Fire Station 67
Built for offsite fabrication and rapid assembly, Fire Station 67 has a future that can reinvent itself.
Fire Station 67 is designed in direct response to the climate crisis, the increasing threat of wildfires, and the needs to the Rancho Mission Viejo community. Prefabricated off-site and assembled from 10 modules, the 4,667-square-foot fire station is a modular design with the ability to reconfigure the structure into something new in the future.
The rapidly deployable steel cubes are designed for re-use, speed, and resilience. The prefab structure is clad in fireproof, corrugated steel siding. Technology and rapid manufacturing are leveraged to maximize construction speed and efficiency.
Location: Rancho Mission Viejo, California
Project Team
Architect: Wittman Estes
Builder: Xtreme Cubes
Prefabricated System: Wittman Estes in collaboration with 2G3R
Interior Design: Birsel+Seck
Landscape Architect: Land Concern
Civil Engineer: Fuscoe Engineering
Clients: 2G3R (Ana Maria Pinto da Silva), Orange County Fire Authority, Rancho Mission Viejo
Wittman Estes Design Team
Matt Wittman
Brandon Patterson
Julia Frost
A Connection to History and Place
Fire Station 67 sits on Cow Camp Road, next to Rancho Mission Viejo’s (RMV) ranching operations.
Originally spanning from the Pacific Ocean to the San Bernardino Mountains, RMV now encompasses nearly 23,000 acres, 17,000 of which is permanent open space watershed ecosystem, managed as The Nature Reserve. Fire Station 67 sits on a ridge above Trampas Canyon and the original historic ranching operations, which hosts one of California’s highest profile professional rodeos.
The climate crisis has brought devastating wildfires to California, burning millions of acres and destroying tens of thousands of homes each year. The functionally driven site plan and configuration of the building zones give firefighters rapid access to serve public safety, and also feel privacy, calm, and connection to the wide-open views of Trampas Canyon.
Designing for the Future Now
Interim fire stations are typically built as generic, interior focused boxes. “We wanted to break open the box and look beyond” says Matt Wittman, the lead architect at Wittman Estes. As single use programs box buildings can have shorter lifespans, built with inexpensive and non-durable materials. These short-term stations end up in landfills, adding to the waste stream and accelerating climate change. Wittman Estes and the Fire Station 67 team wanted a more expansive future for this interim fire station.
Fire Station 67 is built on a modular system that allows for future relocation and reconfiguring. The sturdy and durable steel modules are easily transportable, and re-arranged for future uses, extending the lifespan of the buildings, and accommodating flexibility to meet what the future may bring.
The fire station is built on a modular system of rigid grids of structural steel frames, with ‘pick pockets’ for infinite rearrangements. Wittman Estes created an architectural kit of parts – each one sized and optimized for rapidly deployable transport and fast assembly. “This is the future, there is no doubt,” says Jim Holas, Director of Architecture for RMV.
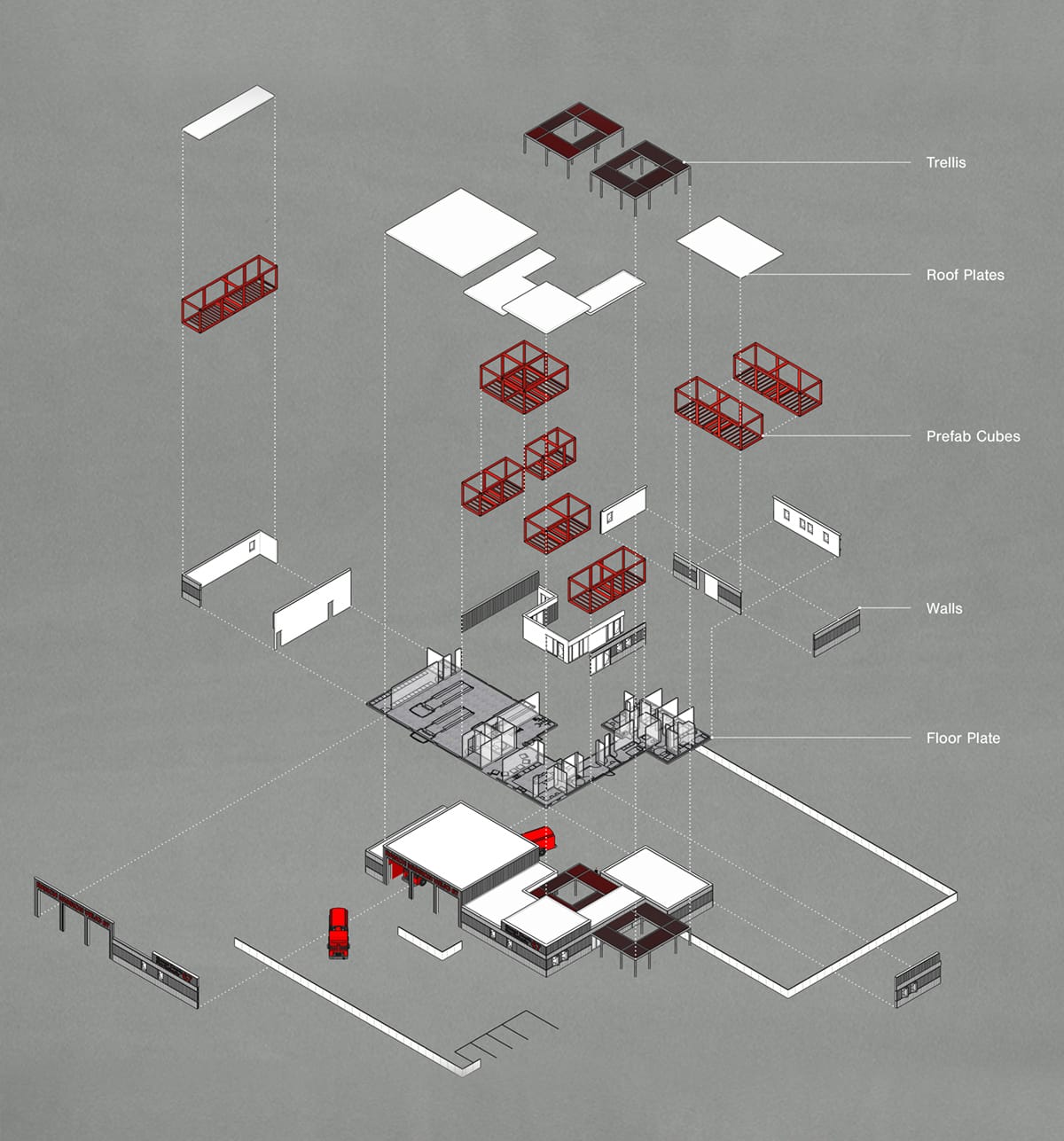
For this project, Wittman Estes created an architectural kit of parts – each one sized and optimized for rapidly deployable transport and fast assembly.
12’ wide modules and 30’ long steel trusses create a rhythm of steel and aluminum. Steel is tough and non-combustible, and the most efficient structural material from a weight to strength ratio. The steel cubes of this kit-of-parts approach are easily placed using a mobile, telescoping forklift within a matter of hours.
By designing for offsite fabrication and rapid assembly, Wittman Estes streamlined the design, documentation, and permitting process so construction could begin less than a year after the design process began. This process allowed for parallel site development work in California and the factory construction in Nevada, resulting in a six-month total construction timeline.
The symbiotic nature of the modular structure is its ability to adapt and serve the community in which it’s placed and to be reconfigured in the future when the community’s needs change. “How can we keep a building in use for as long as possible?”, asked Matt Wittman. Fire Station 67 will be re-purposed and given a second life in ten years when it will become an environmental learning center for Rancho Mission Viejo, California.
Form Follows Function
The flat topography of the site is punctuated with the fire station building, echoing the rising hills in the distance. The site plan is ringed by a circular drive to service rapid entry and exit to the apparatus bay by the fire trucks. The program includes a vehicle bay for two fire trucks, six sleeping rooms, a day room, kitchen/dining room, dispatch/workspace, and a captain’s office.
The 12-foot modules are assembled around a semi-protected central courtyard which provides shaded space for firefighters to recharge and relax. An aluminum trellis in the courtyard protects the space from the hot sun. Rhythmic glazing reinforces a rational exterior and revealing the functionality of the interior. A steel trellis welcomes the visitor and draws them into the heart of the building underneath the large illuminated red letters of the “Orange County Fire Authority 67”.
The muted exterior color palette creates a unified expression while drawing attention away from the structure and towards the verdant ecosystem beyond. The compact plan and simple form optimize efficiency and the future thinking that each space can be reinvented for a different future purpose. The plan adjacencies support an environment for both work, rest, and camaraderie between the firefighters.
The interior of the building is designed with an awareness for function. The north facing public entry, captain’s office and dispatch room look toward the neighborhood. The more active areas, including break room, kitchen, and fitness rooms face east toward fire trucks and the rising sun. The sleeping rooms and bathrooms are located in a quiet zone in the west, away from the noise and activity. The fourth zone is the apparatus bay to the south, which completes a courtyard and courtyard layout. Instead of fitting functions inside a single box, the open distribution of modules follows the flow of firefighter’s daily routines—form follows function.
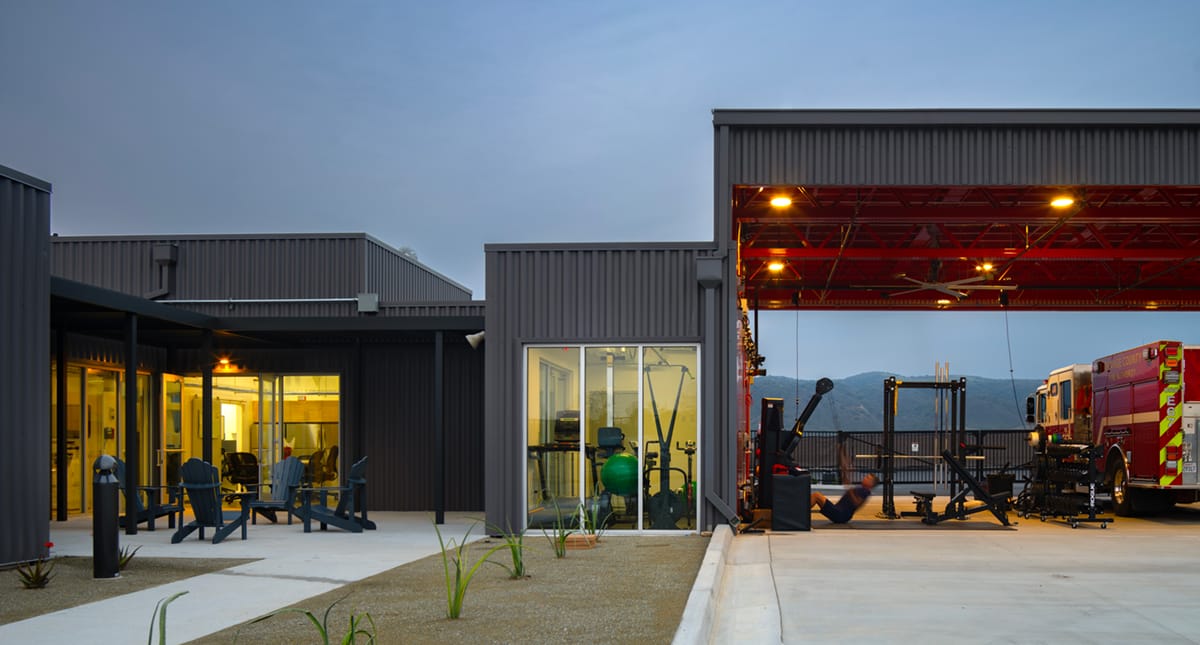
The interior spaces are optimized for firefighters to recharge and relax by toning down in detailing and color for a tranquil palette. In contrast, the active bay where the firetrucks are parked and maintained is painted with a bright red, mimicking the flurry of activity that happens in the bay. “The firetruck red color can be seen from a distance,” says Brandon Patterson of Wittman Estes. “Signaling it’s function, extenuating its form, and serving as a beacon to the community and feel protected.”
Typical fire station garages have poor indoor air quality due to heavy exhaust from fire trucks which remain running inside an enclosed space. Normally this is overcome by energy intensive and expensive mechanical systems to exhaust the toxic air outdoors. Wittman Estes designed an open-air apparatus bay to bring in fresh outside air and eliminate the need for large exhaust machines. The bay also serves as a multi-use space—sheltering the fire trucks while also providing an airy outdoor pavilion for exercise equipment, gatherings, and events.
The interior reinforces the simplicity and efficiency of the modular structure, keeping each element neutral in tone and material while still guiding the sunlight into the heart of the building. Light gray floors, white walls, and simple wood cabinetry create a clear and uncluttered interior encouraging the exposed structure, wiring, and plumbing emphasize the working nature of the building.
Community-Based Reconfigurations
Modular design allows for the building to have multiple life cycles. It can be built for emergency response services and then re-configured for more community-based uses. It combats material waste issues by reconfiguring to a community’s need at different times during its lifespan. It also alleviates inefficiency in construction by adapting to on-site time constraints as prefabricated design can be built off site and then assembled at appropriate time.
In 10 years, the layout will become something new and respond to the climatic specifics of a new site. It will have a new solar exposure to the heat of the sun, the winds, and views to the hills. The kitchen and break rooms will become public event spaces, and the sleeping rooms will become private offices and rooms for work and environmental research on flora, fauna and local ecology. The trellis will be dis-assembled and re-configured to define the perimeter of a new outdoor terrace.
In 50 years, the modules can adapt to any future, as their steel, modular form are universal design, defined by the most basic elements of human routines. Sleeping rooms can be for permanent dwellings, live/work spaces, or any other use of a single human. Break rooms and fitness rooms can be ganged together to create 12’, 24, 36’, or 48’ wide rooms, supporting gathering spaces for varying numbers. The modules are a universal language of space, sized to a variety of comfortable widths and divisions that have infinite possible configurations in a virtuous cycle of future uses.
In its simplest form, a fire station functions as a dwelling with a oversized garage. At its most complex, fire stations embody the values of its community and functions as a high technical operation for emergency response. Combining modular design with this intent, Fire Station 67 symbolizes the future of civic buildings – reflecting the needs of the community, the emergency responders, and the climate of the site itself.
More from Modular Advantage
AI, Faster Sets, and Automation: The Future of Modular is at World of Modular
While the modular building industry has long known that it can be an effective solution to increase affordable housing, the word is slowly spreading to more mainstream audiences. Three presentations at this year’s World of Modular in Las Vegas hope to provide insight and direction for those seeking a real solution to the crisis.
An Insider’s Guide to the 2025 World of Modular
The Modular Building Institute is bringing its global World of Modular (WOM) event back to Las Vegas, and with it comes some of the industry’s best opportunities for networking, business development, and education. Over the course of the conference’s four days, there will be numerous opportunities for attendees to connect, learn, and leverage event resources to get the most out of the conference.
Affordable Housing Now: The Industry’s Best Bring New Solutions to World of Modular
While the modular building industry has long known that it can be an effective solution to increase affordable housing, the word is slowly spreading to more mainstream audiences. Three presentations at this year’s World of Modular in Las Vegas hope to provide insight and direction for those seeking a real solution to the crisis.
Opportunities for Innovation in Modular Offsite Construction
Modular Offsite Construction has already shattered the myth that it only produces uninspired, box-like designs. Architectural innovations in module geometry, configurations, materials, and products make it possible to create visually stunning buildings without sacrificing functionality or efficiency.
Safe Modular Construction with Aerofilm Air Caster Transport
In collaboration with Aerofilm Systems, Heijmans developed innovative skids using air caster technology for moving modules easily and safely. These pallets are equipped with an auto-flow system, making operation extremely simple.
Miles, Modules, and Memes: Building a Modular Network One Flight at a Time
At the end of the day, social media is just another tool for building connections, and like any other tool, needs to be used skillfully to work properly. Use social media thoughtfully, and it will open doors to real opportunities and relationships you didn’t even see coming.
Falcon Structures: Thinking Inside the Box
Some of Falcon’s latest projects include creating container solutions for New York’s Central Park and an East Coast professional baseball team. More and more, Falcon is shipping out container bathrooms and locker rooms to improve traditionally difficult work environments, like those in oil and gas or construction.
UrbanBloc—From Passion to Industry Leader
UrbanBloc specializes in three main categories or markets – what they call “Phase 0” projects, amenities, and urban infill. Clients are often attracted to shipping containers because from a real estate perspective they are considered an asset. Having the flexibility to move and transport these assets allows owners to respond to different circumstances in a fluid manner that they can’t get with standard construction.
The Hospitality Game-Changer
“Hospitality is about more than just providing a service – it’s about delivering an experience,” says Anthony Halsch, CEO of ROXBOX. “And that’s where containers thrive. They allow us to create spaces that are unique, efficient, and sustainable.”
Container Conversions Counts on Simplicity to Provide Critical Solutions
Container Conversions has fabricated and developed thousands of containers for varied projects, including rental refrigeration options, offices, kitchens, temporary workplace housing, and mobile health clinics.