There Were a ‘Sea of Challenges’ for this Modular, Island Development
Question: Can modular construction be used to build a series of affordable, unique housing buildings, all styled to look like they were built in 1845, on an island that caters to the wealthy? The answer is, of course, yes, but how the team at Signature Building Systems and KOH Architecture got there is quite a story.
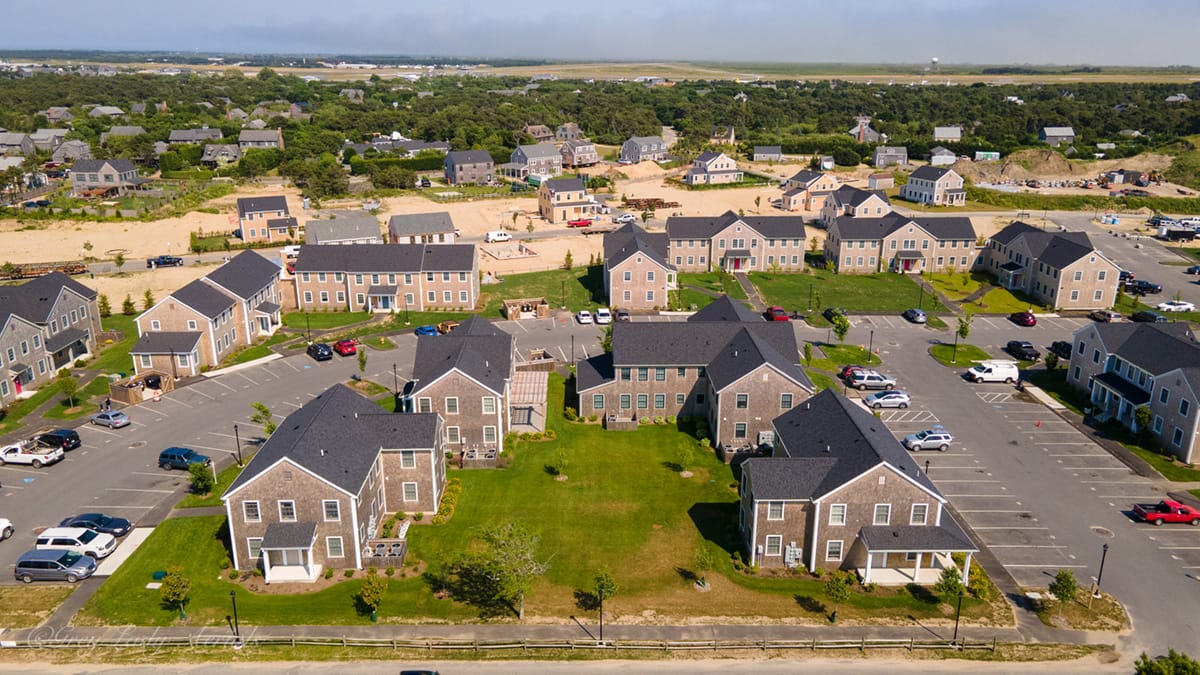
This Nantucket development, built by Signature Building Systems and designed by KOH Architecture, consisted on 44 building and 455 modules. Each module had to be transported to the island by barge.
The island of Nantucket, off the shores of Massachusetts, is home to some of America’s wealthiest homeowners. With a population of around 17,000, it’s home to all the comforts of the mainland, including restaurants, hotels, and Starbucks. What it lacks, however, is affordable housing for those who work in these businesses. Most employees either live on the mainland and take the ferry to work every day, or they live in basement apartments. While there have been attempts in the past to add workforce housing on the island, there just isn’t enough to go around.
In 2017, Tom O’Hara, Manager for Major Projects at Signature Building Systems (SBS), met with developer Phil Pastan of the Richmond Company Co., Inc., from Wilmington, MA. Pastan had acquired 72 acres of land in the middle of Nantucket that he wanted to convert into affordable workforce housing and single-family homes. The trouble was that all buildings on the island have to look like they were built in 1845 and must pass through the Historic District Commission (HDC) before building permits are issued. Add in the fact that most of the construction workforce on the island is busy building custom homes, and the natural conclusion was to use modular construction.
O’Hara and his team convinced Pastan and architect Dinah Klamert of KOH Architecture that they were the manufacturer to do just that. Then the fun began.
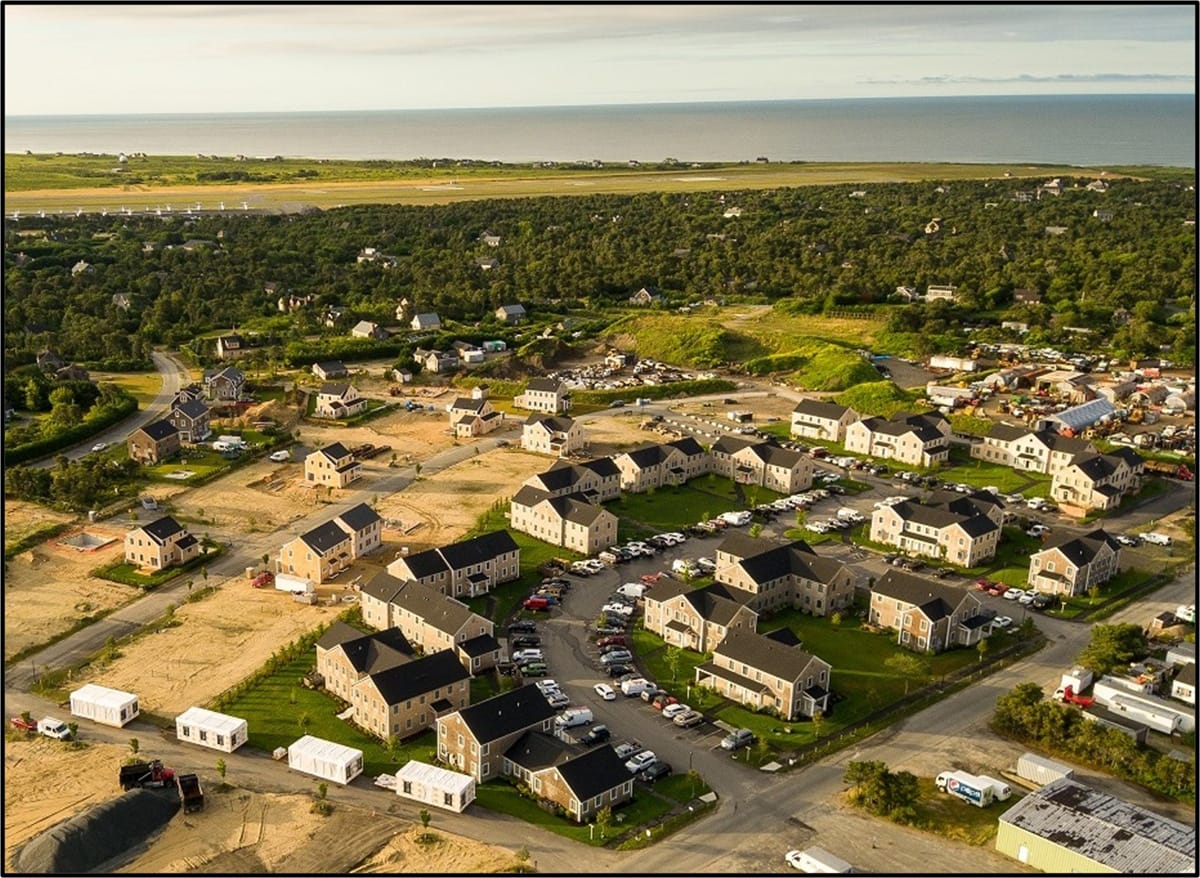
A Sea of Challenges
The project faced a number of challenges from the start: the historical requirements, lack of construction workforce on the island, transportation issues, changing building codes, and the fact that construction could only take place in the winter and early spring, the “off season” on the island. It took two years before construction began, then over the next four years the team slowly progressed, building by building, manufacturing and installing 44 buildings made up of 455 modules, each one completely unique.
HDC
The first hurdle for any building on Nantucket is to pass the HDC review. The design requirements include a certain gable roof style with specific slopes, specific trims, door colors, materials, roofing, etc. that have to be met before building permits are issued. Klamert would take the drawings that had been approved by the HDC to SBS and work with them to modularize the design for production, and if anything was changed, it all had to go back to HDC for reapproval. This process continued for each building of the development, whether it was an apartment building or a single-family home.
In addition, no two buildings on the island could look alike, so each one had to be individually designed. “Every building was different,” said Klamert. “It’s not like we could take the same design and reuse it over and over. The historic district commission would not allow that.” And design approvals for each building took two to six months.
Lack of Experience
O’Hara and his team faced an uphill battle – no one on the contracting team had any direct experience with modular construction. “We had to start from scratch with them and educate them about modular,” said O’Hara. “At one point we sent the boss’s plane and gathered up the plumbers, electricians, and other subcontractors, brought them to our factory and had a seminar. We walked them through the factory and explained what we were going to do.”
The reality of working on the island is that the majority of the workforce lives on the mainland. It’s a 45-minute ferry ride to the island and then they have to be picked up at the dock because they generally don’t bring their vehicles with them. Then they have to leave the site in time to take the last ferry, because if they miss it, a hotel room can be extremely expensive. Workers often only get six hours of work in before they have to return home. “You can’t get any momentum built,” said O’Hara. “It takes forever to build anything.”
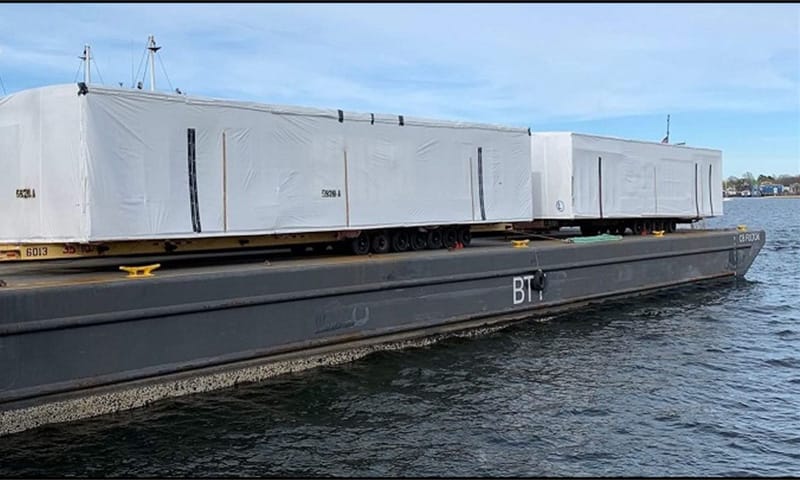
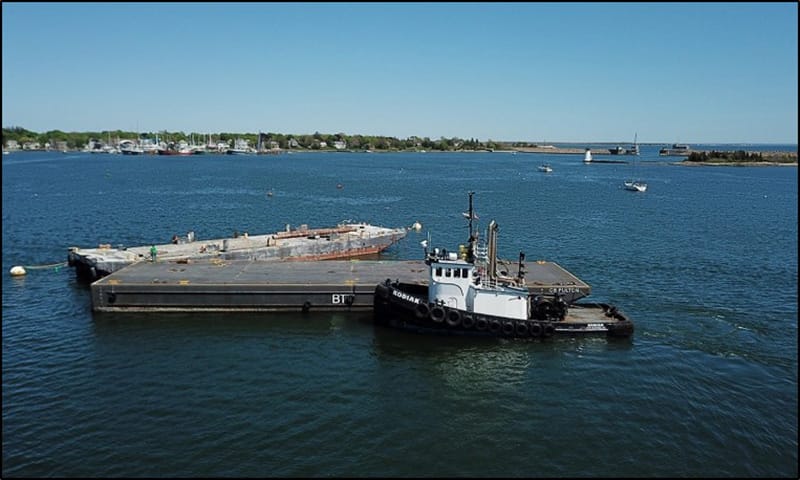
Each module had to make a 357-mile trip by truck to the wharf, then be loaded on a barge for the 66-mile journey across the ocean to Nantucket.
Transportation
Modules were constructed by SBS in Scranton, Pennsylvania. They then had to make a 357-mile trip by truck to the wharf, then be loaded on a barge for the 66-mile journey across the ocean to Nantucket. The journey was longer (Nantucket is only 26 miles off the coast of the mainland) because the wharf where the barge was docked was further away.
Each barge could hold only four modules, and only one barge could be launched per day. The barge carrier maintained a yard that could only contain eight modules, so SBS found a parking space across the road and up the street where they could stage some modules in there. O’Hara explains, “We would drive them up there during the day and park them at the barge head, and we would try to load up that area and the alternate parking area so that in the course of, say a week, five days, they could get 20 modules across.”
SBS found out that there was a limit to the size of module the barge could handle. “The barge couldn’t handle the size limit that we could build. We learned that the hard way by sending out modules that were too big, which they managed to struggle with, but told us not to send again. We said, ‘okay, no more 55 footers,’” said O’Hara. The modules varied in width from 10’ to 15’9” and in length from 27’ to 55’. There were 53 variations in module size for the 455 modules needed for the project.
Sending the modules on a barge also meant that they had to be protected from the harsh ocean climate during the rough winter months along the eastern seaboard. “Water was washing right over the top of the deck. So, we were very, very careful with how we protected the modules. We had to develop new ways to protect them and find new materials to use,” O’Hara said.
Code Changes
Another challenge was the changing energy codes over the four years the project was under construction. Massachusetts has optional energy efficiency codes, called stretch energy codes, that have been adopted in Nantucket. “When we first started, we were building a straight Massachusetts code-compliant product,” said O’Hara. “Then they adopted the first level of the stretch energy codes. During the process of construction, the code changed three times and each one of them necessitated enormous design changes.”
As an example, O’Hara explained that the first modules sent out had ductwork built into the floor trusses of each level of the apartment building. They would then install an air handler in each unit and send along the outdoor unit and pad for the on-site HVAC contractor to install. For the last modules they built (four years later), the HVAC system was completely assembled on-site and was composed of a split system with wall hanging, head units, and ceiling cassette units. Because the line sets had to be home runs and the modules were sectional, there was very little that could be done in a modular factory. Other changes included moving from fiberglass batt insulation to mineral wool batts, increased blown-in insulation in the ceilings and walls, better glass in the windows, and air sealing each module sufficiently to pass on-site blower door testing.
In addition, due to the high humidity on the island, crawlspace ventilation was a requirement for these buildings. “Sometimes you have to put dehumidifiers and ventilators in the crawl space with access to fresh outside air or through mechanical means,” said Klamert.
As if that wasn’t enough, the project team was often juggling the design of modules under one code standard, while contractors were installing modules under a different code standard. O’Hara said, “it was continual chaos, but interesting. Nobody got upset. It was not that kind of thing. Most people in the town wanted this development, so they cut us some slack and helped us get things done.”
Lessons Learned
O’Hara credits this project with providing the impetus for the development and expansion of SBS’s engineering department. “We added people, we learned stuff, and now the stuff we do is better for it. We’re now doing passive house apartment buildings and we learned all those techniques through the years of working on Nantucket. Everything we build, we now build the same way with an eye toward stopping air and energy leakage, which means you’ve increased efficiency enormously with no additional design changes.”
When asked what advice he would give to others about modular construction in similar circumstances, O’Hara said, “Modular construction is an excellent choice for island construction, but homework and planning are required. We commenced discussions with our client on this project in February 2017, but did not ship our first modules until April 2019. It takes time to discover the best alternative, evolve the best designs, and determine the best materials and techniques. And, most importantly, build the best team to accomplish the task.”
About the Author: Dawn Killough is a freelance construction writer with over 25 years of experience working with construction companies, subcontractors and general contractors. Her published work can be found at dkilloughwriter.com.
More from Modular Advantage
Oregon’s Prevailing Wage Proposal: A Wake-Up Call for Modular Construction
Should House Bill 2688A become law, building projects would increase in price, face longer completion timelines, and produce significantly more waste. The bill also incentivizes contract awards to out of state businesses who would not reinvest their earnings into the local Oregon economy.
Behind the Design of Bethany Senior Terraces, NYC’s First Modular Passive House Senior Housing Project
As more developers seek to meet new regulations for energy efficiency, the team at Murray Engineering has set a new record. With the Bethany Senior Terraces project, Murray Engineering has helped to develop NYC’s first modular structure that fully encompasses passive house principles — introducing a new era of energy efficiency in the energy-conscious city that never sleeps.
How LAMOD is Using Modular to Address Inefficiency, Sustainability, and the Future of Construction
As developers, designers, and contractors seek to understand the evolving needs of the modular industry, no one is as well-versed in the benefits of going modular as Mārcis Kreičmanis. As the co-founder and CBDO of LAMOD in Riga, Latvia, Mārcis has made it his ultimate goal to address the inefficiencies of traditional construction.
From Furniture Builder to ‘Activist Architect’: Stuart Emmons’ Unique Journey
Stuart Emmons was fascinated by buildings at a young age. He remembers building sand cities with his brother during trips to the Jersey shore. His father gave him his first drawing table at the age of ten. Today, he is an experienced architect who received his FAIA in June 2025. The road he took is unique, to say the least.
Forge Craft Architecture + Design: Codes, Contracts, and Intellectual Property
Founding Principal and Director of Modular Practice for Forge Craft Architecture + Design, Rommel Sulit, discusses the implications of codes, contracts, and intellectual property on
modular construction.
Eisa Lee, the “Bilingual” Architect
Now as the founder of XL
Architecture and Modular Design in Ontario, Canada, she applies not just her education as a traditional architect but an entire holistic view on modular design. It’s this expansive view that guides her work on being a true partner that bridges the gap between architects and modular factories as they collaborate on the design process.
Tamarack Grove Engineering: Designing for the Modular Sector
The role of a structural engineer is crucial to the success of a modular project, from initial analysis to construction administration. Tamarack Grove offers structural engineering services — project analysis, plan creation, design creation, and construction administration — for commercial, manufacturing, facilities, public services, and modular. Modular is only one market sector the company serves but it is an increasingly popular one.
Engineer Masters the Art of Listening to His Customers
Since founding Modular Structural Consultants, LLC. in 2014, Yurianto has established a steady following of modular and container-based construction clients, primarily manufacturers. His services often include providing engineering calculations, reviewing drawings, and engineering certification
Inside College Road: Engineering the Modules of One of the World’s Tallest Modular Buildings
College Road is a groundbreaking modular residential development in East Croydon, South London by offsite developer and contractor, Tide, its modular company Vision Volumetric (VV), and engineered by MJH Structural Engineers.
Design for Flow: The Overlooked Power of DfMA in Modular Construction
Unlocking higher throughput, lower costs, and fewer redesigns by aligning Lean production flow with design for manufacturing and assembly.