Panel Replacement Adds Years to Life of Navy Vessel
Panel Built, Inc. (PBI), a portable building manufacturer in Blairsville, Georgia, recently replaced all the wall and roof panels on a two-story US Navy barge deck house that the company had originally installed 30 years ago, giving the vessel new life. The structure, which is used for storage and office space while the barge is docked in Charleston, South Carolina, was in pretty sad shape, patches and repairs giving it a rough look, but it was standing. Now, the commanding officer of the unit that uses the barge said the difference between the condition and appearance from when the barge left their facility to when the project was complete was beyond his expectations of what was possible.
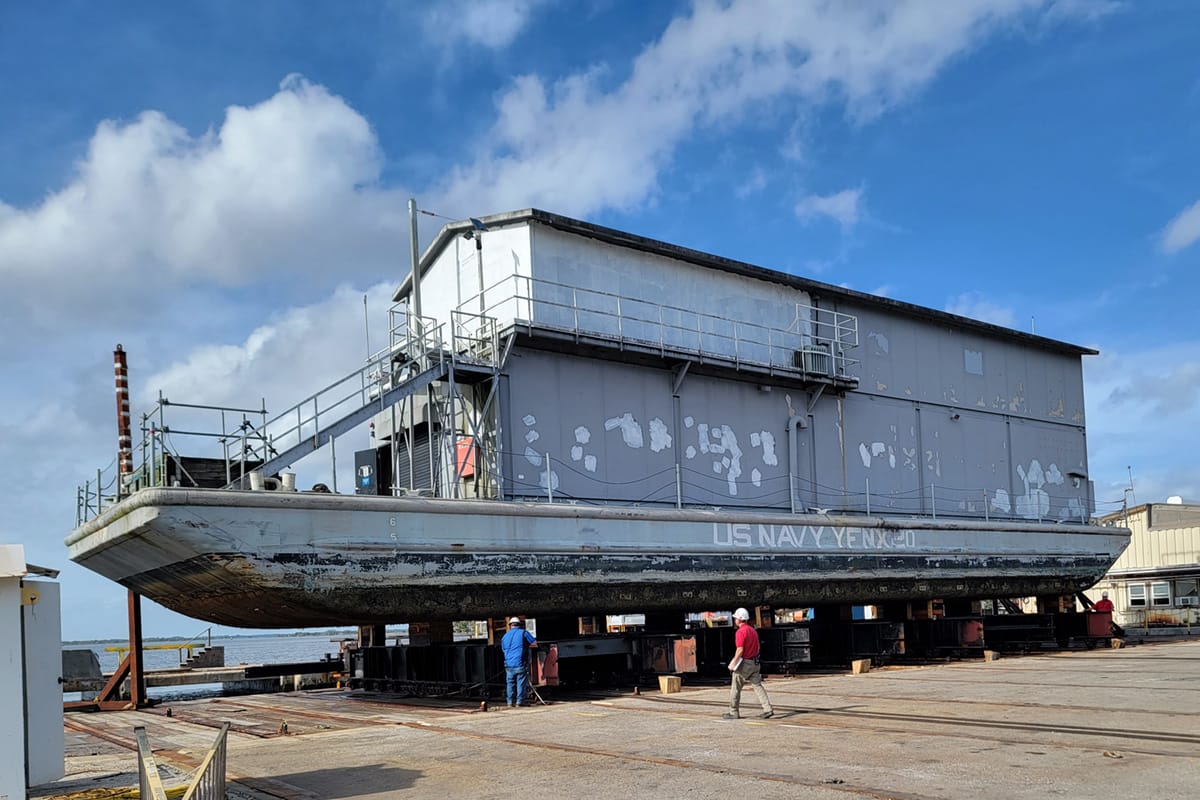
The U.S. Navy worked with Panel Built, Inc. to rebuild a sea-worn two-story deck house barge.
An Unusual Project from the Beginning
Mark Ledger, project manager for BAE Systems Jacksonville Ship Repair, a defense contractor that works on both commercial and military ships, said the project started when they won the contract to perform about 25 maintenance items on a Navy barge, and one of the tasks was to replace the existing deck house structure. “We weren’t familiar with the products or the process because we hadn’t done something specifically like that before,” said Ledger. “We were having difficulty finding sources for the material, so we asked the government, ‘do you have any reference for other companies that have worked on this sort of thing before?’ They recommended Panel Built because, based on the existing design documents, they were the company that constructed the original deck house.”
Eliyah Ryals, outside sales representative for Panel Built, said they didn’t understand the extent of the project until they saw the barge for themselves. “Once we got down to the site,” Ryals said, “we noticed the deck house structure had been through the ringer, you could say. It had been painted over multiple times and was deteriorating due to exposure to the sea. Some panels were in better shape than others, but the whole thing was in pretty bad shape. So, we proposed replacing every panel, the roof, the entire project, basically.”
The original deck house structure had been built and designed by PBI co-founder Michael Tiernan, so the team was able to find the original design documents and work from them. However, with code changes and higher engineering requirements, additional structural elements, including 4,500 pounds of new I-beams and tubular steel, were needed to meet the extreme wind load requirements in Charleston.
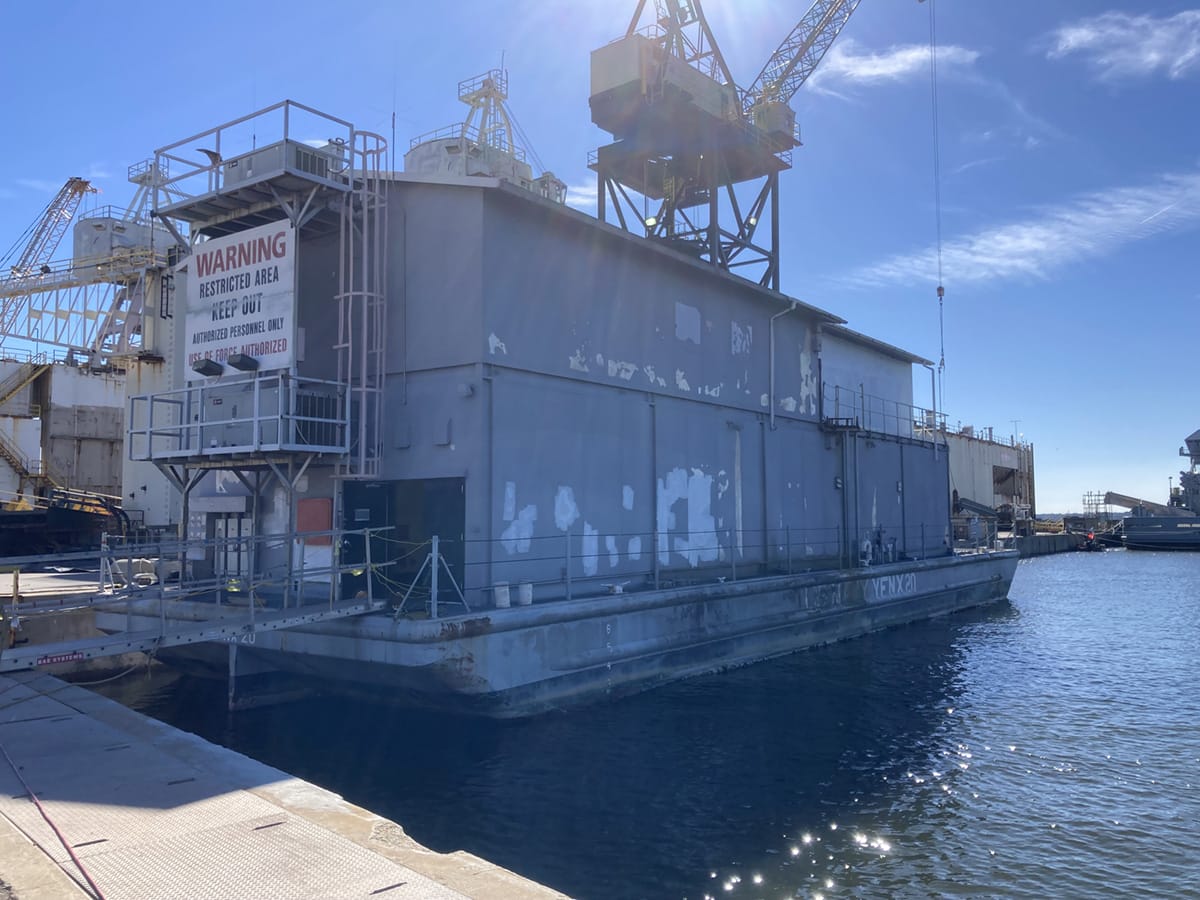
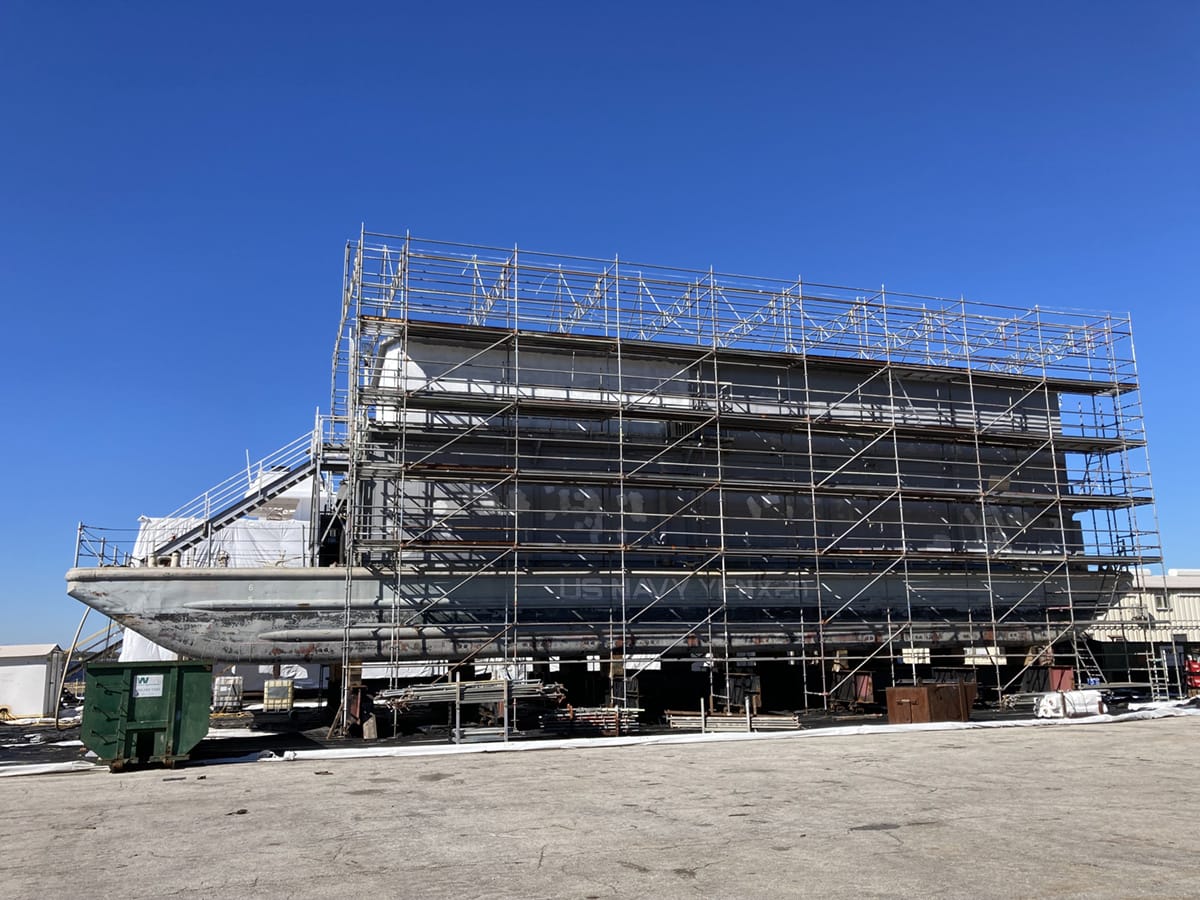
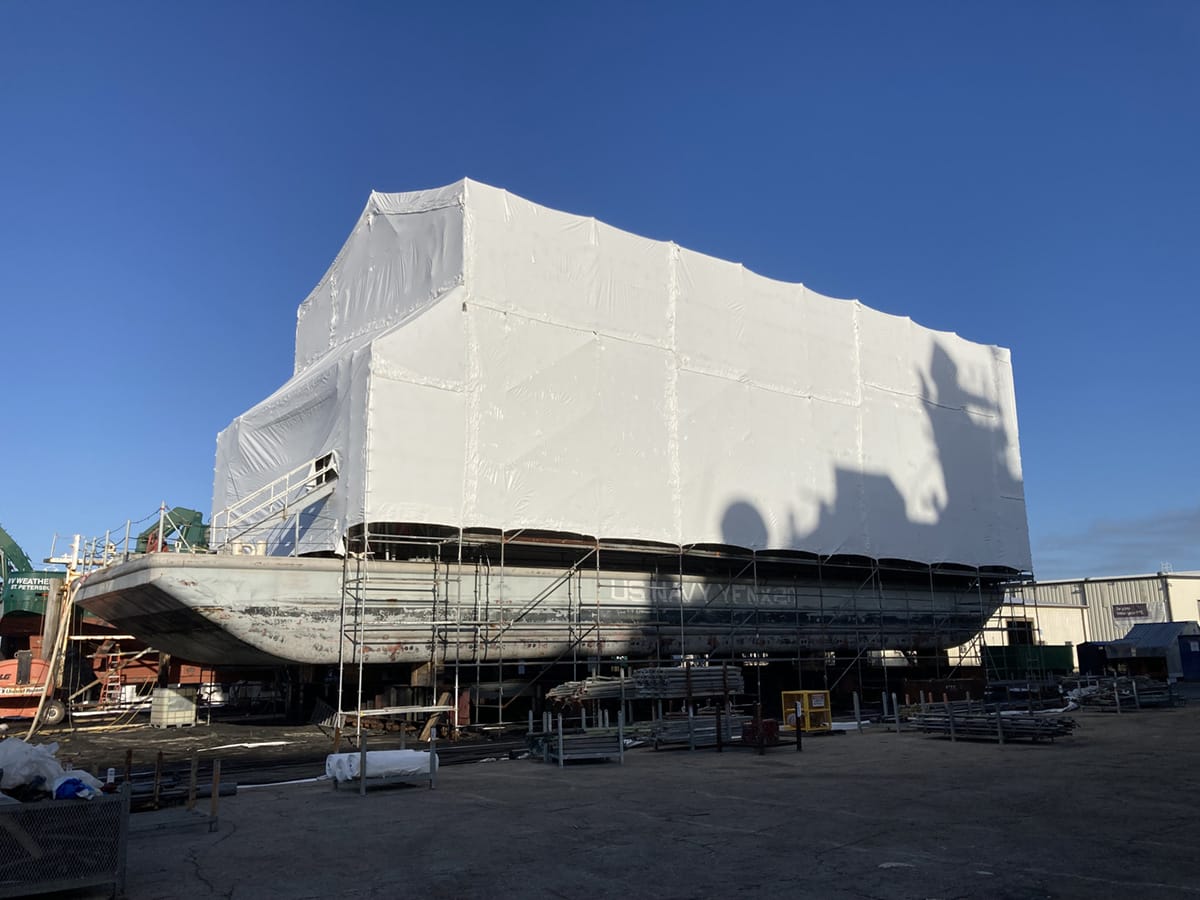
A Multitude of Challenges
Ledger said, “the primary design concern and focus was the wind loads. PBI performed a design study to ensure that the modifications made to the structural supports for the walls and roof would withstand those wind loads.” The materials had to be designed to stand up to sea water, salt air, extreme heat, sunlight, humidity, and the occasional hurricane.
Another concern was the weight of the additional elements. “We needed to know the approximate weight of the materials coming off the barge,” said Ledger. “With new materials and construction techniques, some of the additional elements were lighter and some were heavier. We had to calculate the overall weight increase to make sure it wasn’t going to be significant enough to affect the stability of the vessel.”
Because all the walls and roof panels were going to be removed and replaced, BAE constructed an enclosure to keep the space as dry as possible during the construction process. A plastic skin was wrapped around scaffolding to protect all sides of the structure. This made setting panels and getting materials to the barge very difficult, as the plastic had to be moved or removed temporarily while the panels or materials were being set, then closed up again once they are in place. “Because the structural steel was so large and heavy, we had to crane those pieces in through the roof of the containment and then replace it,” said Ledger. “For the roof and wall panels that Panel Built provided, we were able to use articulated forklifts to raise and lower the materials in and out.” Luckily the work was performed in Jacksonville, Florida, so the weather wasn’t much of a factor.
PBI also had to ensure that the structure was sealed properly to prevent leaks and moisture intrusion. “We have buildings all over the US and the world that get rained on and that’s pretty normal for buildings. But with this structure actually sitting on the water on the coast of Charleston, we definitely had to seal it up a lot tighter than usual.”
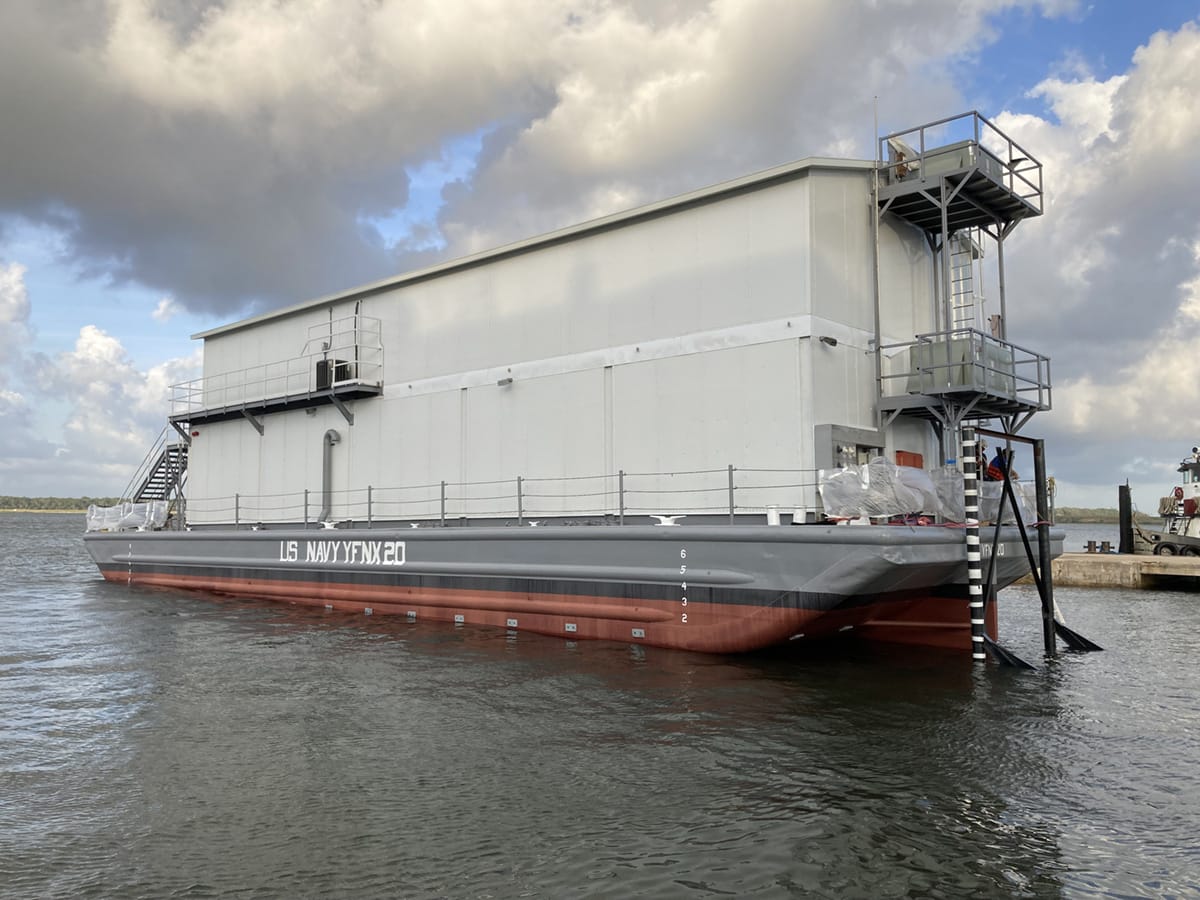
The refurbished barge was delivered to the Navy in June 2024, ready to serve again.
The Navy requested the same panel finishes as the initial installation, but they were no longer available. “The original building panels had a honeycomb core, which nobody builds anymore, so we had to switch it to a polystyrene core with an aluminum finish, for protection from sea water and rust,” said Ryals.
This project was definitely unusual for Panel Built. Ryals said, “I don’t think anybody really does a bunch of modular buildings on a barge on a normal basis.”
PBI shipped over 120 4’x10’ and 4’x12’ panels in just over four weeks from contract to delivery. The process ran smoothly, and installation was completed without any major issues. The panels come with a ten-year warranty, but Ryals said he wouldn’t be surprised if they lasted another 30 years.
Lessons Learned
Ledger calls the project a “great learning experience” and believes that it will help them in future work. “Some of the lessons learned involve how to disassemble and reassemble these types of modular construction components. We didn’t have much experience with these panels in the past. We have trades here in the shipyard that do similar things, but not with these kinds of materials. It was adapting an existing skillset to a new application. Now, instead of welding steel plate or fabricating something out of sheet metal, if we see that having a prefabricated structure like this would be a better alternative, then this gives us the ability to recognize that.”
Ryals said that while their team was a little leery of the project at the beginning, because of the high potential for something to go wrong, he is glad they took a chance on it because the product is performing well. “This was something that no other company wanted to tackle because they knew the risk. But all in all, it worked out.” He encourages those seeking similar work to contact PBI. “We’ve done it multiple times, so we’re well tooled to do it.”
The barge was delivered to the Navy at the end of June 2024. Here’s hoping the deck house lasts for another 30 years.
About the Author: Dawn Killough is a freelance construction writer with over 25 years of experience working with construction companies, subcontractors and general contractors. Her published work can be found at dkilloughwriter.com.
More from Modular Advantage
Oregon’s Prevailing Wage Proposal: A Wake-Up Call for Modular Construction
In early February, 2024, the Massachusetts Board of Building Regulations and Standards (BBRS) released its proposed 10th Edition building codes. This draft included several amendments targeting modular construction that would have created an extremely difficult environment for the entire modular industry and could have eliminated the industry entirely in the state.
Behind the Design of Bethany Senior Terraces, NYC’s First Modular Passive House Senior Housing Project
As more developers seek to meet new regulations for energy efficiency, the team at Murray Engineering has set a new record. With the Bethany Senior Terraces project, Murray Engineering has helped to develop NYC’s first modular structure that fully encompasses passive house principles — introducing a new era of energy efficiency in the energy-conscious city that never sleeps.
How LAMOD is Using Modular to Address Inefficiency, Sustainability, and the Future of Construction
As developers, designers, and contractors seek to understand the evolving needs of the modular industry, no one is as well-versed in the benefits of going modular as Mārcis Kreičmanis. As the co-founder and CBDO of LAMOD in Riga, Latvia, Mārcis has made it his ultimate goal to address the inefficiencies of traditional construction.
From Furniture Builder to ‘Activist Architect’: Stuart Emmons’ Unique Journey
Stuart Emmons was fascinated by buildings at a young age. He remembers building sand cities with his brother during trips to the Jersey shore. His father gave him his first drawing table at the age of ten. Today, he is an experienced architect who received his FAIA in June 2025. The road he took is unique, to say the least.
Forge Craft Architecture + Design: Codes, Contracts, and Intellectual Property
Founding Principal and Director of Modular Practice for Forge Craft Architecture + Design, Rommel Sulit, discusses the implications of codes, contracts, and intellectual property on
modular construction.
Eisa Lee, the “Bilingual” Architect
Now as the founder of XL
Architecture and Modular Design in Ontario, Canada, she applies not just her education as a traditional architect but an entire holistic view on modular design. It’s this expansive view that guides her work on being a true partner that bridges the gap between architects and modular factories as they collaborate on the design process.
Tamarack Grove Engineering: Designing for the Modular Sector
The role of a structural engineer is crucial to the success of a modular project, from initial analysis to construction administration. Tamarack Grove offers structural engineering services — project analysis, plan creation, design creation, and construction administration — for commercial, manufacturing, facilities, public services, and modular. Modular is only one market sector the company serves but it is an increasingly popular one.
Engineer Masters the Art of Listening to His Customers
Since founding Modular Structural Consultants, LLC. in 2014, Yurianto has established a steady following of modular and container-based construction clients, primarily manufacturers. His services often include providing engineering calculations, reviewing drawings, and engineering certification
Inside College Road: Engineering the Modules of One of the World’s Tallest Modular Buildings
College Road is a groundbreaking modular residential development in East Croydon, South London by offsite developer and contractor, Tide, its modular company Vision Volumetric (VV), and engineered by MJH Structural Engineers.
Design for Flow: The Overlooked Power of DfMA in Modular Construction
Unlocking higher throughput, lower costs, and fewer redesigns by aligning Lean production flow with design for manufacturing and assembly.