contracts, and Intellectual Property
Founding Principal and Director of Modular Practice for Forge Craft Architecture + Design, Rommel Sulit, discusses the implications of codes, contracts, and intellectual property on
modular construction.
Eisa Lee, the “Bilingual” Architect
Now as the founder of XL
Architecture and Modular Design in Ontario, Canada, she applies not just her education as a traditional architect but an entire holistic view on modular design. It’s this expansive view that guides her work on being a true partner that bridges the gap between architects and modular factories as they collaborate on the design process.
Tamarack Grove Engineering: Designing for the Modular Sector
The role of a structural engineer is crucial to the success of a modular project, from initial analysis to construction administration. Tamarack Grove offers structural engineering services — project analysis, plan creation, design creation, and construction administration — for commercial, manufacturing, facilities, public services, and modular. Modular is only one market sector the company serves but it is an increasingly popular one.
Engineer Masters the Art of Listening to His Customers
Since founding Modular Structural Consultants, LLC. in 2014, Yurianto has established a steady following of modular and container-based construction clients, primarily manufacturers. His services often include providing engineering calculations, reviewing drawings, and engineering certification
Inside College Road: Engineering the Modules of One of the World’s Tallest Modular Buildings
College Road is a groundbreaking modular residential development in East Croydon, South London by offsite developer and contractor, Tide, its modular company Vision Volumetric (VV), and engineered by MJH Structural Engineers.
Design for Flow: The Overlooked Power of DfMA in Modular Construction
Unlocking higher throughput, lower costs, and fewer redesigns by aligning Lean production flow with design for manufacturing and assembly.
Choosing the Right Ramp
Modular construction offers a compelling alternative to traditional methods for designing and building ADA and IBC-compliant entrances. By addressing the challenges of traditional construction, such as time-consuming processes, unavailable specialized labor, and variable field conditions, modular solutions provide a more efficient, cost-effective, and reliable approach.