Automation: The Future for Offsite Modular Construction
Making the switch to automation is a big step for offsite modular construction companies. But it’s a necessary one if they want to succeed moving forward. Brave Control Solutions Inc. specializes in building customized automated solutions for offsite modular construction. It’s been Vice President Cooper Lane’s focus for the last seven years, and he’s developed a comprehensive roadmap to automation to guide customers to the best option to fit their needs now and in the future.

Automation of framed walls and post processing including drywall installation.
You could say manufacturing is in Cooper Lane’s DNA. Lane, vice president at Brave Control Solutions, grew up in Windsor, Ontario, an “automotive hotbed” with proximity to automotive suppliers and assembly plants from Windsor to Detroit. His family owns a stamping operation that supplies the automotive industry.
Upon graduating from the University of Windsor with honors, Lane looked for a position outside of the family business and wanted to be in more a of a job shop environment. He landed at a Tool and Die shop in the London, Ontario area. Here, while serving as operations manager, he discovered his love for sales.
In 2012, Lane accepted a position as vice president of sales and engineering with a Windsor-based structural steel fabricating company.
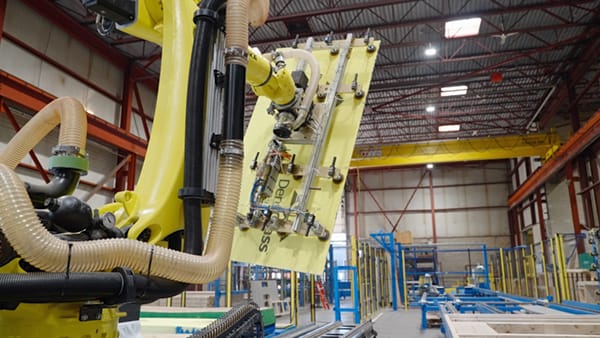
Lane’s sales efforts with the fabrication company helped diversify its client base to include aerospace, power generation, and defense work. He was first exposed to the offsite modular construction market when they were awarded a contract to build automated equipment for Z Modular. To complete the project, he partnered with Brave Control Solutions, a controls expert. It was a fortunate pairing for Lane.
When the project came to an end, Lane moved over to assume the role as Vice President of Sales with Brave Control Solutions.
Making the Move to Offsite Modular Construction
That was in July 2020 when COVID made it impossible to conduct face-to-face meetings. For the first six months, Lane and his team scheduled four to six virtual meetings per week.
“That wouldn’t have been possible if it weren’t for the acceptance of virtual meetings,” Lane said. “It was a big silver lining for us to have the reach and the impact that we did during those challenging times.”
Established in 2008, Brave designed and delivered automation solutions, primarily to the automotive industry. In 2017, it began the transition to the offsite modular construction sector, when it was approached by Z Modular. Over the last seven years, offsite modular construction has been Brave’s primary focus.
Today, Brave is a leader in customized automation for the offsite modular construction sector, which is 90% of its customer base. Now, potential customers often contact Brave to learn more about what the company can do.
"I’d like to think we’re seen as a company that’s driving more modern means of manufacturing,” Lane said. “We’re a leader in the space of custom automation, someone that brings a fresh set of eyes on how things might be able to be done better moving forward.”
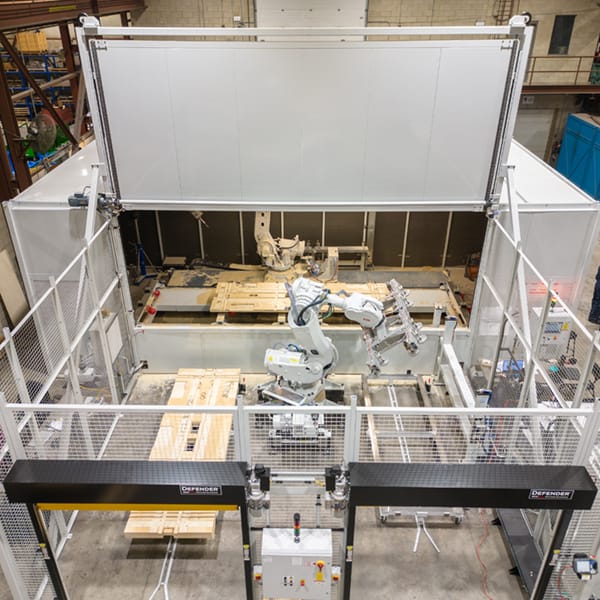
Custom CNC machining cell for mass timber for Intelligent City in Vancouver, BC.
Built-in Flexibility with CAD2FAB™
The beauty of automated equipment is the efficiency, speed, and precision with which it makes the same part repeatedly. Introducing variables to the product after the machine is built can be difficult, even impossible. “We were in our first project, and we started to realize that the amount of product variability in offsite construction doesn’t bode well with conventional automation,” Lane said. “We knew customers had to have some way to change the machine after it was delivered to their floor.”
That’s how CAD2FAB software, Brave’s invention for the offsite modular construction space, was born. CAD2FAB drives the equipment and allows the owner to reprogram it within minutes. For example, the frame sizes for offsite wall panel framing production can be customized to meet the owner’s current needs.
“CAD2FAB is built into the machines and eliminates the need for retooling, reteaching, and retouching,” Lane said. “Flexibility is now embedded in every machine we make.”
That said, Lane explained that Brave is a systems integrator and inventing new technology is not typically their repertoire. “We’re not looking to develop new technologies,” Lane said. “We’re looking at technologies being used in other industries and crossing those technologies over to offsite construction to make our customers more efficient.”
Why Automate?
“Coming into modular construction, it was a huge eyeopener for us to discover that a lot of the technology we were used to seeing on a regular basis, wasn’t present there,” Lane said.
Offsite modular construction lags far behind other industries in embracing and adopting automation. Some people believe it will decrease jobs. Others feel they’ve done okay without it, so why change? In reality, conventional construction methods simply cannot keep up. Lane points to the labor shortage and the housing crisis that’s rampant in Canada, the U.S., and globally.
“Unlike the automotive industry, there’s been no focus on using more technology to build houses better, faster, and cheaper,” Lane said. “We believe that automation can be at the heart of that.”
Although automation can’t transform a company into a “lights out” operation, with everything automated, when implemented properly, automation can increase productivity, reduce costs, and improve safety—a huge concern for construction companies.
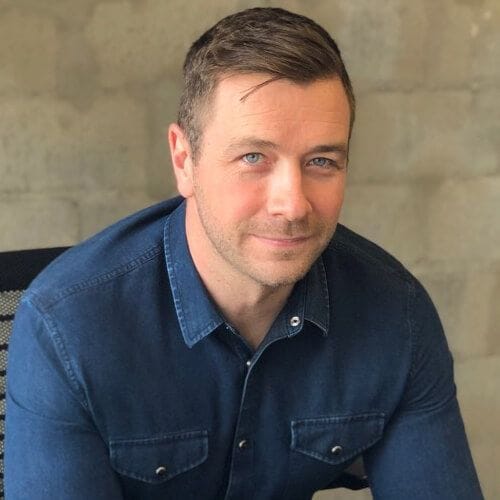
Talking Automation at the 2024 World of Modular
Cooper Lane, Vice President of Sales, Brave Control Solutions
Building a business case around automation will be the major emphasis of Cooper Lane’s presentation. It will appeal to offsite modular builders, investors, or anyone interested in bolstering productivity at their facilities.
After the session, attendees should understand what efficient automation will mean for their operation and how it can easily be justified.
“Certain aspects of offsite construction are prime for the application of automation and certain processes and applications are a better fit for a manual process,” Lane said.
The shortage of skilled labor is another reason to consider automation. Some of those jobs could be automated and an employee trained to operate the equipment. “If automation is implemented properly, it empowers employees,” Lane said. “It drives the operation so it is more successful.”
Related Listening:
Design for Automated Modular Manufacturing w/ Brave Control Solutions
In this episode of Inside Modular, Brent McPhail, founder and CEO of Brave Control Solutions, returns to discuss the current state of automation within the modular construction industry and what lies ahead as both designers and manufacturers embrace the benefits and challenges of modular automation.
The Onboarding Process and Beyond
Brave has a comprehensive process for helping potential customers understand what automation is capable of and their options. Potential customers complete an automation questionnaire to gather basic information prior to the onsite visit.
Brave starts by getting an understanding of their customer’s unique need. Most of the time a facility visit is conducted to better understand a company’s process, its pain points, local labor situation, and whether technology already exists that can improve the company’s productivity. Brave doesn’t build off-the-shelf solutions. All automation is customized to the customer’s needs, wants, budget, and situation.
“One of the biggest services we provide is a roadmap to automation,” Lane said. “If a customer has a limited budget, but wants to begin modernizing, we’ll find a solution that fits their budget to get them started.”
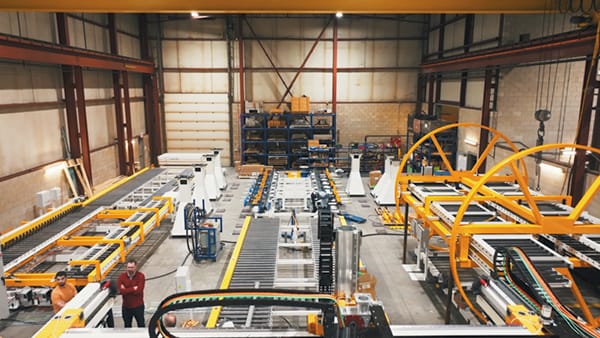
Automated panel assembly and processing cell for Boxabl in Las Vegas, Nevada.
The process is one of collaboration and partnership. “What sets us aside in this space, besides the production systems we design and build, is we offer a high standard of service,” Lane said. “And we want our customers to become accustomed to it and to expect it, moving forward.”
Brave has learned many lessons over the years, such as machine operators need to be trained and ready to go before the machines hit the floor. The company works with customers’ human resources teams to help them understand the skillsets necessary for machine operators. Once the machine is up and running, customer employees can get a head-start on training at Brave, plus continued training once the equipment is installed at their plant.
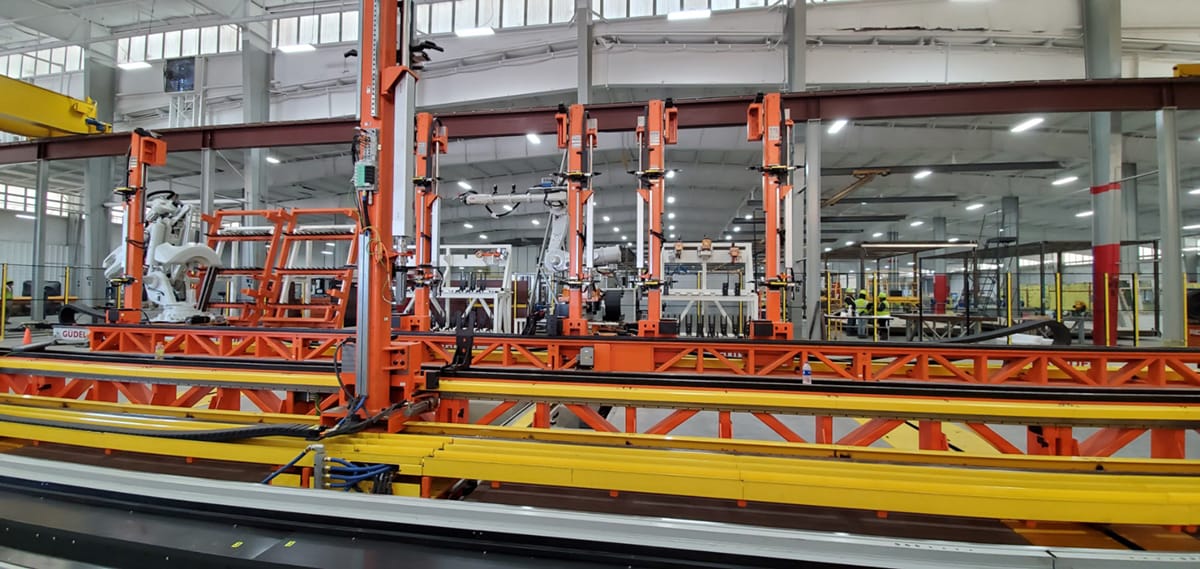
Automated steel fabrication cell for Z Modular at multiple plants across North America.
Customers are always welcome to visit during fabrication to see how their machines are built. Familiarity with that process helps them better understand maintenance issues. Brave also offers production support, both remote and onsite, to ensure the equipment runs continuously.
Brave can also provide an ROI analysis to project when the equipment will pay for itself, allowing the company to create sound business plans around their capital expenditure.
“We’ve learned a lot from the offsite construction industry. We have domain knowledge in this space that, when combined with our automotive background, will lead to game-changing solutions moving forward,” Lane said.
Lane said offsite modular construction companies need to realize that once automation is introduced, it’s not going to be “business as usual.” Change will be necessary for it to be successful. They also need to ensure that whomever they turn to for automated equipment, it will be a partner that helps them understand how to run the machines efficiently.
Brave has several large projects currently underway. The company has, to date, finished multiple retrofits on wall panel and truss machines for building component manufacturers across North America. They have a panel assembly and machining cell on the go for Boxabl, an ADU manufacturer based in Las Vegas, Nev. Also on the books, is building floor, ceiling, and wall automation equipment for a Canadian volumetric modular construction company and working with a mass timber company on the West Coast of Canada.
About the Author: Shari Held is an Indianapolis-based freelance writer who has been covering the construction industry for more than 20 years.
More from Modular Advantage
AI, Faster Sets, and Automation: The Future of Modular is at World of Modular
While the modular building industry has long known that it can be an effective solution to increase affordable housing, the word is slowly spreading to more mainstream audiences. Three presentations at this year’s World of Modular in Las Vegas hope to provide insight and direction for those seeking a real solution to the crisis.
An Insider’s Guide to the 2025 World of Modular
The Modular Building Institute is bringing its global World of Modular (WOM) event back to Las Vegas, and with it comes some of the industry’s best opportunities for networking, business development, and education. Over the course of the conference’s four days, there will be numerous opportunities for attendees to connect, learn, and leverage event resources to get the most out of the conference.
Affordable Housing Now: The Industry’s Best Bring New Solutions to World of Modular
While the modular building industry has long known that it can be an effective solution to increase affordable housing, the word is slowly spreading to more mainstream audiences. Three presentations at this year’s World of Modular in Las Vegas hope to provide insight and direction for those seeking a real solution to the crisis.
Opportunities for Innovation in Modular Offsite Construction
Modular Offsite Construction has already shattered the myth that it only produces uninspired, box-like designs. Architectural innovations in module geometry, configurations, materials, and products make it possible to create visually stunning buildings without sacrificing functionality or efficiency.
Safe Modular Construction with Aerofilm Air Caster Transport
In collaboration with Aerofilm Systems, Heijmans developed innovative skids using air caster technology for moving modules easily and safely. These pallets are equipped with an auto-flow system, making operation extremely simple.
Miles, Modules, and Memes: Building a Modular Network One Flight at a Time
At the end of the day, social media is just another tool for building connections, and like any other tool, needs to be used skillfully to work properly. Use social media thoughtfully, and it will open doors to real opportunities and relationships you didn’t even see coming.
Falcon Structures: Thinking Inside the Box
Some of Falcon’s latest projects include creating container solutions for New York’s Central Park and an East Coast professional baseball team. More and more, Falcon is shipping out container bathrooms and locker rooms to improve traditionally difficult work environments, like those in oil and gas or construction.
UrbanBloc—From Passion to Industry Leader
UrbanBloc specializes in three main categories or markets – what they call “Phase 0” projects, amenities, and urban infill. Clients are often attracted to shipping containers because from a real estate perspective they are considered an asset. Having the flexibility to move and transport these assets allows owners to respond to different circumstances in a fluid manner that they can’t get with standard construction.
The Hospitality Game-Changer
“Hospitality is about more than just providing a service – it’s about delivering an experience,” says Anthony Halsch, CEO of ROXBOX. “And that’s where containers thrive. They allow us to create spaces that are unique, efficient, and sustainable.”
Container Conversions Counts on Simplicity to Provide Critical Solutions
Container Conversions has fabricated and developed thousands of containers for varied projects, including rental refrigeration options, offices, kitchens, temporary workplace housing, and mobile health clinics.