Oldivai on 31st – Modular Housing, Rinse and Repeat
What Makes Oldivai Different?
Fast and high-quality construction rarely go together—until now. Oldivai on 31st (aka Project Zero) redefined modular housing by combining speed with exceptional standards. Developed as the inaugural project for Oldivai Capital, this 7,280-squarefoot, three-story complex wasn’t just designed to address Spokane’s growing housing shortage, it was created to serve as a prototype for scalable, repeatable workforce housing solutions.
With a “kit-of-parts” approach, Oldivai on 31st demonstrated how a predesigned layout could deliver consistent programming and rapid deployment. This project didn’t just match the site; it set a standard for matching the design to sites across multiple locations. With five additional projects and a larger multi-unit complex slated for 2025, this proof of concept has already paved the way for future developments.
Quick Facts
- Project Name: Oldivai on 31st
- Location: Spokane, Washington
- Building Type:
Multifamily Apartments - Number of Units: 10
- Number of Modules: 15
- Total Area: 7,280 square feet
- Timeline:
- Groundbreaking: July
31, 2023 - Modular Set: Jan. 29 – Feb. 1, 2024 (4 days)
- (TCO) Substantial
Completion: July 2, 2024 (310 days from site start)
- Groundbreaking: July
- Total Construction Cost: $2,692,850
Why Modular? Why Now?
Traditional construction simply can’t keep up with the rising demand for housing. Modular construction offers not just a faster solution but a smarter one. Oldivai on 31st tackled inefficiencies head-on, sidestepping weather delays and labor shortages to deliver a completed project in under a year. But this wasn’t just about speed. The real challenge was scalability: could modular construction deliver consistent quality across future developments? Project Zero answered that with a resounding yes, setting a new standard for efficiency, precision, and repeatability in multifamily housing.
Designing for Precision and Efficiency
At Oldivai on 31st, efficiency meant doing things right from the start. Every stage of the process was optimized to maximize quality while minimizing delays. Building modules in a climate-controlled factory protected materials from Spokane’s unpredictable weather. This method reduced waste, ensured tighter tolerances, and allowed interiors, mechanical systems, and finishes to be 80% complete before shipping. Modules arrived on-site nearly move-in ready. Plumbing, electrical systems, and finishes were pre-installed, leaving minimal onsite labor. The modules were craned into place in just four days, bypassing typical delays caused by weather or onsite inefficiencies. From groundbreaking to substantial completion, Oldivai was finished in 310 days, shaving weeks off traditional construction timelines.
Challenges and Lessons Learned: Smarter Construction Every Step of the Way
Every challenge faced during the development of this project became an opportunity to refine modular construction processes. These obstacles not only shaped the Project Zero’s success but also established a framework for improving future developments.
Think Lifecycle, Build Smarter
The journey from factory fabrication to tenant move-in requires planning for every phase of a building’s lifecycle. At Oldivai, the team embraced a “start with the end in mind” philosophy. Features like standardized crawl space and attic access simplified future maintenance, ensuring the building functioned efficiently long after completion. This forward-thinking approach highlighted the importance of designing for long-term usability—not just immediate results.
Streamlining Communication
Early misalignments between architectural and modular plans caused delays and confusion, underscoring the need for clear documentation and communication.
- Solution: A unified labeling system and centralized digital repository ensured that all stakeholders—from architects to contractors—worked from the same, up-to-date information.
- Result: Improved consistency across teams, reduced miscommunication, and faster resolutions to onsite challenges.
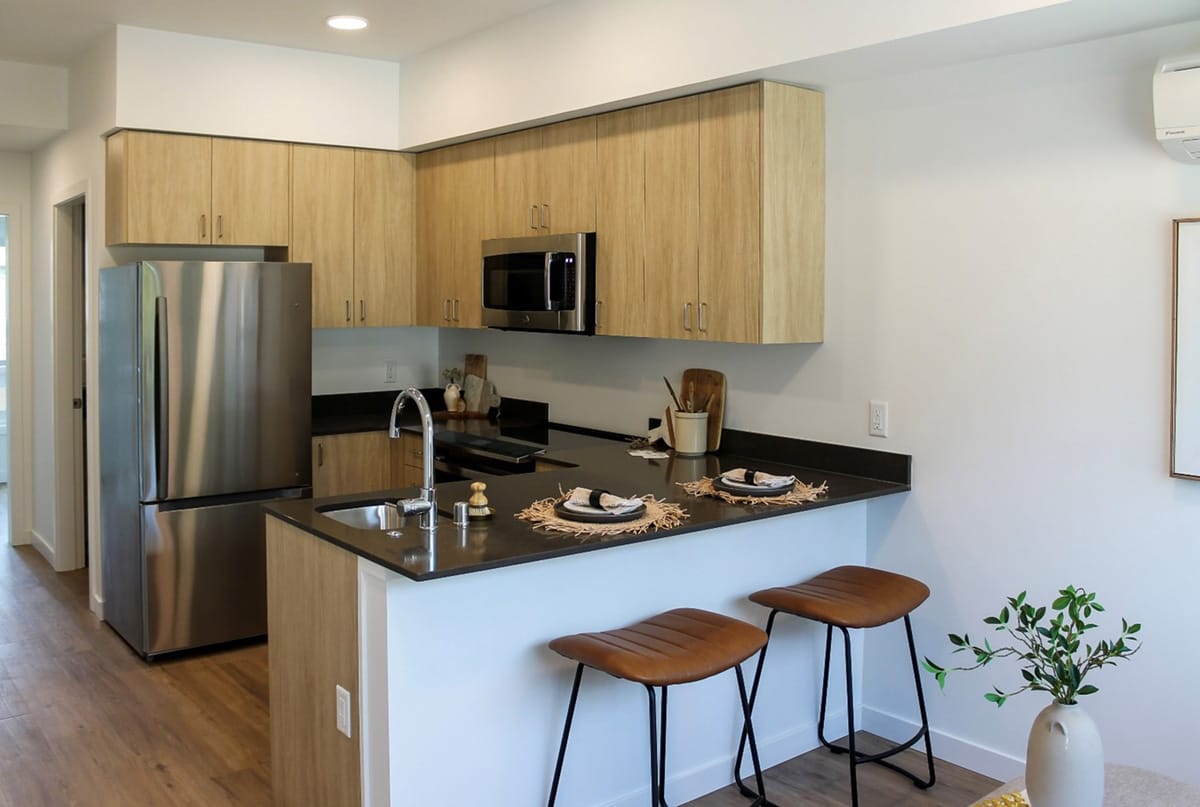
Fire Safety and Critical Systems Coordination
Ensuring compliance with fire safety requirements was a recurring challenge. Factory and onsite integration revealed the need for better coordination in critical systems like plumbing and fire suppression.
- Solution: The team expanded zones for fire suppression systems and standardized plumbing bays to simplify installation. Detailed firestopping designs were also integrated into the architectural set to meet inspection standards.
- Result: These adjustments avoided costly delays and have become a new standard for future modular projects.
Continuous Improvement
Modular construction thrives on iteration. Every success and setback at Oldivai informed a scalable framework for the future. Lessons weren’t just learned—they were applied, proving that modular isn’t just about speed but about smarter, more reliable results.
- Standardization for Simplicity: Consistent fixtures, finishes, and system designs reduced variability and accelerated production.
- Flexibility for the Unexpected: Challenges like fire safety revisions reinforced the importance of adaptability, ensuring that future projects are equipped to handle surprises.
Continuous Improvement
The insights from Oldivai on 31st offer practical guidelines for future modular developments:
- Design for the Lifecycle: Plan beyond completion—incorporate features that simplify maintenance, upgrades, and tenant satisfaction.
- Invest in Systems: Clear documentation, precise Oldivai on 31st Level 1 Floorplan labeling, and real-time updates prevent errors and build trust across teams.
- Standardize for Scalability: Uniformity in fixtures and finishes ensures consistent quality and reduces variability in production.
- Embrace Feedback: Every project provides lessons. Use them to refine processes and create smarter solutions.
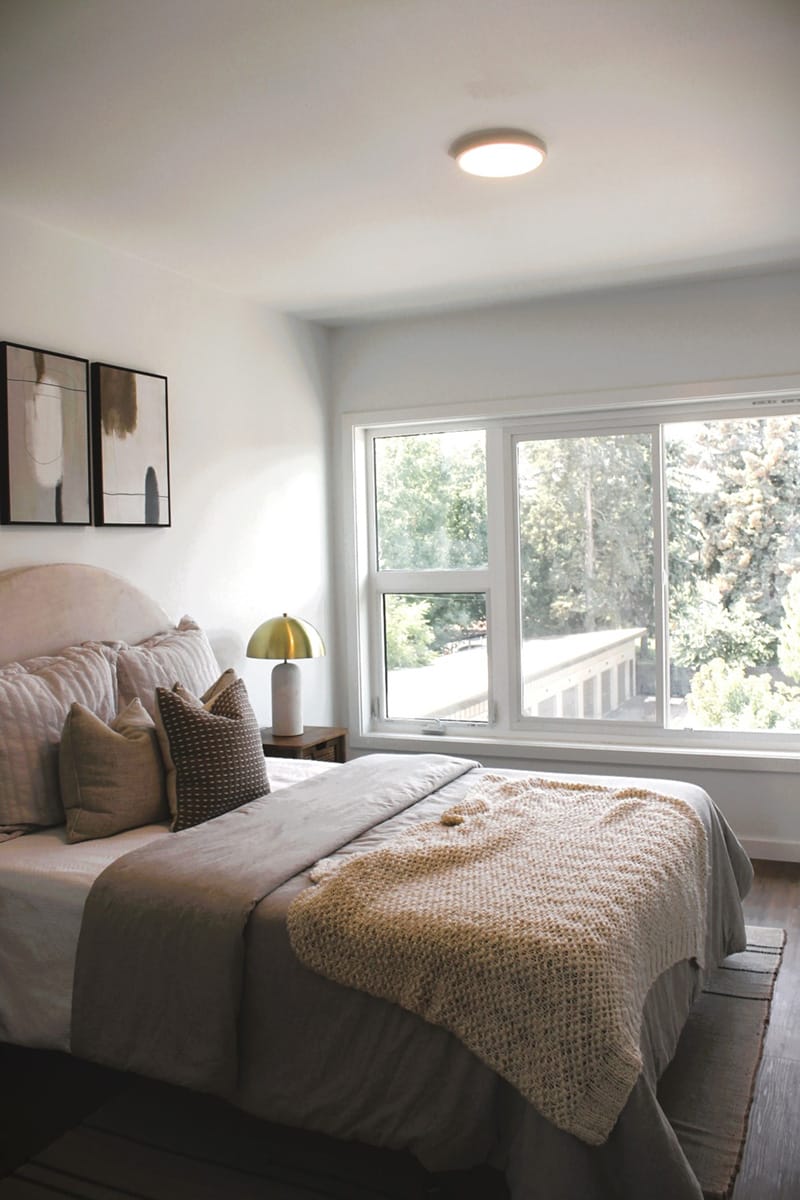
Cost Effectiveness
With a total cost of $2,692,850, Oldivai on 31st demonstrated that cost savings don’t come from cutting corners—they come from doing things right. Time is money, and Project Zero proved that faster construction saves both.
Conclusion: Building Better, Smarter, and Faster
For Jackson | Main Architecture and Oldivai Capital, Project Zero isn’t just a success—it’s a promise. This project demonstrates that better, faster, and smarter construction is achievable without compromising durability or design. For tenants, it offers a home they can trust, built to the highest standards. More than a single modular project, Oldivai on 31st is the foundation of a larger vision—one that extends far beyond Spokane and will shape housing solutions for years to come.
More from Modular Advantage
AI, Faster Sets, and Automation: The Future of Modular is at World of Modular
While the modular building industry has long known that it can be an effective solution to increase affordable housing, the word is slowly spreading to more mainstream audiences. Three presentations at this year’s World of Modular in Las Vegas hope to provide insight and direction for those seeking a real solution to the crisis.
An Insider’s Guide to the 2025 World of Modular
The Modular Building Institute is bringing its global World of Modular (WOM) event back to Las Vegas, and with it comes some of the industry’s best opportunities for networking, business development, and education. Over the course of the conference’s four days, there will be numerous opportunities for attendees to connect, learn, and leverage event resources to get the most out of the conference.
Affordable Housing Now: The Industry’s Best Bring New Solutions to World of Modular
While the modular building industry has long known that it can be an effective solution to increase affordable housing, the word is slowly spreading to more mainstream audiences. Three presentations at this year’s World of Modular in Las Vegas hope to provide insight and direction for those seeking a real solution to the crisis.
Opportunities for Innovation in Modular Offsite Construction
Modular Offsite Construction has already shattered the myth that it only produces uninspired, box-like designs. Architectural innovations in module geometry, configurations, materials, and products make it possible to create visually stunning buildings without sacrificing functionality or efficiency.
Safe Modular Construction with Aerofilm Air Caster Transport
In collaboration with Aerofilm Systems, Heijmans developed innovative skids using air caster technology for moving modules easily and safely. These pallets are equipped with an auto-flow system, making operation extremely simple.
Miles, Modules, and Memes: Building a Modular Network One Flight at a Time
At the end of the day, social media is just another tool for building connections, and like any other tool, needs to be used skillfully to work properly. Use social media thoughtfully, and it will open doors to real opportunities and relationships you didn’t even see coming.
Falcon Structures: Thinking Inside the Box
Some of Falcon’s latest projects include creating container solutions for New York’s Central Park and an East Coast professional baseball team. More and more, Falcon is shipping out container bathrooms and locker rooms to improve traditionally difficult work environments, like those in oil and gas or construction.
UrbanBloc—From Passion to Industry Leader
UrbanBloc specializes in three main categories or markets – what they call “Phase 0” projects, amenities, and urban infill. Clients are often attracted to shipping containers because from a real estate perspective they are considered an asset. Having the flexibility to move and transport these assets allows owners to respond to different circumstances in a fluid manner that they can’t get with standard construction.
The Hospitality Game-Changer
“Hospitality is about more than just providing a service – it’s about delivering an experience,” says Anthony Halsch, CEO of ROXBOX. “And that’s where containers thrive. They allow us to create spaces that are unique, efficient, and sustainable.”
Container Conversions Counts on Simplicity to Provide Critical Solutions
Container Conversions has fabricated and developed thousands of containers for varied projects, including rental refrigeration options, offices, kitchens, temporary workplace housing, and mobile health clinics.