Inside the Construction of 355 Sango Court
The 2024 Best of Show for Permanent Modular Construction
This year’s Awards of Distinction winner for Best of Show for Permanent Structures is 355 Sango Court, a 105,818 square foot affordable housing development manufactured by Nampa, Idaho based Autovol. The project team also included Prefab Logic for module design, Nibbi Brothers as the general contractor, Acc U Set Construction as the modular installer, and the overall project design was by David Baker Architects and DCI and Fard. The 102-unit development was constructed in Milpitas, California, and is comprised of 113 modules.
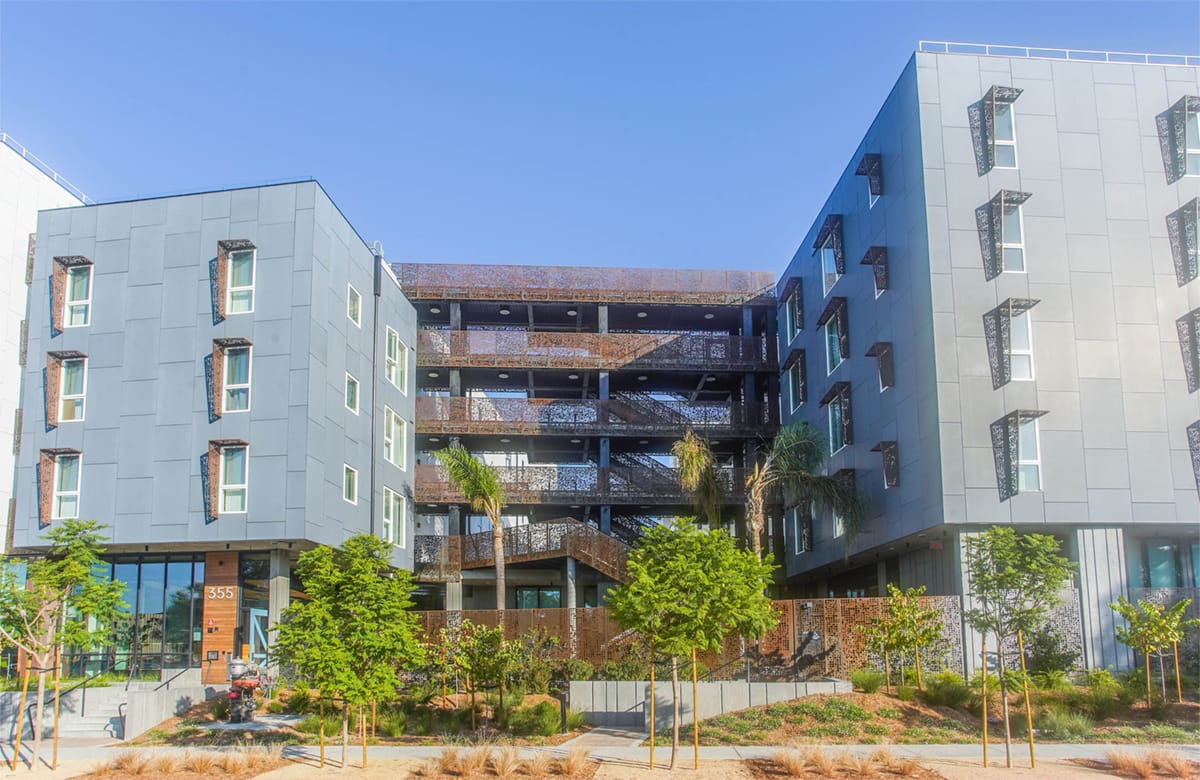
Rick Murdock, CEO and co-founder of Autovol, said it was one of the smoothest projects he’s experienced, which is surprising when you consider that this was the first modular project for the general contractor.
Nibbi Brothers approached Autovol after another manufacturer dropped out of the project. The two had an existing relationship, but no previous modular project experience. Murdock admits he was a bit nervous about taking on the project with a contractor who had no experience with modular construction. “All your alerts are out because there’s a lot of education that has to happen because it’s done differently.” But his nerves were unfounded.
“They worked with us all the way through the project. They were here at the plant really trying to understand how modular works, what are the issues with modular, what are the differences than with a traditionally built project. I was really pleased with the way they dove in and took ownership of their piece of it and did a tremendous job.” Nibbi even staffed a person at the factory to get a better understanding of Autovol’s quality assurance program.
Interestingly, Autovol also learned something from Nibbi Brothers during the project. Nibbi suggested a change in the material used to wrap the units and keep them dry while they are in transit and being installed. Murdock admits he was against it in the beginning because it was different than what they normally did and took more labor. But Nibbi was persistent, so they tried it, and now it has been implemented as the standard for all units going out of Autovol’s factory.
An important part of Autovol’s process is the design and programming for their automated assembly line. In 2016, Murdock and Autovol co-founder Curtis Fletcher started a company to provide those services to Autovol and other modular manufacturers called Prefab Logic. According to Murdock, “There’s a disconnect between developers, general contractors, and modular manufacturers because modular is not as common as we’d like it to be and it’s a different type of building. So, we started the company to help everyone understand how it works.”
A year and a half ago they added a mechanical, electrical, and plumbing engineering group to their team. With in-house engineering they are able to be more efficient with their design process. “That’s one of the things we’re really focused on, trying to make the process better, faster, and more accurate from an engineering and architectural standpoint, so we have fewer coordination issues, improved accuracy, and better documentation for our teams,” said Fletcher.
Prefab Logic’s role in this project was to make the design viable for Autovol’s automated manufacturing, get the project through permitting, and then convert the design to programming language for the robots on the manufacturing floor. Their in-house MEP engineering team played a key part in this process.
Fletcher’s team created a digital twin of the completed structure. “We use it for our customers to preview what we’re doing and see if there’s anything that they would like to change or any comments they have,” said Murdock. All facets of the building are modeled, right down to framing, structural components, MEP locations, and every hole, screw, and nail. The model is also used by the internal manufacturing team to spot issues that might come up on the line.
Once the project is completed, a Navisworks model is then passed on to the owner for use in operations and maintenance.
The project had a pretty aggressive timeline as it needed to fit into Autovol’s production schedule, so the team worked diligently to expedite the design and programming process, which was completed in only four and a half months. Autovol has one of the fastest production lines, so the project’s 102 units took just under two and a half months to manufacture, with the entire project taking 443 days to complete.
The four-story development consists of two concrete and steel buildings connected by a series of linked courtyards, providing access to nature for all residents. On the ground floor there’s a garden entry and open-air lobby, with 102 permanent supportive homes on the floors above. The units are a mix of studios, one-, two-, and three-bedroom apartments. An emphasis was placed on sustainability and energy efficiency, building to CalGreen standards, using WaterSense certified plumbing fixtures, and efficient windows. The facility is managed by Resources for Community Development, which provides rental homes for more than 5,450 people in 25 cities in the region, about one third of which are reserved for people with special needs.
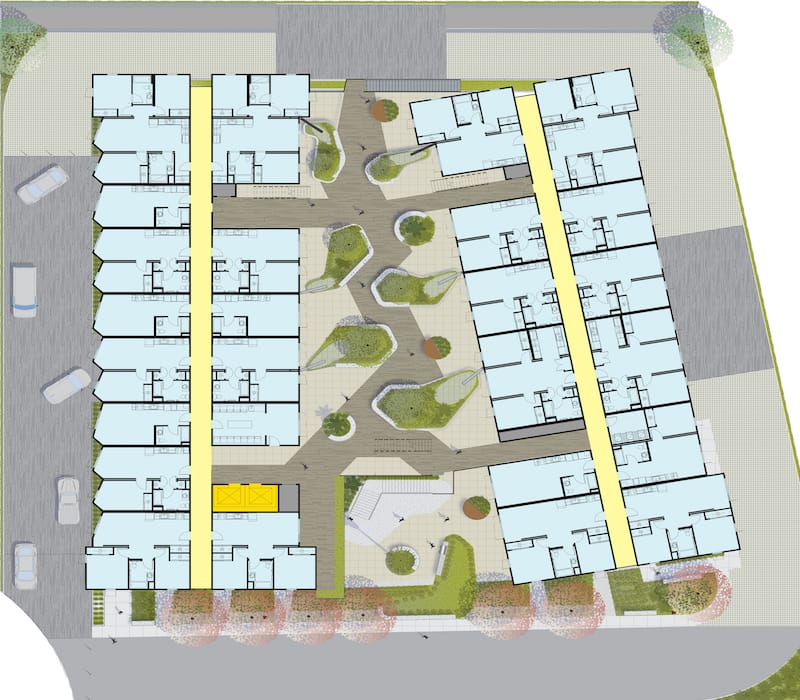
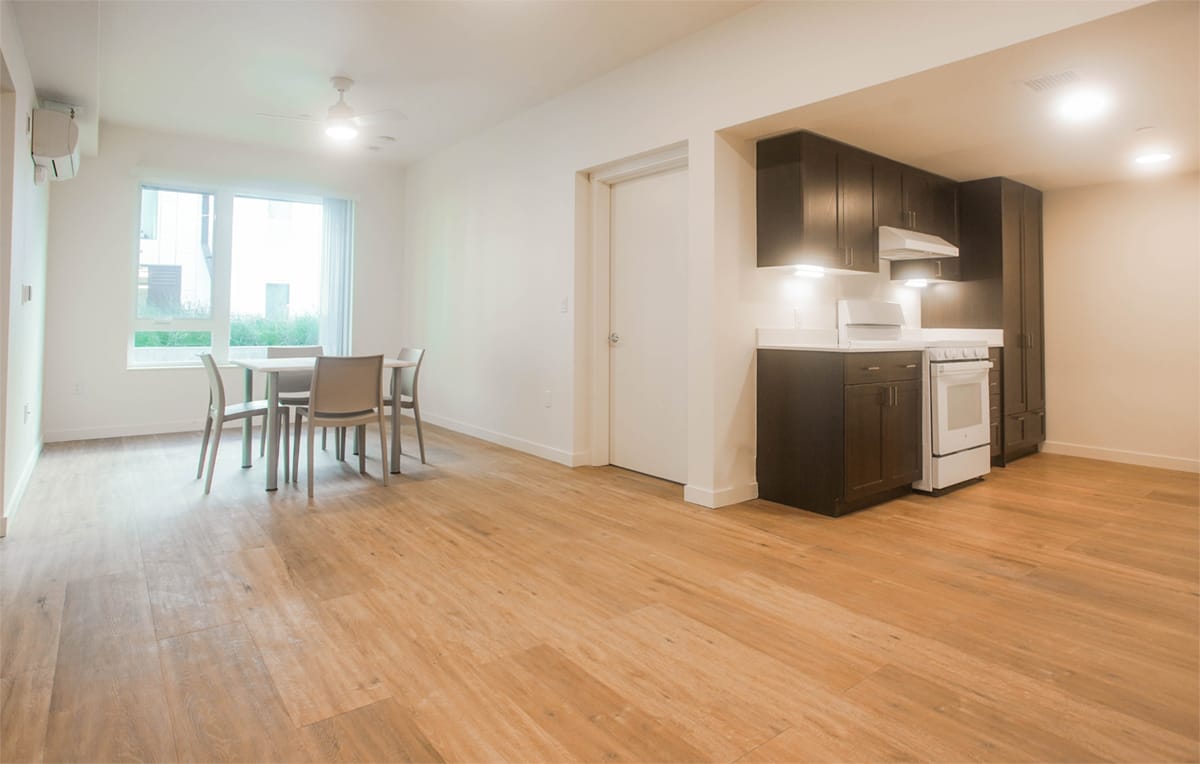
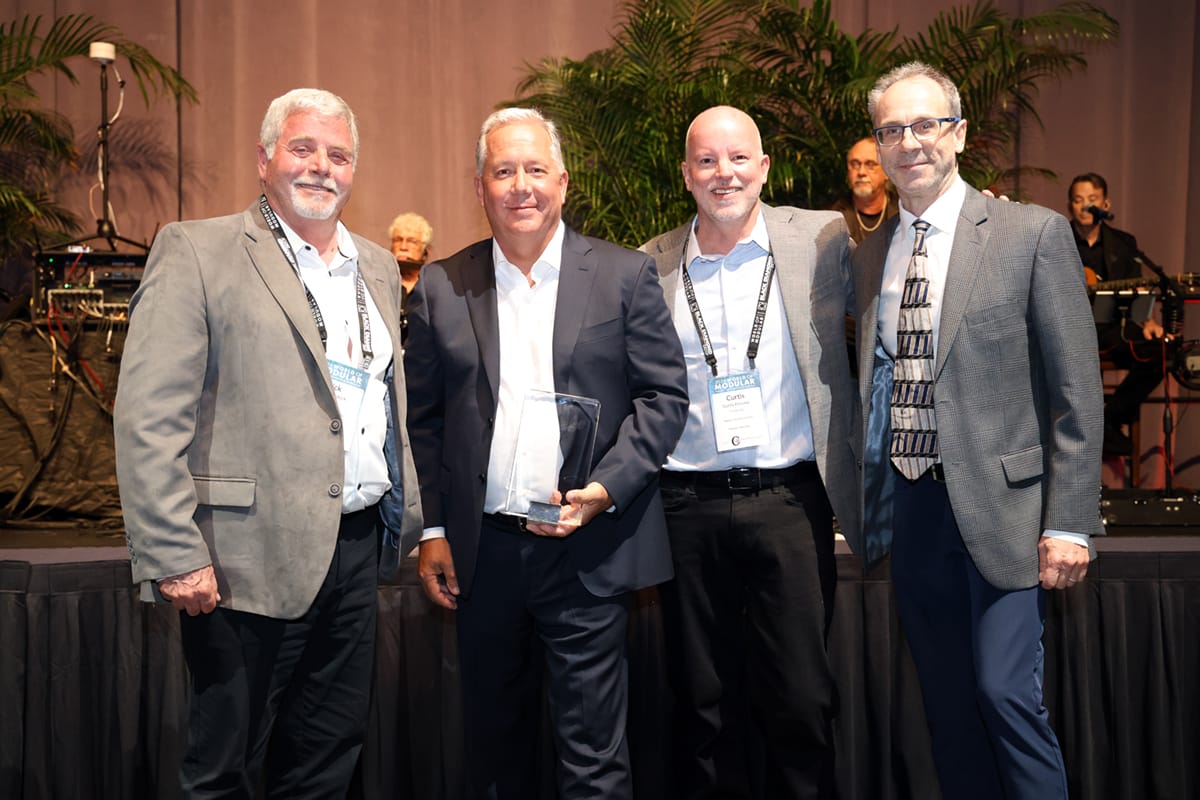
There are significant cost savings for using modular construction on a project like this. Murdock said that developers in the Bay Area could save between $80 to $100 a square foot. And of course, the real benefit is the time savings, as a modular building can be manufactured and assembled significantly quicker than a traditional building.
Autovol boasts the world’s first fully automated volumetric modular factory. At 400,000 square feet the factory utilizes robots to do most of the heavy lifting and repetitive processes, including building the floors, walls, and ceilings, while skilled workers, called “solutioneers,” perform the interior finish work, fixture installation, and mechanical, electrical, and plumbing. Their production rate is an incredible five units a day, which translated into 629,772 square feet of living space in 2023.
Prefab Logic provides services to a variety of modular manufacturers and developers. They can help owners or contractors select a modular factory, work with design teams to design for modular construction, provide digital twin and BIM modeling, and walk projects through the permitting process.
About the Author: Dawn Killough is a freelance construction writer with over 25 years of experience working with construction companies, subcontractors and general contractors. Her published work can be found at dkilloughwriter.com.
More from Modular Advantage
Oregon’s Prevailing Wage Proposal: A Wake-Up Call for Modular Construction
Should House Bill 2688A become law, building projects would increase in price, face longer completion timelines, and produce significantly more waste. The bill also incentivizes contract awards to out of state businesses who would not reinvest their earnings into the local Oregon economy.
Behind the Design of Bethany Senior Terraces, NYC’s First Modular Passive House Senior Housing Project
As more developers seek to meet new regulations for energy efficiency, the team at Murray Engineering has set a new record. With the Bethany Senior Terraces project, Murray Engineering has helped to develop NYC’s first modular structure that fully encompasses passive house principles — introducing a new era of energy efficiency in the energy-conscious city that never sleeps.
How LAMOD is Using Modular to Address Inefficiency, Sustainability, and the Future of Construction
As developers, designers, and contractors seek to understand the evolving needs of the modular industry, no one is as well-versed in the benefits of going modular as Mārcis Kreičmanis. As the co-founder and CBDO of LAMOD in Riga, Latvia, Mārcis has made it his ultimate goal to address the inefficiencies of traditional construction.
From Furniture Builder to ‘Activist Architect’: Stuart Emmons’ Unique Journey
Stuart Emmons was fascinated by buildings at a young age. He remembers building sand cities with his brother during trips to the Jersey shore. His father gave him his first drawing table at the age of ten. Today, he is an experienced architect who received his FAIA in June 2025. The road he took is unique, to say the least.
Forge Craft Architecture + Design: Codes, Contracts, and Intellectual Property
Founding Principal and Director of Modular Practice for Forge Craft Architecture + Design, Rommel Sulit, discusses the implications of codes, contracts, and intellectual property on
modular construction.
Eisa Lee, the “Bilingual” Architect
Now as the founder of XL
Architecture and Modular Design in Ontario, Canada, she applies not just her education as a traditional architect but an entire holistic view on modular design. It’s this expansive view that guides her work on being a true partner that bridges the gap between architects and modular factories as they collaborate on the design process.
Tamarack Grove Engineering: Designing for the Modular Sector
The role of a structural engineer is crucial to the success of a modular project, from initial analysis to construction administration. Tamarack Grove offers structural engineering services — project analysis, plan creation, design creation, and construction administration — for commercial, manufacturing, facilities, public services, and modular. Modular is only one market sector the company serves but it is an increasingly popular one.
Engineer Masters the Art of Listening to His Customers
Since founding Modular Structural Consultants, LLC. in 2014, Yurianto has established a steady following of modular and container-based construction clients, primarily manufacturers. His services often include providing engineering calculations, reviewing drawings, and engineering certification
Inside College Road: Engineering the Modules of One of the World’s Tallest Modular Buildings
College Road is a groundbreaking modular residential development in East Croydon, South London by offsite developer and contractor, Tide, its modular company Vision Volumetric (VV), and engineered by MJH Structural Engineers.
Design for Flow: The Overlooked Power of DfMA in Modular Construction
Unlocking higher throughput, lower costs, and fewer redesigns by aligning Lean production flow with design for manufacturing and assembly.