Panel Built Provides Custom Modular Enclosure for Major Beverage Manufacturer
In October 2023, CE Thurston contacted Panel Built Inc., a modular building company, on behalf of a major beverage manufacturer. The manufacturer a place to house their large facility crane and a means of expanding office space within their existing plant. Panel Built Inc. was tasked with delivering a high-quality, functional structure that could meet those needs and do so quickly and efficiently.
The Challenge
The challenge was twofold. Firstly, Panel Built needed to create a spacious enclosure that could accommodate a large facility crane. This enclosure required a design that provided ample storage space and integrated seamlessly with the existing infrastructure. Secondly, the structure needed to incorporate office space that offered personnel an unimpeded, 360-degree view of the factory floor. Achieving these objectives within a stringent timeline was essential to ensure minimal disruption to the manufacturer's operations.
About Panel Built Inc.: Panel Built was founded in 1995 by brothers Pat and Mike Kiernan and began with the construction of pre-manufactured buildings. Today, Panel Built offers a complete line of custom modular offices, mezzanines, security booths, pre-assembled exterior buildings, and cleanrooms. All our product lines are manufactured on-site in one of our state-of-the-art modular production facilities. We offer "A Better Way to Create Space" for all your building projects.
The Solution
Panel Built Inc. responded to this challenge with a comprehensive modular building solution. The team designed, fabricated, and installed a 37' x 27' enclosure with a mezzanine, effectively augmenting the available space by 1,365 square feet. The enclosure featured 45 surrounding windows, which ensured panoramic visibility of the factory floor and enhanced operational oversight.
Project Timeline and Quality Assurance
Despite the project's complexity and the need for rapid completion, Panel Built Inc. completed the structure within approximately three months from the date of the order. Throughout the process, the company maintained a steadfast commitment to quality, ensuring that every aspect of the structure met high standards of craftsmanship and functionality.
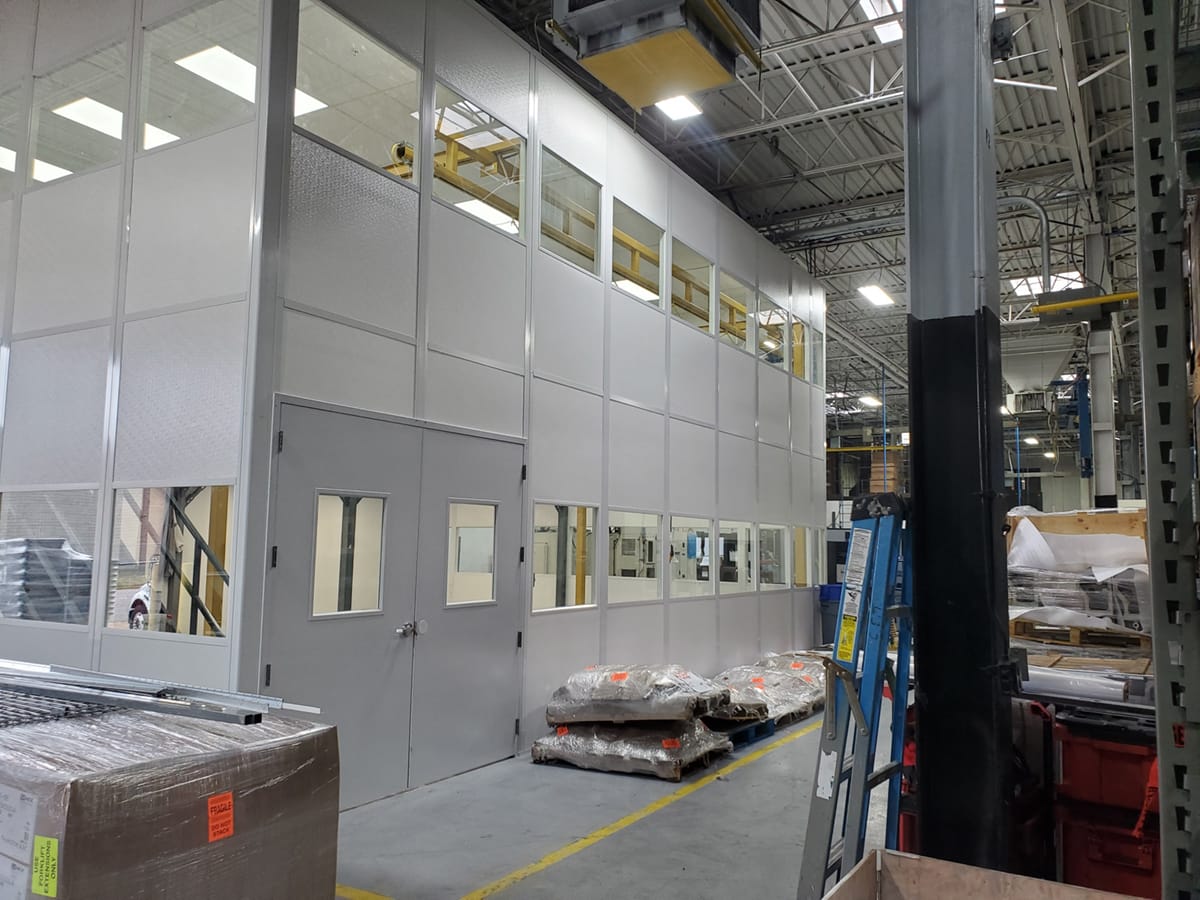
The completed modualr enclosure featured 45 surrounding windows, which ensured panoramic visibility of the factory floor and enhanced operational oversight.
Key Features of the Solution
Class A Interior Walls: The walls were crafted with 3" thick composite sandwich panels featuring 1/8" Fiberglass Reinforced Plastic on the exterior and interior surfaces, finished in pristine white. An aluminum extruded binder post system, positioned every 4', housed all electrical components, maintaining functionality and aesthetic coherence.
Ceiling: A suspended ceiling system spanning 945 square feet was implemented to integrate seamlessly with the existing structure. The Class "A" suspension system and acoustic materials enhanced the interior ambiance and provided a platform for essential utilities, including lighting, heating, ventilation, and air conditioning systems.
Doors and Windows: The building was equipped with double doors to facilitate the easy transportation of equipment. Entry points were outfitted with 20-gauge insulated steel doors featuring half-glass panels to allow natural light to penetrate the interior. The interior picture windows were glazed with 1/4" clear tempered glass, ensuring complete visibility while maintaining safety standards.
Electrical Package: The entire enclosure was pre-wired with a modular electrical package. This package included wall switches, duplex receptacles, and 110-volt LED fixtures, allowing for future HVAC installation. The modular wiring allowed for easy set-up of the building's electrical grid, saving the project time and sparing facility installers the risk of electrical injury.
Mezzanine: The mezzanine was engineered to withstand 125 pounds per square foot, meeting the standards for a loading mezzanine system. This multifunctional space accommodated storage needs and housed a dedicated in-plant office. The elevated platform featured steel decking sub-flooring and resilient recessed decking for enhanced durability.
Stair Systems & Handrails: Safety was a top priority for Panel Built Inc. As such, the 42" tall railings and diamond plate stairs were designed to meet factory, storage use groups, and OSHA standards. The stair system and handrails received a powder coat finish, with the handrails colored a bright safety yellow for optimal visibility.
Conclusion
Panel Built Inc.'s innovative approach and modular building techniques effectively solved the major beverage manufacturer's dual challenge of storage and office space expansion. This case study exemplifies the capabilities of modular construction in addressing complex industrial needs and shows Panel Built Inc.'s expertise in delivering tailored solutions that enhance operational efficiency and safety.
More from Modular Advantage
AI, Faster Sets, and Automation: The Future of Modular is at World of Modular
While the modular building industry has long known that it can be an effective solution to increase affordable housing, the word is slowly spreading to more mainstream audiences. Three presentations at this year’s World of Modular in Las Vegas hope to provide insight and direction for those seeking a real solution to the crisis.
An Insider’s Guide to the 2025 World of Modular
The Modular Building Institute is bringing its global World of Modular (WOM) event back to Las Vegas, and with it comes some of the industry’s best opportunities for networking, business development, and education. Over the course of the conference’s four days, there will be numerous opportunities for attendees to connect, learn, and leverage event resources to get the most out of the conference.
Affordable Housing Now: The Industry’s Best Bring New Solutions to World of Modular
While the modular building industry has long known that it can be an effective solution to increase affordable housing, the word is slowly spreading to more mainstream audiences. Three presentations at this year’s World of Modular in Las Vegas hope to provide insight and direction for those seeking a real solution to the crisis.
Opportunities for Innovation in Modular Offsite Construction
Modular Offsite Construction has already shattered the myth that it only produces uninspired, box-like designs. Architectural innovations in module geometry, configurations, materials, and products make it possible to create visually stunning buildings without sacrificing functionality or efficiency.
Safe Modular Construction with Aerofilm Air Caster Transport
In collaboration with Aerofilm Systems, Heijmans developed innovative skids using air caster technology for moving modules easily and safely. These pallets are equipped with an auto-flow system, making operation extremely simple.
Miles, Modules, and Memes: Building a Modular Network One Flight at a Time
At the end of the day, social media is just another tool for building connections, and like any other tool, needs to be used skillfully to work properly. Use social media thoughtfully, and it will open doors to real opportunities and relationships you didn’t even see coming.
Falcon Structures: Thinking Inside the Box
Some of Falcon’s latest projects include creating container solutions for New York’s Central Park and an East Coast professional baseball team. More and more, Falcon is shipping out container bathrooms and locker rooms to improve traditionally difficult work environments, like those in oil and gas or construction.
UrbanBloc—From Passion to Industry Leader
UrbanBloc specializes in three main categories or markets – what they call “Phase 0” projects, amenities, and urban infill. Clients are often attracted to shipping containers because from a real estate perspective they are considered an asset. Having the flexibility to move and transport these assets allows owners to respond to different circumstances in a fluid manner that they can’t get with standard construction.
The Hospitality Game-Changer
“Hospitality is about more than just providing a service – it’s about delivering an experience,” says Anthony Halsch, CEO of ROXBOX. “And that’s where containers thrive. They allow us to create spaces that are unique, efficient, and sustainable.”
Container Conversions Counts on Simplicity to Provide Critical Solutions
Container Conversions has fabricated and developed thousands of containers for varied projects, including rental refrigeration options, offices, kitchens, temporary workplace housing, and mobile health clinics.