How to Fail at Delivering a Modular Project
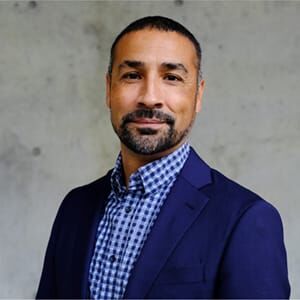
Nick Gomez is the Principal-Director of Modular Design and Construction at AO.
Top ten lists are everywhere. It is a simple way of taking vast information and distilling it into 10 simple bullet points. While the list can often be subjective, the aim is to help you further explore a subject in depth. Most lists are about things to do or see, but I have decided to look at the repetitive mistakes people make that can derail a modular project.
A client of mine put it best, “I’m hiring you for your expertise as you know what to do, but I’m also aware you have made mistakes on other projects and know how to avoid making them again.”
I’m a firm believer that we learn from both our successes and failures. Success can involve challenges, but it often provides valuable experiences that can be replicated in future endeavors. Failures can be categorized into two types: those that transform into successes through perseverance, and those that are resolved during the project but serve as valuable lessons to avoid in the future. Here are a few to avoid on your next project:
1. Converting a site-built project that’s already been entitled to modular construction.
This may seem like common sense, but this is one of the most common mistakes developers make. While I have converted projects and successfully delivered them, most of the studies don’t work or would require significant redesign.
Modular buildings are taller, with double-floor ceiling assemblies. Converting would mean compromising ceiling heights or having to go back to planning for a height adjustment. Trying to adhere to the entitled design, factories sometimes accept inefficiencies that can slow or impact production schedules.
You can avoid this mess and start with a project that is “modular possible”, adhering to the design parameters and layout required. It Is infinitely easier to de-modularize a plan than it is to try and modularize a site-built layout. Removing the double floor assemblies and walls within units takes time, but it is not a total re-design. In my experience, I’ve never heard of a planning agency or neighbor complaining that you are making your building 5’ shorter.
2. Onboarding a factory too late.
The best practice is to start a project with a factory onboard. This allows the team to design a project that is optimized to fit the production capabilities of the factory. Modular projects require more upfront coordination between the A & E team and the factory. Having a factory on board late means rework, or compromise to the plans. Having them onboard early allows for early input on the layout, ensuring a plan optimized for their production.
I tell my clients that we must put pencils down at 20% DD if a factory is not onboard. Not only do the drawings need to reflect accurately the scope of work between the site and factory, but also incorporate the proprietary detailing of the factory that can have impacts on plans and sections. People like to complain about the proprietary and preferred detailing that is factory specific. If you tour factories and see how they are slightly different, the details help them build more efficiently for their scope. Get a factory onboard as early as possible. Avoid rework in the plans and design. Collaborate with the factory and A&E team to optimize the plan for factory production.
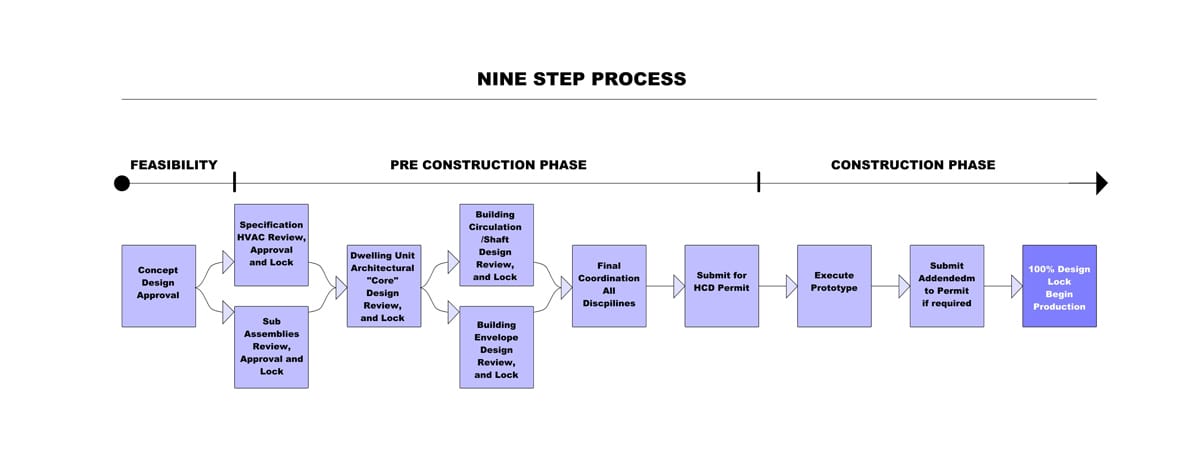
A defined workflow for modular preconstruction and design is critical for project success.
3. Forcing inefficiencies into a modular scope.
This isn’t going to derail your project, but you want to avoid this as much as possible. If you start with a modular design that is tailored to the factory you are working with, you can avoid this.
When you take a stick-built design and force it to be modular, sometimes the factory makes compromises that require additional site work or can impact their production schedule. Tracking factory versus site scope on the resume of work is critical for the team, as that is where things get missed and coordination can fall through the cracks.
4. Selecting separate site and modular consultants.
Modular projects require a high level of coordination between the Factory and Site scope to be successful. With some factories, it is common to have a set of MEP and S engineers that works on the factory side for permitting, shop drawings, and fabrication and a separate set of MEP and S consultants for the site foundation/podium work. The more information that changes hands, the more opportunity for scope gaps and uncoordinated items to occur.
While factory work contractually ends with the production and shipping of modules, there are critical hands-offs if using separate site and factory consultants, for site utility tie-in and structural connections. For any project to be successful, it must be thought of holistically, from design to construction. With modular, the dual permitting and construction processes require more attention and coordination.
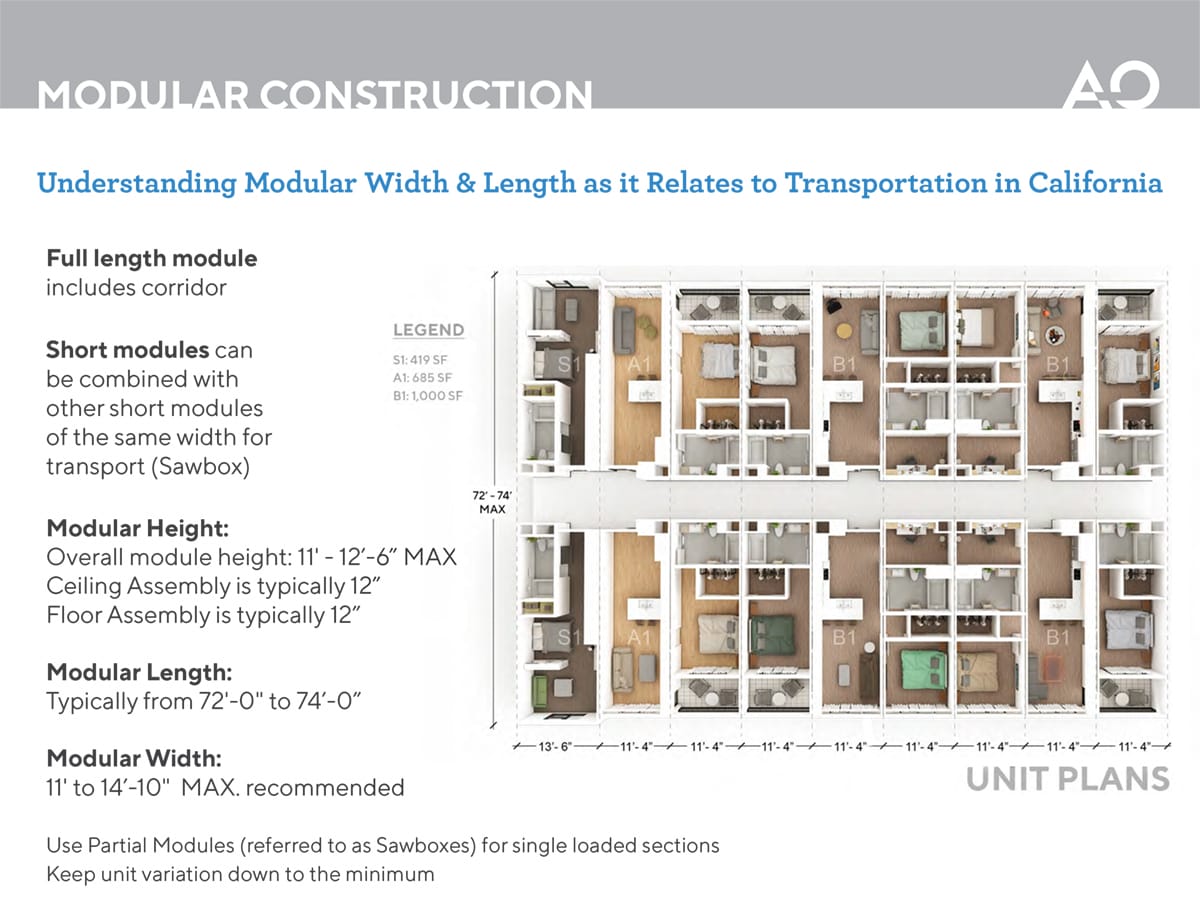
5. Not hiring experienced consultants and contractors to execute the project.
If it’s your first or second project, surround yourself with people who have the experience, understand the process, and know the critical path items. As Larry Pace at Factory OS said, “You want to avoid paying the dumb tax that first time around.”
With modular projects, things are front-loaded for the factory build and are out of sequence if compared to conventional build. Not knowing these items can quickly diminish any time savings you had achieved from building off-site while preparing the site foundations.
I have talked to a fair share of owner-builders looking at using modular construction, who want to learn by doing their first project. I always tell them “Get a good set crew, and you are halfway there.” I also let them know they will probably not get any schedule or cost savings the first time around, but they should hopefully learn enough to do better on the second and third jobs. I also recommend some of the consultants out there who can help a new team along the way to avoid “paying the dumb tax” as much as possible.
6. Not respecting the factory design lock and making late changes.
This is something I make sure owners who have never done a modular project know. We make any changes needed during the extensive shop drawing review and not during the prototype sign-off.
With site-built construction, owners and their reps do not pay attention to casework and finishes until the submittals come out in the middle of construction. With modular, the sitework has not even started and we need a sign-off for procurement. The design lock and review must be done by the decision makers and must not be overlooked.
I once had an owner who requested late changes during prototype sign-off. This resulted in a factory change order and schedule delay to incorporate. All could have been avoided if the correct team had looked at the shop drawings and finished schedule submittals.
7. Not educating the local AHJ on the factory’s party review process.
Every municipality is a little different, but it is never a wasted effort to educate the local AHJ about both their role and HCDs (California-specific) in the review and approval process. My preference is to have the factory initiate a meeting that has a factory representative, HCD representative, third-party agency, and A&E team to go over rules and responsibilities.
HCD can explain regulatory rules governing offsite construction. This is important, as the locals can sometimes misunderstand their role and try and review and comment on items beyond their jurisdiction.
The third-party agency can explain their document review (DAA = Permit) and the quality assurance review (QAA = Factory inspections). Clarifying how permitting and inspections are done helps the local understand the process happening outside their review.
Even if you have completed modular projects in a city, you may need to still have a meeting, as you may be getting a reviewer who has not dealt with a project using offsite construction. If you are hosting these meetings, please request that the city identify possible reviewers if the project has not been assigned. I had a comprehensive meeting with the city, which only allocated department heads to attend. When it came time for the actual review, some of the department heads had transferred and we were dealing with plan reviewers who did not understand the process.
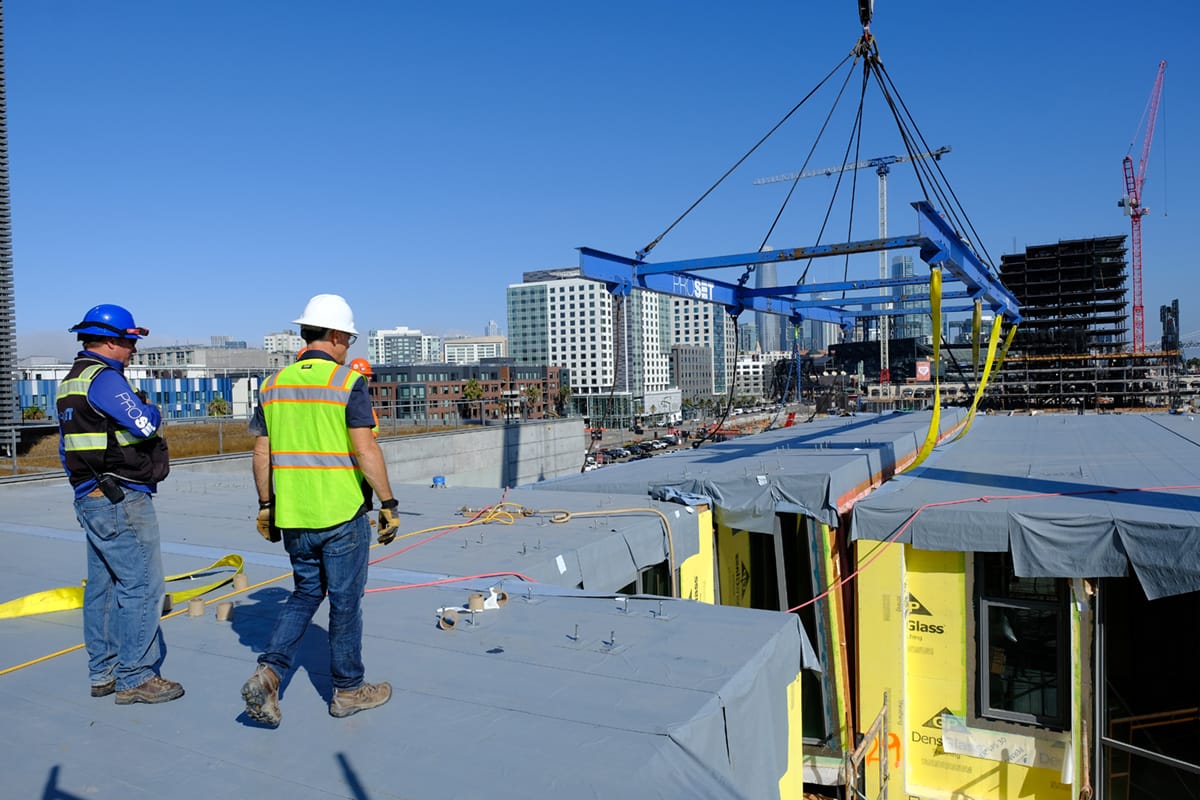
A set crew places part of a volumetric modular building.
8. Lack of clear drawings defining factory and site scope.
I have 3 words for you: Resume of Work!
This is not just a document that explains factory scope and responsibilities, but also helps communicate what is out of their scope and requires Local AHJ review and approval. It is the road map for the scope included in both the Factory and Local Site sets. This is one of the reasons why we want a factory onboard as early as possible to define the scope and negotiate the resume of work.
It does take a little extra work to produce drawings, but being clear, noting plans and details, and graphically showing factory vs site scope helps reviewers know what they should be looking at and what is out of their review. Avoiding confusion will hopefully avoid unnecessary plan check comments. Factories that manage their state sets, and AORs who do both, have developed graphic language in their plans to clearly communicate the scope.
9. Exposing the modular building to elements before the exterior envelope is sealed.
First, this is not just a modular problem, site-built structures are also susceptible to water damage during construction. The site-built process is to build the superstructure, and the roof, enclosing the building before starting interior finishing. Modular offsite construction has finished modules being stacked as the structure rises, which are vulnerable to the weather while being installed.
We have all heard horror stories about projects that were not weatherproofed properly, and a fluke rainstorm caused damage to mods. Many more projects have been erected without issue. Contractors are getting better at putting belt and suspender methods in place to protect these structures at the most vulnerable times. Some have even worked with envelope consultants to develop their construction sequence methods.
It’s an additional cost to the project for the added layer of protection, but water damage would not be just a financial cost to the project for repair, but also a costly schedule impact for the schedule. Don’t even get me started on the confusion of the local AHJ on what the role is for the in-kind repairs.
Let’s avoid this, get a game plan with the install team, reach out to a consultant if needed, and protect those modular buildings from weather damage during site construction.
10. Blaming every construction issue on modular.
Seems like every time someone has an issue with modular construction, because of a past project, they want to blame everything on it. Yes, I am a proponent of offsite construction and will be quick to point out that similar issues happen on conventional build projects.
Yes, the process is different, and I make the point all the time, but if you don’t respect the process, and adhere to critical items and coordination noted above, it’s not the modular technology’s fault but the team’s. Blaming modular technology without addressing underlying coordination and process issues is counterproductive.
So please start modular and optimize your design for the factory you will bring on board early. Collaborate on all upfront critical design and decisions that need to be made, and lastly, always protect the structure during site assembly.
As an advocate for modular, I want to see it grow and wish you success on your next modular project. Successful modular projects require early factory involvement, clear communication, and meticulous planning. By addressing these key points, you can optimize your project for success in this burgeoning industry.
More from Modular Advantage
Oregon’s Prevailing Wage Proposal: A Wake-Up Call for Modular Construction
In early February, 2024, the Massachusetts Board of Building Regulations and Standards (BBRS) released its proposed 10th Edition building codes. This draft included several amendments targeting modular construction that would have created an extremely difficult environment for the entire modular industry and could have eliminated the industry entirely in the state.
Behind the Design of Bethany Senior Terraces, NYC’s First Modular Passive House Senior Housing Project
As more developers seek to meet new regulations for energy efficiency, the team at Murray Engineering has set a new record. With the Bethany Senior Terraces project, Murray Engineering has helped to develop NYC’s first modular structure that fully encompasses passive house principles — introducing a new era of energy efficiency in the energy-conscious city that never sleeps.
How LAMOD is Using Modular to Address Inefficiency, Sustainability, and the Future of Construction
As developers, designers, and contractors seek to understand the evolving needs of the modular industry, no one is as well-versed in the benefits of going modular as Mārcis Kreičmanis. As the co-founder and CBDO of LAMOD in Riga, Latvia, Mārcis has made it his ultimate goal to address the inefficiencies of traditional construction.
From Furniture Builder to ‘Activist Architect’: Stuart Emmons’ Unique Journey
Stuart Emmons was fascinated by buildings at a young age. He remembers building sand cities with his brother during trips to the Jersey shore. His father gave him his first drawing table at the age of ten. Today, he is an experienced architect who received his FAIA in June 2025. The road he took is unique, to say the least.
Forge Craft Architecture + Design: Codes, Contracts, and Intellectual Property
Founding Principal and Director of Modular Practice for Forge Craft Architecture + Design, Rommel Sulit, discusses the implications of codes, contracts, and intellectual property on
modular construction.
Eisa Lee, the “Bilingual” Architect
Now as the founder of XL
Architecture and Modular Design in Ontario, Canada, she applies not just her education as a traditional architect but an entire holistic view on modular design. It’s this expansive view that guides her work on being a true partner that bridges the gap between architects and modular factories as they collaborate on the design process.
Tamarack Grove Engineering: Designing for the Modular Sector
The role of a structural engineer is crucial to the success of a modular project, from initial analysis to construction administration. Tamarack Grove offers structural engineering services — project analysis, plan creation, design creation, and construction administration — for commercial, manufacturing, facilities, public services, and modular. Modular is only one market sector the company serves but it is an increasingly popular one.
Engineer Masters the Art of Listening to His Customers
Since founding Modular Structural Consultants, LLC. in 2014, Yurianto has established a steady following of modular and container-based construction clients, primarily manufacturers. His services often include providing engineering calculations, reviewing drawings, and engineering certification
Inside College Road: Engineering the Modules of One of the World’s Tallest Modular Buildings
College Road is a groundbreaking modular residential development in East Croydon, South London by offsite developer and contractor, Tide, its modular company Vision Volumetric (VV), and engineered by MJH Structural Engineers.
Design for Flow: The Overlooked Power of DfMA in Modular Construction
Unlocking higher throughput, lower costs, and fewer redesigns by aligning Lean production flow with design for manufacturing and assembly.