Building Skills in a Virtual World: Immersive Training for the Modern Workforce
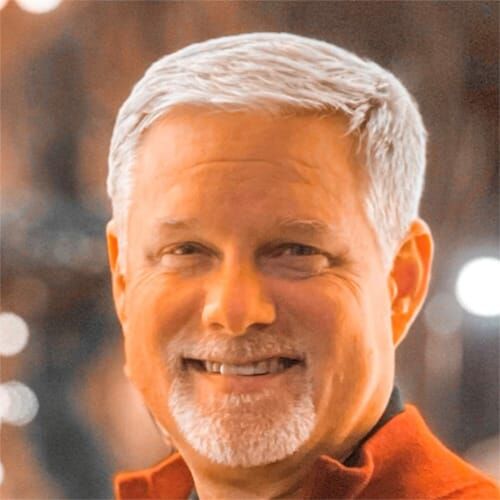
Kent Anderson is the Business Development Manager at Wesco.
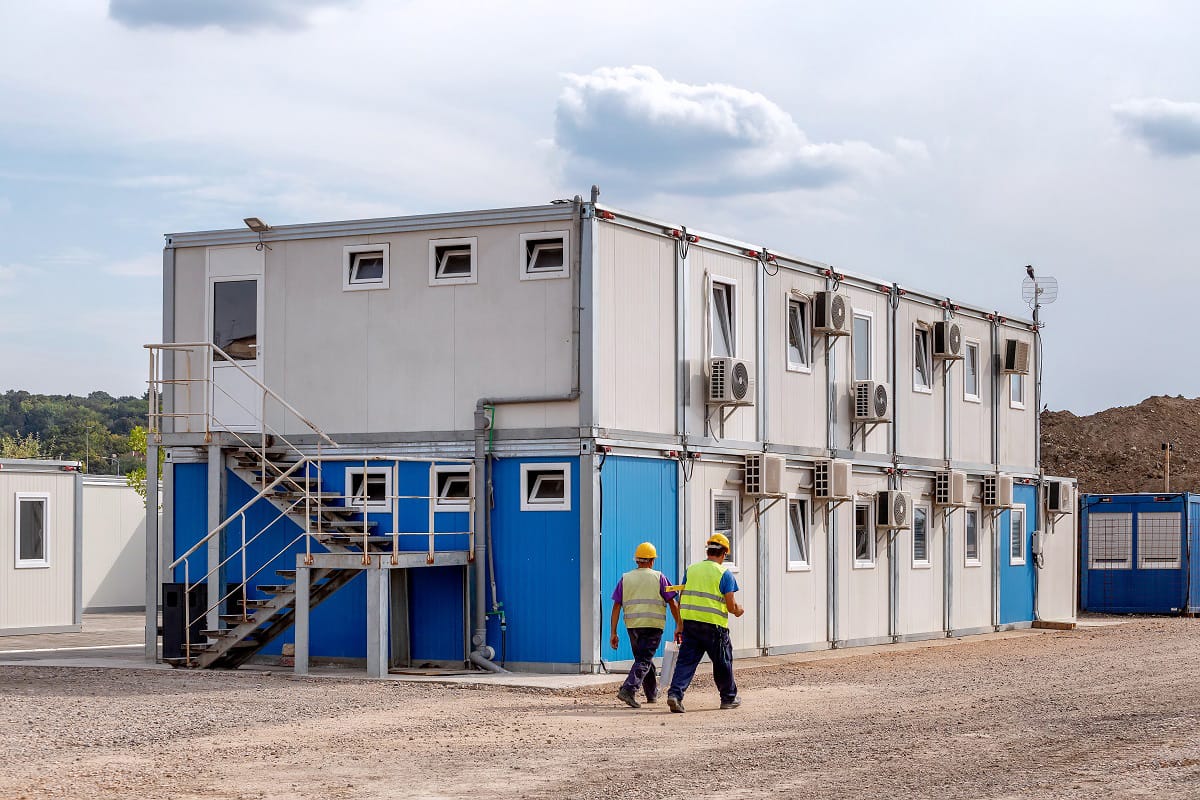
Commercial modular buildings and manufactured structures have long suffered from a perception issue. The ability to build large-scale buildings faster and cheaper seemed too good to be true and the market at large decided it must be a low-quality product. However, a decade ago, hotel giant Marriott was one of the first (in modern times) to champion modular structures and showcase just how wrong the industry had been about modular builds.
Since that time studies have continuously shown that modular construction can significantly cut build time and generate project cost savings with fewer laborers and equipment needed onsite, but it can also improve build quality and provide a safer environment for workers. In fact, according to the Modular Building Institute (MBI), more than two-thirds of general contractors reported that modular construction resulted in cost savings of 5% or more. The MBI also noted that offsite framing via modular construction reduces wood waste by at least 23%. From a safety perspective, the ability to utilize modular processes to build multistory buildings on the ground floor of a factory drastically reduces the risks of injuries associated with falls.
In fact, the lack of skilled labor in the construction market is a major driving force as companies are now more willing to take a closer look at modular builds. According to the Bureau of Labor Statistics, nearly one in five construction workers is age 55 or older. As these skilled laborers retire or age out, construction companies will have their hands full as they look to hire, train and deploy a new generation of workers. Modular’s factory approach can help fill the gap and ensure jobs are completed according to the project timeline without interruption.
As labor, competitive and cost factors push more contractors and developers to embrace the opportunity to go modular as a first choice and not a last resort, it’s become clear that adopting this new model requires more than just a willingness to make it happen. How can your business gear up for making the shift to think as a manufacturer and not just a contractor? How do you equip your company to move from project to production? And how can you structure your teams and operations for success? Here are five factors to consider as your company moves to a modular construction model:
1. Don’t Wait to Collaborate
Constructing any building project requires multiple experts from across the building lifecycle. From engineers to architects, designers to permitting, electricians to HVAC, everyone needs to be involved to get the job done. For modular builds, early collaboration is even more important. Discussing the goals, objectives and nuances of a modular build from the outset enables the collective group to identify issues and concerns, develop a comprehensive plan for execution, and ensure you can deliver a successful project.
2. Evaluate Size and Scale
Modular builds are bound by only a few different factors, and size is one of the most critical. For example, deciding which factory to work with may come down to size limitations based on production layout. The other element where size is a consideration is transportation. How will you get the pieces of the build from the factory to the site? Perhaps your team has decided it makes more sense to put the façade on the building onsite. You don’t need to give up your design or architectural elements and the cost benefits of a factory product. But you should leave time and space to determine how you’ll get them to the site.
3. Be Mindful of State Regulations
Speaking of transporting modular components, it’s important to note that while the Department of Transportation has some control over how oversized loads are moved, by and large it comes down to state regulations. How you move things in Massachusetts is different than how modular builds can be transported in Texas, for example. Do you need a flag car in front and in back? A police escort to the site? These nuances can raise or lower your overall costs, so be sure your team has transportation considerations built into your project expenses from the start.
4. Embrace Technology and Innovation
In the past decade, technology has advanced significantly, providing both applications and automation needed on the plant floor to drive efficiencies on production, materials and the broader supply chain. In tandem, innovative building products from plumbing to drywall have come to market. Understanding which advancements can help streamline your processes and deliver a superior quality product is paramount. Work with a trusted partner who can help navigate the ins and outs of technology innovations at both the plant floor level and the materials used in the build.
5. Use Your Resources
When it comes to construction, there is no silver bullet. But projects of every size and scale have one major success factor: collaboration. Modular construction is just one group of people figuring out how to work together to get the project done efficiently and effectively. With so many intricacies however, you simply can’t go it alone. Leverage industry associations and work with strategic partners that have experience with multiple plants and multiple scenarios. Take advantage of the collective industry knowledge to make your build as successful as possible. Distribution partners can help you understand the advantages of modular, and trade events can provide valuable opportunities to network and learn more.
From medical facilities to quick-service restaurants, hotels to multifamily homes, modular is finally gaining traction in the market. The industry has better capabilities, better technology, and better processes that are primed and ready to make modular a reality and eliminate the poor-quality perception, even as the skills gap persists. As your business makes the shift to modular construction, there are proven best practices that can be utilized to help make the transition as seamless as possible. Understanding the subtleties and working with industry partners can ease the path forward and help you capitalize on the modular movement.
More from Modular Advantage
AI, Faster Sets, and Automation: The Future of Modular is at World of Modular
While the modular building industry has long known that it can be an effective solution to increase affordable housing, the word is slowly spreading to more mainstream audiences. Three presentations at this year’s World of Modular in Las Vegas hope to provide insight and direction for those seeking a real solution to the crisis.
An Insider’s Guide to the 2025 World of Modular
The Modular Building Institute is bringing its global World of Modular (WOM) event back to Las Vegas, and with it comes some of the industry’s best opportunities for networking, business development, and education. Over the course of the conference’s four days, there will be numerous opportunities for attendees to connect, learn, and leverage event resources to get the most out of the conference.
Affordable Housing Now: The Industry’s Best Bring New Solutions to World of Modular
While the modular building industry has long known that it can be an effective solution to increase affordable housing, the word is slowly spreading to more mainstream audiences. Three presentations at this year’s World of Modular in Las Vegas hope to provide insight and direction for those seeking a real solution to the crisis.
Opportunities for Innovation in Modular Offsite Construction
Modular Offsite Construction has already shattered the myth that it only produces uninspired, box-like designs. Architectural innovations in module geometry, configurations, materials, and products make it possible to create visually stunning buildings without sacrificing functionality or efficiency.
Safe Modular Construction with Aerofilm Air Caster Transport
In collaboration with Aerofilm Systems, Heijmans developed innovative skids using air caster technology for moving modules easily and safely. These pallets are equipped with an auto-flow system, making operation extremely simple.
Miles, Modules, and Memes: Building a Modular Network One Flight at a Time
At the end of the day, social media is just another tool for building connections, and like any other tool, needs to be used skillfully to work properly. Use social media thoughtfully, and it will open doors to real opportunities and relationships you didn’t even see coming.
Falcon Structures: Thinking Inside the Box
Some of Falcon’s latest projects include creating container solutions for New York’s Central Park and an East Coast professional baseball team. More and more, Falcon is shipping out container bathrooms and locker rooms to improve traditionally difficult work environments, like those in oil and gas or construction.
UrbanBloc—From Passion to Industry Leader
UrbanBloc specializes in three main categories or markets – what they call “Phase 0” projects, amenities, and urban infill. Clients are often attracted to shipping containers because from a real estate perspective they are considered an asset. Having the flexibility to move and transport these assets allows owners to respond to different circumstances in a fluid manner that they can’t get with standard construction.
The Hospitality Game-Changer
“Hospitality is about more than just providing a service – it’s about delivering an experience,” says Anthony Halsch, CEO of ROXBOX. “And that’s where containers thrive. They allow us to create spaces that are unique, efficient, and sustainable.”
Container Conversions Counts on Simplicity to Provide Critical Solutions
Container Conversions has fabricated and developed thousands of containers for varied projects, including rental refrigeration options, offices, kitchens, temporary workplace housing, and mobile health clinics.