To Remake North Minneapolis, Devean George Swaps Basketball For Buildings
He’s lived in Los Angeles, Dallas, and San Francisco (to name a few). He’s delivered championships with the Los Angeles Lakers and made career-defining moves with the Dallas Mavericks and the Golden State Warriors.
No matter the wins, the championships, or even the seemingly impossible 3-pointers, Devean George has always returned to where it all started for him: Minneapolis.
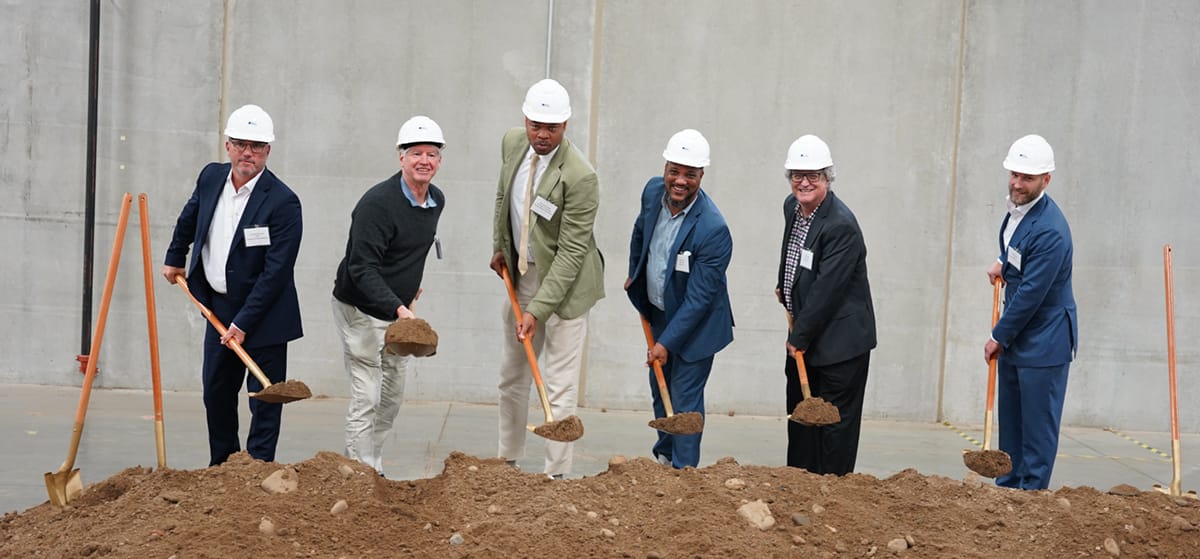
Devean George (third from left) attends the groundbreaking ceremony for his George Modular Solutions' new modular building factory in Minneapolis, MN.
George, born and raised in North Minneapolis, was an active athlete all throughout childhood, training in loads of camps throughout the region. He attended Augsburg College and from there was drafted to the NBA. He was one of the Los Angeles Lakers’ first-round draft picks—and from a Division III school at that—a rarity that reflected a history of hard work, dedication, and local investment from the Minneapolis community.
“I was able to get [into] free camps, so I’ve always been appreciative of those types of things,” he said. “Naturally when I made it to the NBA, I really wanted to help my neighborhood out.”
Giving back to Minneapolis from LA, Dallas, and San Francisco
During the summers off from the NBA, George was coming back home to Minneapolis. He first started working with a nonprofit called “Why Can’t I Go?” where he sponsored the trips of 20 star students to Disneyland and LA for a brief vacation to show them life
outside the state of Minnesota. In Dallas, he sponsored five low-income families for the holidays through Buckner International, paying for their holiday preparations, gifts, and more.
After 11 years in the NBA, George started looking at other career shifts. While many of his colleagues went either into sports punditry,
entertainment, or other places, he saw the value of real estate development. Having purchased some properties in LA, Dallas, and elsewhere, he wanted to see what he could do with his existing nonprofit “Building Blocks,” real estate, and creating new developments.
It was also a pressing need that he saw evolve over the years in Minneapolis. With his consistent trips back home over the summer and the All-Star break, George saw a gradual decrease in financial investment in his neighborhood.
“My dad still lives in the house that I grew up in. He’s been there for over 45 years,” said George. “But every year I came back, there were fewer and fewer resources being put into our community…That was really what got me going and talking to my dad. I said, ‘Hey, why don’t we start trying to get some resources put back in our community? Because I’m seeing more and more abandoned buildings, more and more vacant buildings, more and more vacant homes.”
George saw an opportunity to address the lack of equitable community development and also provide jobs for those who still lived in the area.
“How do I help my community with my nonprofit?” he asked. “I kind of combined that question with a business one so I can help my community with rebuilding it and also help my community with providing the permanent jobs that’s needed.”
He answered both queries with one business idea: modular manufacturing.
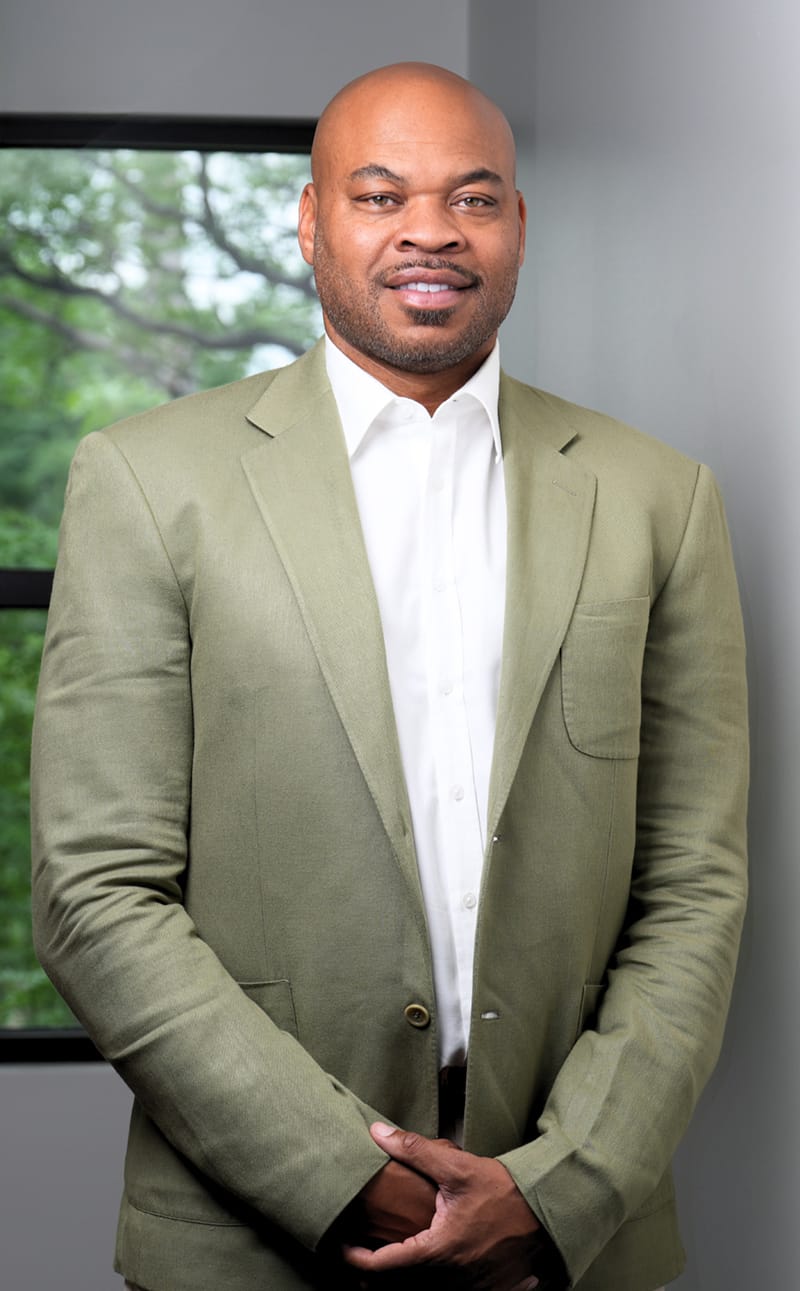
Investing in North Minneapolis with Modular
This wasn’t George’s first foray into real estate, as he’s built and developed projects aimed at providing affordable housing. When addressing issues as widespread and systemic related to housing shortages and affordable residences, he had to take certain things into consideration to ensure the viability and resilience of his developments.
“In our region where there are climate issues, there are extra costs in the winter, as well as road restrictions where you can’t have heavy machinery moving at times,” said George. “It’s just a lot of hoop jumping that you have to do in a cold weather climate.”
Alongside his previous work as a local speaker, he also heard from other former basketball professionals doing social work or afterschool programs, which echoed the demand he saw for more housing options. A lot of children who attended these programs or families who worked with social services often talked about the lack of stable housing. George heard this over and over again.
“Being from North Minneapolis, I knew where I was staying at every night,” he said. “I wasn’t staying at different homes or bouncing around. I was at my house every day. I knew we had stable housing. I wanted to really tackle that issue with the affordable housing projects to create that stable housing. So that’s kind of how I got started.”
George cited three positives that made modular the natural choice: predictability, speed, and being able to build year-round. All these help to answer the more pressing issue on his mind.
“[With] the housing shortage throughout the nation, especially in our region, there’s no way we can just do stick-built,” he said. “There’s no way.”
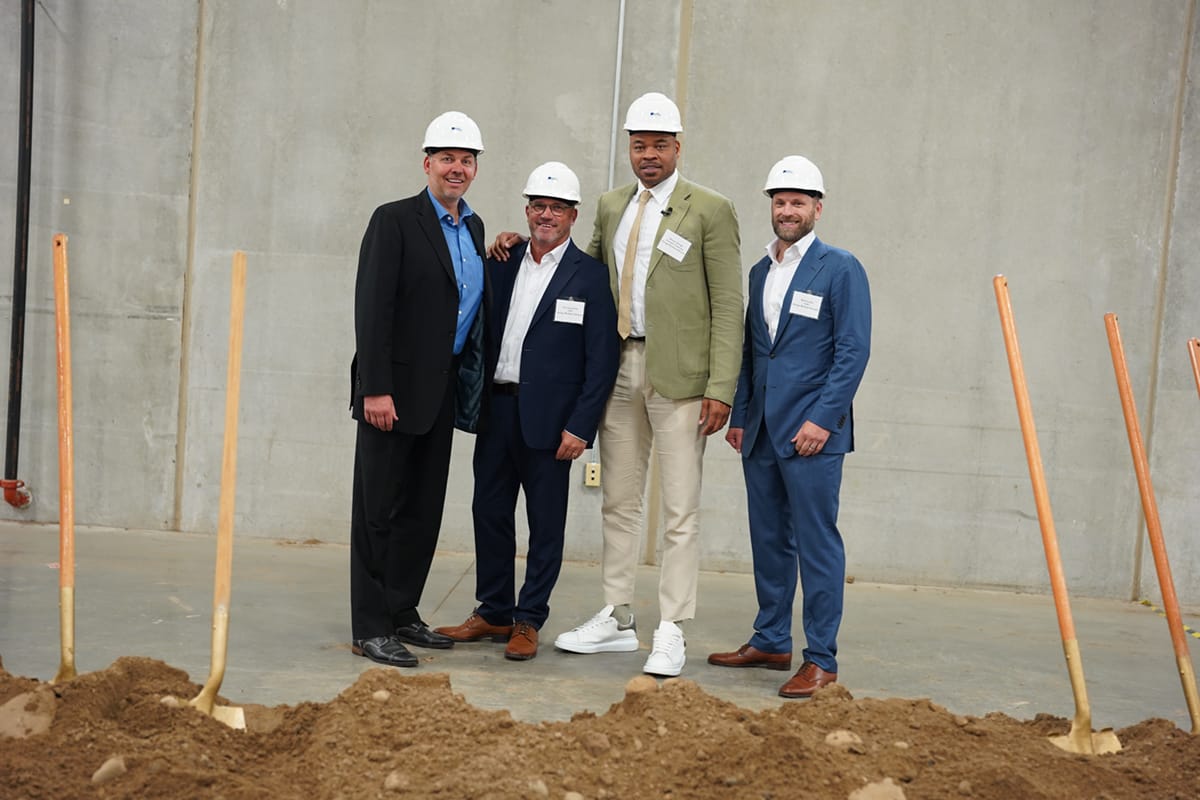
Devean George and his executive team at George Modular Solutions.
A Modular Education for Complete Business Innovation
With the decision to go fully modular, George needed to find executives and mentors that shared his vision and desire to move forward.
One of his earliest contacts was Archie Givens, a mentor that George said, “showed me the process and handed me the consultants that I need to help me with the process I was going through.”
Consultants pointed him to relevant literature, as well as attending valuable seminars and conferences. However, it wasn’t just related to modular construction, as the focus on affordable housing meant understanding how federal and state subsidies and grants would apply to modular developments.
Currently George Modular Solutions has four employees, including himself, CEO Lewis Lockwood, and COO Will Gorrilla. They are starting with two developments in Minneapolis, an 83-unit property and a 190-unit complex. They are planning to grow to seven employees once construction starts, with the aim of expanding to over 100 employees within the first year.
The number of employees will help, as George has also purchased a modular factory to make everything quickly and in-house.
“I now have a modular plant, not just for me, but for a need throughout,” said George. “This is just not a Devean need or a George Group North need. This is a need from city to city.”
As the business continues to establish itself in the space, George looks to expand his project options with the factory, not just in terms of project types but also locations. He is also innovating within the modular industry itself, creating new types of modular design using light-gauge steel.
“We’ll be working with hotels, we’ll be working with hospitals, we’ll be working with both the market rate and affordable developers, people looking for office buildings,” he said. George also mentioned a stated interest from developers in California and in other states, giving the company a series of potential business partnerships to nurture over the years.
Keeping a Company Grounded While Seeking Growth
While the business goals are realistic for George Modular Solutions, they’re not the main goals. In going back to Minneapolis for George, he is looking for practical ways to infuse the community with vibrant growth and to inject much-needed stability and economic development.
With his company, George is looking to train people to keep them in-house, providing a stable paycheck. With the two upcoming developments, he is hoping to provide houses for those who are seeking stable housing—offering a solid foundation for the growth of Minneapolis.
“We’re going to have a great environment to come in and work,” he said. “That’s been one of the things that I’ve been most proud of too, of building my business in our community, [because] people see that there’s a cause to it. People see that there’s a reason for it, so I want to build that culture.”
There’s a lot of hope for the business, but it comes with a certain amount of challenges as well. Chief among these challenges is the education hurdle for funders, city officials, and business partners, said George, as they are typically unaware of what modular construction can entail and how different it can be from stick-built construction.
“It’s hard, but I would say that’s kind of my comfort zone of tackling difficult projects,” said George. “So this is kind of right in my wheelhouse.”
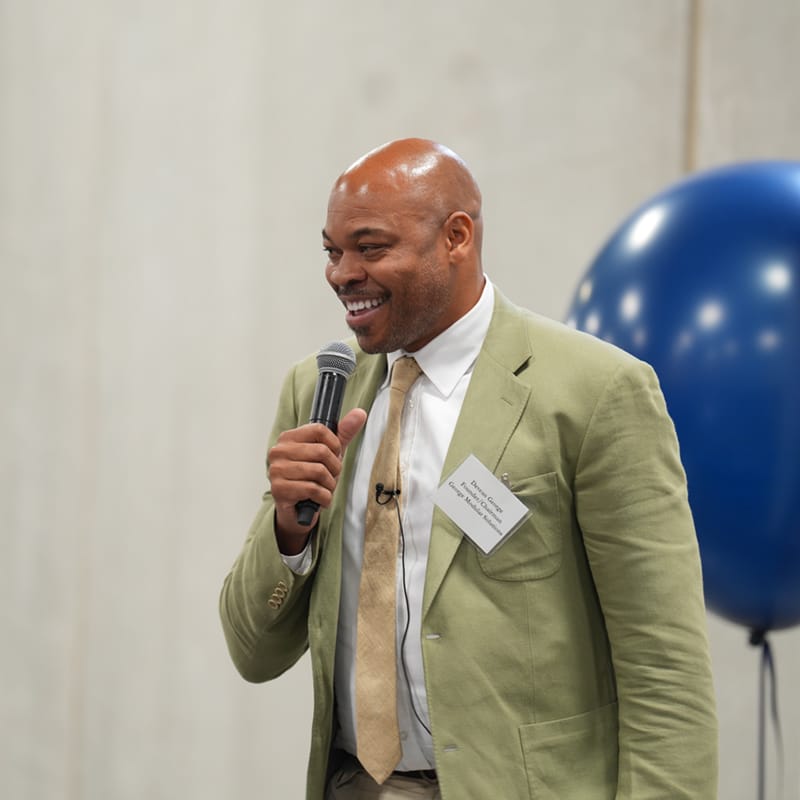
No Matter if it’s Basketball or Business, it’s All About the People
As the saying goes, you are only as strong as your weakest link. For George, he takes that to heart both on the court and in business.
Athletes are known for their dedication and discipline to the craft, but they also know the value of teamwork.
“Even if I am the head of the company, I have to know what I’m good at and what I’m not good at, and make sure I get the right people,” said George. “I don’t have a problem saying, ‘I don’t understand.’ I don’t have a problem with asking a question. I don’t have a problem with saying I’m not really good at that. It’s okay. But I am good at finding the right people to get those things done.”
George cares deeply about retaining a positive reputation, as all businesses want to be seen as credible and reliable. However, he also understands the value of healthy risk—something that’s come natural to him as an athlete.
“I don’t second guess myself,” he said. “Everything doesn’t have to be perfect. I’m a person that takes action. I really do a lot of due diligence, [but] once that’s done, I can care less about the little stuff. I’ll just figure it out and make it happen. So that’s why I’ve been successful. I think I just don’t have fear.”
In combining fearlessness and teamwork, George is looking to set up George Modular Solutions to fulfill its mission of giving back to the community that raised him. The modular plant that he recently purchased happened to be across the street from another older plant where most of the community’s older residents used to work.
“My mother, my architect’s mother, and [State] Senator Bobby Joe Champion’s mother, they all worked there in that plant,” said George. “And that’s the story that we’re telling is that we want to give somebody else a chance from the community. We want to build that unity that we’ve had in the past through this, and we want to be on the other side and say, ‘Hey, we’ve paid it forward and now our plant has produced the next senator.’”
About the Author: Karen P. Rivera is a freelance writer and editor with a passion for storytelling. She is a former United Nations-based reporter, with experience covering international breaking news, venture capital, emerging healthcare tech, and the video game industry.
More from Modular Advantage
AI, Faster Sets, and Automation: The Future of Modular is at World of Modular
While the modular building industry has long known that it can be an effective solution to increase affordable housing, the word is slowly spreading to more mainstream audiences. Three presentations at this year’s World of Modular in Las Vegas hope to provide insight and direction for those seeking a real solution to the crisis.
An Insider’s Guide to the 2025 World of Modular
The Modular Building Institute is bringing its global World of Modular (WOM) event back to Las Vegas, and with it comes some of the industry’s best opportunities for networking, business development, and education. Over the course of the conference’s four days, there will be numerous opportunities for attendees to connect, learn, and leverage event resources to get the most out of the conference.
Affordable Housing Now: The Industry’s Best Bring New Solutions to World of Modular
While the modular building industry has long known that it can be an effective solution to increase affordable housing, the word is slowly spreading to more mainstream audiences. Three presentations at this year’s World of Modular in Las Vegas hope to provide insight and direction for those seeking a real solution to the crisis.
Opportunities for Innovation in Modular Offsite Construction
Modular Offsite Construction has already shattered the myth that it only produces uninspired, box-like designs. Architectural innovations in module geometry, configurations, materials, and products make it possible to create visually stunning buildings without sacrificing functionality or efficiency.
Safe Modular Construction with Aerofilm Air Caster Transport
In collaboration with Aerofilm Systems, Heijmans developed innovative skids using air caster technology for moving modules easily and safely. These pallets are equipped with an auto-flow system, making operation extremely simple.
Miles, Modules, and Memes: Building a Modular Network One Flight at a Time
At the end of the day, social media is just another tool for building connections, and like any other tool, needs to be used skillfully to work properly. Use social media thoughtfully, and it will open doors to real opportunities and relationships you didn’t even see coming.
Falcon Structures: Thinking Inside the Box
Some of Falcon’s latest projects include creating container solutions for New York’s Central Park and an East Coast professional baseball team. More and more, Falcon is shipping out container bathrooms and locker rooms to improve traditionally difficult work environments, like those in oil and gas or construction.
UrbanBloc—From Passion to Industry Leader
UrbanBloc specializes in three main categories or markets – what they call “Phase 0” projects, amenities, and urban infill. Clients are often attracted to shipping containers because from a real estate perspective they are considered an asset. Having the flexibility to move and transport these assets allows owners to respond to different circumstances in a fluid manner that they can’t get with standard construction.
The Hospitality Game-Changer
“Hospitality is about more than just providing a service – it’s about delivering an experience,” says Anthony Halsch, CEO of ROXBOX. “And that’s where containers thrive. They allow us to create spaces that are unique, efficient, and sustainable.”
Container Conversions Counts on Simplicity to Provide Critical Solutions
Container Conversions has fabricated and developed thousands of containers for varied projects, including rental refrigeration options, offices, kitchens, temporary workplace housing, and mobile health clinics.