From Toronto to Suriname A Global Modular Building Story
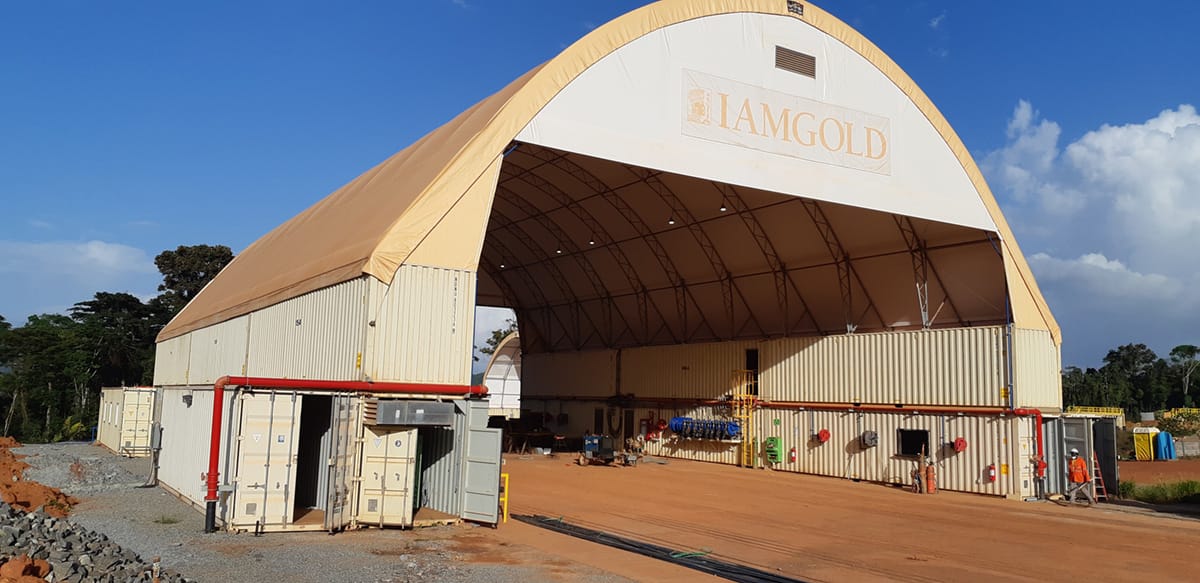
When I AM Gold first conceived of the project in Suriname to maintain its trucks and mining equipment, company leaders were planning to complete it as a stick-build project.
When I AM Gold – a Canadian gold mining operation based in Toronto, Ontario – wanted to expand its mining operations in Suriname, it knew it would also need to expand its infrastructure.
More specifically, they needed to build a mechanical services compound for their Pikin Saramacca project that would allow their local crews to maintain and repair trucks and other equipment critical to their mining operations. They also knew that it would be a challenge.
However, as a company with operations in some of the most remote and challenging places in the world, they’ve never shied away from difficult situations, and they weren’t about to start with this project.
So, in 2017, they started working on the design and planning how they would manage the construction process, and at that time, no one truly had any idea of the scale of the obstacles they would have to overcome.
Choosing Modular
When I AM Gold first approached a multidisciplinary engineering firm BBA in Montreal, including engineer Christian Tremblay, they were planning to complete their truck shop development as a stick-built project. Early budgets and feasibility studies, however, quickly proved that the cost to build on-site in a remote location like Suriname would not only be exceedingly difficult but also exponentially more expensive than anticipated.
The only viable option to complete the project on time and within budget was to build offsite, ship completed modules to the site, and assemble them using local labor and resources. But even that would prove challenging, as the team was soon to discover.
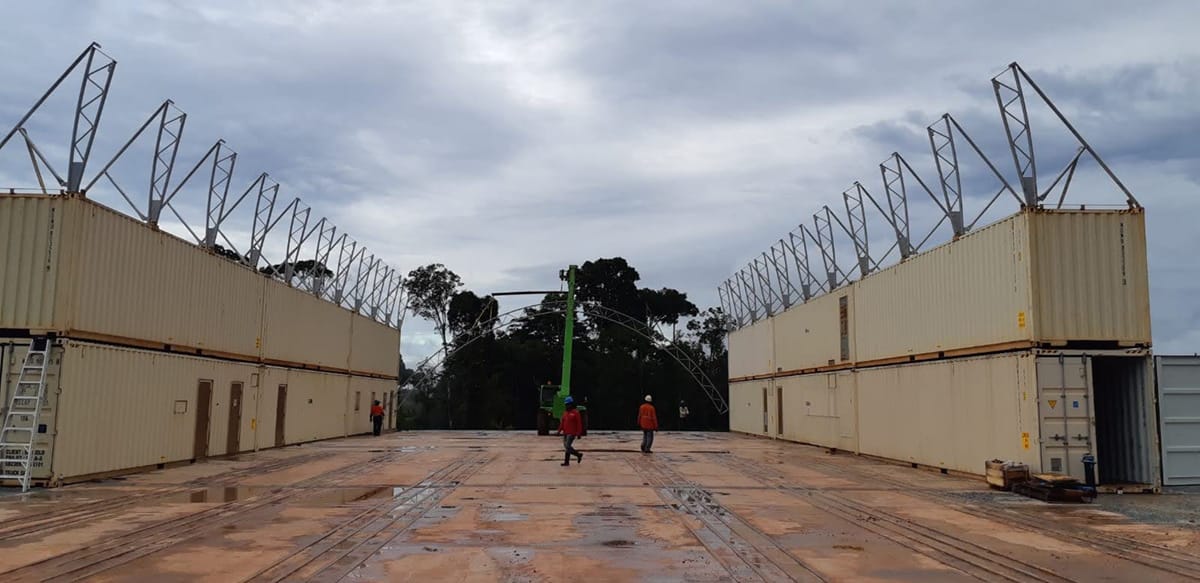
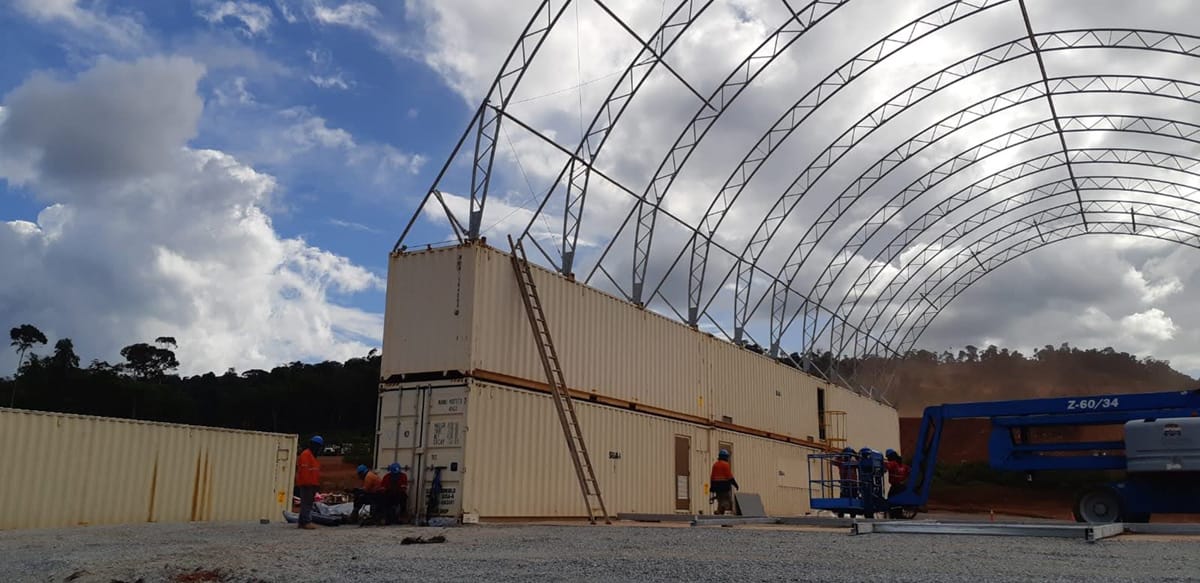
Invited Bidders
Once I AM Gold and their engineering and design team at BBA realized that modular was the only option for their Amazon expansion project, they also realized that there are a finite number of modular building companies who could successfully design, manufacture, and outfit the steel container-based structure they needed. A short list of companies with the skills and capacity needed to deliver was created, and the companies were contacted for pricing, design, and manufacturing information.
By the end of the procurement process, Corner Cast, a Montreal-based custom modular building company specializing in steel structures, had chosen to tackle the project.
Designing for International Shipping
While Corner Cast has been designing, building, and delivering high-quality steel modular structures since 2011, most of their projects thus far have been within Canada or in the continental United States.
This meant that the Corner Cast team, led by COO René Bernaert and project manager Aurélien Perez, had to ensure that all of their designs needed to be completely contained inside the shipping containers used for the project and weatherproofed for the trip to South America. It also meant that they needed to modify their designs to comply with local laws, including eliminating all wooden elements from the project.
However, with a capable and experienced in-house design team, Corner Cast handled these requirements easily, ensuring that all the modules and structural elements required for the project met the design and functionality requirements and were ready for rail shipping on time.
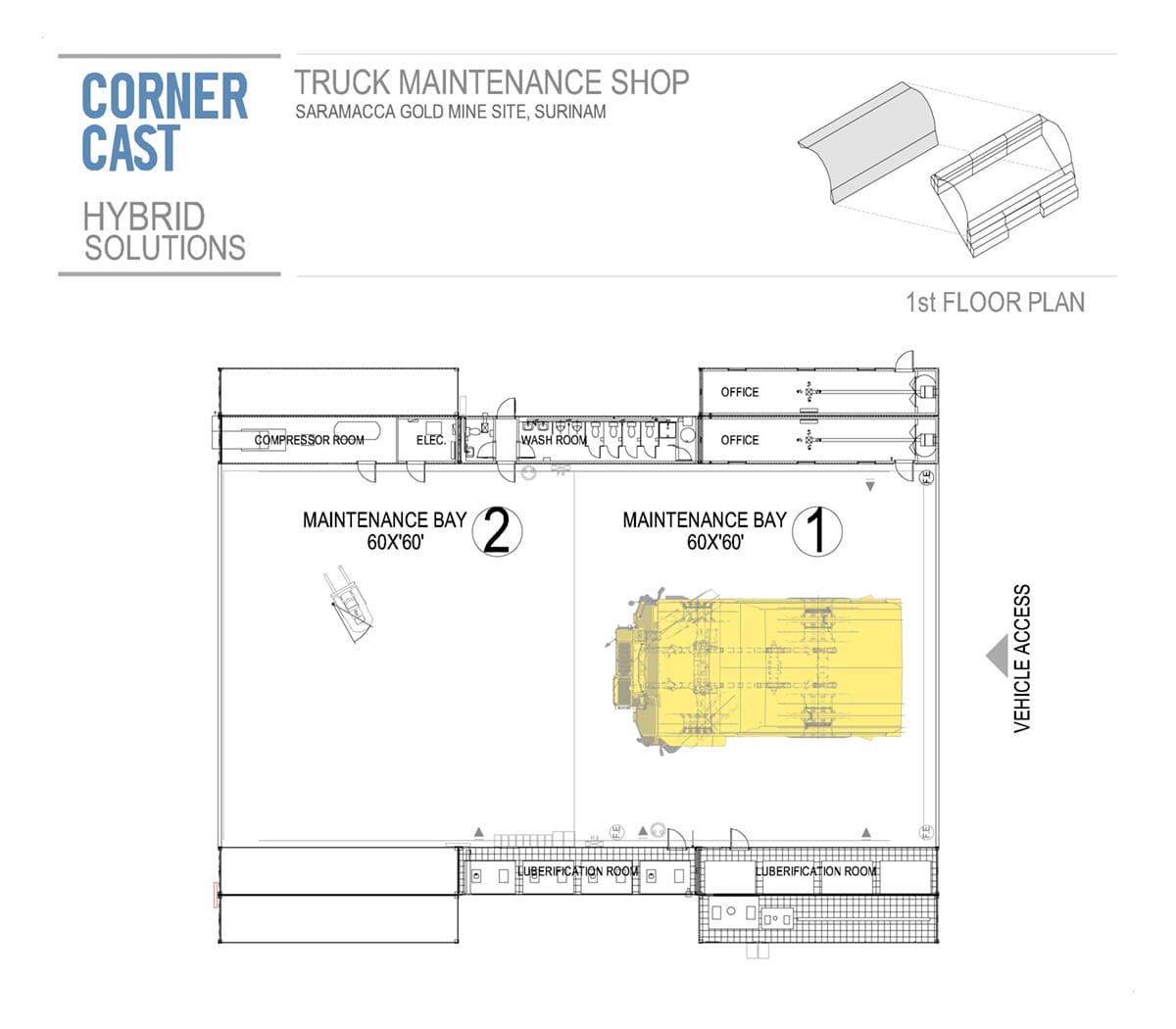
The Long Journey to Suriname
When you’re talking about most construction projects, the nearly 800-mile (1,200-kilometer) train journey the I AM Gold structures took from Montreal to Halifax would already be pushing the limits in terms of shipping or freight. But in this case, the containers and other structural elements built by Corner Cast had much more to travel before they arrived on site.
In fact, due to the remoteness of the port and the shipping line’s standard routes, all the containers destined for Suriname would first go to Spain before heading back across the ocean to the west coast of South America.
However, since this meant no special trips had to be made, there was a distinct environmental advantage to waiting a little longer for the containers to arrive.
A Road to the Amazon Rainforest
Having already navigated some complex issues, at this point of the project, you might assume that there would be plain sailing ahead. But not in this case.
Before and during the manufacturing and shipping of the building modules for I AM Gold’s new pit mechanical complex, the on-site construction crew led by Steve Chin A Foeng of Beyond Mining & Consulting had already been tackling some intense challenges of their own.
First and most importantly, there was the fact that the site chosen for the new mechanical workshop development was not level and needed extensive earthworks and that they had to build a haul road to the site for equipment access and to get the container modules themselves into position.
Since the site is also in a rainforest, engineers and construction crews had to carefully plan and construct concrete pads and other elements of the civils and services to minimize the impact of natural water runoff. This meant that even after the container modules and other elements of the structure arrived at the local port, they had to be stored there for nearly a year. So it wasn’t until the site and the road that would take them there were ready for use that they could finally be shipped to their final destination.
Local Challenges
Once the design, planning, manufacturing, and critical infrastructure were all in place and ready for the containers to make the final leg of the journey, the team building I AM Gold’s new mechanical service complex still had some unique issues to overcome.
Some, like the high rainfall, meant construction crews had to figure out how to keep trenches and excavations free of water for long enough to cast concrete or lay pipes. Others, like the differences in equipment and training of local crews, were solved with intensive, ongoing training, shipping tools and equipment, and making do with smaller machines wherever possible.
Then, there were some that could only be avoided, like the snakes and scorpions the crews shared the site with. Only in the Amazon will health and safety plans include the words ‘anaconda’ and ‘snake bite kits.’
Since the whole world was also caught in the grip of the COVID pandemic for a large part of this project, you can add travel restrictions and supply chain interruptions to this long list of once-in-a-lifetime problems. It’s hard to imagine any other project of this size that would face so many diverse and often quite unique difficulties.
Yet somehow, in spite of intense heat, torrential rain, unfinished roads, language and cultural differences, and deadly wildlife, the teams involved in this project successfully delivered the project to the client.
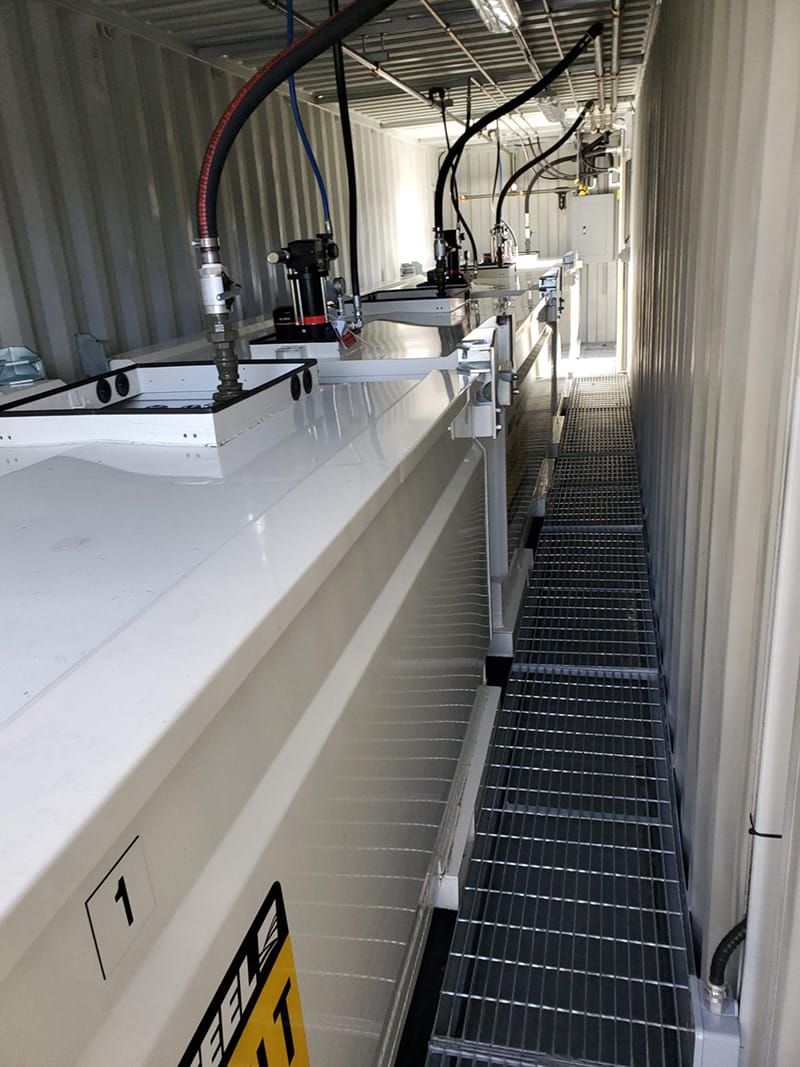
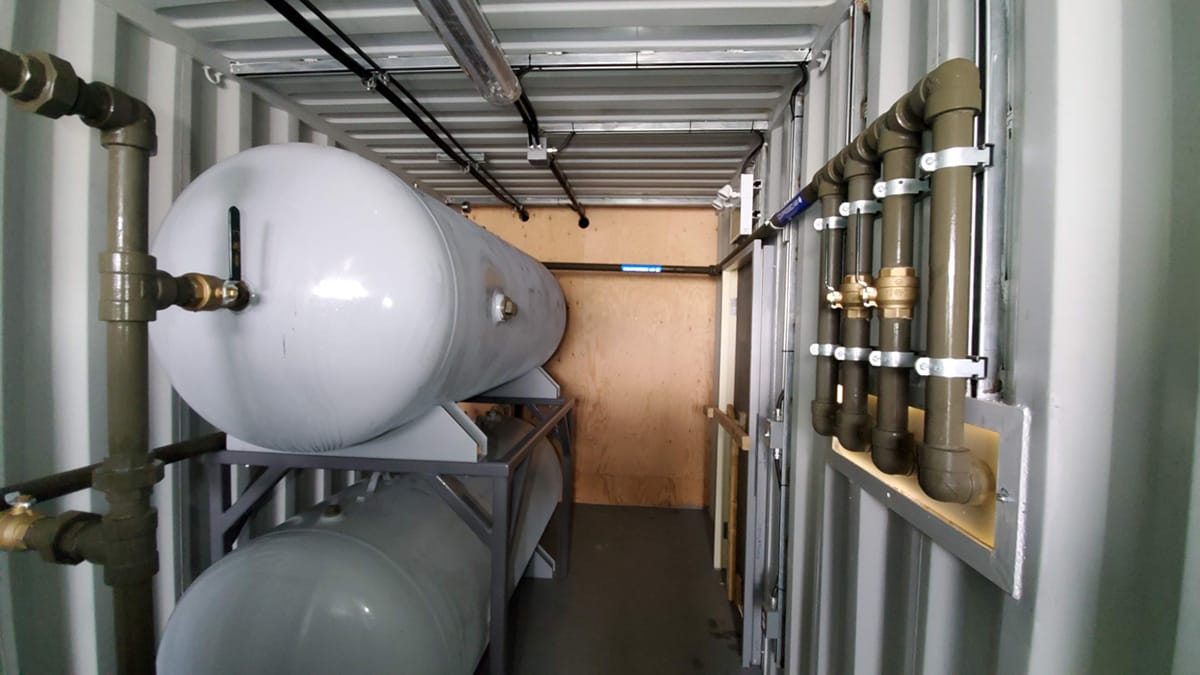
A Modular Solution to Complex Problems
Now that the dust has settled and I AM Gold has their new truck servicing and maintenance depot, there’s one thing every member of the team involved can agree on: there’s no way they could have completed a project with this many challenges and obstacles in the time it took if they were not building modular.
In fact, by all accounts, assembling the project’s modular elements on-site and connecting and commissioning them for use was the fastest and easiest part of the process, all thanks to the hard work and design skills of the modular professionals at Corner Cast.
That proves that when you’re faced with the most difficult sites in most remote places, modern modular construction solutions – and especially steel container-based buildings – should always be at the top of your list of options.
About the Author: Tamara Aspeling is a published author and freelance writer who specializes in construction and writes for print and web. She’s also a trained estimator and project manager with over 20 years of industry experience. You can reach her at www.theconstructionwriter.ca or words@theconstructionwriter.ca.
More from Modular Advantage
Oregon’s Prevailing Wage Proposal: A Wake-Up Call for Modular Construction
Should House Bill 2688A become law, building projects would increase in price, face longer completion timelines, and produce significantly more waste. The bill also incentivizes contract awards to out of state businesses who would not reinvest their earnings into the local Oregon economy.
Behind the Design of Bethany Senior Terraces, NYC’s First Modular Passive House Senior Housing Project
As more developers seek to meet new regulations for energy efficiency, the team at Murray Engineering has set a new record. With the Bethany Senior Terraces project, Murray Engineering has helped to develop NYC’s first modular structure that fully encompasses passive house principles — introducing a new era of energy efficiency in the energy-conscious city that never sleeps.
How LAMOD is Using Modular to Address Inefficiency, Sustainability, and the Future of Construction
As developers, designers, and contractors seek to understand the evolving needs of the modular industry, no one is as well-versed in the benefits of going modular as Mārcis Kreičmanis. As the co-founder and CBDO of LAMOD in Riga, Latvia, Mārcis has made it his ultimate goal to address the inefficiencies of traditional construction.
From Furniture Builder to ‘Activist Architect’: Stuart Emmons’ Unique Journey
Stuart Emmons was fascinated by buildings at a young age. He remembers building sand cities with his brother during trips to the Jersey shore. His father gave him his first drawing table at the age of ten. Today, he is an experienced architect who received his FAIA in June 2025. The road he took is unique, to say the least.
Forge Craft Architecture + Design: Codes, Contracts, and Intellectual Property
Founding Principal and Director of Modular Practice for Forge Craft Architecture + Design, Rommel Sulit, discusses the implications of codes, contracts, and intellectual property on
modular construction.
Eisa Lee, the “Bilingual” Architect
Now as the founder of XL
Architecture and Modular Design in Ontario, Canada, she applies not just her education as a traditional architect but an entire holistic view on modular design. It’s this expansive view that guides her work on being a true partner that bridges the gap between architects and modular factories as they collaborate on the design process.
Tamarack Grove Engineering: Designing for the Modular Sector
The role of a structural engineer is crucial to the success of a modular project, from initial analysis to construction administration. Tamarack Grove offers structural engineering services — project analysis, plan creation, design creation, and construction administration — for commercial, manufacturing, facilities, public services, and modular. Modular is only one market sector the company serves but it is an increasingly popular one.
Engineer Masters the Art of Listening to His Customers
Since founding Modular Structural Consultants, LLC. in 2014, Yurianto has established a steady following of modular and container-based construction clients, primarily manufacturers. His services often include providing engineering calculations, reviewing drawings, and engineering certification
Inside College Road: Engineering the Modules of One of the World’s Tallest Modular Buildings
College Road is a groundbreaking modular residential development in East Croydon, South London by offsite developer and contractor, Tide, its modular company Vision Volumetric (VV), and engineered by MJH Structural Engineers.
Design for Flow: The Overlooked Power of DfMA in Modular Construction
Unlocking higher throughput, lower costs, and fewer redesigns by aligning Lean production flow with design for manufacturing and assembly.