Data, Efficiencies Behind the Rise of MID-RISE Modular
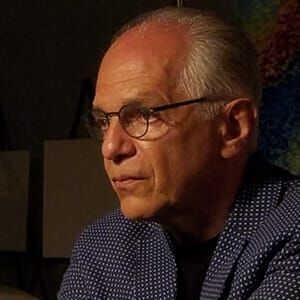
Peter DeMaria is the Chief Design Officer at MID-RISE Modular.
For the past 14 years, Diego Rivera, has been providing light gauge panels, structural and non-structural, to the largest general contractor companies throughout Los Angeles. In early 2023, he joined forces with Architect Peter DeMaria, to create MID-RISE Modular – an integrated design, engineering, fabrication and modular company in Southern California. Diego’s 2D panel solution technology created a segway into the 3D volumetric modules that DeMaria had been developing over the past decade. Their hybrid work at MID-RISE includes 2-D panel and 3-D volumetric modular solutions for student housing, assisted-living and a special emphasis on affordable multifamily housing - bringing modular solutions to those most in need of housing. Providing “white label” panel solutions to some of the most prominent LGS modular fabricators in the US, MID-RISE is also under contract for the design/fabricate/build of “The Liberty” – an affordable 8-story, 80-unit volumetric modular multi-family apartment building based in Los Angeles.
States Diego Rivera, “…at MID-RISE, the core of all fabrication is based in REVIT parametric models. When others utilize any other software to do cost estimating, production with roll forming machines or fabrication of 2D & 3D modules, we call that “finger painting” - we don’t finger paint here. We create parametric models and obtain all the data needed to be ultra efficient on price, speed and quality.” DeMaria adds, “…our REVIT models drive our fabrication processes, equipment and data that has an immediate impact on project design and budget. All captured data is digested prior to fabrication; thus, our REVIT tech is not only a driver of our fabrication process, it’s also is a direct extension of our Architecture design studio.”
Both Rivera and DeMaria are well versed in the arena of international fabrication. From the rain forests of Central America to the villages of Africa, to the massive modular facilities of China – they’re global footprint always leads back to their commitment to a parametric strategy. With their international experience, they’ve now expanded their production to Mexico. “Our commitment to REVIT technology enables us to transcend language, geographical and cultural challenges. We’ve walked away from “project manager” roles and have created “product managers” instead. These are our REVIT operators, engineers and fabricators who are intimately familiar with fabrication. Each has started with the company on the factory floor and is well versed in the realities of roll forming, screw fastening, welding, logistics and delivery – basically they’re empowered with a tremendous amount of knowledge prior to taking on roles as managers and engineers. While working in REVIT, they understand the nuances of 1/16” precision, dimpled studs, deflection and creep – it’s a powerful combination of skills and knowledge - a precursor to success in creating light gauge steel modular assemblies.
The transition to REVIT was a natural part of the company evolution and the driving factor has been simple – reduce, if not eliminate, conflicts on the jobsite.
2D panel-based projects were the first hurdle cleared. Full integration of the various engineering disciplines (Structural, M/E/P & F/LS) is merged and redrawn into parametric models. Collaborating engineers and architects love this strategy as any engineering conflicts are unveiled during the planning stages, not during the assembly, installation and construction phases. The result is a drastic reduction, if not elimination, of change orders and project delays.
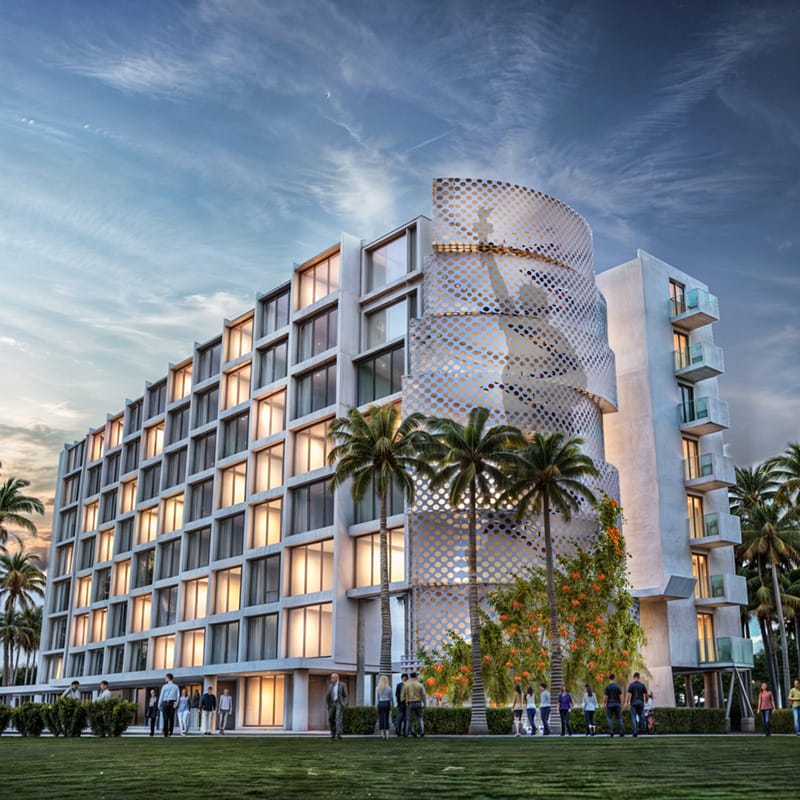
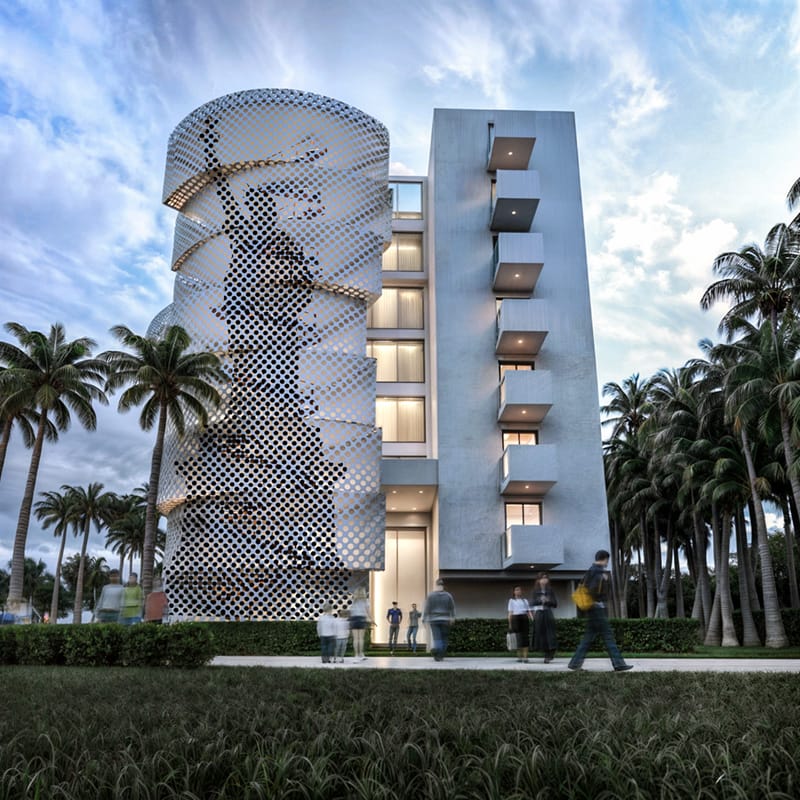
The Liberty in Los Angeles, CA.
Related Listening:
Communication & Collaboration: How Successful Modular Design and Fabrication Teams Work w/ MID-RISE Modular
Peter DeMaria and Diego Rivera of MID-RISE Modular unpack the intricate dynamics of integrating modern architectural methods into successful multi-story modular projects. Peter and Diego also share their insights on the logistical challenges and precision required in modular construction. The discussion highlights how aesthetics and technical expertise must harmonize to produce efficient and visually appealing buildings.
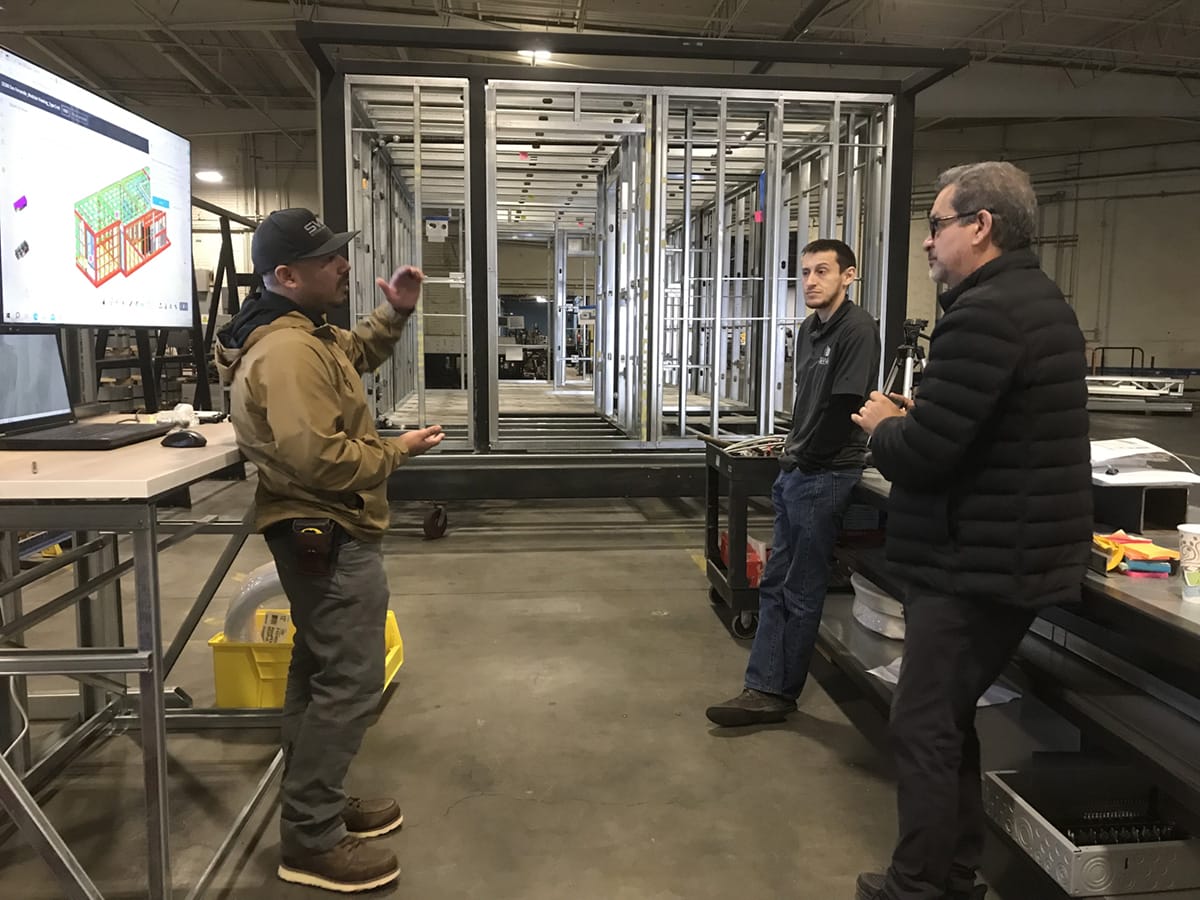
Diego Rivera (right) works with team members at MID-RISE Modular.
Instead of putting the fabrication team or a general contractor in a position where they’re forced to coordinate thousands and thousands of connections and integrations, that coordination is meticulously undertaken during the modeling stage, long before fabrication or building begins.
Migrating the REVIT strategy into 3D volumetric modular pursuits has been nothing more than extending and applying the same DNA that has proven so effective in the 2D panel world. The team has a masterful understanding of fabrication of light gauge steel and heavy gauge steel, however the current focus in the volumetric world is on the refinement and integration of the various building systems that are specific to building types. Multi-family residential projects provide an opportunity to eliminate on-site roofing, façade installation, ductwork, etc. and these are all MID-RISE developments made in the past year. All are by-products of a commitment to minimizing on-site work. None of this would be possible without the strong control over parametric models that enable the project to be clearly visualized early in the design and construction document phases. This level of predictability translates into an ultra-efficient fabrication process for MID-RISE.
DeMaria states, “when we combine our past and current REVIT prowess with new advances in Artificial Intelligence (AI), it is enabling us to jumpstart projects more rapidly. We’re able to reconfigure our building products and designs at unprecedented speeds.” Early exploration of feasibility and the massing of building modules quickly considers code compliance, sun/solar gain, building views, neighbor views, and a host of factors that enable the configuration of buildings more efficiently. While MID-RISE is committed to AI and the digital tools that provide for so much efficiency, DeMaria states there is another overarching influence in their work, “…we never lose sight of who and what our buildings are serving – and it’s always people. We’re creating buildings and spaces that enhance the built environment. More than creating modular buildings that are efficiently constructed, we’re responsible for creating places that have a positive impact on our quality of life. AI is in it’s infancy but on its way to taking into consideration local vernacular, how people live in a specific neighborhood, and all the other nuances that impact the design of a site-specific project – it then makes recommendations on how to satisfy this wide range of design criteria. Ultimately, much like our commitment to REVIT, we’ll harness AI as well.
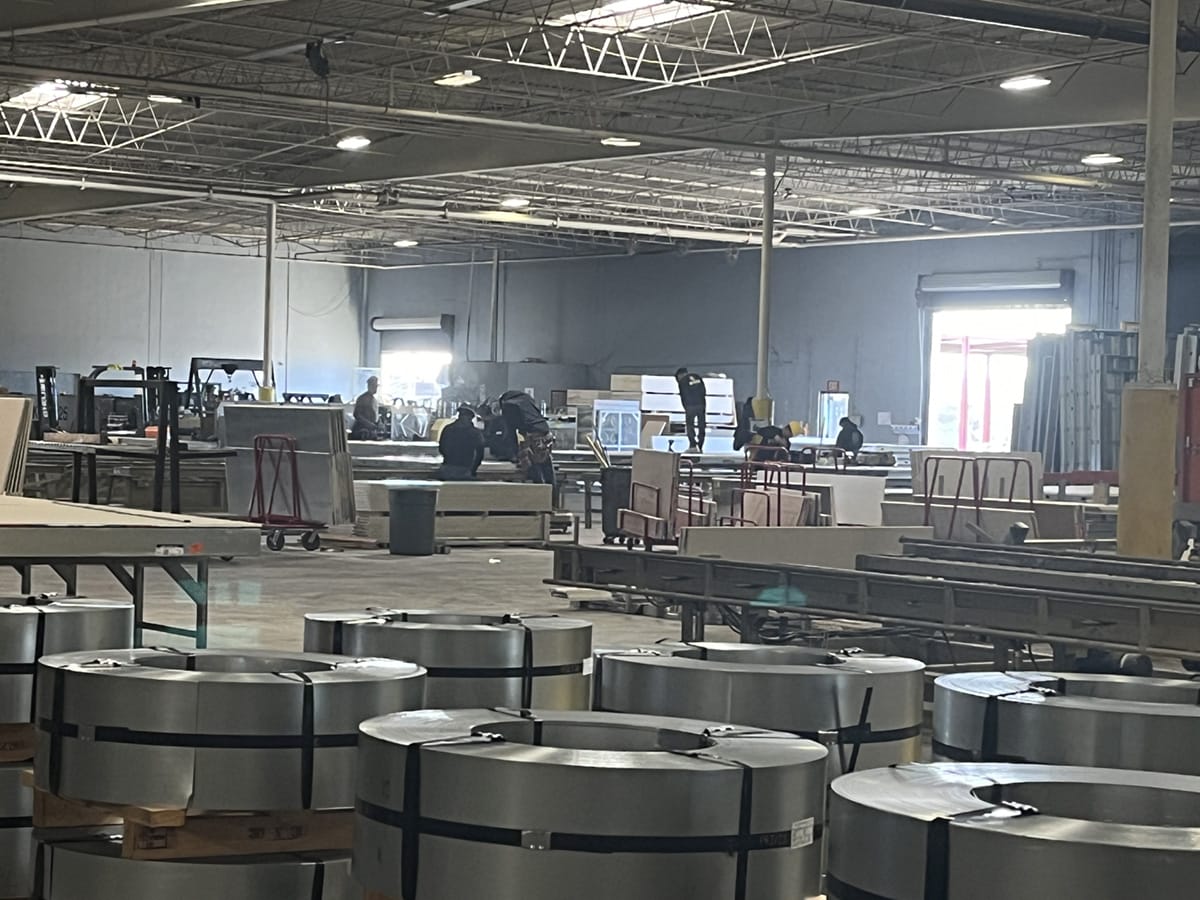
Inside the MID-RISE Modular factory and fabrication facility.
Diego adds to DeMaria’s thoughts, “I was introduced to the work of W. Edwards Deming. He was the American who assisted with the reconstruction of Japan after World War II. He said, “… without data, you’re just another person with an opinion...” This leads me to a have some strong thoughts on AI. For AI to work, you always need data. In our shop, we’ve been collecting data for the past 10 to 12 years. So, I know how to track a every facet of a carpenter’s time whether he’s using a compression table or putting number 10 screws into a 16-gauge or 20-gauge metal track. We’re taking all this data to the next generation. We’re writing an algorithm where you have three variables that you must consider. Number one is the product delivery schedule. The second is the daily quantity of resources you have in your shop, and the third, is the procurement of the materials.
These three factors are at the core of determining what panel stage takes place this week, next week and beyond – all of which is predicated on team fabrication performance. All of this is digested, and a sequencing strategy is generated to leverage our resources, to be productive and to make money. So basically, I think “data” is the secret for AI – it will not work without the data from the resources we’ve been tracking. Deming also had another good quote, “…In God we trust, all others bring the data…” So, a lot of the new shops are trusting in God, but they’re not trusting resources – most importantly data and experience. There is no substitute for knowledge, mistakes being made, and all the information that has been accumulated. Within that resource pool is data which is a benefit to all. At MID-RISE, we share that data with everyone and as we now take on 3D volumetric fabrication, we’re well prepared.
More from Modular Advantage
AI, Faster Sets, and Automation: The Future of Modular is at World of Modular
While the modular building industry has long known that it can be an effective solution to increase affordable housing, the word is slowly spreading to more mainstream audiences. Three presentations at this year’s World of Modular in Las Vegas hope to provide insight and direction for those seeking a real solution to the crisis.
An Insider’s Guide to the 2025 World of Modular
The Modular Building Institute is bringing its global World of Modular (WOM) event back to Las Vegas, and with it comes some of the industry’s best opportunities for networking, business development, and education. Over the course of the conference’s four days, there will be numerous opportunities for attendees to connect, learn, and leverage event resources to get the most out of the conference.
Affordable Housing Now: The Industry’s Best Bring New Solutions to World of Modular
While the modular building industry has long known that it can be an effective solution to increase affordable housing, the word is slowly spreading to more mainstream audiences. Three presentations at this year’s World of Modular in Las Vegas hope to provide insight and direction for those seeking a real solution to the crisis.
Opportunities for Innovation in Modular Offsite Construction
Modular Offsite Construction has already shattered the myth that it only produces uninspired, box-like designs. Architectural innovations in module geometry, configurations, materials, and products make it possible to create visually stunning buildings without sacrificing functionality or efficiency.
Safe Modular Construction with Aerofilm Air Caster Transport
In collaboration with Aerofilm Systems, Heijmans developed innovative skids using air caster technology for moving modules easily and safely. These pallets are equipped with an auto-flow system, making operation extremely simple.
Miles, Modules, and Memes: Building a Modular Network One Flight at a Time
At the end of the day, social media is just another tool for building connections, and like any other tool, needs to be used skillfully to work properly. Use social media thoughtfully, and it will open doors to real opportunities and relationships you didn’t even see coming.
Falcon Structures: Thinking Inside the Box
Some of Falcon’s latest projects include creating container solutions for New York’s Central Park and an East Coast professional baseball team. More and more, Falcon is shipping out container bathrooms and locker rooms to improve traditionally difficult work environments, like those in oil and gas or construction.
UrbanBloc—From Passion to Industry Leader
UrbanBloc specializes in three main categories or markets – what they call “Phase 0” projects, amenities, and urban infill. Clients are often attracted to shipping containers because from a real estate perspective they are considered an asset. Having the flexibility to move and transport these assets allows owners to respond to different circumstances in a fluid manner that they can’t get with standard construction.
The Hospitality Game-Changer
“Hospitality is about more than just providing a service – it’s about delivering an experience,” says Anthony Halsch, CEO of ROXBOX. “And that’s where containers thrive. They allow us to create spaces that are unique, efficient, and sustainable.”
Container Conversions Counts on Simplicity to Provide Critical Solutions
Container Conversions has fabricated and developed thousands of containers for varied projects, including rental refrigeration options, offices, kitchens, temporary workplace housing, and mobile health clinics.