One Answer from AI Can Provide Innumerable Opportunities, Says Stack Modular’s Jim Dunn
With access to an abundance of labor and materials, Stack Modular has been able to manufacture modules in China and then ship them out to customers anywhere around the world. Thanks to key port access in Shanghai, there’s no place their modules can’t go. But it was almost a stroke of luck that led to the success of Stack Modular, especially starting in 2008, according to President and Founder Jim Dunn.
Nowadays, Stack Modular relies on its 15 years of experience to fabricate modules for farflung places such as the Arctic Circle (to build a local hotel), the small Pacific Island of Vanuatu (to build a dormitory), and a plethora of locations in North America, their target market.
“For us, no modules ever sit and stay in China,” said Jim.
Manufacturing is thriving at Stack Modular, as the firm recently opened a fourth factory, adding more labor and power to their manufacturing engine. That said, Jim measures success not by the amount of factories the company is running, but by cutting down the time the project spends in the “pre-construction” process.
And he sees artificial intelligence (AI) as the tool to shrink this window of time and transform it into a real business opportunity.
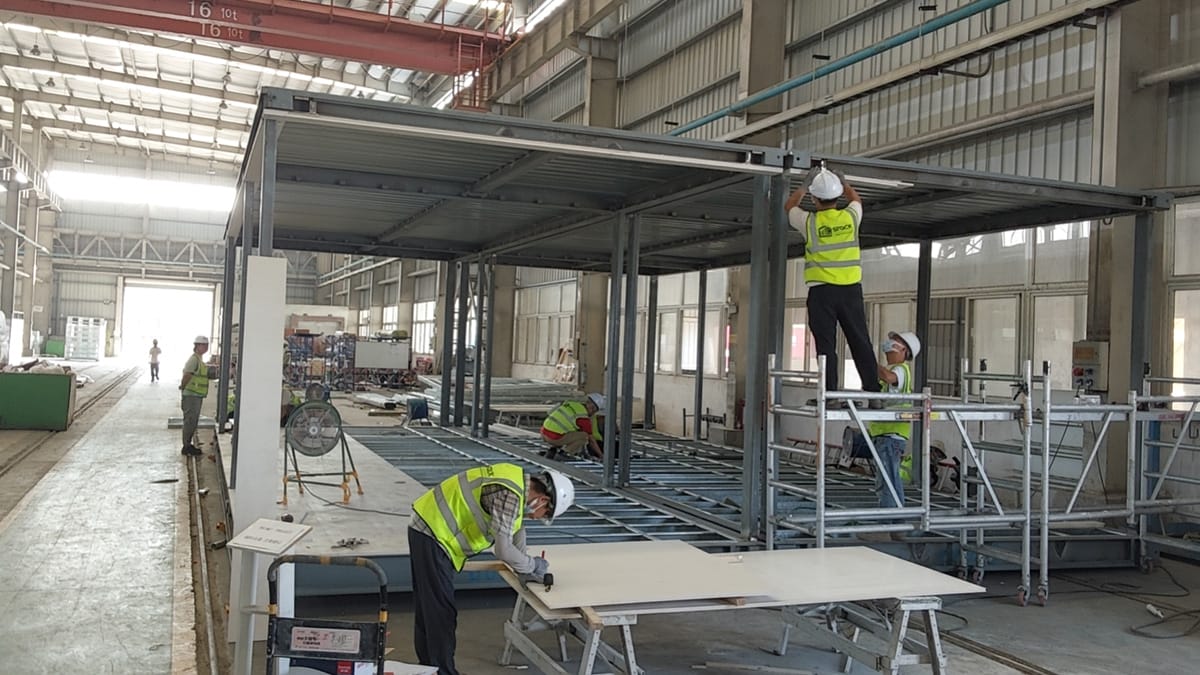
Making the Case for AI at Stack Modular
For Jim Dunn, the need for AI can’t be made clearer. Stack Modular is currently working on constructing and designing the tallest modular building in Canadian history. The 14-story building in Vancouver is a city-owned structure, paid for by the city to help people suffering from homelessness. However, the building is in “pre-construction” limbo.
As Jim points out, there is no single entity to blame for this limbo and ultimately the housing crisis North America is experiencing. But rather, all stakeholders involved in the development process carry responsibility.
“We’re on year four of [this project] and we still haven’t broken ground,” he said. “We’ve just opened a fourth factory. We can get more space, so our issue isn’t shaving a week off manufacturing.”
He cites a number of issues that aren’t just relegated to meeting local zoning restrictions and regulations, but an issue with the process on the whole.
“It’s not just government permits, it’s also the architects trying to design without modular in mind,” he said. “It’s the engineers working in silos, the design [team], and the cumbersome red tape bureaucratic program we’ve created in North America.”
In Stack Modular’s case, they acquired a stake in an architecture firm to simplify design ownership to address one part of the pre-construction phase.
“You can partner with the firm, so now you become an equity partner in the process,” he said. “You’re incentivized and you’re part of the development team. You’re going to the bank and saying, ‘here’s the performance.’ You have to control your destiny there, and [being able to recognize that] comes with years of experience.”
But this was just the tip of the iceberg, in Stack Modular’s case. Jim sees this as an industry-wide issue, and wants to focus on easing the pain for all stakeholders to connect and collaborate.
“[In construction,] North America actually produces less than what we did decades ago,” he said. “So that’s the mentality we’re up against. We’re actually in a system that’s getting slower every day.” This view has been well-documented over the years. News outlets like The New York Times and The Economist have reported on lagging productivity in the construction industry, noting slowdowns from as early as the 1970s.
All of these problems have raised more questions than answers, especially for Jim at Stack Modular.
“How do we make [the pre-construction process] easier and/or simplified now?” he said. “How do we make it also more enjoyable? How do you get these dozens of stakeholders to agree on a building moving forward faster and more efficiently?”
One way to address these problems was to use the litany of technology tools out there, specifically artificial intelligence.
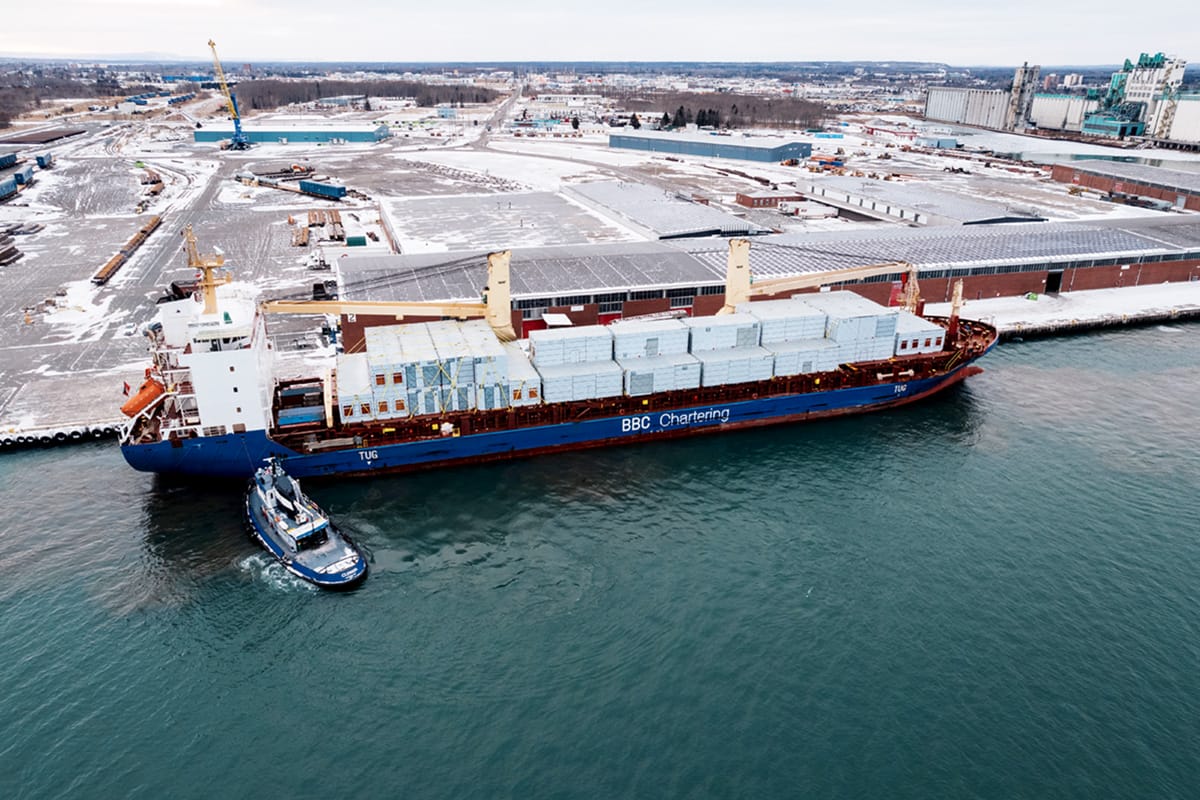
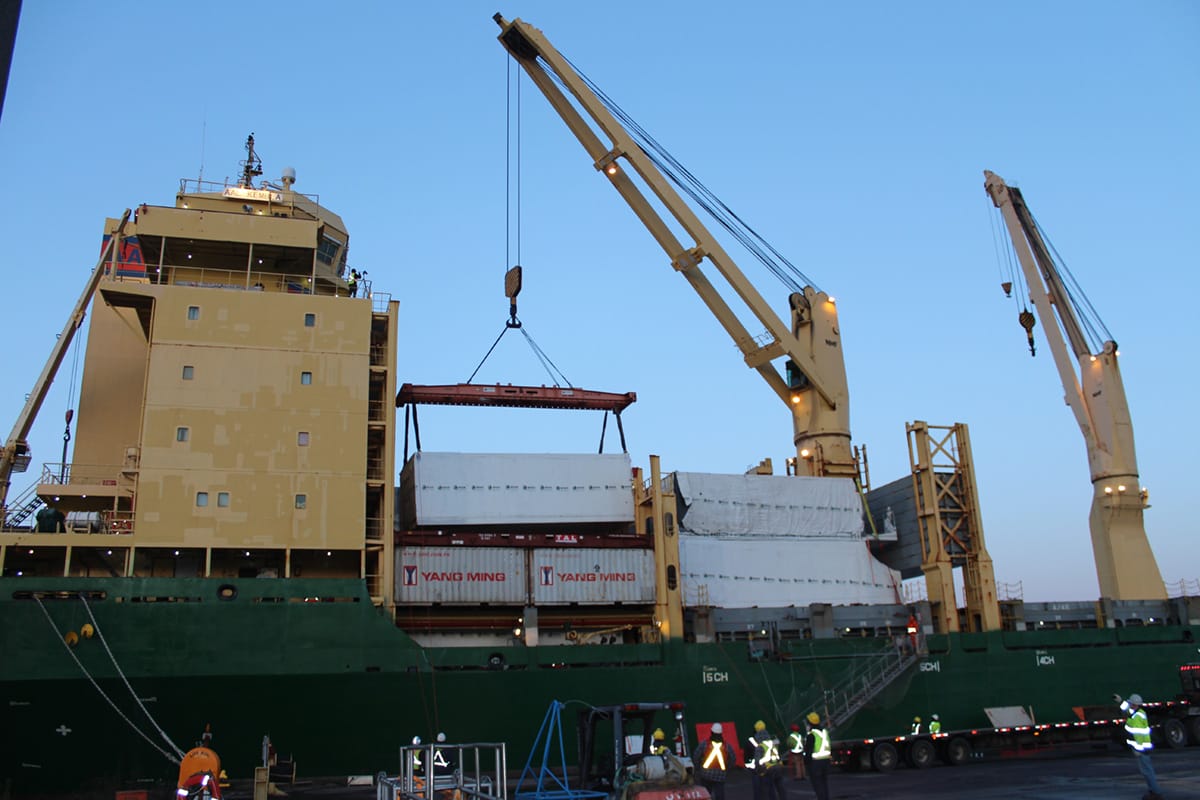
Providing the Fuel for the AI Stack Modular Engine
As Jim explains, AI simplifies the procurement of information and brings it to each decision maker. For example, if an architect sends you five pages of design, you can ask AI to review the pages to tell you how much drywall you need.
But even AI has its limitations—most notably with its source of information, as many have experienced with the use of ChatGPT and Google’s Gemini AI.
“When your engine is the web,” says Jim, you can ask it anything about anyone and pull up basic information that you need. “But in our world, I can’t ask ChatGPT how much drywall I need in the building.” What was Jim’s solution to the problem? To build their own Stack Modular AI engine.
When to Build New and When to Adopt
Jim has always been an early adopter of new technology, familiarizing himself with the first version of ChatGPT by downloading it onto his phone. But it wasn’t until a Harvard lecturer gave a talk to a group of business leaders that Jim was inspired to bring AI to Stack Modular.
That was about a year ago, when “the proverbial hamster wheel started running,” he said. Soon after, Stack Modular obtained the corporate license for Google’s Gemini AI chatbot. That led to various teams adopting some smaller plug-ins or add-ons to existing programs to eliminate some more rote design work.
“There’s some really nice artistic toolings from AI, like with generative facade structuring,” he said. “So rather than us building our own engine that can create a beautiful picture of a building, we’ll have this add-on that’s already existed.”
With software, chances are there are already some small tools and solutions available to fix very specific problems you might have, says Jim. The difference in applying AI to your business, especially in modular, has to do with the information you have accessible to insert into your AI engine for use.
“The proprietary opportunity was realizing that AI, in the global sense of the word, isn’t actually going to do much for us, but a Stack AI Engine would be a game changer,” he said. “Unfortunately, that comes with radical higher costs, as you’re building your own engine. It’s just a lot of work to get the Stack Engine [up].”
The company is committed to building out the Stack AI Engine to revolutionize the pre-construction process. They’ve hired a full-time consultant well-versed in the Google ecosystem to help develop decision-useful AI programs.
“Our team is full of amazing engineers, architects, builders, manufacturers, but they don’t know anything about AI,” he said, and vice versa. “So just combining the two groups for a pretty penny under the same roof has been essential and we’re nowhere near where we need to be, but we’re certainly closer today than yesterday.”
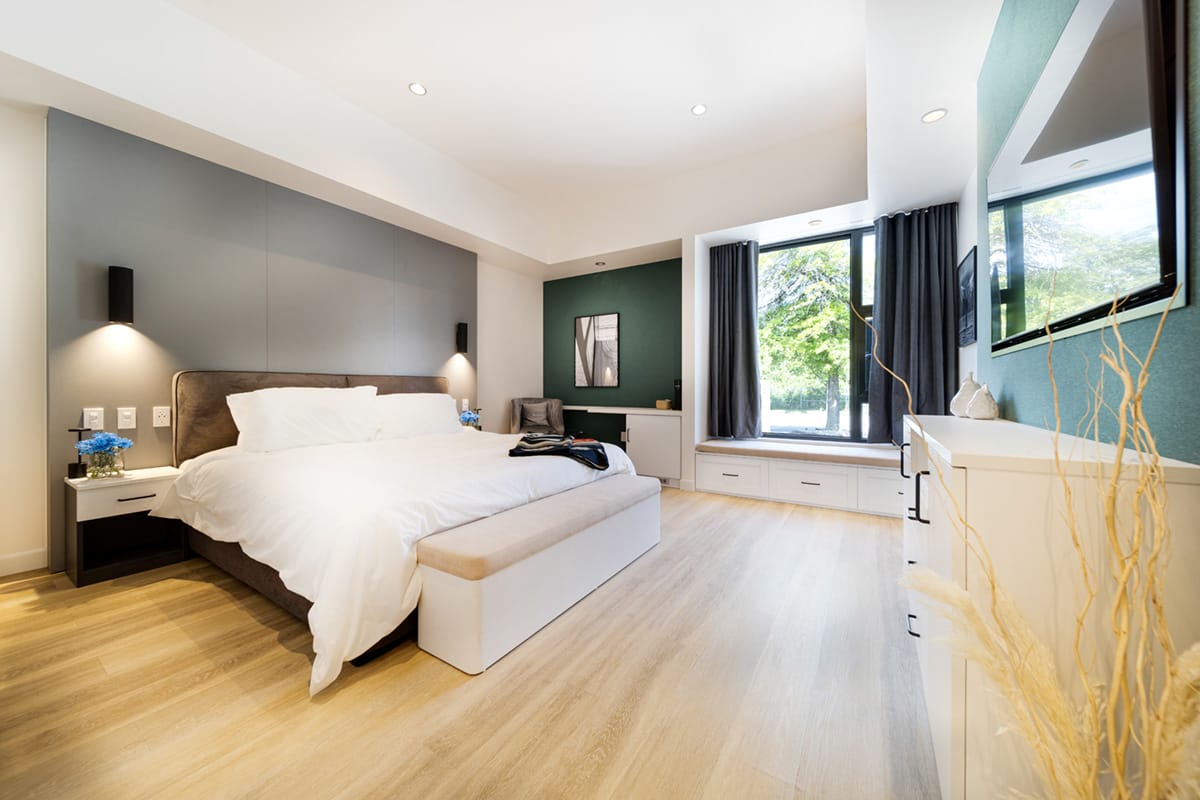
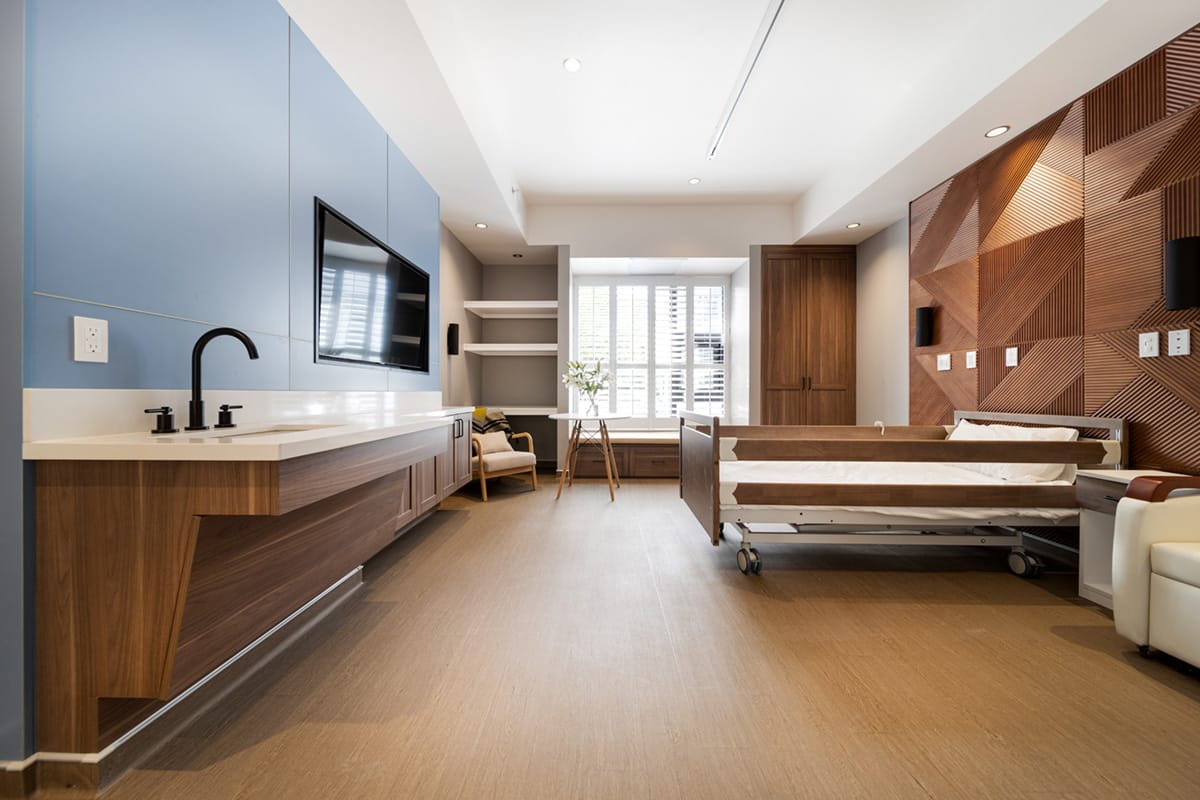
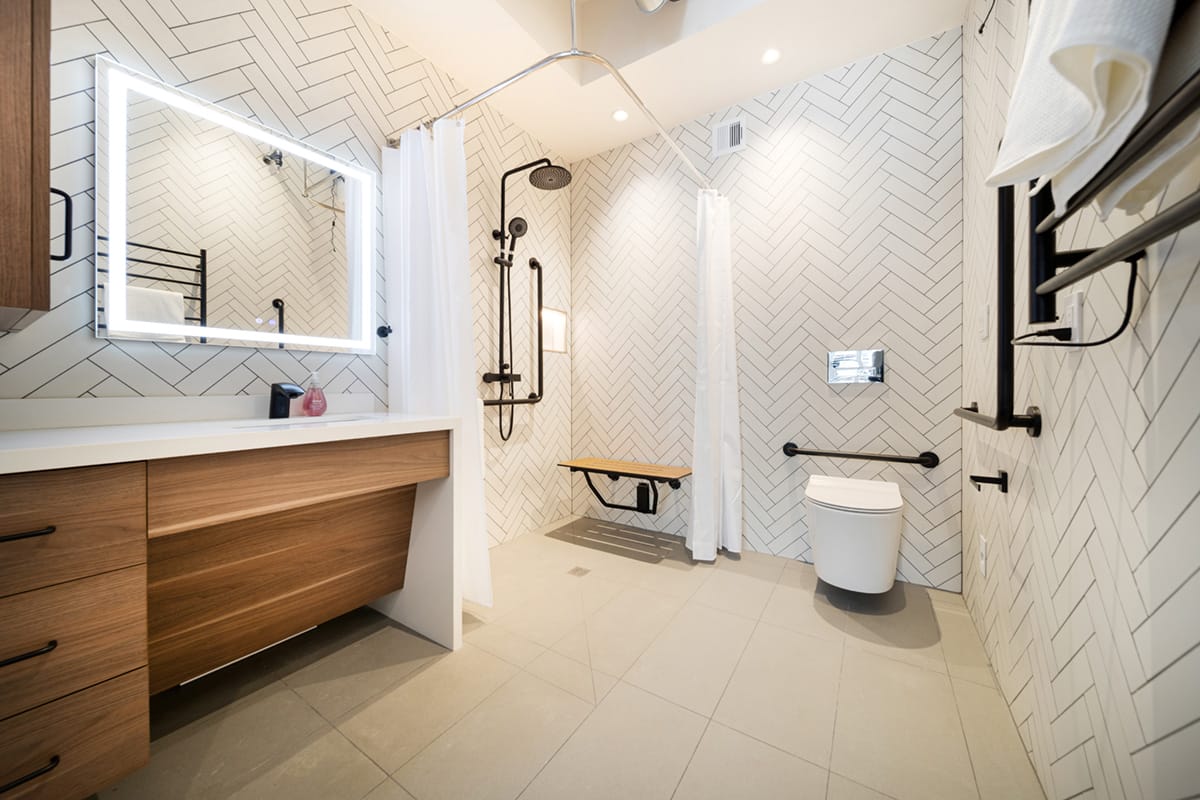
Stack AI Engine Benefits are Limitless
Right now, AI can help with digital admin work, such as naming files and providing readily accessible information on the web in a snap. However, building a useful AI tool requires that fountain of knowledge and 15 years of experience in order to be applicable in modular.
The Stack AI Engine is not fully functional yet, but it offers an unlimited number of productivity benefits. One particular function is the ability to scan dense project requirements—using past projects at Stack Modular—to spit out relevant information, says Jim. Currently, the company is using AI for cost estimates, most recently for a project out in California.
“If the client adds a floor, AI tells me immediately how much more drywall I need, as an example. We can then relay this cost change to the developer in seconds.” he said.
AI has provided some success from the get-go, but more remains to be done at Stack Modular, said Jim. As part of building the Stack AI Engine, Jim has asked his teams to get their noses off the grindstone and give AI access and insight into every part of their day-to-day roles.
“The biggest limitation is getting them out of that role, which I’ve trained them for 15 years to do and say, ‘pause, stop being great for a second, and go backwards,’” he said. “‘Get this AI engine, Google Drive, all set up.’ That’s been the hardest, getting people to realize that we got to take a step backwards to go step forward.”
Using AI to Transform the Modular Industry on the Whole
As Jim continues to work on the Stack AI Engine, he is also aware of some of the pervasive attitudes in some corners of the modular industry.
“I wish my module partners of the world would be more open-minded and think how rising tides raise all ships, but they don’t,” he said. “We actually have a housing crisis. So if we could check our egos at the door and share some of the lessons learned—the AI victories and experience in our case, which is the fuel for AI—I’m happy to do it.”
Even with that sentiment, he is also aware of the narrower area of operation that Stack Modular has settled on. Some companies may be more inclined to bring AI to the manufacturing plant to shorten time in the factory, but that’s not where Stack Modular’s focus is, according to Jim.
“I would say an opportunity for us to share and win as an industry, both in modular and construction, would be ‘how can we utilize AI for the collaborative efforts that pre-construction requires?’” said Jim.
The future could be much brighter and collaborative, he says. Through showing, rather than telling, the modular industry has a better chance of growing.
“Imagine this,” Jim says. “Stack offers a login name to an architect and developer with little to no modular experience. And by using our Stack AI Engine, they are able to design, manipulate, change and even price a TRUE modular project, without a Stack engineer in the room. That is where we need to be, and frankly, Stack will be in 2025.”
About the Author: Karen P. Rivera is a freelance writer and editor with a passion for storytelling. She is a former United Nations-based reporter, with experience covering international breaking news, venture capital, emerging healthcare tech, and the video game industry.
More from Modular Advantage
Oregon’s Prevailing Wage Proposal: A Wake-Up Call for Modular Construction
In early February, 2024, the Massachusetts Board of Building Regulations and Standards (BBRS) released its proposed 10th Edition building codes. This draft included several amendments targeting modular construction that would have created an extremely difficult environment for the entire modular industry and could have eliminated the industry entirely in the state.
Behind the Design of Bethany Senior Terraces, NYC’s First Modular Passive House Senior Housing Project
As more developers seek to meet new regulations for energy efficiency, the team at Murray Engineering has set a new record. With the Bethany Senior Terraces project, Murray Engineering has helped to develop NYC’s first modular structure that fully encompasses passive house principles — introducing a new era of energy efficiency in the energy-conscious city that never sleeps.
How LAMOD is Using Modular to Address Inefficiency, Sustainability, and the Future of Construction
As developers, designers, and contractors seek to understand the evolving needs of the modular industry, no one is as well-versed in the benefits of going modular as Mārcis Kreičmanis. As the co-founder and CBDO of LAMOD in Riga, Latvia, Mārcis has made it his ultimate goal to address the inefficiencies of traditional construction.
From Furniture Builder to ‘Activist Architect’: Stuart Emmons’ Unique Journey
Stuart Emmons was fascinated by buildings at a young age. He remembers building sand cities with his brother during trips to the Jersey shore. His father gave him his first drawing table at the age of ten. Today, he is an experienced architect who received his FAIA in June 2025. The road he took is unique, to say the least.
Forge Craft Architecture + Design: Codes, Contracts, and Intellectual Property
Founding Principal and Director of Modular Practice for Forge Craft Architecture + Design, Rommel Sulit, discusses the implications of codes, contracts, and intellectual property on
modular construction.
Eisa Lee, the “Bilingual” Architect
Now as the founder of XL
Architecture and Modular Design in Ontario, Canada, she applies not just her education as a traditional architect but an entire holistic view on modular design. It’s this expansive view that guides her work on being a true partner that bridges the gap between architects and modular factories as they collaborate on the design process.
Tamarack Grove Engineering: Designing for the Modular Sector
The role of a structural engineer is crucial to the success of a modular project, from initial analysis to construction administration. Tamarack Grove offers structural engineering services — project analysis, plan creation, design creation, and construction administration — for commercial, manufacturing, facilities, public services, and modular. Modular is only one market sector the company serves but it is an increasingly popular one.
Engineer Masters the Art of Listening to His Customers
Since founding Modular Structural Consultants, LLC. in 2014, Yurianto has established a steady following of modular and container-based construction clients, primarily manufacturers. His services often include providing engineering calculations, reviewing drawings, and engineering certification
Inside College Road: Engineering the Modules of One of the World’s Tallest Modular Buildings
College Road is a groundbreaking modular residential development in East Croydon, South London by offsite developer and contractor, Tide, its modular company Vision Volumetric (VV), and engineered by MJH Structural Engineers.
Design for Flow: The Overlooked Power of DfMA in Modular Construction
Unlocking higher throughput, lower costs, and fewer redesigns by aligning Lean production flow with design for manufacturing and assembly.