World of Modular Europe to Bring Industry Insights, Expertise to Brussels
Modular and offsite construction are nothing new to European building stakeholders. Still, with the rate of industry innovation and evolution around the world, continuous education, networking, and knowledge sharing is key. To that end, the Modular Building Institute (MBI), the world’s largest international trade association for the commercial modular construction industry, is bringing its premier event to the heart of Europe in October, 2024.
World of Modular Europe, to be held in Brussels on 1-2 October, will be an event like none other. Featuring speakers, exhibitors, and attendees from across Europe and around the globe, World of Modular Europe will be a world-class forum, offering key insights, best practices, and the opportunity to meet leaders and stakeholders from every corner of industry.
Examining the State of Modular Construction in the UK and Europe
Speakers from around the UK and Europe will be presenting at World of Modular Europe, including Michael Hough, principal at Ireland’s MJH Structural Engineers, and Franco Vietti, associate at Holland-based Green Prefab. Both Hough and Vietti will be sharing—among other things—their insights on the industry based on their 20-plus year careers.
“Recently,” says Hough, “the UK government conducted an enquiry into the barriers to modern methods of construction (MMC) to see how government may assist with improving the output of housing. In broader terms, there appears to be a move towards some level of standardization within the industry, through platforms and repetition. While there is a place for standardized platforms in the industry, I believe that this is just one piece of the puzzle in the goal to redefine the construction industry and improve productivity in line with the developments in technology in society.”
Outside the UK, adds Vietti, “Europe is steadily increasing the premanufactured value of each building project by moving towards the adoption of not just one particular offsite system, but a combination of systems depending on each application. From my perspective, hybridization—combining different prefabrication methods—is the best approach to industrializing the sector in Europe, especially from the developer's standpoint, in order to mitigate the risks of a yet-to-develop broad supply chain.”
"Ultimately, says Hough, “in order to move the needle towards general acceptance of modular construction we need to see the promotion of innovation, flexibility and the adoption of more modular solutions to construct more and more statement buildings.”
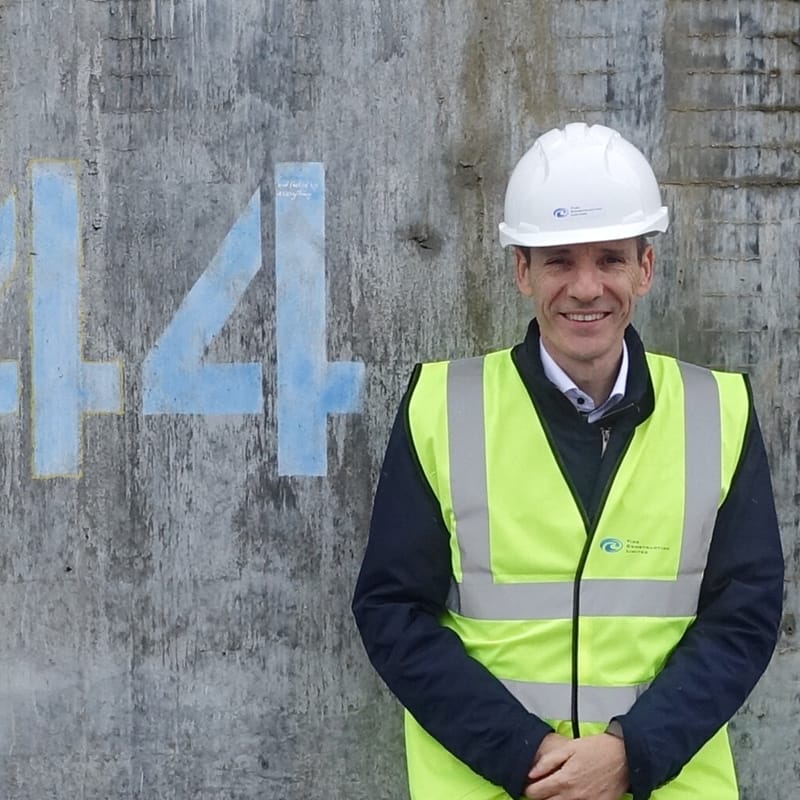
Michael Hough, principal at MJH Structural Engineers, stands next to the core of 101 George Street in London, a high-rise volumetric modular project he and his team engineered. Photo credit: Michael Hough.
Exploring the Barriers to MMC Adoption—And the Opportunities That Lay Ahead
"Europe is a complex landscape shaped by stringent regulatory frameworks,” says Vietti, “which can vary significantly from one country to another, and even between regions within the same country. In some cases, there is strong support from governments, but this doesn't always yield efficient and quick results. Like everywhere, governmental initiatives to quickly solve long-term structural problems, such as housing shortages and emergencies, are often less effective in boosting the industry than addressing inefficiencies and bureaucracy, allowing the private sector to take the lead.”
That said, “modular construction is still very much in its infancy,” adds Hough, “with no clearly defined system operating across all markets. There are pockets of Europe where modular is very prolific, such as Sweden, and plenty of countries where it has not taken off at all yet. The flexibility in codes in Europe…allows innovation but also requires that the construction system is proven to do so, as well.”
"Modular volumetric construction is showing strong performance as a delivery system for commercial buildings, including healthcare, education, student accommodation, and build-to-rent developments,” says Vietti. “There is also increasing interest in data centers and other mission-critical buildings. It is important to note that these markets are also targeted by real estate developers during economic downturns, and modular volumetric construction stands as a perfect solution for them. Within these groups, companies with diversified business models and a more service-oriented approach are outperforming the design-build ones, especially those targeting affordable housing.”
As for Hough, he says “medium-rise modular construction is probably where the most benefits are being realized around Europe right now. The split between site and factory is good and the parallel constructions have a large effect on program and the overall bottom line for a project. For some modular manufacturers, once adequate repetition is achieved vertically to allow viability of a project, then additional flexibility in horizontal changes to module layouts may be accommodated. These effects are increased in high rise construction, and we would like to see the high rise modular construction market increase in size with other companies entering the market building increasingly taller modular buildings and providing much needed homes in urban centers.”
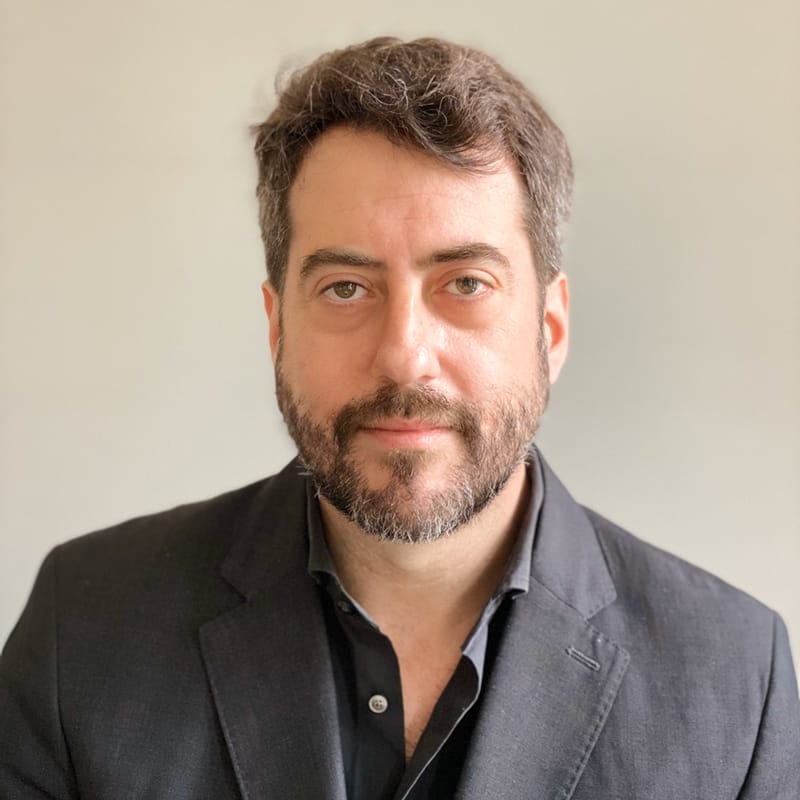
Franco Vietti, associate at Green Prefab, is an engineer and entrepreneur with nearly 20 years of experience in the modular construction industry. He’s worked across Europe, Latin America, and the Middle East and has been involved in projects with teams from the USA and Africa.
Related Reading:
The Digitalization of Offsite Construction: Trends & Best Practices to be Featured at World of Modular Europe
Digitalization and ever-advancing project modelling software have been aiding traditional manufacturers, builders, and designers for years. More recently, tech-savvy modular and offsite construction stakeholders have also embraced these tools, adding their own knowledge and data to create newer, faster, more efficient ways of building. Together with quickly-evolving AI-powered tools, these builders are now pushing the boundaries of what’s possible with offsite construction.
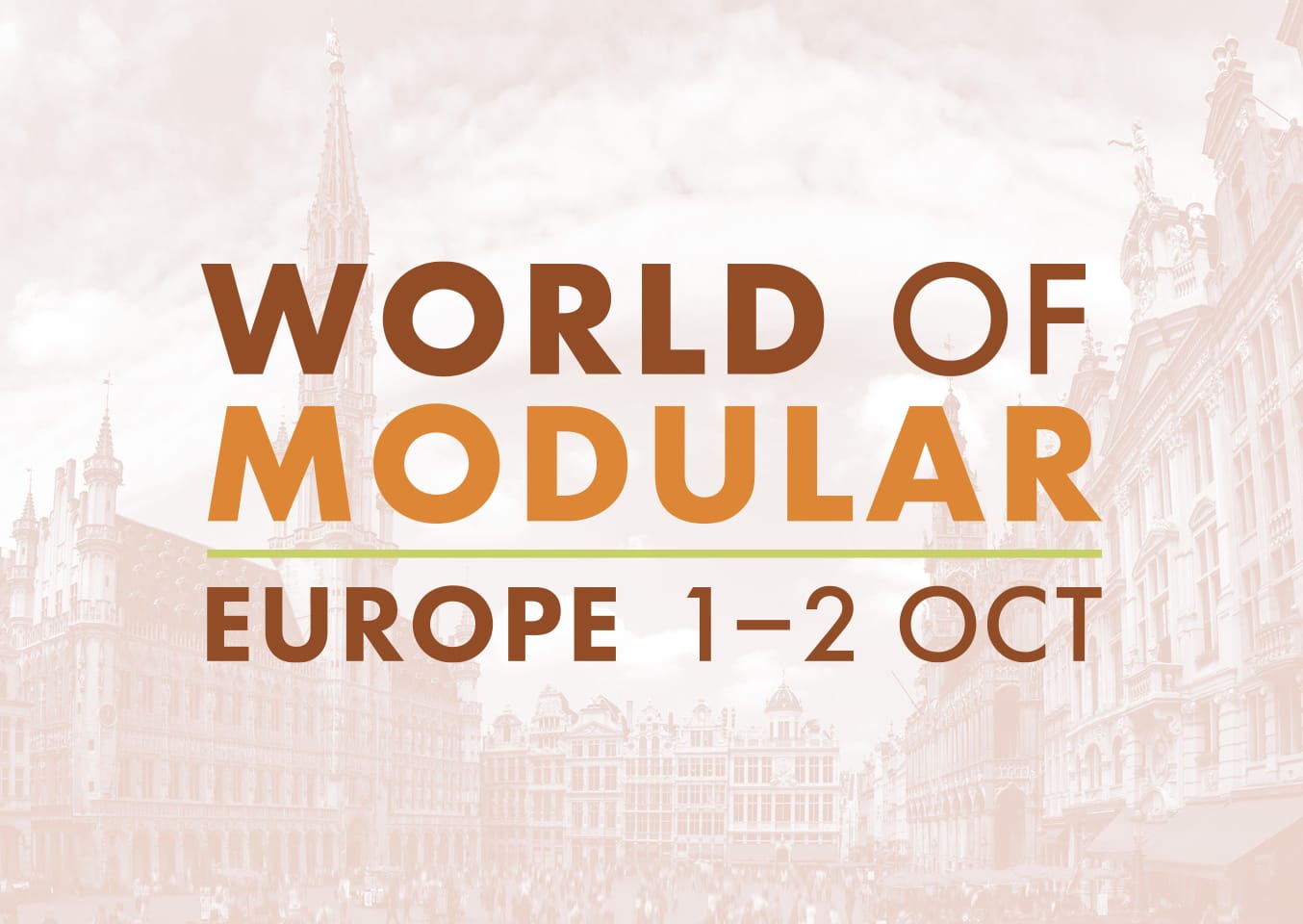
Setting the Stage for World of Modular Europe
"At the World of Modular Europe,” says Vietti, “I will focus on the opportunities for modular construction to truly enter the service economy. The service economy, comprising nearly 80% of developed countries' economies, has been boosted by the sharing economy and new generations' behaviors emphasizing ‘using versus owning’ assets, favoring an asset-light strategy. This trend presents a significant opportunity for the modular industry, as modular building allows one to own and service flexible building solutions for clients. In other words, there will be a transition from fixed real estate building assets to dynamic relocatable building asset solutions, creating outstanding opportunities for development.
"We call it Modular Building as a Service (MBaaS). This will revolutionize the commercial real estate industry by transitioning from traditional 'product and space' offerings to dynamic 'system and service' solutions, boosted by advanced automation and AI. In my presentation, I will explore this new concept and how it can be a disruptor for the industry.
"Additionally, I will examine the performance of different business models, including design-build, operating lease, and MBaaS in the modular industry. I will discuss how diversifying business models is a winning strategy for manufacturing companies looking to mitigate risk and increase profitability, investment opportunities, and return on equity for investors, developers, and asset managers.”
And in his presentation, Hough will track the evolution of modular construction in UK—with a focus on his recently completed work for the 50-story College Road Croydon project—to see what further advantages lay ahead.
“If anything has been learned in the last few years,” says Hough, “it is that a revolution in construction is difficult for many reasons. We will outline the progress in modular from the early 2000’s up to the current levels of construction and show what has been happening. We will showcase projects and the progression of modular construction over the years.
“Our latest completed project, College Road Croydon,” concludes Hough, “provided homes at a rate of more than one per day for the duration of the construction program in a building with seven levels of amenities. This is achieved only by the parallel processes of site and factory in tandem, the nature of the occupancy and using offsite to minimize the program. We would aim for the main takeaways to be the potential and successes of modular as it moves into more mainstream construction.”
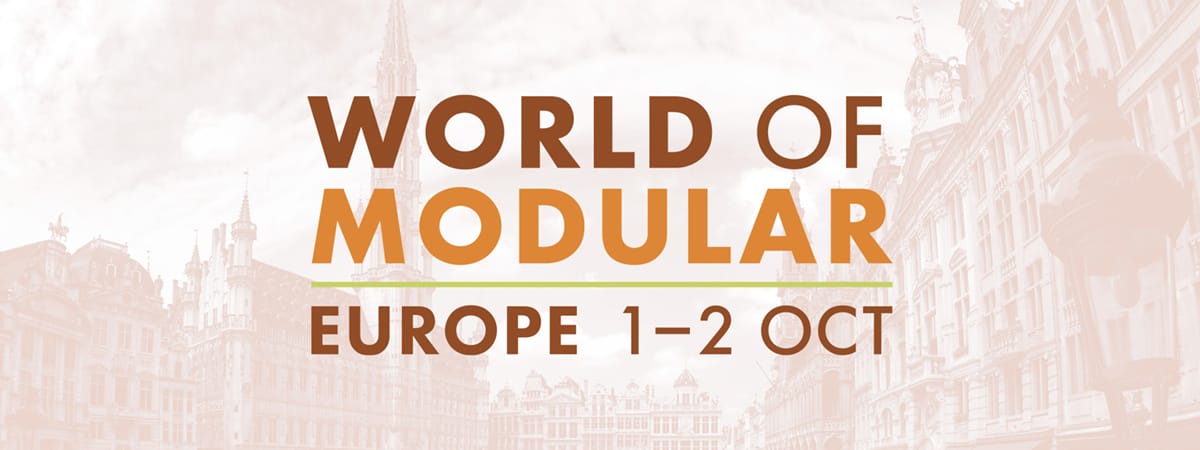
World of Modular Europe, presented by the Modular Building Institute, comes to Brussels on 1-2 October. Registration is now open.
Join the Industry in Brussels, 1-2 October, 2024
"Taking part in World of Modular Europe excites me because it provides a unique platform to connect with industry leaders, innovators, and visionaries from around the globe,” says Vietti. “I would not have worked all over the world and be collaborating with Green Prefab if not for an MBI event. These events foster knowledge sharing, collaboration, and the exchange of ideas that drive the industry forward. I am particularly eager to learn from my peers, discover new trends and technologies, and contribute to the ongoing dialogue about the future of modular construction. And maybe come back home with some new projects.”
See all speakers and presentations for World of Modular Europe and register today.
About the Author: John McMullen, PCM, is the marketing director for the Modular Building Institute. You can reach him directly at mcmullen@modular.org or on LinkedIn.
More From Modular Advantage
AI, Faster Sets, and Automation: The Future of Modular Is at World of Modular
While the modular building industry has long known that it can be an effective solution to increase affordable housing, the word is slowly spreading to more mainstream audiences. Three presentations at this year’s World of Modular in Las Vegas hope to provide insight and direction for those seeking a real solution to the crisis.
An Insider’s Guide to the 2025 World of Modular
The Modular Building Institute is bringing its global World of Modular (WOM) event back to Las Vegas, and with it comes some of the industry’s best opportunities for networking, business development, and education. Over the course of the conference’s four days, there will be numerous opportunities for attendees to connect, learn, and leverage event resources to get the most out of the conference.
Affordable Housing Now: The Industry’s Best Bring New Solutions to World of Modular
While the modular building industry has long known that it can be an effective solution to increase affordable housing, the word is slowly spreading to more mainstream audiences. Three presentations at this year’s World of Modular in Las Vegas hope to provide insight and direction for those seeking a real solution to the crisis.
Opportunities for Innovation in Modular Offsite Construction
Modular Offsite Construction has already shattered the myth that it only produces uninspired, box-like designs. Architectural innovations in module geometry, configurations, materials, and products make it possible to create visually stunning buildings without sacrificing functionality or efficiency.
Safe Modular Construction with Aerofilm Air Caster Transport
In collaboration with Aerofilm Systems, Heijmans developed innovative skids using air caster technology for moving modules easily and safely. These pallets are equipped with an auto-flow system, making operation extremely simple.
Miles, Modules, and Memes: Building a Modular Network One Flight at a Time
At the end of the day, social media is just another tool for building connections, and like any other tool, needs to be used skillfully to work properly. Use social media thoughtfully, and it will open doors to real opportunities and relationships you didn’t even see coming.
Falcon Structures: Thinking Inside the Box
Some of Falcon’s latest projects include creating container solutions for New York’s Central Park and an East Coast professional baseball team. More and more, Falcon is shipping out container bathrooms and locker rooms to improve traditionally difficult work environments, like those in oil and gas or construction.
UrbanBloc—From Passion to Industry Leader
UrbanBloc specializes in three main categories or markets – what they call “Phase 0” projects, amenities, and urban infill. Clients are often attracted to shipping containers because from a real estate perspective they are considered an asset. Having the flexibility to move and transport these assets allows owners to respond to different circumstances in a fluid manner that they can’t get with standard construction.
The Hospitality Game-Changer
“Hospitality is about more than just providing a service – it’s about delivering an experience,” says Anthony Halsch, CEO of ROXBOX. “And that’s where containers thrive. They allow us to create spaces that are unique, efficient, and sustainable.”
Container Conversions Counts on Simplicity to Provide Critical Solutions
Container Conversions has fabricated and developed thousands of containers for varied projects, including rental refrigeration options, offices, kitchens, temporary workplace housing, and mobile health clinics.