Strong, Resilient, Sea-Crossing Boxes Repurposed Efficiently As Homes
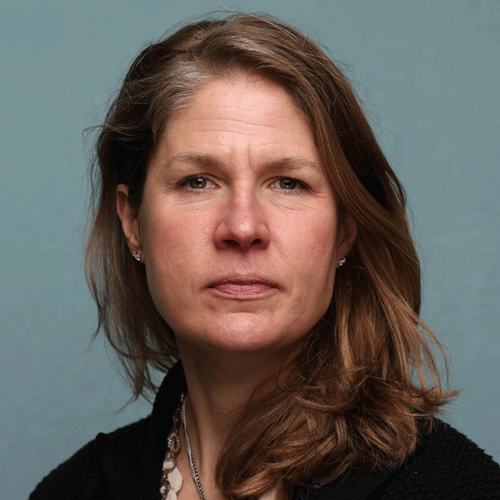
Jennifer Castenson is a contributing writer to Forbes.com.
Since shipping containers were first introduced in 1956, they have carried trillions of dollars of goods across the oceans, and as exports became more popular over the years, so did the manufacture of shipping containers.
To answer demand, shipping containers have been manufactured in excess, to the point that some sit without being used. Creative designers saw that unused product, recognized its strength, resiliency, size and structure, and soon imagined it as a home. Now, in an environment where housing is in critical demand, shipping containers have been used in all types of housing.
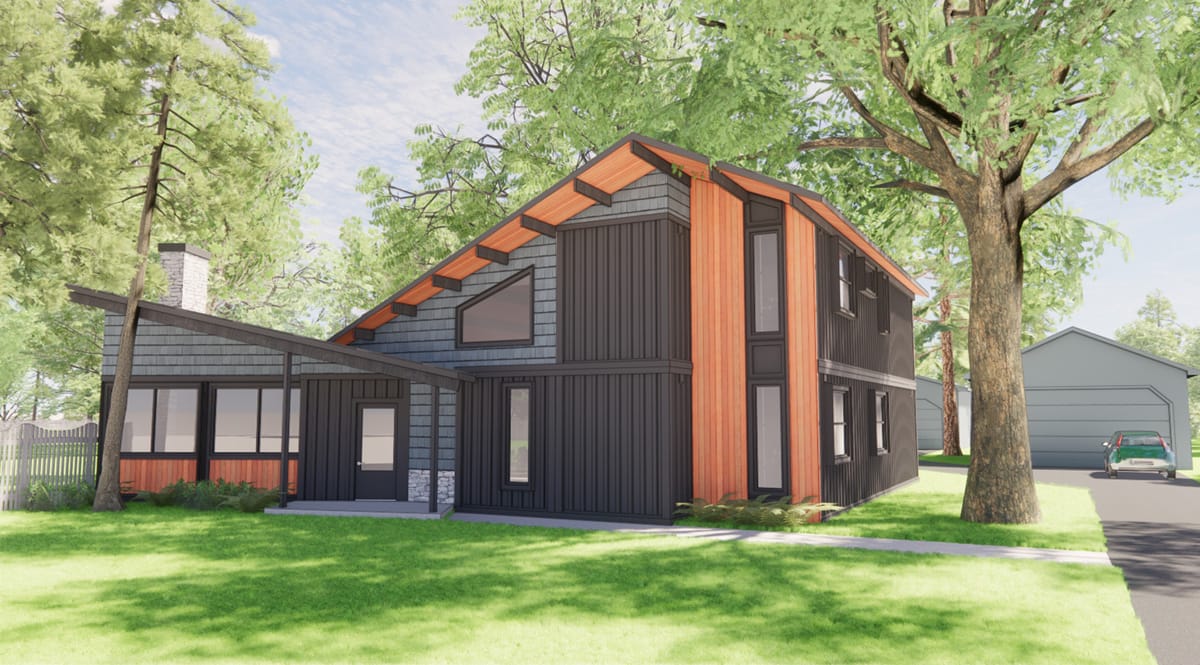
The Mariposa Home, designed by Three Squared, is a multigenerational home constructed in Ohio using eight shipping containers where each generation designed their own wing of the home and the two generations worked together to design the common space.
Shipping Containers Through the Years
In 1987, Phillip Clark was recorded as the first to use a shipping container as a home, and then filing a patent to document how to modify shipping containers to be turned into living quarters. Several others quickly followed with different housing applications, but the movement didn’t gain real momentum until after 2007 when the first shipping container home was built in the U.S. by architect Peter DeMaria.
Since then, the trend has continued, bringing all types of architecture, from customized, one-container, luxury dwellings to stacked, affordable housing complexes.
The Making of Building Codes
With the container’s growing popularity as a housing structure, the International Code Council worked to develop building code requirements for the resulting structures. Ryan Colker, the council’s vice president of innovation, says that the codes were developed by a joint committee with the Modular Building Institute to eventually create a guideline that was released in 2019.
The new section of building code was published in 2021 with an outline of design and performance requirements to ensure its effective use. The guide includes requirements on anchors, welding, structural integrity, foundation, and material properties. It also provides details on penetration and bracing requirements.
Supply Chain Dynamics
Ken Pinto is the owner of global supply chain consulting group Kenzai USA and has been heavily invested in housing supply dynamics for decades. He reports that since COVID there has been an excess of shipping containers.
He writes that in the past decade, there was an average annual container production of 2.6 million twenty-foot containers. In 2021, almost 5.2 million were manufactured, which has driven a surplus of containers and its associated trailer chassis.
And, although there are plenty of shipping containers moving around and available to be used for creative housing projects, Pinto says that building products shipping from overseas could still have big challenges ahead.
“There are real threats to the supply chain,” he said. “Anyone looking for shipping containers should still have an eye on pirate attacks, another pandemic, war, and droughts drying up canals. These all have real potential to disrupt the supply chain.”
He believes that shipping containers have many practical purposes, but doesn’t consider housing to be top of the list.
“I love the innovation that is coming through with shipping container homes and 3D printing,” he said. “Builders are kidding themselves if they think that they can survive without making serious changes to what they deliver. It’s critical to innovate in this market and I welcome all new ideas.”
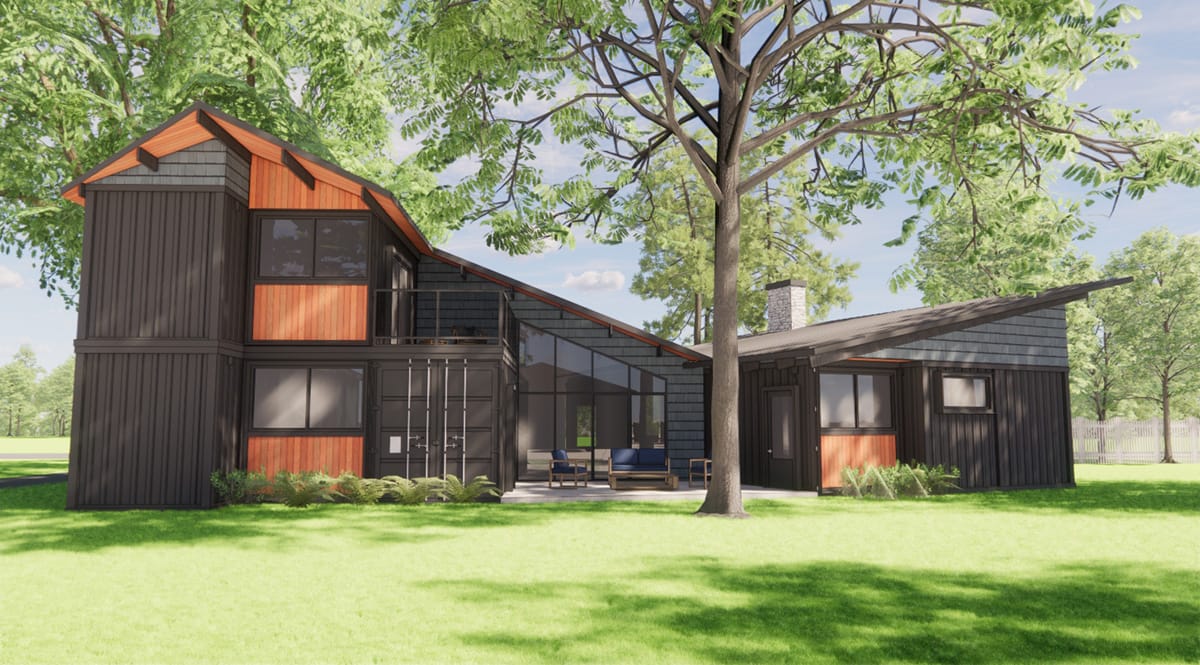
Elements of Design
Leslie Horn serves as the founder and CEO of Three Squared, a design firm that focuses on innovative, creative solutions, and that has completed dozens of shipping container projects.
The firm has experienced and promoted the benefits of container construction, including its speed, strength, energy efficiency, and its ability to simplify the construction process. Her team designs using the containers and sources them locally to further leverage these benefits.
“Using containers can cut construction time in half,” she said. “We’re trying new ways to deliver them, and finish them out, and find that they are stronger and more durable. The containers also are seamless and there is no opportunity for air leakage, so they can reduce energy costs by more than 50%.”
One of Three Squared’s projects was the Mariposa Home, a multigenerational home constructed in Ohio using eight shipping containers where each generation designed their own wing of the home and the two generations worked together to design the common space.
With this unique project and with other projects, Three Squared works with the municipality in advance, especially if they haven’t approved a container project previously, Horn said. That allows them to head off any challenges and to address the most common questions like insulation, meeting code and systems to manage condensation and thermal barriers. The firm also has created a library of residential building assemblies that meet or exceed building code compliance.
In addition to being environmentally friendly, Horn points out that shipping containers are built to travel overseas in harsh weather conditions, so they are extremely durable making them more relevant and marketable in areas like Florida that are getting hammered by tropical storms.
John Hakan Senaltan, is the CEO at Florida-based Global Modulars and is currently working on a 24-unit apartment project using more than 200 shipping containers. The company offers 16 standard houses with the largest made from 12 containers for 4,000-square-feet of living space.
“The homes are very popular, and we ship them all over the United States,” Senaltan said. “The homes are cheaper than regular construction and faster than regular construction, but most clients are buying for single family houses and are business owners in the middle upper class.”
LOT-EK is another creative design firm upcycling shipping containers for residential projects. A unique mixed-use project in Johannesberg was designed in a V-formation to showcase a triangular shared space with a swimming pool and sundeck. The container-based residential units are studio apartments between 430 and 630 square feet.
Texas-based Bob’s Containers customizes containers with dozens of starting models and a process that includes concurrent project management, where a customer can fully prepare the land while the container is being prepared off site. With that parallel work, the company can deliver a turnkey home ready for utility hookups in about 10 weeks.
Bob’s offers standardized models to expedite permitting. Plus, all customizations are handled in a production line fashion, fluidly moving from cuts and welds to framing, then to finishing and painting.
Customers can run through a Bob’s Containers home purchase much like any ecommerce experience, building it online with customization tools, and having complete pricing transparency and AI chatbot support throughout the process. After the online purchase, the complete home can be delivered anywhere in the U.S.
The company’s “Joshua” Model was featured on Netflix and is popular as a one-bedroom home that starts at $90,255. It can be customized with a rooftop deck, cabin cladding, and hurricane glass.
Fourteen states have now passed approval for accessory dwelling units, and more have it under consideration, giving shipping container homes a large growth potential.
California-based Conex Modular is striking at that opportunity and has put it into four simple steps starting with an assessment, moving to a tour to select a model, going under contract, and finally to the delivery of the converted shipping container.
Focus on Florida
Shipping containers have an opportunity in the sunshine state. As a resilient and adaptable housing option, containers are well positioned to support Florida’s rapidly increasing population, said Philip Donovan, partner and director at Florida-based Little design firm.
He reports that more than 1,000 people arrive in Florida per day, causing a shortage of housing. The demand is forcing prices to rise, while ongoing climate threats are stressing the insurance industry.
“Shipping container housing solutions could help begin to ease the housing burden if planned and deployed properly,” Donovan wrote.
At the same time that housing demand is increasing in Florida, climate threats are strengthening. He believes that shipping container homes offer a resilient, responsive and adaptive response to both challenges.
“With a small footprint, shipping containers can be adapted to handle the extreme temperatures that Florida is beginning to face,” Donovan said. “Humidity is also an issue coincidental to the heat. The containers will need to be well insulated as the steel skin will exacerbate the issue.”
A container’s smaller footprint can be cooled with less energy than a typical home. Plus, its long rectangular shape can be used to take advantage of prevailing winds and to utilize cross ventilation to suck the hot, humid air out of the interior spaces. However, a container’s steel surfaces can reflect the heat to the surrounding environment, radiating it into surrounding environments.
Insulation becomes a critical factor, Donovan said. Best practice is to install insulation on the warm side of the exterior skin of a building, and when that is translated to a shipping container, it means installing insulation on the outside of the container with an exterior finish that meets hurricane wind requirements.
The Future
Pinto doesn’t believe that President-elect Trump’s tariff policies will have a critical impact on the container industry.
He’s also excited about a new five-in-one, foldable shipping container from Compact Container Systems. The 40’ container improves operating inefficiencies, reduces unnecessary container movements, and dramatically reduces carbon emissions throughout the transportation and logistics supply chain.
More than 20% of containers return to a port of origin empty, so this innovation has the potential to cut storage space by 80%, and carbon emissions by 70%. Affordable transportation has been a substantial hurdle for modular home construction, so these benefits could offer an attractive benefit for housing.
“The opportunity to place five of our folded containers in the same slot as one 40’ HC standard container is a game changer in managing container movements, maximizing storage capacity, and greatly reducing carbon emissions,” said Charlie Santos-Buch, the company’s chairman and CEO in a press release.
This innovation could help bring more creative home designs online, and while certainly not the end all be all for housing, shipping containers have a spot as an affordable, resilient and sustainable solution.
More from Modular Advantage
Oregon’s Prevailing Wage Proposal: A Wake-Up Call for Modular Construction
In early February, 2024, the Massachusetts Board of Building Regulations and Standards (BBRS) released its proposed 10th Edition building codes. This draft included several amendments targeting modular construction that would have created an extremely difficult environment for the entire modular industry and could have eliminated the industry entirely in the state.
Behind the Design of Bethany Senior Terraces, NYC’s First Modular Passive House Senior Housing Project
As more developers seek to meet new regulations for energy efficiency, the team at Murray Engineering has set a new record. With the Bethany Senior Terraces project, Murray Engineering has helped to develop NYC’s first modular structure that fully encompasses passive house principles — introducing a new era of energy efficiency in the energy-conscious city that never sleeps.
How LAMOD is Using Modular to Address Inefficiency, Sustainability, and the Future of Construction
As developers, designers, and contractors seek to understand the evolving needs of the modular industry, no one is as well-versed in the benefits of going modular as Mārcis Kreičmanis. As the co-founder and CBDO of LAMOD in Riga, Latvia, Mārcis has made it his ultimate goal to address the inefficiencies of traditional construction.
From Furniture Builder to ‘Activist Architect’: Stuart Emmons’ Unique Journey
Stuart Emmons was fascinated by buildings at a young age. He remembers building sand cities with his brother during trips to the Jersey shore. His father gave him his first drawing table at the age of ten. Today, he is an experienced architect who received his FAIA in June 2025. The road he took is unique, to say the least.
Forge Craft Architecture + Design: Codes, Contracts, and Intellectual Property
Founding Principal and Director of Modular Practice for Forge Craft Architecture + Design, Rommel Sulit, discusses the implications of codes, contracts, and intellectual property on
modular construction.
Eisa Lee, the “Bilingual” Architect
Now as the founder of XL
Architecture and Modular Design in Ontario, Canada, she applies not just her education as a traditional architect but an entire holistic view on modular design. It’s this expansive view that guides her work on being a true partner that bridges the gap between architects and modular factories as they collaborate on the design process.
Tamarack Grove Engineering: Designing for the Modular Sector
The role of a structural engineer is crucial to the success of a modular project, from initial analysis to construction administration. Tamarack Grove offers structural engineering services — project analysis, plan creation, design creation, and construction administration — for commercial, manufacturing, facilities, public services, and modular. Modular is only one market sector the company serves but it is an increasingly popular one.
Engineer Masters the Art of Listening to His Customers
Since founding Modular Structural Consultants, LLC. in 2014, Yurianto has established a steady following of modular and container-based construction clients, primarily manufacturers. His services often include providing engineering calculations, reviewing drawings, and engineering certification
Inside College Road: Engineering the Modules of One of the World’s Tallest Modular Buildings
College Road is a groundbreaking modular residential development in East Croydon, South London by offsite developer and contractor, Tide, its modular company Vision Volumetric (VV), and engineered by MJH Structural Engineers.
Design for Flow: The Overlooked Power of DfMA in Modular Construction
Unlocking higher throughput, lower costs, and fewer redesigns by aligning Lean production flow with design for manufacturing and assembly.