Opportunities for Innovation
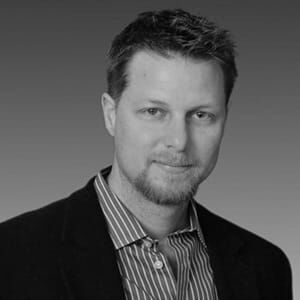
Colby Swanson is a Partner at Momentum Innovation Group and an Executive In Residence at ADL Ventures.
Innovation exists to positively change the status quo, drive progress, and create new value - something the construction industry desperately needs. Our industry faces a critical juncture, grappling with a shortage of skilled labor, stagnant productivity, escalating costs, and inconsistent quality. The complexity of challenges requires convergent collaboration - across disciplines (engineering, architecture, material science, finance, supply chain, etc.) and across sectors (construction, manufacturing) - where entrepreneurial agility is coupled with deep technical expertise and executive business savvy to propel construction innovation to new heights. We must look beyond traditional practices and embrace innovation inspired by industrialized construction (“IC”).
The often cited 2019 McKinsey report, Modular construction: From Projects to Products, succinctly states that a shift from traditional site-based construction (projects) to offsite prefabrication (products), when designed correctly, could provide up to a 12 percent improvement in productivity and reshape the construction supply and value chain as we know it. The reality is more nuanced so I have restated their “From projects to product” moniker to “From projects to building systems and processes”. The difference being a broader definition of “product” to include both a building system (of components) plus wrap-around processes which enable configurability, repeatability and scale.
The construction industry, often seen as resistant to change, is ripe for a revolution. The shift towards “building systems and processes” isn’t merely theoretical; it’s already taking shape in remarkable ways. From 3D-printed houses that rise in days (100 home subdivision 3D printed homes by ICON and Lennar) to modular skyscrapers that assemble like LEGOs (461 Dean St in Brooklyn consists of 32 modular stories, designed by SHoP Architects), the future of construction is unfolding before our eyes. But what does this mean for the average project? How can these innovations impact the way we design, build, and live in our spaces?
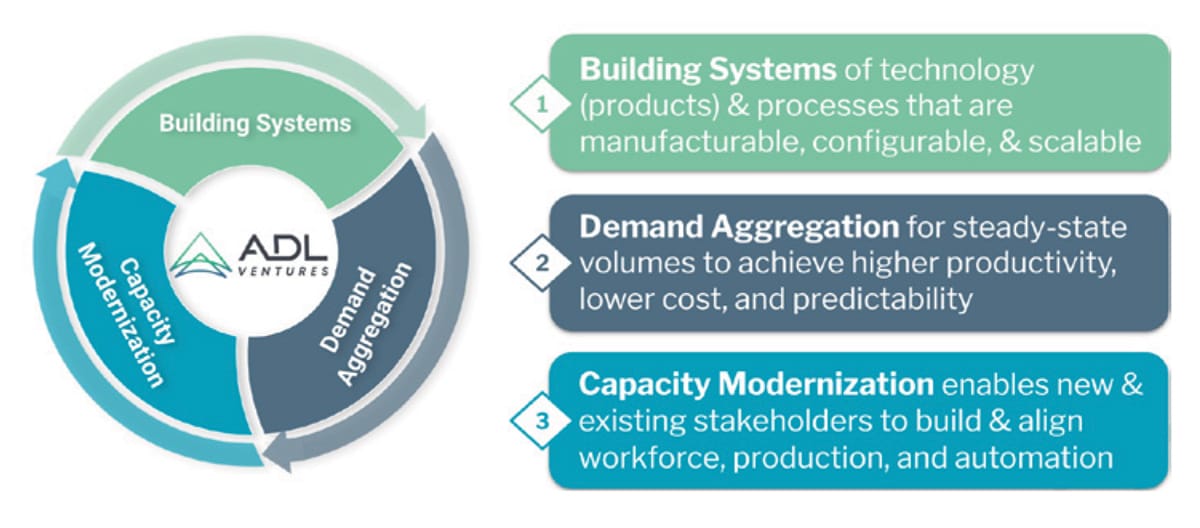
Theory of Change. Image courtesy ADL Ventures.
When considering where to innovate in the growing IC space, it helps to have a clear theory of change (“ToC”) to provide a focused roadmap of how change is expected to happen. ADL Ventures, a venture development firm who has spun-out eight companies, uses ToCs to guide decisions on where innovation has the highest potential for impact and success. There is another article to unpack in this ToC, but the core definition of each intervention is described in order of priority in the image as 1) Building Systems, 2) Demand Aggregation, and 3) Capacity Modernization.
In the next sections, we’ll delve into specific examples of construction and manufacturing innovation that are shifting more and more construction offsite. We’ll explore how these groundbreaking technologies and approaches are addressing the challenges faced by the sector, from labor shortages to sustainability concerns. We are at the dawn of a new era in construction, where imagination and ingenuity converge to build a better future.
Building Systems Innovation
citizenM’s revolutionary approach to hotel construction centers around their innovative one-room modular hotel product and process. Recognizing the inefficiencies and high costs associated with traditional construction, they boldly embraced modularization, aiming to create a standardized, high-quality guest room experience that could be replicated across the globe (12 modular hotels representing 3,000 keys). This singular focus on a single room type allowed them to streamline design, production, and assembly.
To achieve this, citizenM partnered with modular manufacturers (Polcom, CIMC) to produce these compact (8’x26’) yet comfortable guest rooms, prioritizing functionality and essential amenities. This streamlined approach eliminated unnecessary frills, enabling them to manufacture modules with exceptional precision in multiple off-site factories. These fully-furnished modules are transported and assembled on-site like building blocks, dramatically reducing construction time (~40% faster over site-built), cost (~10% savings compared to site built), and disruption. It also allowed them to reduce the punch list process from 2 months to 2 days. This process, rooted in both product AND process simplification, has allowed citizenM to expand rapidly, offering affordable luxury accommodations in prime urban locations, while setting a new benchmark for efficiency and sustainability in the hospitality industry.
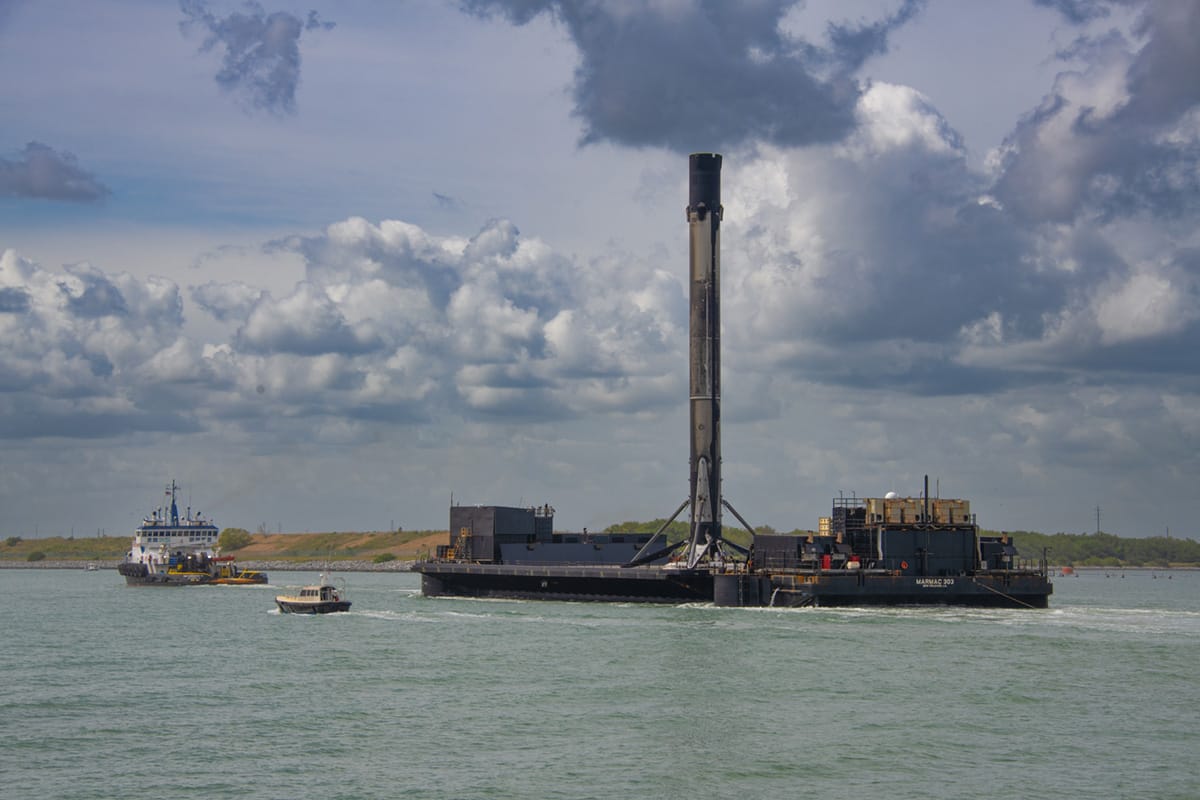
The SpaceX drone ship “Just Read the Instructions” and Falcon 9 booster are towed into port. The booster successfully landed on the droneship 8-1/2 minutes following its launch on 2/29/2024. It was the 11th flight for this booster and the 3rd landing on this droneship. Port Canaveral, Florida, USA 03/02/2024.
SpaceX’s Falcon rocket stands as a testament to the power of combining product and process innovation to revolutionize an entire industry. On the product front, Falcon’s reusable design fundamentally challenged the traditional expendable rocket model, drastically reducing launch costs ($67M Falcon vs. $350M+ for ULA’s Delta IV Heavy) and increasing accessibility to space. This innovation was complemented by a relentless focus on process optimization with SpaceX vertically integrating its manufacturing, streamlining production, and pioneering rapid iteration and testing. This holistic approach has not only disrupted the established aerospace giants but has also spurred a new era of space innovation and democratizing access to space.
Demand Aggregation Innovation
There are two great examples of demand aggregation in the IC sector: Sears Mail Order Homes and the HUD Manufactured Home Dealer network. It may not seem like it today but starting in 1908 and ending in 1940, Sears offered and sold around 85,000 house kits as part of its famous Sears catalog. By leveraging its vast mail-order catalog network, they were able to reach a massive audience and helped to make homeownership more accessible across the country (and particularly in rural areas). The standardized house kits included pre-cut lumber, all other materials (windows, doors, fasteners, etc) and instructions needed to streamline the construction process, and reduced the reliance on skilled labor.
While Sears wasn’t the first to offer kit homes, their bold approach, combining widespread distribution, mass production, and standardized components, helped shape the modern suburban landscape of the 20th century.
The modern non-construction innovative example of demand aggregation is cloud computing. Providers like Amazon Web Services and Microsoft Azure aggregated the computing needs of individuals and businesses of all sizes, onto a shared infrastructure. Instead of each entity needing to build and maintain their own expensive hardware data centers, they can rent computing resources on-demand from the cloud. The massive scale of cloud providers allows them to achieve significant economies of scale in purchasing hardware, managing data centers, and developing software. The demand aggregation in cloud computing has industrialized the IT industry, democratized access to powerful computing resources from startups to large enterprises, allows for easy demand scale-up (or down) flexibility, and significantly lowered cost for end users.
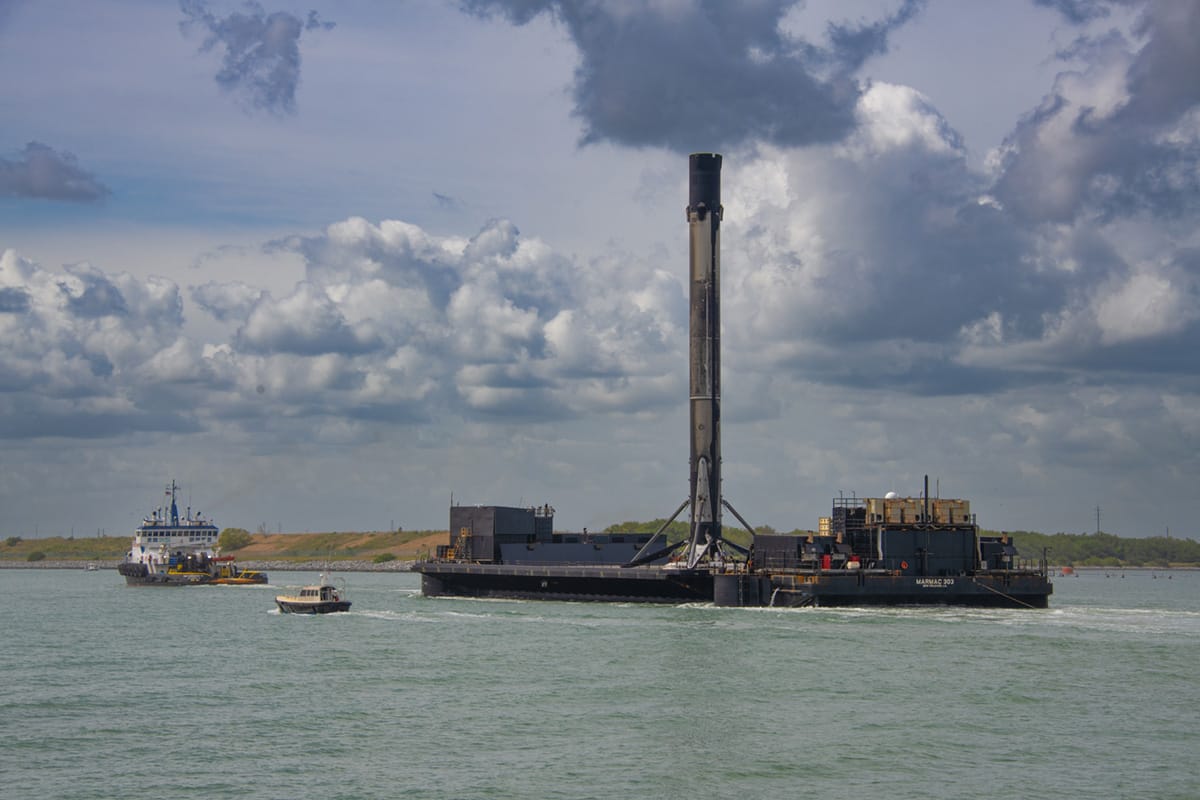
The SpaceX drone ship “Just Read the Instructions” and Falcon 9 booster are towed into port. The booster successfully landed on the droneship 8-1/2 minutes following its launch on 2/29/2024. It was the 11th flight for this booster and the 3rd landing on this droneship. Port Canaveral, Florida, USA 03/02/2024.
Capacity Modernization
First off, by “capacity” we mean both production capacity of IC components as well as developing the IC workforce needed to manage and run these facilities. Although we aren’t going to address the workforce in this article, it should be noted the opportunity to innovate in this space is tremendous considering over the next few decades, we will need to train millions of new IC-based construction workers to engineer, design, procure, manufacture, operate and assemble the future IC economy - blue ocean opportunities.
The factory is where a significant portion of the industrialization efficiency happens in the construction industry - the other areas are up-front product engineering and the onsite building assembly. A common mistake I see with investors and existing factories is wanting to first invest in a facility, or even worse, a highly automated facility, without first perfecting the building systems and securing a stable pipeline (demand aggregation). Today there are enormous inefficiencies of capital in current offsite factories. Value creation and manufacturing economies of scale are usually only occurring in a small portion of a factory considering most operations are basically site-building under a roof (and calling it manufacturing) or manufacturing building products that were designed for on-site use (vs. off-site use).
Only after the product and demand have been sufficiently resolved is it time to to design, optimize, then automate the manufacturing-to-site assembly process. Again, most people want to go right to automation, but this is the LAST step.
One innovative area to consider when trying to both design and manufacture more effectively, is fasteners. The auto industry learned many years ago that to accelerate production they needed to eliminate expensive and heavy rivets and screws. The secret to quickly assembling stronger, lighter cars lies in how they are assembled. Heavy fastening systems were required in the past. Today very high bond tapes and super glues, and quick connect engineered plastic and velcro fasteners, have replaced heavier mechanical fasteners. Modern fasteners provide speed, better performance, and result in total assembly cost savings. While mechanical fasteners concentrate stress at their connection points, tape spreads out this stress over a much larger area, mitigating stress fractures and failures.
Even better, is utilizing fewer components to assemble. The Tesla giga press was invented to cast the entire rear underbody of its Model Y vehicle into one part. Redesigning this part down to a one-step process eliminated around 370 other parts and massively reduced the time to assemble, weld and/or fasten.
We are starting to see building materials that are designed with IC in mind. Larger format products such as Cross Laminated Timber (CLT), Mass Plywood Panels, precast concrete elements, SIPs, and advanced insulation materials (VIPs, aerogel insulation) … much of these IC technologies cost more than their competition’s basic building material products, but when full production and installation cost are considered, the IC-based products win out every time.
The construction industry stands at a crossroads. By embracing the principles of industrialized construction, learning from other industries, and harnessing digital technologies, the industry can tackle its major challenges head-on. This transformation promises a future of increased productivity, improved quality, cost control, and a more sustainable, affordable and resilient built environment.
More from Modular Advantage
Oregon’s Prevailing Wage Proposal: A Wake-Up Call for Modular Construction
Should House Bill 2688A become law, building projects would increase in price, face longer completion timelines, and produce significantly more waste. The bill also incentivizes contract awards to out of state businesses who would not reinvest their earnings into the local Oregon economy.
Behind the Design of Bethany Senior Terraces, NYC’s First Modular Passive House Senior Housing Project
As more developers seek to meet new regulations for energy efficiency, the team at Murray Engineering has set a new record. With the Bethany Senior Terraces project, Murray Engineering has helped to develop NYC’s first modular structure that fully encompasses passive house principles — introducing a new era of energy efficiency in the energy-conscious city that never sleeps.
How LAMOD is Using Modular to Address Inefficiency, Sustainability, and the Future of Construction
As developers, designers, and contractors seek to understand the evolving needs of the modular industry, no one is as well-versed in the benefits of going modular as Mārcis Kreičmanis. As the co-founder and CBDO of LAMOD in Riga, Latvia, Mārcis has made it his ultimate goal to address the inefficiencies of traditional construction.
From Furniture Builder to ‘Activist Architect’: Stuart Emmons’ Unique Journey
Stuart Emmons was fascinated by buildings at a young age. He remembers building sand cities with his brother during trips to the Jersey shore. His father gave him his first drawing table at the age of ten. Today, he is an experienced architect who received his FAIA in June 2025. The road he took is unique, to say the least.
Forge Craft Architecture + Design: Codes, Contracts, and Intellectual Property
Founding Principal and Director of Modular Practice for Forge Craft Architecture + Design, Rommel Sulit, discusses the implications of codes, contracts, and intellectual property on
modular construction.
Eisa Lee, the “Bilingual” Architect
Now as the founder of XL
Architecture and Modular Design in Ontario, Canada, she applies not just her education as a traditional architect but an entire holistic view on modular design. It’s this expansive view that guides her work on being a true partner that bridges the gap between architects and modular factories as they collaborate on the design process.
Tamarack Grove Engineering: Designing for the Modular Sector
The role of a structural engineer is crucial to the success of a modular project, from initial analysis to construction administration. Tamarack Grove offers structural engineering services — project analysis, plan creation, design creation, and construction administration — for commercial, manufacturing, facilities, public services, and modular. Modular is only one market sector the company serves but it is an increasingly popular one.
Engineer Masters the Art of Listening to His Customers
Since founding Modular Structural Consultants, LLC. in 2014, Yurianto has established a steady following of modular and container-based construction clients, primarily manufacturers. His services often include providing engineering calculations, reviewing drawings, and engineering certification
Inside College Road: Engineering the Modules of One of the World’s Tallest Modular Buildings
College Road is a groundbreaking modular residential development in East Croydon, South London by offsite developer and contractor, Tide, its modular company Vision Volumetric (VV), and engineered by MJH Structural Engineers.
Design for Flow: The Overlooked Power of DfMA in Modular Construction
Unlocking higher throughput, lower costs, and fewer redesigns by aligning Lean production flow with design for manufacturing and assembly.