Jamie Metzger: From Construction to Apparel and Back Again
Growing up in a blue-collar city like Edmonton, Alberta, Canada, it’s no surprise that Jamie Metzger spent some time working labour jobs on construction sites. It’s one of the most common summer jobs in the city.
But that’s probably the last predictable thing about this particular story.
That’s because Jamie moved away, got a design degree, spent some time in the apparel industry, and then moved back to Edmonton to eventually be an instrumental force in high-end single-family modular home design and manufacture. It’s not exactly what you would think of as a typical path to a construction career.
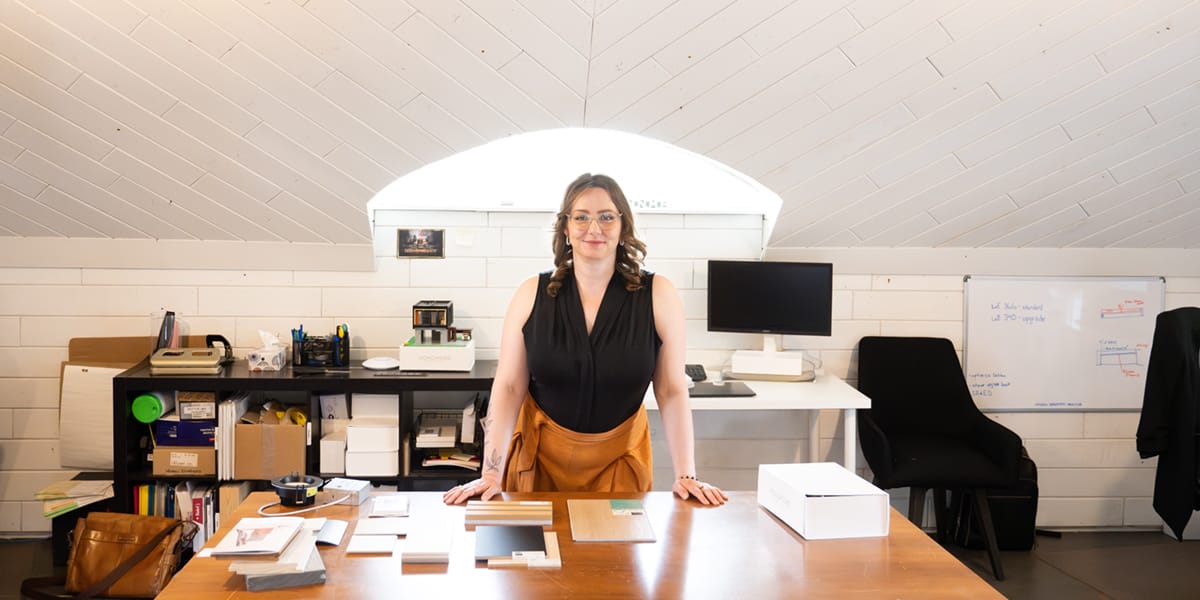
Jamie Metzger currently serves as Honomobo's director of design.
Designing a Solid Foundation
Long before Metzger landed in her current role, she moved to Toronto and completed a very intense technical design degree at Ryerson University.
After graduation, she spent some time in the apparel industry, which is about as far removed from construction as you can get.
However, it gave her experience in something that most on-site construction companies don’t do too much of. Manufacturing. More specifically, Jamie learned to create product lines, design with manufacturing in mind, and standardize concepts so they could be replicated easily.
A Return to Edmonton
After some time away from her home city, Jamie moved back to Edmonton and once again found herself back in the construction world.
This time, she started working for a custom home builder who specialized in infill housing, using her existing design skills and learning much of the homebuilding expertise she needed on the job.
Evolving to Offsite Building
Like so many companies in the modular building world, Honomobo evolved almost organically out of a need for innovative building solutions.
In this case, the company Jamie worked for recognized that there was a growing market for garage suites or ADUs. They soon realized that they could design them as modular structures, build them off-site and control and speed up the process significantly, although it would be a while before they developed their standard design range.
What they didn’t expect was the surge in demand for their high-end single-family designs for primary and secondary residences. Or that their modular business division would be in demand not only in Canada but throughout the United States, too.
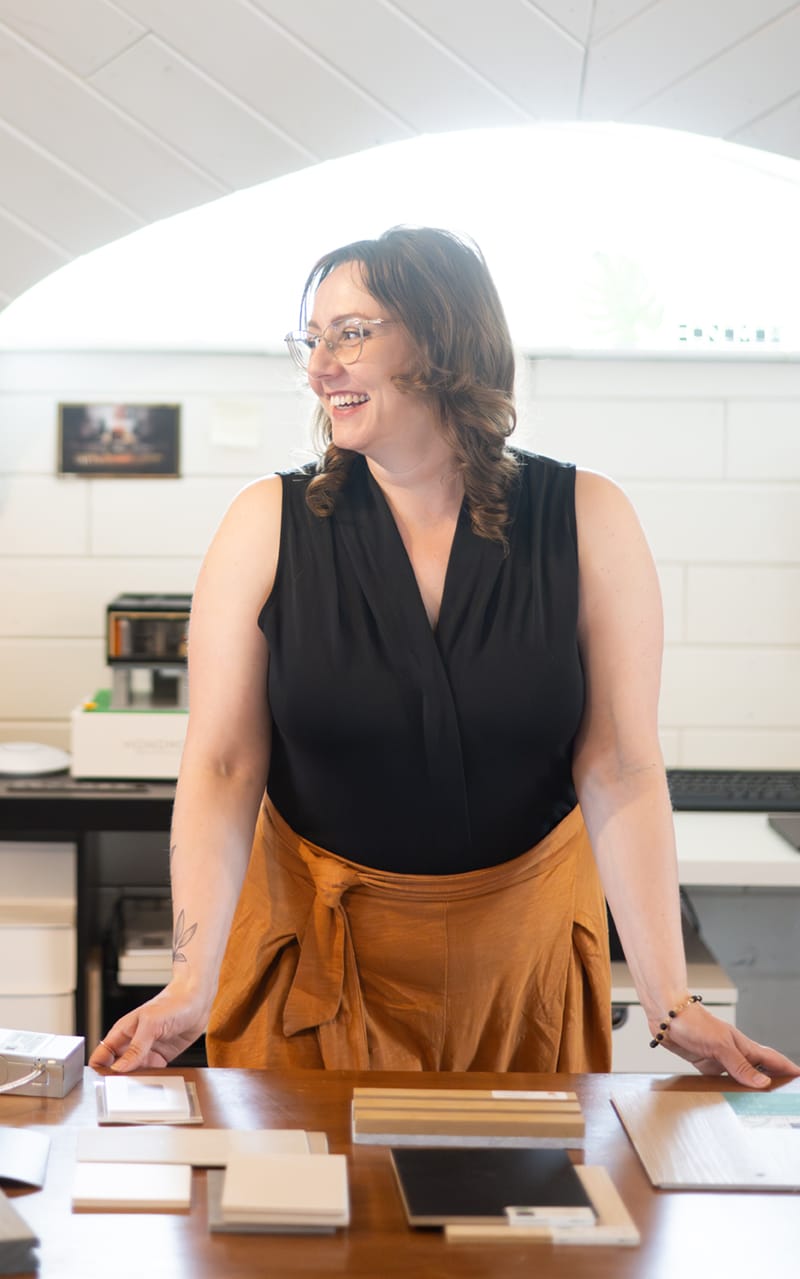
In fact, once the team began designing and building their sleek, modern, energy-efficient homes, it quickly overtook even their established custom-building business.
Committing to Modular
In 2019, when Jamie joined the team full-time, they realized that the future of their business lay in modular building. They wound down the on-site construction division of the business, and the Honomobo brand was born.
Jamie took on the role of design director, and since then, she’s been using not only her technical knowledge of design and permitting in construction but also her manufacturing knowledge to help grow and develop winning designs and the team to build them.
A Varied Work Week
Like many people who have been involved in creating a forward-thinking, boundary-pushing company like Honomobo, Jamie Metzger has her finger in more than one pie.
As design director, she oversees the full design team process and assists in new product design, prototyping, permitting and state certifications. But her role involves more than just managing a team of talented designers.
Many days, you will find Jamie on the factory floor, working directly with the people who turn those designs into tangible products. Sometimes, she’s even consulting with on-site construction crews about the planning and execution of the installation process.
It’s this kind of flexibility and the ability to connect with people across the whole modular building spectrum that has been part of Jamie’s success in the industry.
Unique Challenges and Opportunities
Working in two different countries, spread out over such a vast geographical area, comes with some unique challenges.
One is that as a company that manufactures high-end custom modular homes for clients throughout Canada and the United States, every new job site location brings unique permitting, approvals and even financing challenges.
Another is changing the perception of modular homes. However, in this case, Honomobo’s ultra-modern designs usually speak for themselves.
One challenge the company does not have that many other Edmonton home builders battle every year is the weather. Even in a city that has six months of winter, Honomobo can plan, control, and execute multiple projects all year round.
Embracing Innovation and Change
Perhaps the most surprising thing about Jamie Metzger is how well she’s made the transition from one of the world’s oldest manufacturing industries to one of the newest.
Whether it is working with remote and hybrid teams in Canada and the United States or fitting R&D into their already packed production schedule, Jamie Metzger and the team at Honomobo are surprisingly comfortable being ahead of the curve.
Digital technology (including collaborative drawing and project management tools) helps. Still, it’s the Honomobo team’s willingness to embrace them, along with new systems, innovative ideas and cutting-edge design, which is the real secret.
Or, as Jamie puts it, “Design is a process for solving problems. No matter how unexpected, there is always a solution.”
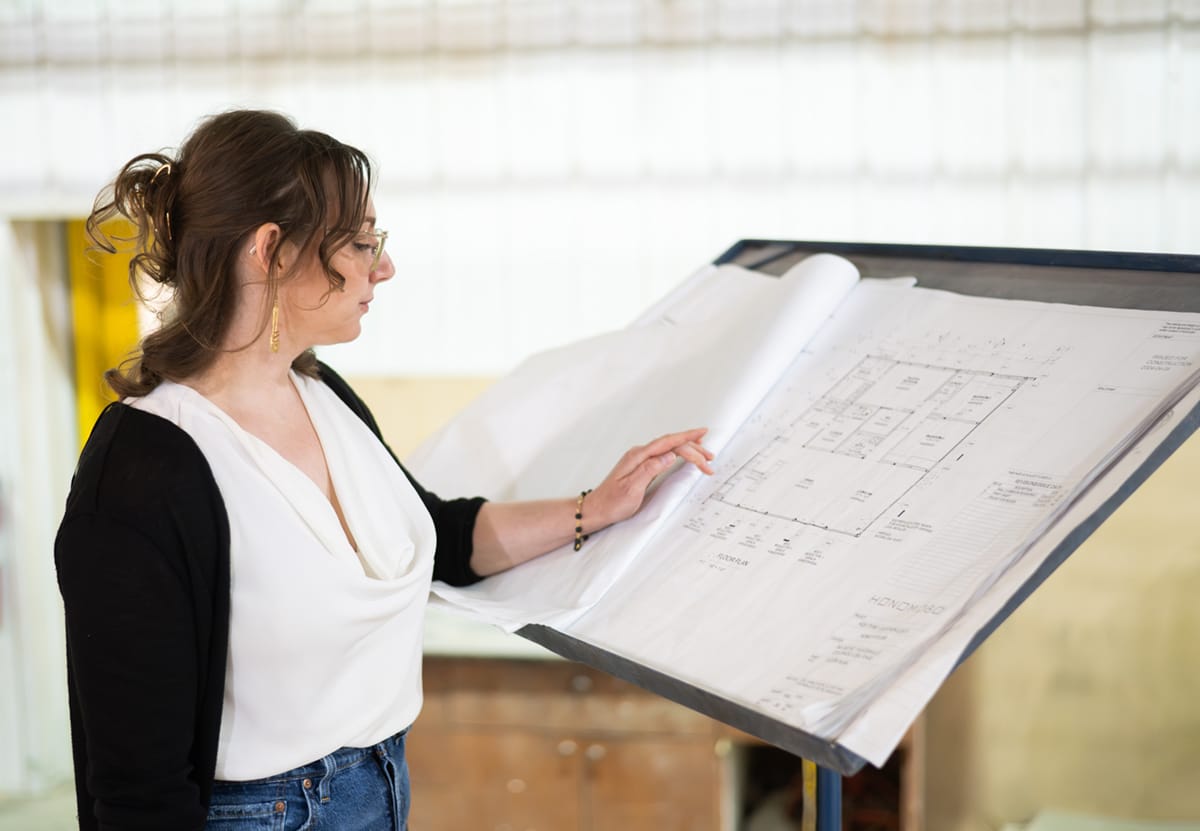
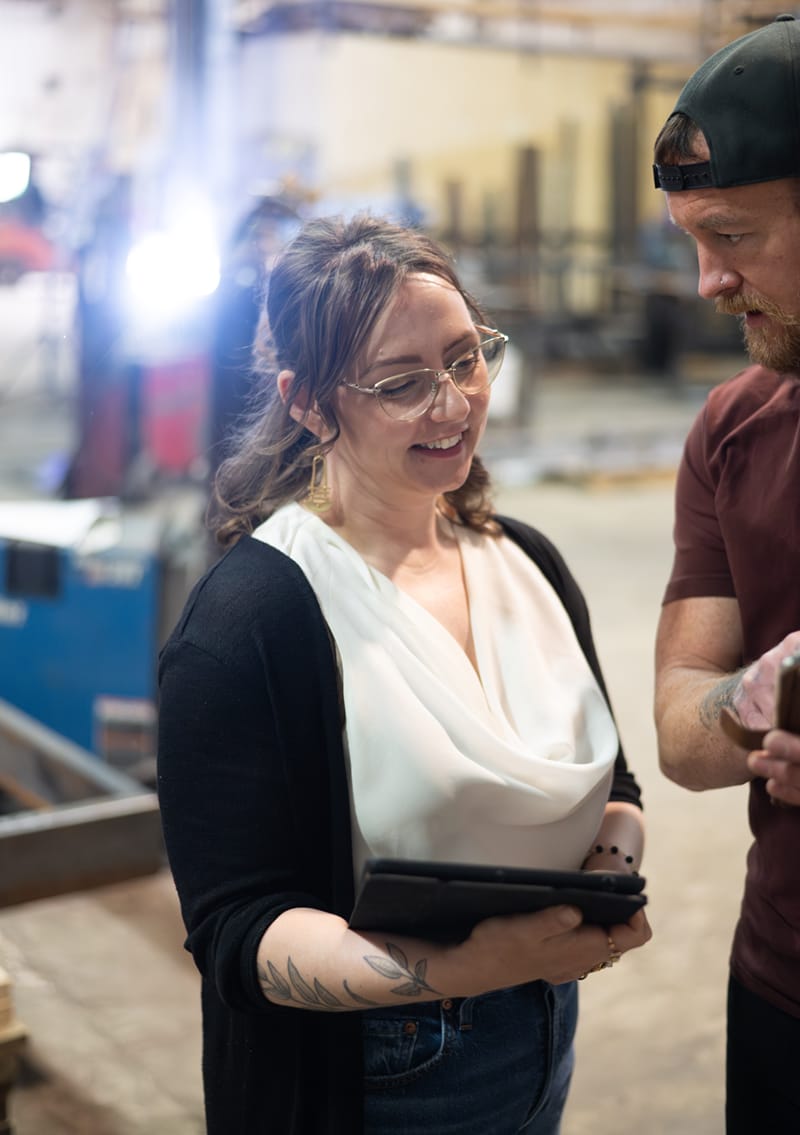
About the Author: Tamara Aspeling is a published author and freelance writer who specializes in construction and writes for print and web. She’s also a trained estimator and project manager with over 20 years of industry experience. You can reach her at www.theconstructionwriter.ca or words@theconstructionwriter.ca.
More from Modular Advantage
AI, Faster Sets, and Automation: The Future of Modular is at World of Modular
While the modular building industry has long known that it can be an effective solution to increase affordable housing, the word is slowly spreading to more mainstream audiences. Three presentations at this year’s World of Modular in Las Vegas hope to provide insight and direction for those seeking a real solution to the crisis.
An Insider’s Guide to the 2025 World of Modular
The Modular Building Institute is bringing its global World of Modular (WOM) event back to Las Vegas, and with it comes some of the industry’s best opportunities for networking, business development, and education. Over the course of the conference’s four days, there will be numerous opportunities for attendees to connect, learn, and leverage event resources to get the most out of the conference.
Affordable Housing Now: The Industry’s Best Bring New Solutions to World of Modular
While the modular building industry has long known that it can be an effective solution to increase affordable housing, the word is slowly spreading to more mainstream audiences. Three presentations at this year’s World of Modular in Las Vegas hope to provide insight and direction for those seeking a real solution to the crisis.
Opportunities for Innovation in Modular Offsite Construction
Modular Offsite Construction has already shattered the myth that it only produces uninspired, box-like designs. Architectural innovations in module geometry, configurations, materials, and products make it possible to create visually stunning buildings without sacrificing functionality or efficiency.
Safe Modular Construction with Aerofilm Air Caster Transport
In collaboration with Aerofilm Systems, Heijmans developed innovative skids using air caster technology for moving modules easily and safely. These pallets are equipped with an auto-flow system, making operation extremely simple.
Miles, Modules, and Memes: Building a Modular Network One Flight at a Time
At the end of the day, social media is just another tool for building connections, and like any other tool, needs to be used skillfully to work properly. Use social media thoughtfully, and it will open doors to real opportunities and relationships you didn’t even see coming.
Falcon Structures: Thinking Inside the Box
Some of Falcon’s latest projects include creating container solutions for New York’s Central Park and an East Coast professional baseball team. More and more, Falcon is shipping out container bathrooms and locker rooms to improve traditionally difficult work environments, like those in oil and gas or construction.
UrbanBloc—From Passion to Industry Leader
UrbanBloc specializes in three main categories or markets – what they call “Phase 0” projects, amenities, and urban infill. Clients are often attracted to shipping containers because from a real estate perspective they are considered an asset. Having the flexibility to move and transport these assets allows owners to respond to different circumstances in a fluid manner that they can’t get with standard construction.
The Hospitality Game-Changer
“Hospitality is about more than just providing a service – it’s about delivering an experience,” says Anthony Halsch, CEO of ROXBOX. “And that’s where containers thrive. They allow us to create spaces that are unique, efficient, and sustainable.”
Container Conversions Counts on Simplicity to Provide Critical Solutions
Container Conversions has fabricated and developed thousands of containers for varied projects, including rental refrigeration options, offices, kitchens, temporary workplace housing, and mobile health clinics.