Aster Place by ROC Modular
The 2024 Best of Show for Relocatable Structures
Aster Place, a supportive housing building in Richmond, British Columbia, Canada, won the Best of Show Award and Honorable Mention for relocatable structures in the social and supportive housing category of the 2024 Awards of Distinction ceremony, held on the fnal evening of the 2024 World of Modular conference. The project was constructed by Tasu Construction Ltd., a general contractor from Squamish, British Columbia, and ROC Modular, a modular manufacturer in Bow Island, Alberta, and was completed in 2022.
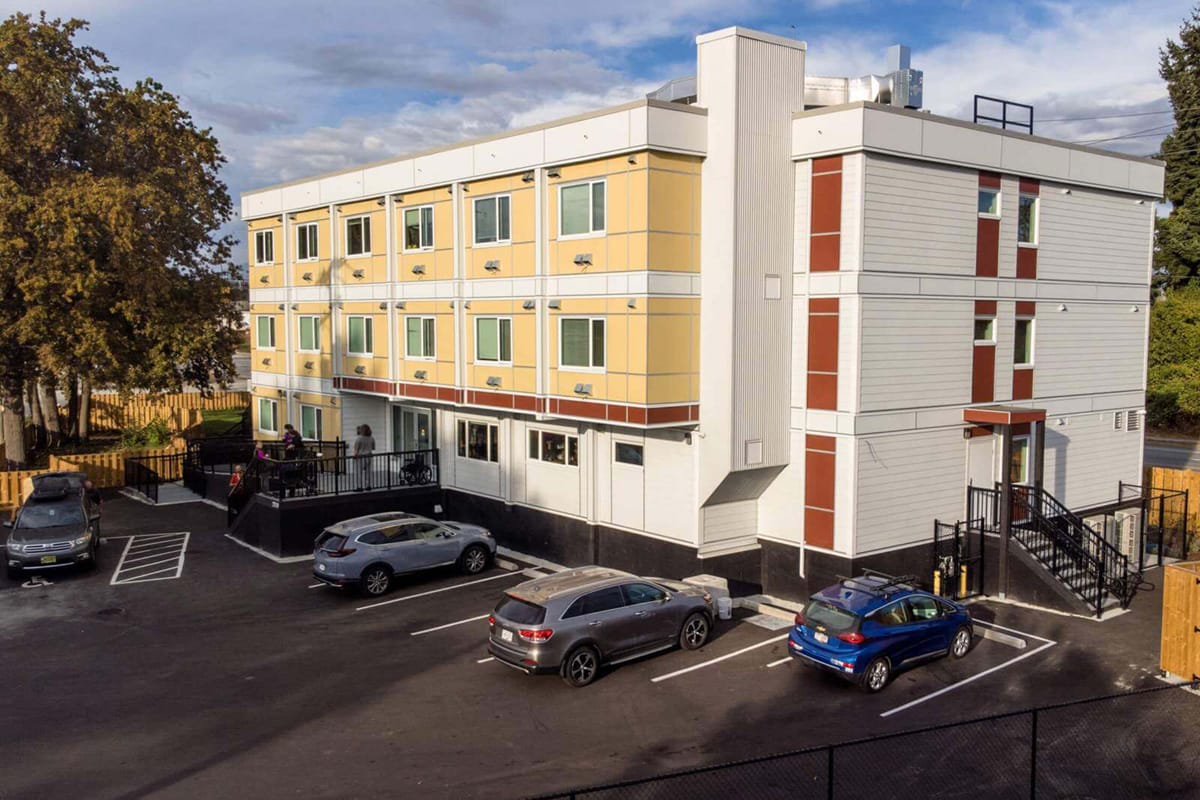
The 40-unit, 21,726 square foot temporary housing structure is part of an extensive investment by British Columbia to provide affordable housing and services for residents who are elderly, disabled, in financial need, and indigenous populations. The program, called Building BC, represents an investment of $1.2 billion over 10 years to deliver an additional 2,500 new homes in the province. Many of those new homes are benefitting from the multiple advantages modular construction provides.
The agency is focusing on underutilized sites to provide temporary housing. Aster Place is set on an existing parking lot with a Triodetic foundation.
Rhys Kane, Director of Business Development for ROC Modular, likens the foundation to a raft. “It’s a scaffold-type structure of metal and it sits as a raft slab across the top of the ground. It has these pivot points that you can adjust, and it effectively moves with the ground. It was invented and developed in northern Canada to sit above the permafrost. We’ve used it on northern projects and recognized that it was a good option for a relocatable foundation.”
The specialized foundation is a good investment because it reduces construction time and can be moved along with the building, saving the cost of another foundation.
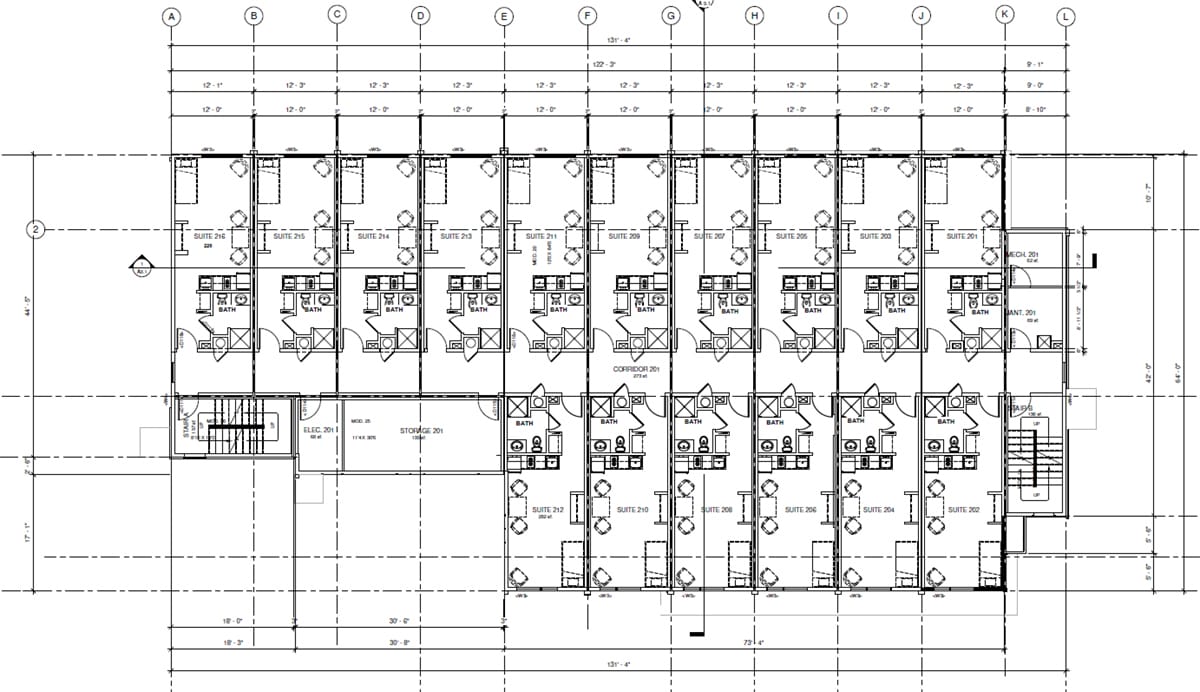
The building is three stories, with the main floor housing support services and common areas for residents, including meeting rooms,
an office, a TV room, laundry facilities, storage, medical rooms, and a shared commercial-grade kitchen. Services provided include daily meals, life-skills training, employment assistance, counselling, physical and mental health resources, and access to addiction treatment and recovery services. Each unit provides a private bathroom and kitchenette.
Units come out of the factory completely finished, including mechanical systems, interior finishes, exterior finishes, kitchens, bathrooms, and even furniture, beds, and mattresses. Four of the 40 units are accessible. The project required 39 modules and took 345 days to complete.
The modules are built to meet all local building codes and permitting requirements. Aster Place meets Step Code three of the BC Energy Code, and includes features like triple pane windows, additional wall insulation, high performance mechanical systems, and LED lighting. Living units are designed to keep energy costs low for residents. The structure is set to remain on site for five to ten years while the local government explores additional housing opportunities.
Kane sees the development as a perfect showcase for how modular can help communities respond to the affordable housing crisis. “It’s very repeatable in terms of the design. There’s a template, a kit of parts to do these buildings. The modular approach is a great way to fast track. And it shows what commitment to a program can do to deliver these buildings at such speed. It takes the city of Richmond and BC Housing to say, ‘We’ve identified this site. We’re going to fast track this project, and we’re going to call it temporary. That means it avoids all the entitlements and all of the things that come with a permanent structure in terms of building permit process and timelines, which can take one to two years. And the modular company can basically repeat the modules at the factory. It provides a retained asset for the city and BC Housing that can be moved in the future.”
So far, the province has deployed over 600 housing units in similar fashion. Most are in 30-to-50-unit, three-story configurations, similar to Aster Place. The smaller-sized buildings reduce the amount of community pushback that might come with larger developments containing more units. Everything is fast-tracked through the review and permit process to speed deployment.
The project wasn’t without its struggles, of course. Since the site was in an urban environment, getting the modules to the site, setting up cranes, finding staging areas, and setting them was a challenge. The speed of design is another hurdle the team had to collaborate on to solve.
“You are delivering the project at such a fast pace, putting together the design and engineering at the same time, getting client input, and trying to meet code requirements is a challenge. We wanted to be manufacturing within six months, so there was lots of early engagement and decision making early in the process.” ROC and Tasu worked closely with suppliers, subcontractors, and the design team to ensure that the project met its budget requirements while providing energy efficiency within the short design timeframe. ROC also served as a consultant to help the team adapt modular construction techniques to the needs of the project.
ROC Modular has built over 5,000 modules and has extensive experience in creating affordable housing. They focus their services in western Canada and the north and central United States and have a 60,000 square foot manufacturing facility in southern Alberta. They specialize in social and affordable housing, hospitality, multi-family, education, and industrial modular construction. ROC gives back to the communities it serves, with a relentless focus on “creating spaces for people to thrive.”
The Aster Place development is operated by Community Builders Group, which provides culturally appropriate living assistance to those in need.
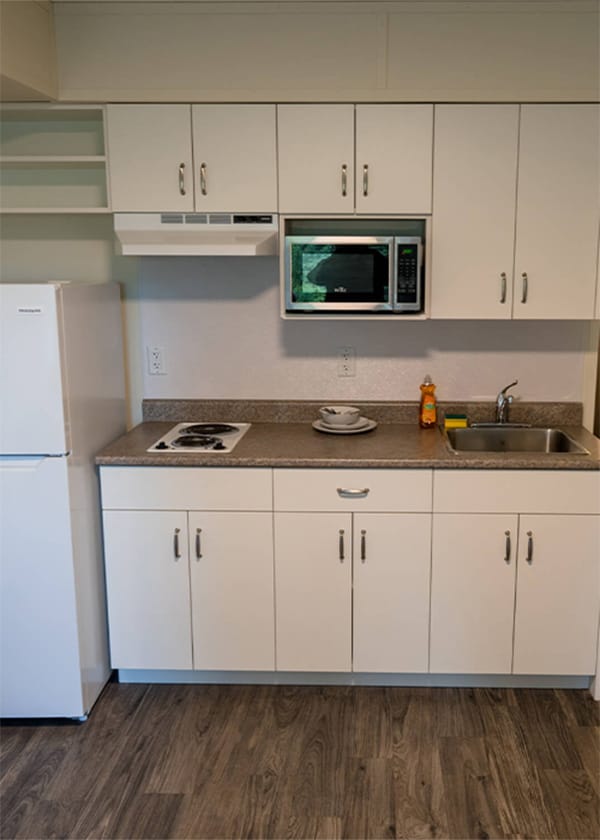

ROC Modular CEO Joe Kiss (left) and Rhys Kane (right) accept an Award of Distinction from MBI past president Chuck Walen at the 2024 World of Modular.
About the Author: Dawn Killough is a freelance construction writer with over 25 years of experience working with construction companies, subcontractors and general contractors. Her published work can be found at dkilloughwriter.com.
More from Modular Advantage
AI, Faster Sets, and Automation: The Future of Modular Is at World of Modular
While the modular building industry has long known that it can be an effective solution to increase affordable housing, the word is slowly spreading to more mainstream audiences. Three presentations at this year’s World of Modular in Las Vegas hope to provide insight and direction for those seeking a real solution to the crisis.
An Insider’s Guide to the 2025 World of Modular
The Modular Building Institute is bringing its global World of Modular (WOM) event back to Las Vegas, and with it comes some of the industry’s best opportunities for networking, business development, and education. Over the course of the conference’s four days, there will be numerous opportunities for attendees to connect, learn, and leverage event resources to get the most out of the conference.
Affordable Housing Now: The Industry’s Best Bring New Solutions to World of Modular
While the modular building industry has long known that it can be an effective solution to increase affordable housing, the word is slowly spreading to more mainstream audiences. Three presentations at this year’s World of Modular in Las Vegas hope to provide insight and direction for those seeking a real solution to the crisis.
Opportunities for Innovation in Modular Offsite Construction
Modular Offsite Construction has already shattered the myth that it only produces uninspired, box-like designs. Architectural innovations in module geometry, configurations, materials, and products make it possible to create visually stunning buildings without sacrificing functionality or efficiency.
Safe Modular Construction with Aerofilm Air Caster Transport
In collaboration with Aerofilm Systems, Heijmans developed innovative skids using air caster technology for moving modules easily and safely. These pallets are equipped with an auto-flow system, making operation extremely simple.
Miles, Modules, and Memes: Building a Modular Network One Flight at a Time
At the end of the day, social media is just another tool for building connections, and like any other tool, needs to be used skillfully to work properly. Use social media thoughtfully, and it will open doors to real opportunities and relationships you didn’t even see coming.
Falcon Structures: Thinking Inside the Box
Some of Falcon’s latest projects include creating container solutions for New York’s Central Park and an East Coast professional baseball team. More and more, Falcon is shipping out container bathrooms and locker rooms to improve traditionally difficult work environments, like those in oil and gas or construction.
UrbanBloc—From Passion to Industry Leader
UrbanBloc specializes in three main categories or markets – what they call “Phase 0” projects, amenities, and urban infill. Clients are often attracted to shipping containers because from a real estate perspective they are considered an asset. Having the flexibility to move and transport these assets allows owners to respond to different circumstances in a fluid manner that they can’t get with standard construction.
The Hospitality Game-Changer
“Hospitality is about more than just providing a service – it’s about delivering an experience,” says Anthony Halsch, CEO of ROXBOX. “And that’s where containers thrive. They allow us to create spaces that are unique, efficient, and sustainable.”
Container Conversions Counts on Simplicity to Provide Critical Solutions
Container Conversions has fabricated and developed thousands of containers for varied projects, including rental refrigeration options, offices, kitchens, temporary workplace housing, and mobile health clinics.