Joshua Hart: Pushing Boundaries
Joshua Hart, P.E., vice president at Modular Solutions, can sum up his job responsibilities in one sentence: “I do whatever needs to be done.” Hart thrives on the variety and the opportunity to be involved in every aspect of the company. And it shows!
You might say Hart has come full circle.
He grew up working at Modular Solutions, the company his father, mother, and aunt started in 1996, doing odd jobs during summers and high school.
He thought it would be “cool” to run the company one day, but when it came time for college, he opted for a career path in engineering.
After graduating from Arizona State University with a degree in electrical engineering, he was hired by a small engineering firm where he received extensive mentoring. Within a few years, the company merged with WSP USA, a global engineering and professional service company. There, Hart worked with a variety of clients and many general contractors, learning different styles and approaches to construction.
“I had a great little seat to see how things are done in the construction industry through a lot of different eyes,” he says.
About five years ago, at age 29, Hart entertained the idea of starting his own firm. His father, Joe Hart, gave him another option: Come to work at Modular Solutions as vice president, learn the ropes, and run the company after he retired.
Modular Solutions, based in Phoenix, AZ, began as a small modular dealership. Today, it’s a full-service, design-build manufacturer serving Arizona, California, Utah, Nevada, New Mexico, and the greater Southwest. It produces custom modular buildings for a variety of commercial applications such as educational facilities, office buildings, and healthcare facilities.
“I never thought I’d be back,” Hart says.
But he is, and he’s immersed himself in learning the business and using his acquired knowledge to make it even better.
Full Steam Ahead
Hart isn’t afraid of hard work. Far from it. During the summer, he typically arrives at the plant around four in the morning to meet with production. By nine, he’s in the office and usually doesn’t leave until eight at night. During the school year, however, the father of seven daughters works shorter hours so he can devote more time to family.
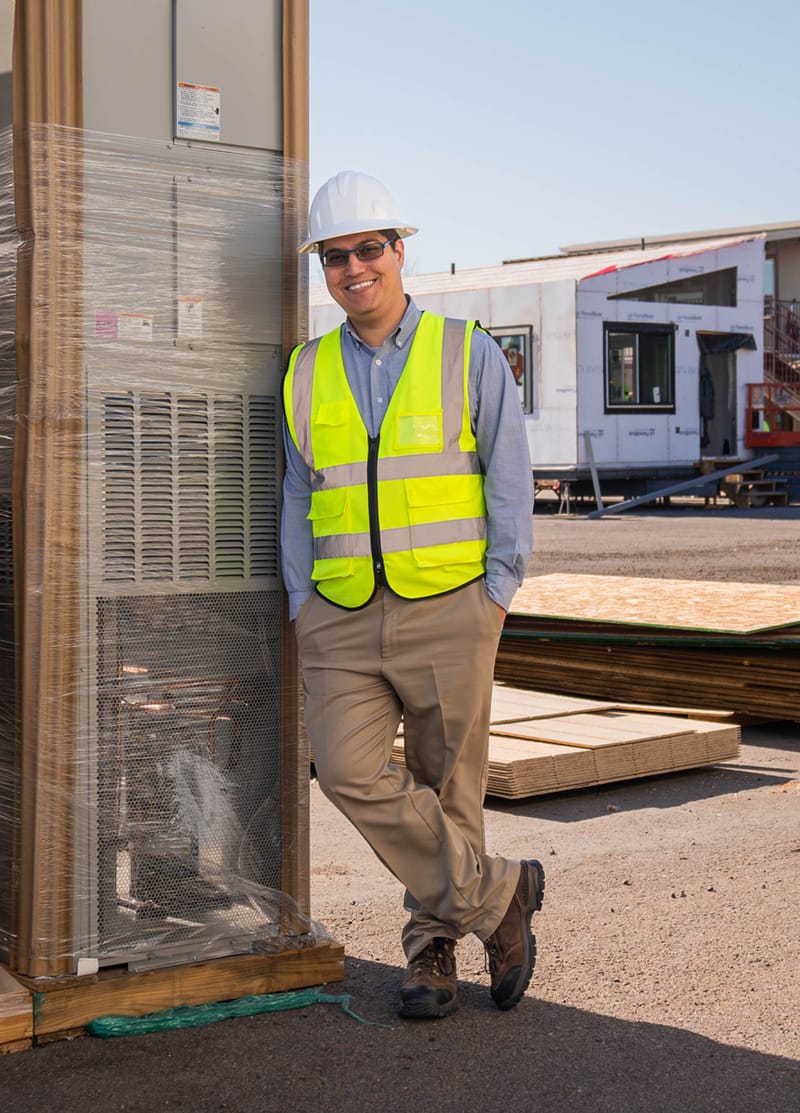
Joshua Hart is vice president at Modular Solutions in Phoenix, AZ.
He is directly responsible for the architectural engineering department, quality control, and project management. He’s also actively involved in human resources—hiring, conducting employee reviews, and, in general, ensuring employees are happy on the job.
One of the favorite parts of his job is onsite client visits. He enjoys being able to oversee a client’s project from beginning to end. At WSP USA, he worked on just a portion of many huge expensive projects.
“Our projects aren’t as big or as expensive as those, but they are very cool, different processes,” Hart says. “Some of the jobs we’ve done were thought to be close to impossible, but we figured out to do them, and do them cost effectively. I really enjoy pushing the boundaries of what modular buildings are.”
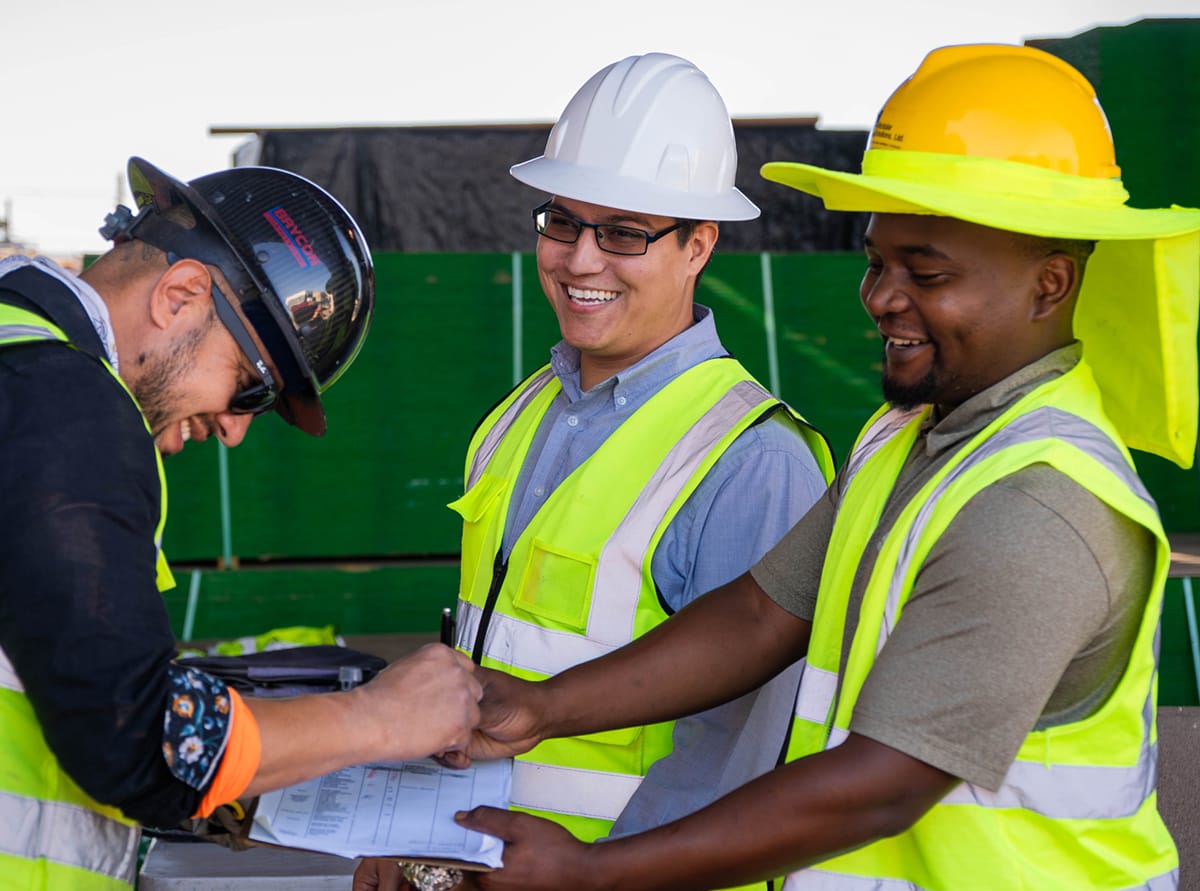
Caring Leads to Success
Modular Solution’s biggest challenge is a good one to have—acquiring enough new staff to keep up with the rapidly growing workload. Fortunately, the company has a core of experienced people who help new hires grow into their respective roles and understand the industry.
Hart attributes the company’s success to the caring exhibited by this core group who have been there from the beginning and understand the industry and how the company has evolved. They are the ones who helped Hart understand the different processes and the reasoning behind them when he returned to Modular Solutions.
It’s a two-way street.
“They have given me the trust to make changes using the different processes I’ve learned,” Hart says. “It’s a great relationship.”
Many of their kids and grandkids work at the company as well.
“It’s humbling and nice to know that we’re doing a good enough job that people want to stay her and have their family work here,” Hart says.
In fact, once the team began designing and building their sleek, modern, energy-efficient homes, it quickly overtook even their established custom-building business.
Advice to Live By
Hart has had many mentors along the way who imparted great wisdom, but one piece of advice he lives by is a saying a wrestling coach once told his dad: ‘He who hesitates is lost.’
“If you sit around and wait for answers or for something to happen, you’re pretty much done,” Hart says. “You’ve got to get out there and just do it.”
For example, in his new role, Hart must communicate with people inside and outside of the company. While he’d taken a class in school and had met with clients, contractors, and consultants in his prior workplace, he realized he needed to improve his communication skills. What did he do? He joined Toastmasters.
“It’s fantastic,” he says. “It helps tremendously with communication.”
Looking Ahead
Hart is looking forward to seeing continued growth for the company over the next few years, especially in the company’s design firm and general contractor services.
He’s also looking forward to running the company, alongside his two brothers, after his father retires. He’s already mastered the basics. Next, he’ll tackle company finances, insurance, taxes, “and all that fun stuff” in preparation for running the company.
“That’s one of the reasons why I work so hard,” he says.
Over the past fifteen to twenty years, Hart’s seen a gradual increase in the acceptance of modular construction. When he talks about modular buildings, some people still think of only manufactured homes or double classrooms. It has been challenging to change the perception of what a modular building can be, but he believes acceptance will continue to grow.
“Throughout all industries, we’ve made breakthroughs on the possibilities with and advantages of modular building,” Hart says. “I think people are starting to see that, understand that, and get excited about it.”
With people like Hart advocating for modular building and pushing the boundaries of what modular building can be, there is indeed a lot to get excited about.
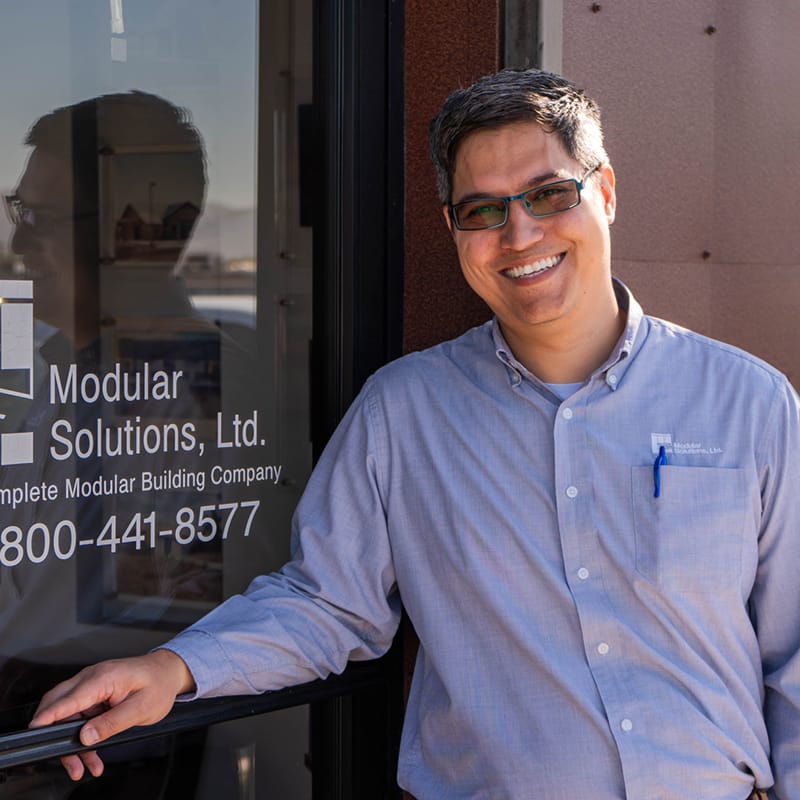
About the Author: Shari Held is an Indianapolis-based freelance writer who has been covering the construction industry for more than 20 years.
More from Modular Advantage
Oregon’s Prevailing Wage Proposal: A Wake-Up Call for Modular Construction
In early February, 2024, the Massachusetts Board of Building Regulations and Standards (BBRS) released its proposed 10th Edition building codes. This draft included several amendments targeting modular construction that would have created an extremely difficult environment for the entire modular industry and could have eliminated the industry entirely in the state.
Behind the Design of Bethany Senior Terraces, NYC’s First Modular Passive House Senior Housing Project
As more developers seek to meet new regulations for energy efficiency, the team at Murray Engineering has set a new record. With the Bethany Senior Terraces project, Murray Engineering has helped to develop NYC’s first modular structure that fully encompasses passive house principles — introducing a new era of energy efficiency in the energy-conscious city that never sleeps.
How LAMOD is Using Modular to Address Inefficiency, Sustainability, and the Future of Construction
As developers, designers, and contractors seek to understand the evolving needs of the modular industry, no one is as well-versed in the benefits of going modular as Mārcis Kreičmanis. As the co-founder and CBDO of LAMOD in Riga, Latvia, Mārcis has made it his ultimate goal to address the inefficiencies of traditional construction.
From Furniture Builder to ‘Activist Architect’: Stuart Emmons’ Unique Journey
Stuart Emmons was fascinated by buildings at a young age. He remembers building sand cities with his brother during trips to the Jersey shore. His father gave him his first drawing table at the age of ten. Today, he is an experienced architect who received his FAIA in June 2025. The road he took is unique, to say the least.
Forge Craft Architecture + Design: Codes, Contracts, and Intellectual Property
Founding Principal and Director of Modular Practice for Forge Craft Architecture + Design, Rommel Sulit, discusses the implications of codes, contracts, and intellectual property on
modular construction.
Eisa Lee, the “Bilingual” Architect
Now as the founder of XL
Architecture and Modular Design in Ontario, Canada, she applies not just her education as a traditional architect but an entire holistic view on modular design. It’s this expansive view that guides her work on being a true partner that bridges the gap between architects and modular factories as they collaborate on the design process.
Tamarack Grove Engineering: Designing for the Modular Sector
The role of a structural engineer is crucial to the success of a modular project, from initial analysis to construction administration. Tamarack Grove offers structural engineering services — project analysis, plan creation, design creation, and construction administration — for commercial, manufacturing, facilities, public services, and modular. Modular is only one market sector the company serves but it is an increasingly popular one.
Engineer Masters the Art of Listening to His Customers
Since founding Modular Structural Consultants, LLC. in 2014, Yurianto has established a steady following of modular and container-based construction clients, primarily manufacturers. His services often include providing engineering calculations, reviewing drawings, and engineering certification
Inside College Road: Engineering the Modules of One of the World’s Tallest Modular Buildings
College Road is a groundbreaking modular residential development in East Croydon, South London by offsite developer and contractor, Tide, its modular company Vision Volumetric (VV), and engineered by MJH Structural Engineers.
Design for Flow: The Overlooked Power of DfMA in Modular Construction
Unlocking higher throughput, lower costs, and fewer redesigns by aligning Lean production flow with design for manufacturing and assembly.