Built for Brutal Cold, This Modular Office Building Shines
A modular building approach is the perfect solution for the design of an office project that presented many environmental and logistical challenges. By employing an experienced team, continual communication, and strategic planning, Modular Genius provided a solution for each issue and completed the project on-time and to the client’s satisfaction.
Houlton, the county seat of Aroostook County, Maine, is a small town with a population of about 6,000 residents. Situated along the border between the U.S. and Canada, what the town is most noted for is bitterly cold, snowy winters comparable to those of Fargo, North Dakota or St. Petersburg, Russia. Temperatures can reach a brutal -41 degrees Fahrenheit during the winter months.
In 2020, government contractor CCI Alliance was awarded the job to build additional office space for the Houlton U.S. Border Control. CCI Alliance reached out to Modular Genius, a full-service modular building contractor, located in Joppa, Maryland, for help in ascertaining the best approach for constructing the building—traditional stick-built construction or modular construction.
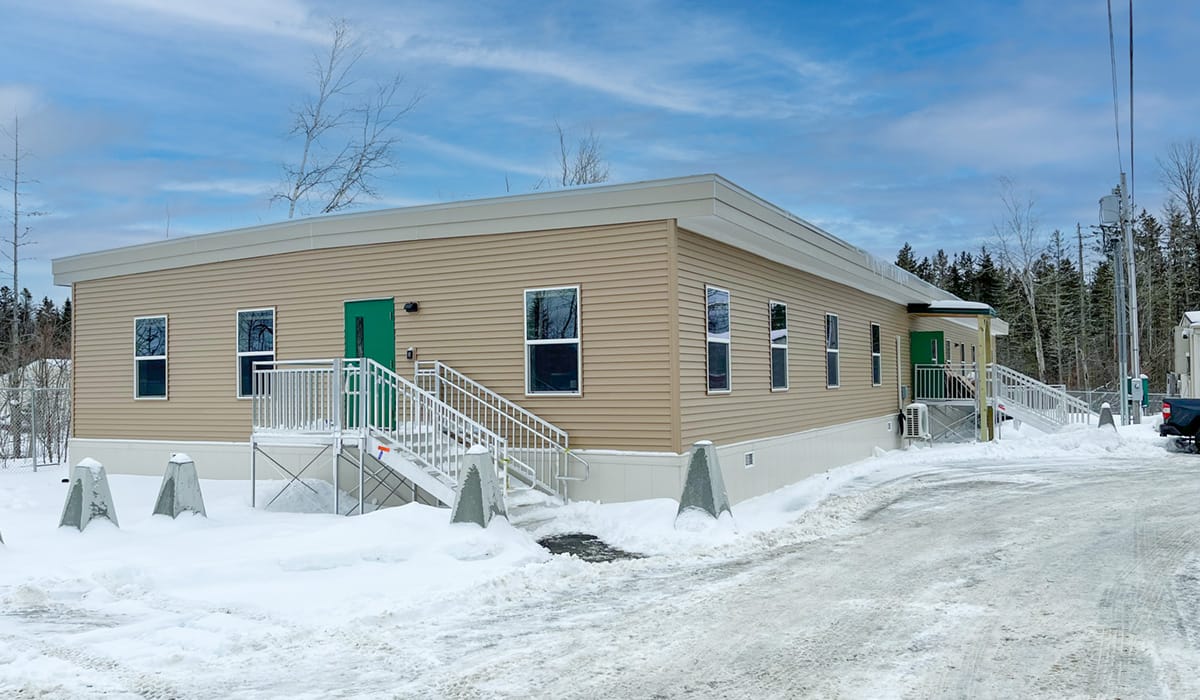
Built by Modular Genius, this modular office building was built to serve the U.S. Border Patrol during harsh Maine winters.
Why Modular?
A modular approach was deemed the best option for dealing with the many challenges the project presented. The environmental conditions limited the timeline for the project.
“Going modular made sense because the building could be manufactured in a controlled environment, leaving only minimal work to be done on-site,” says Edward Craig, business development manager for Modular Genius.
Working space on-site was tight—it was essentially restricted to the footprint of the new office building. Stick-built construction would require a very large lay-down yard for all the necessary building materials. Modular construction uses considerably less space.
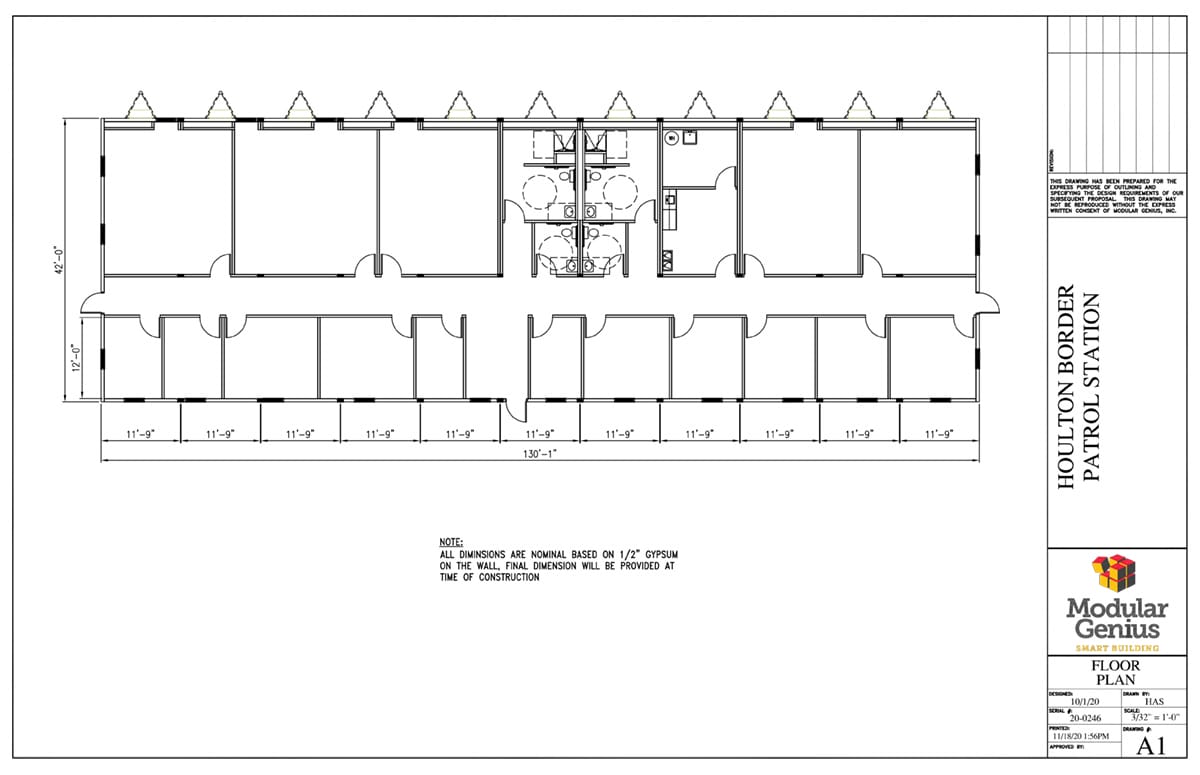
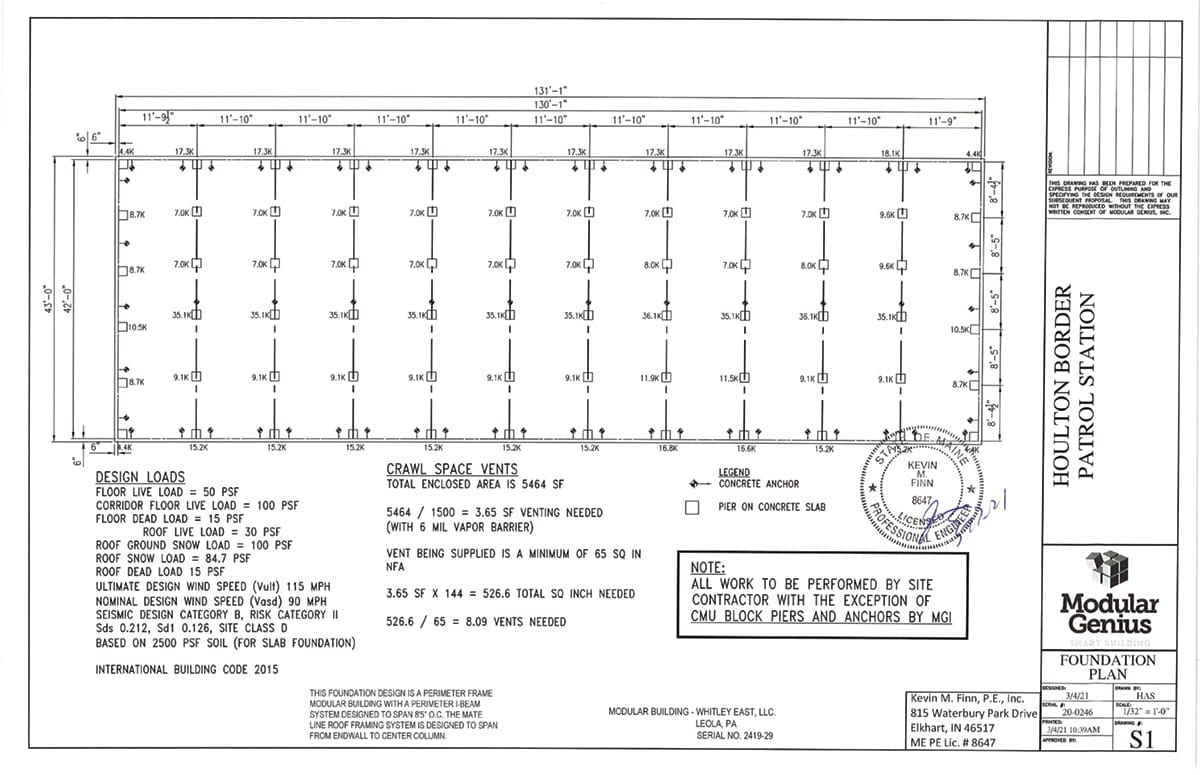
Designing for the Elements
Eric Gudeman, one of the company’s most experienced project managers, and Howard Scarpola, design & engineering manager, along with Craig, were the three key members of Modular Genius’s project team.
The 5,463-square-foot office building was designed using 12-foot by 42-foot modules, set roughly 36 inches above grade on piers, over a poured-in-place concrete slab. A total of 11 modules were used.
The building was designed with the environmental conditions in mind. Besides the extreme cold, the area often sees up to nine feet of snow annually.
Long overhangs were designed to cover the front and back of the building to prevent snowfall accumulation and help eliminate the freeze-thaw cycle which could stress the building. The overhangs do double duty by also protecting the HVAC systems from the elements.
Since the snow load for the area is 100 pounds per square foot, extra roof truss units were installed during the manufacturing of the modules.
Perhaps the biggest design challenge was to construct the foundation to withstand the harsh winters.
“In this part of Maine, the frost can reach up to three-and-a-half feet deep below grade, which can cause heaving and cracking of the concrete,” Gudeman says.
The solution was to reinforce the concrete slab with 4-foot by 8-foot by 2-foot rigid foam insulation around the perimeter of the poured concrete slab. Insulation was also embedded in the earth surrounding the perimeter of the foundation.
An insulated skirting panel, with an R-9 value, was installed around the building to help retain heat inside the crawlspace which houses the plumbing and electrical systems. While not requested by the client or required by Maine code, Modular Genius suggested the addition of a snow melt wire, an electrified heating element laid at the edge of the roofline.
“It helps to control ice damming by allowing the snow to melt evenly so it doesn’t come crashing down off the building,” Gudeman says.
One design consideration didn’t involve environmental conditions, but transportation issues. The modules had to meet the transportation requirements for each state as they were transported by truck from Pennsylvania, where they were manufactured, to Maine.
A Logistics Nightmare
The remote location posed its own problems. It was difficult to find local resources and supplies to support the project. For example, the town didn’t have any local utility contractors. Items like dumpsters and portable toilets, which were typically a phone call away, had to be procured in Augusta, Maine, a six-hour round trip.
The project required a greater than normal emphasis on communication with all tradesmen and workers on the project as well as tactical scheduling to keep it on track.
“There’s not a Home Depot down the street where you can buy a missing sheet of drywall,” Craig says. “If the subcontractors didn’t have all the proper materials with them on-site, it caused delays on the job.”
To complicate things further, a security fence ran along two sides of the site and a third side was for the sole use of the border patrol trucks. That left construction workers only one access point to the job site, which was confined to the modular building footprint, plus a lay-down area large enough to hold two modules at a time.
Normally the staging area is within half-a-mile of a project site, but for this project, the staging area was an hour-and-a-half away at Loring Air Force Base in Limestone, Maine. There, the modules were stored in an airplane hangar on the base to protect them from the elements.
Accessing the hangar at Loring Air Force Base to pick up the modules added extra steps and time to the normal process. Modular Genius had to adhere to a strict protocol which required additional paperwork, acquiring permission to enter, and waiting for an escort.
Gudeman had to coordinate the transportation of the modules so their delivery and the pace of construction were in sync. No small feat.
On-Site Work
The window of time for pouring the concrete foundation was late April into May. To speed the process, chemical additives were added to the concrete mix. Once the concrete was poured, it was covered with insulated mats to retain heat and moisture during the curing process so the concrete didn’t lose its viscosity and become brittle.
Installation of the modules began in October 2022. It took the installation team three 12-hour days of working under snowy conditions to rough-set the 11 modules so they formed one structure.
Plumbing and electrical was installed at the manufacturer, but the utilities had to be connected on-site. The pipes were insulated and heat trace wrapped. In addition, a circular pump was installed on the water lines so a minimal amount of water would circulate through each of the pipes, ensuring they wouldn’t freeze during a power outage.
Each module had its own panel box and the mechanical room was located internally.
A UV Tight-Fit Kit was placed in the HVAC system to kill airborne viruses, mold, and bacteria. It provides a healthier indoor environment and also extends the life of the HVAC system.
“This is not something we commonly see in modular buildings that we build,” Craig says. “But we were coming off the Pandemic and the client wanted it.”
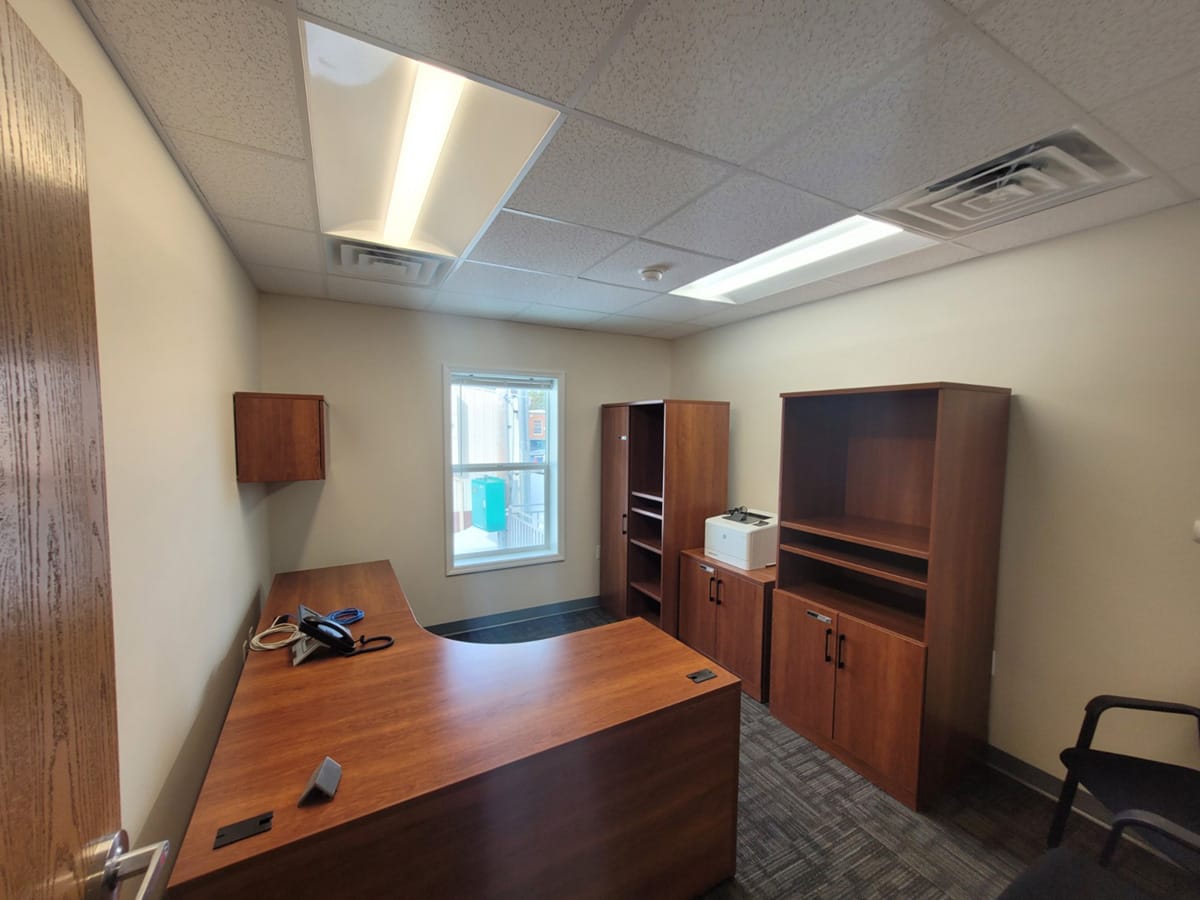
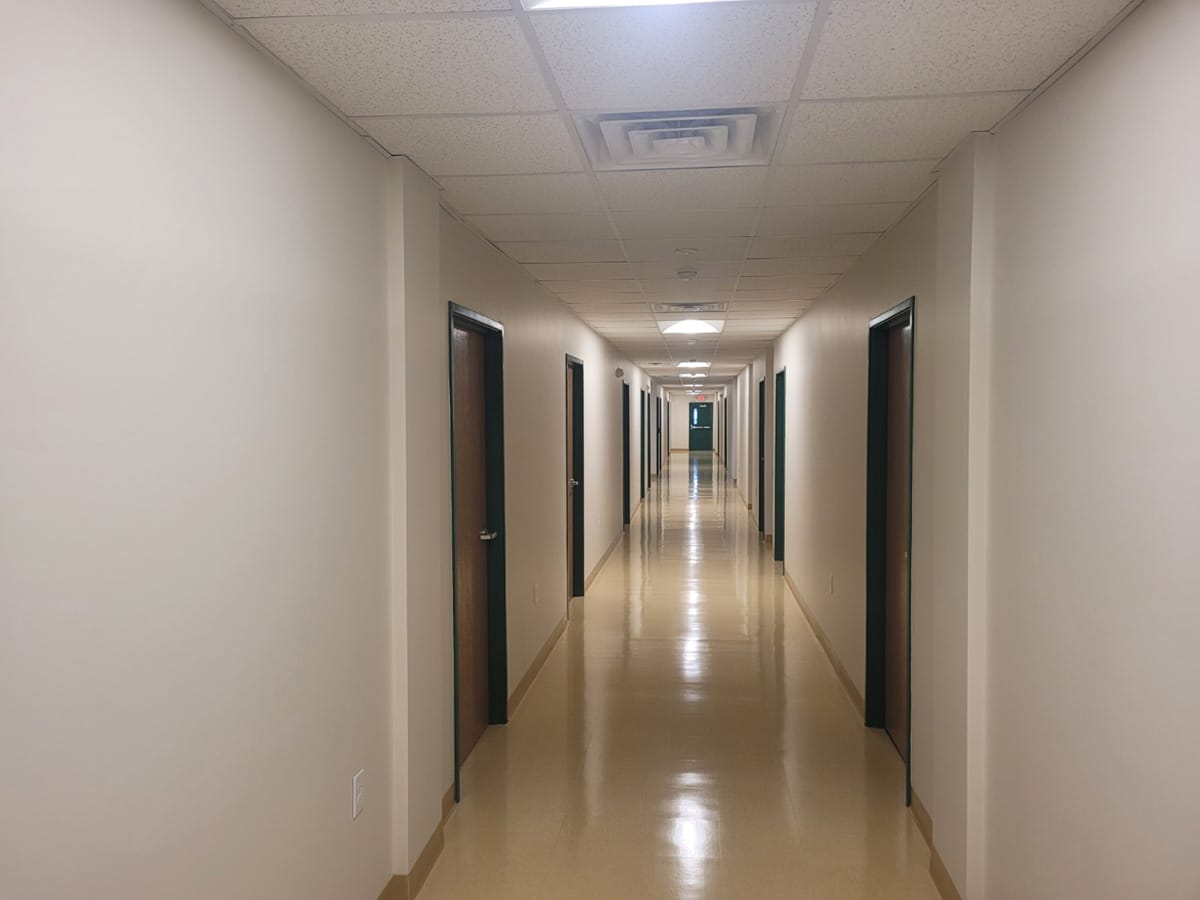
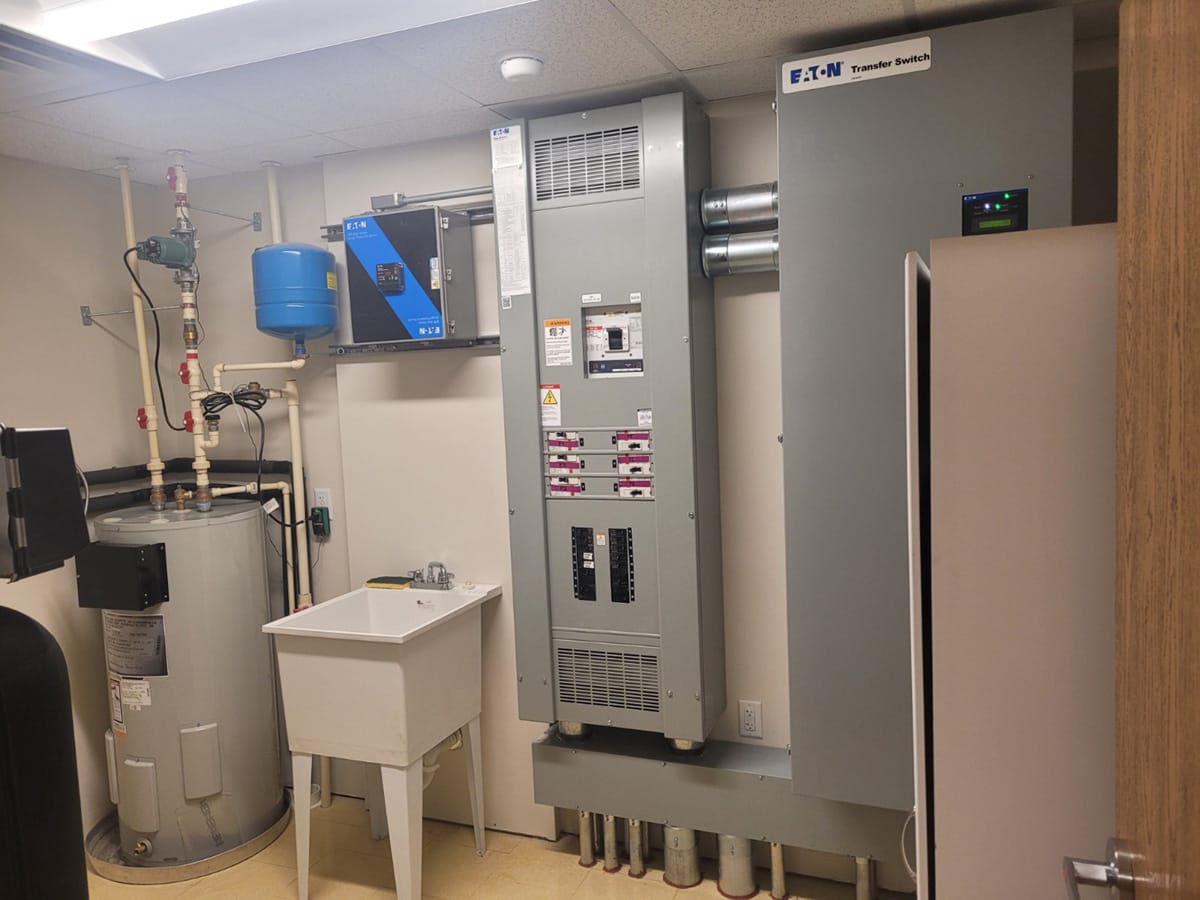
The interior work, such as painting the drywall and installing the flooring, began once the utilities were hooked up and the building was climatized.
The project was completed right after Thanksgiving of 2022. The whole process was finished in about one month.
Modular Genius always checks in with the client after the project is finished in case there are any little things that need to be addressed. They also take photographs of the finished building. It’s all part of the company’s customer service.
The new Houlton U.S. Border Control office is another success story for Modular Genius.
“The Border Patrol is happy and CCI is happy because they aren’t getting any calls from them,” Craig says.
Lessons Learned
Regardless of how many projects a company has completed, there’s always something new to be learned. This project was no exception.
“On the business development side, I learned to ask a lot of questions,” Craig says. “If you don’t ask the right questions, you won’t get the right information to help you execute the job smoothly for the client.”
Gudeman echoes that and adds, “It was all about the importance of coordination and communication—asking questions up front, and checking and double-checking materials and lists.”
For those who might be planning a similar project under cold, snowy conditions, Gudeman suggests researching the location, the weather, and the changing weather patterns. “Learning that information upfront was very beneficial once we started working on-site,” he says.
Craig suggests having an experienced team that can execute the deliverables, including a good vendor network. “One of the reasons we were able to execute is we have an equally experienced vendor network,” Craig says.
Would Modular Genius be willing to take on another job with so many challenges? “Absolutely,” Craig says. “One of the reasons people pick us is because we don’t shy away from the hard jobs.”
About the Author: Shari Held is an Indianapolis-based freelance writer who has been covering the construction industry for more than 20 years.
More from Modular Advantage
Oregon’s Prevailing Wage Proposal: A Wake-Up Call for Modular Construction
Should House Bill 2688A become law, building projects would increase in price, face longer completion timelines, and produce significantly more waste. The bill also incentivizes contract awards to out of state businesses who would not reinvest their earnings into the local Oregon economy.
Behind the Design of Bethany Senior Terraces, NYC’s First Modular Passive House Senior Housing Project
As more developers seek to meet new regulations for energy efficiency, the team at Murray Engineering has set a new record. With the Bethany Senior Terraces project, Murray Engineering has helped to develop NYC’s first modular structure that fully encompasses passive house principles — introducing a new era of energy efficiency in the energy-conscious city that never sleeps.
How LAMOD is Using Modular to Address Inefficiency, Sustainability, and the Future of Construction
As developers, designers, and contractors seek to understand the evolving needs of the modular industry, no one is as well-versed in the benefits of going modular as Mārcis Kreičmanis. As the co-founder and CBDO of LAMOD in Riga, Latvia, Mārcis has made it his ultimate goal to address the inefficiencies of traditional construction.
From Furniture Builder to ‘Activist Architect’: Stuart Emmons’ Unique Journey
Stuart Emmons was fascinated by buildings at a young age. He remembers building sand cities with his brother during trips to the Jersey shore. His father gave him his first drawing table at the age of ten. Today, he is an experienced architect who received his FAIA in June 2025. The road he took is unique, to say the least.
Forge Craft Architecture + Design: Codes, Contracts, and Intellectual Property
Founding Principal and Director of Modular Practice for Forge Craft Architecture + Design, Rommel Sulit, discusses the implications of codes, contracts, and intellectual property on
modular construction.
Eisa Lee, the “Bilingual” Architect
Now as the founder of XL
Architecture and Modular Design in Ontario, Canada, she applies not just her education as a traditional architect but an entire holistic view on modular design. It’s this expansive view that guides her work on being a true partner that bridges the gap between architects and modular factories as they collaborate on the design process.
Tamarack Grove Engineering: Designing for the Modular Sector
The role of a structural engineer is crucial to the success of a modular project, from initial analysis to construction administration. Tamarack Grove offers structural engineering services — project analysis, plan creation, design creation, and construction administration — for commercial, manufacturing, facilities, public services, and modular. Modular is only one market sector the company serves but it is an increasingly popular one.
Engineer Masters the Art of Listening to His Customers
Since founding Modular Structural Consultants, LLC. in 2014, Yurianto has established a steady following of modular and container-based construction clients, primarily manufacturers. His services often include providing engineering calculations, reviewing drawings, and engineering certification
Inside College Road: Engineering the Modules of One of the World’s Tallest Modular Buildings
College Road is a groundbreaking modular residential development in East Croydon, South London by offsite developer and contractor, Tide, its modular company Vision Volumetric (VV), and engineered by MJH Structural Engineers.
Design for Flow: The Overlooked Power of DfMA in Modular Construction
Unlocking higher throughput, lower costs, and fewer redesigns by aligning Lean production flow with design for manufacturing and assembly.