Hawthorn Extended Stay by Wyndham—Jackson, WY
Few places are as picturesque as Jackson, Wyoming. That can be both a blessing and a curse. The scarcity of housing has forced even dual-income families to make a tough choice: commute from the few towns nearby with scarce but less costly housing, or leave their dream community. People like Casey Rammell are attacking this challenge on multiple levels—and they’ve tapped Autovol for help.
Growing up in nearby Driggs, Idaho, Casey has built a range of housing and accommodations in the area, and cofounded GCHB Venture with partner George Masing. Bringing housing to these parts takes a lot of know-how and ingenuity. Mountain resort conditions pose a triple threat: short build seasons, lack of local workforce, and a huge imbalance in housing supply and demand.
“We’re attacking a 3,000-unit problem 60 units at a time,” Casey shares. “The quicker we can turn more projects, the sooner we’ll bring some real impact. It starts with being able to house the crews we bring to the area during the summer months when lodging prices are astronomical.”
Casey had tried projects using panelized and containerized approaches that left him unsure, but still determined to try again. He and George saw automated modular as a possible silver bullet worth reconsidering. Reaching out to Autovol soon helped them get on board.
“We were still very interested in the process, but we had to find the right company to do it with,” Casey said. “Once I went over and walked Autovol’s plant to see how they did it and what their inspection process was, it closed all the gaps for us right there.”
Initial Autovol visits included Casey and George as well as Autovol’s CEO, Rick Murdock; CTO, Curtis Fletcher; Director of Business Development, Michael Merle; and Director of Preconstruction, Steve Clough. Steve helped define the project upfront by designing a preconstruction checklist that aligns developer needs with modular design and factory best practices to optimize efficiency and constructability.
Before hitting Autovol’s factory floor, the project was designed and modeled by Prefab Logic, another firm co-founded by Rick and Curtis. The design was created using Prefab Logic Housing products, developed by Curtis. Already factory-proven and site-friendly, the predesigned products accelerated the process for the developer/architect significantly and reduced the overall design costs. These products also leveraged the power of standardized design and supply-chain materials to take advantage of economies of scale.
“The initial design came together in a matter of a couple hours,” Curtis says. “That formed a good basis to customize with some customer-specific features. With these tools, we can establish a starting place and customize a design in a fraction of the time. At the same time, the design is basically vetted for constructability in the modular factory and onsite. Besides speed, these tools also greatly simplify materials procurement and project execution.”
The plan was to build the project in two phases. This would enable the property to open sooner and start accommodating guests while completing the second phase. The digital twin was designed to provide a complete factory-ready model for both phases upfront. That gave the factory everything it needed to bring each phase into production quickly. It also enabled everyone a way to plan both phases ahead of time, and begin prepping the site in advance.
“All the stakeholders leaned into this project and I think it really paid off in quality and strong execution,” Steve says. “We had developed a preconstruction checklist to define things upfront. It paid off as everything came together. Things like the room size put Autovol’s module length limit to the test, but the factory crew was ready, and they delivered.”
All the careful planning and collaboration enabled the finished modules to begin shipping immediately after factory completion. Seasoned crews from Snake River MEP and Accuset Construction were keyed up to set the building at breakneck speed.
“Onsite logistics were amazing,” Steve says. “And the alignment turned out extremely tight, with tolerances of 1/8-inch.” Some advanced approaches made the onsite set process especially efficient. Autovol onsite services director Joe Sievers and Accuset founder Kirk Hall brought forward a smart suggestion: pre-building the roof in pieces on the site foundation in advance.
While the modules were enroute from Nampa to Alpine, an onsite team sheeted prebuilt roof trusses on what would become the building foundation. This sped up the completion of the roof structures, as well as the “dry in” process essential to protect the building from any potential rain.
“We finished the roof structures on the ground,” Casey says. “They swung them out of the way while setting the modules, then set them on top. We probably got the roof sheeted in a quarter of the time on the ground than we would have in the air. With this approach, it had us pretty much dried in after about 10 days.”
At this writing, the project is still a few months from occupancy. But many of first-phase rooms are already reserved for long-term guests including GCHB Venture crews, and staff at a clinic in Alpine eager to provide housing for healthcare staff in such a limited market.
“This project would have gone 18 to 24 months on a conventional schedule. We’ll do it in eight,” Casey says. “That kind of speed is good for everyone. I like to do things as efficiently as possible so that everyone on the project makes money. In that process, things go quicker, we get the doors open quicker, and our customers get a better project in the end. Hopefully we’re generating a few million a year in gross revenue, so getting your doors open 10 months sooner can mean a pretty big savings.”
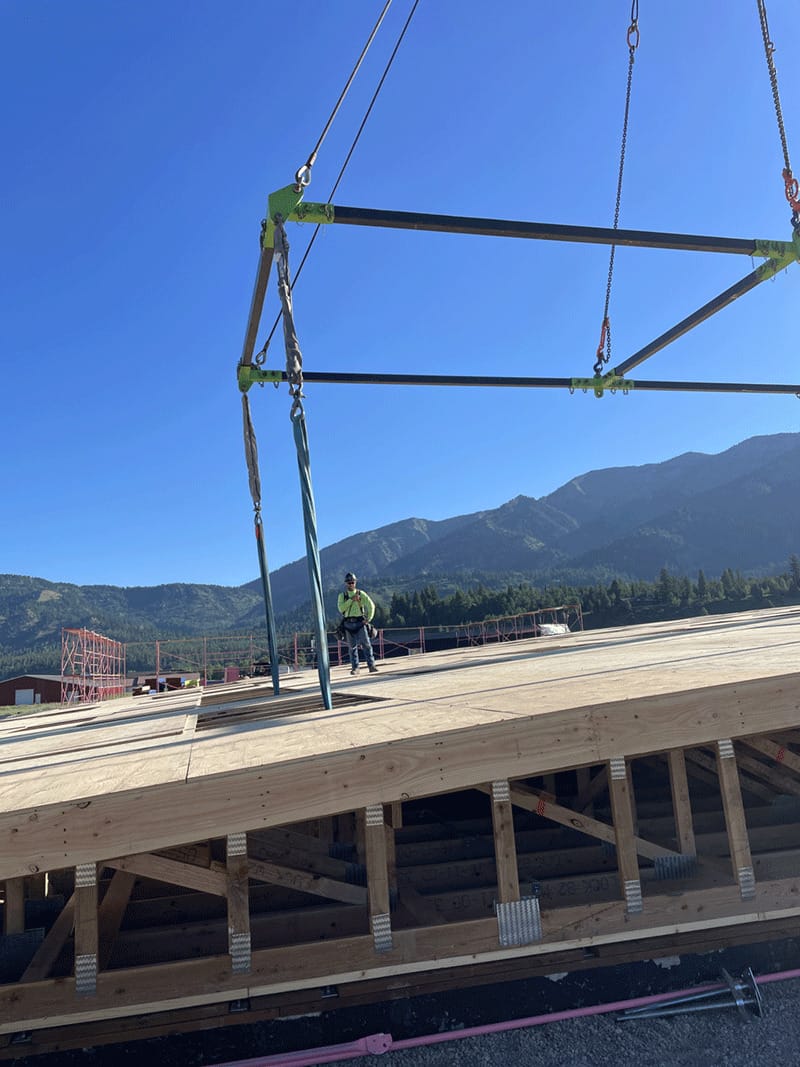
More from Modular Advantage
Oregon’s Prevailing Wage Proposal: A Wake-Up Call for Modular Construction
In early February, 2024, the Massachusetts Board of Building Regulations and Standards (BBRS) released its proposed 10th Edition building codes. This draft included several amendments targeting modular construction that would have created an extremely difficult environment for the entire modular industry and could have eliminated the industry entirely in the state.
Behind the Design of Bethany Senior Terraces, NYC’s First Modular Passive House Senior Housing Project
As more developers seek to meet new regulations for energy efficiency, the team at Murray Engineering has set a new record. With the Bethany Senior Terraces project, Murray Engineering has helped to develop NYC’s first modular structure that fully encompasses passive house principles — introducing a new era of energy efficiency in the energy-conscious city that never sleeps.
How LAMOD is Using Modular to Address Inefficiency, Sustainability, and the Future of Construction
As developers, designers, and contractors seek to understand the evolving needs of the modular industry, no one is as well-versed in the benefits of going modular as Mārcis Kreičmanis. As the co-founder and CBDO of LAMOD in Riga, Latvia, Mārcis has made it his ultimate goal to address the inefficiencies of traditional construction.
From Furniture Builder to ‘Activist Architect’: Stuart Emmons’ Unique Journey
Stuart Emmons was fascinated by buildings at a young age. He remembers building sand cities with his brother during trips to the Jersey shore. His father gave him his first drawing table at the age of ten. Today, he is an experienced architect who received his FAIA in June 2025. The road he took is unique, to say the least.
Forge Craft Architecture + Design: Codes, Contracts, and Intellectual Property
Founding Principal and Director of Modular Practice for Forge Craft Architecture + Design, Rommel Sulit, discusses the implications of codes, contracts, and intellectual property on
modular construction.
Eisa Lee, the “Bilingual” Architect
Now as the founder of XL
Architecture and Modular Design in Ontario, Canada, she applies not just her education as a traditional architect but an entire holistic view on modular design. It’s this expansive view that guides her work on being a true partner that bridges the gap between architects and modular factories as they collaborate on the design process.
Tamarack Grove Engineering: Designing for the Modular Sector
The role of a structural engineer is crucial to the success of a modular project, from initial analysis to construction administration. Tamarack Grove offers structural engineering services — project analysis, plan creation, design creation, and construction administration — for commercial, manufacturing, facilities, public services, and modular. Modular is only one market sector the company serves but it is an increasingly popular one.
Engineer Masters the Art of Listening to His Customers
Since founding Modular Structural Consultants, LLC. in 2014, Yurianto has established a steady following of modular and container-based construction clients, primarily manufacturers. His services often include providing engineering calculations, reviewing drawings, and engineering certification
Inside College Road: Engineering the Modules of One of the World’s Tallest Modular Buildings
College Road is a groundbreaking modular residential development in East Croydon, South London by offsite developer and contractor, Tide, its modular company Vision Volumetric (VV), and engineered by MJH Structural Engineers.
Design for Flow: The Overlooked Power of DfMA in Modular Construction
Unlocking higher throughput, lower costs, and fewer redesigns by aligning Lean production flow with design for manufacturing and assembly.