Offsight’s Digital Certification Program Can Accelerate Modular Industry Growth
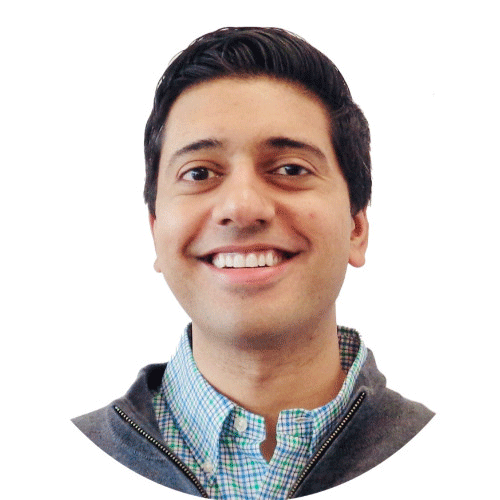
Vikas Murali is the CEO & Co-Founder at Offsight
When it comes to modular and offsite construction the benefits and advantages are widely known and accepted. Industry analysts have forecasted that the traditional construction value chain is ripe for disruption and a $256 Billion annual profit pool can be accessed by new offsite and modular businesses.
Analysis by McKinsey & Company already confirms that modular techniques accelerate construction timelines by 20 to 50 percent and can reduce overall costs by 20 percent. The benefits of modular construction over traditional methods are obvious and include faster project delivery, reduced overall project cost, and far greater overall project quality excellence. However, in the same analysis the authors directly address the key factors that must be addressed to accelerate modular adoption:
“The benefits of modular buildings come from the industrialization of key construction tasks. Modular companies aim to standardize, streamline, and automate big parts of the value chain, allowing buildings to be treated like products rather than projects. To get that right, modular players need best-in-class manufacturing capabilities, including sophisticated digital design platforms and lean, efficient production lines.”
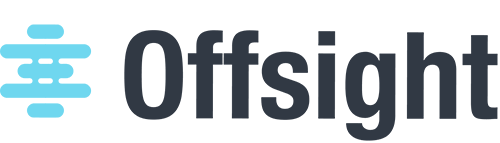
In other words, simply moving work from a traditional job site into a factory doesn’t ensure that the true benefits of modular and offsite construction including speed, cost savings, and quality excellence are achieved. In order to truly realize the return on investment of offsite construction, companies must run a highly efficient manufacturing and production process. Investing in digitization and training your workforce to capitalize on the move to modular will be the key to truly harnessing the full potential and value add of offsite construction.
Going Digital, Getting Certified & Capturing The Full ROI of Modular Construction
At Offsight, we’ve built a solution specifically for the modular, offsite, and prefab industry. Our platform is robust enough to manage all forms of building project manufacturing over the full scope of prefab and modular product lines, from fully volumetric modules and bath pods to panels, trusses, and floor cassettes.
By developing a solution specific to the needs of the industry, we meticulously considered each aspect of managing a modular and prefab project at the factory level and built a full feature set to address the entire scope of factory operations. This includes Production & Quality Tracking, Reporting & Auditing, Advanced Analytics & Insights, Labor Tracking & Timesheets and Materials & Inventory Management.
To achieve the full potential from Offsight, our customers needed to drive adoption internally through educating their workforce and developing internal champions to learn our platform and train others. After witnessing our most successful modular customers deploy and expand our solution to their other factories successfully, Offsight was able to track progress and quality across several major commercial projects in parallel. We incorporated these insights into a digital certification and training program curated to foster shared knowledge among industry leaders within our customer base.
Related Listening:
The Value-Add of Offsite Construction Project Management Software w/ Offsight
Vikas Murali, CEO of Offsight, discusses the advantages that offsite factory owners and manufacturers can realize through the use of customized project management software. Vikas also talks about the development and capabilities of his company's Offsight software platform, as well as about how his background in enterprise-level software development—combined with the modular and offsite industry experience of his key staff—has led to Offsight's growth as an industry software solution.
To achieve the full potential from Offsight, our customers needed to drive adoption internally through educating their workforce and developing internal champions to learn our platform and train others. After witnessing our most successful modular customers deploy and expand our solution to their other factories successfully, Offsight was able to track progress and quality across several major commercial projects in parallel. We incorporated these insights into a digital certification and training program curated to foster shared knowledge among industry leaders within our customer base.
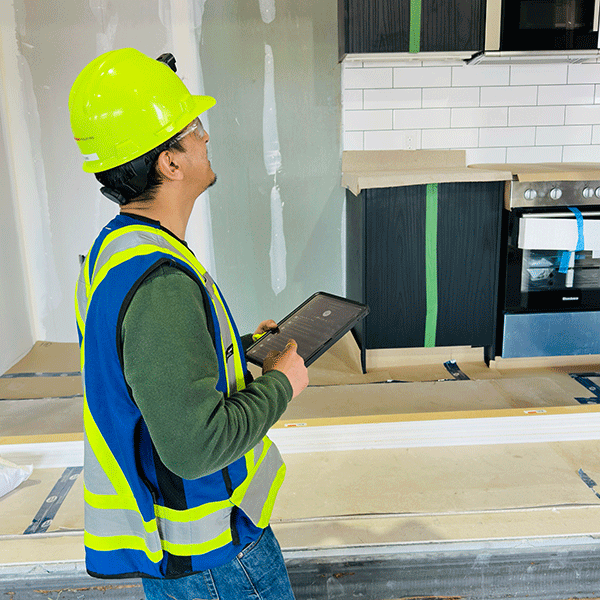
Commercial modular builder Z Modular utilizes Offsight to manage projects across multiple factories in the U.S. and Canada.
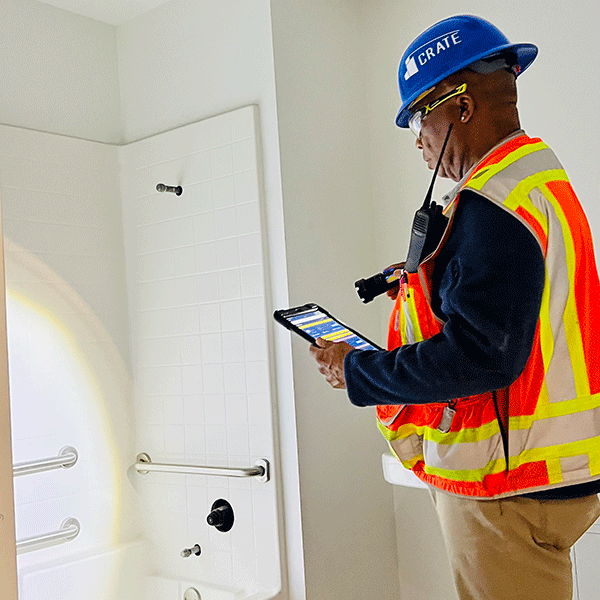
Multifamily residential builder CRATE Modular, leverages Offsight to manage full factory operations and production.
Therefore, we launched the Offsight Certification Program in January 2024. Our program is designed to equip production managers, quality inspectors, plant managers, and operators with a deeper understanding of how technology and digitization can be a game-changer in driving process improvements and productivity benefits, which will ultimately allow our customers to capture the full value of modular and offsite construction.
As Offsight Solutions Engineering Manager, Jason Dixon states: “Before joining Offsight, I held quality manager and operations roles at modular manufacturing companies. It was my responsibility to implement Offsight across our workforce of 50+ operators and managers. My biggest takeaway was the importance of training a technical lead responsible for learning how Offsight works and the value it can provide the factory. Our Offsight Certification Program will enable our clients to better train and recognize these internal leads and drive technological changes throughout the company.”
Our program consists of two major certifications that help operators, managers, and inspectors apply digitization to all aspects of factory operations. The Offsight Factory Operations Project Management Certification trains modular industry leaders in leveraging Offsight’s production, quality, analytics, and material and labor tracking capabilities to manage overall prefab project progress, collaborate with other project stakeholders, and accurately manage project costs. The Offsight Digital Quality Building Inspections Certification is designed to help quality personnel, managers and accredited building inspectors leverage digitization to manage complex code conformance and tracking, including mandatory and State-regulated reporting and auditing.
Through both programs, modular professionals learn how digitization can be a game-changer in driving modular construction adoption and delivering on the innate benefits the process offers.
As Offsight customer, Keizah Coye, Plant Project Manager at CRATE Modular, states: “As a production leader, I interact with Offsight daily. It’s a very robust solution that helps manage all factory operations and provides crucial visibility to our management. Their Certification and training program is exactly what production leaders in the modular, offsite, and prefab industry, like myself, need to quickly get up to speed on how Offsight’s technology can be utilized to meet our major operations and project goals and scale our business.”
At Offsight, our vision is to be the leading provider of digital tools and products that empower companies to unlock the complete potential of modular and offsite construction. We invite you to join us on this journey and hope that we can partner with you to help push the industry forward.
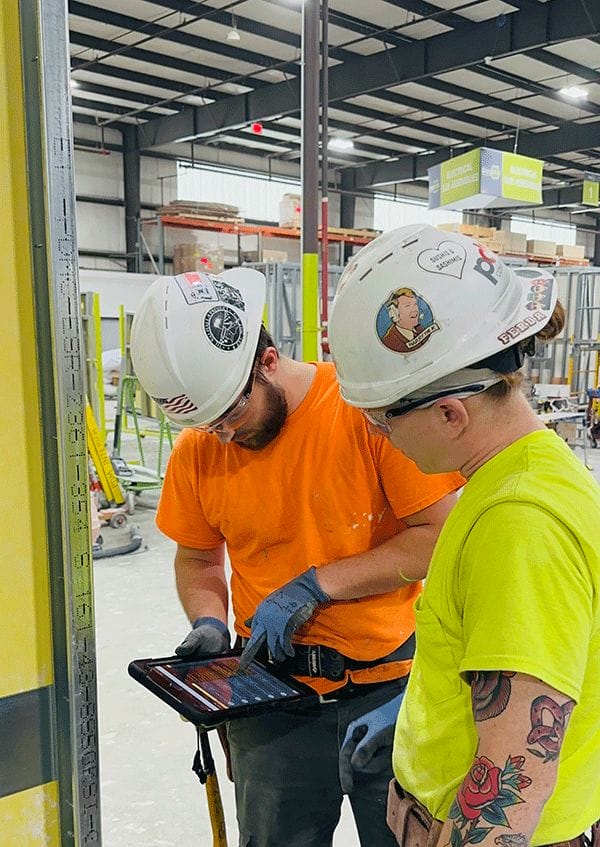
Specialty contractor PDM Constructors manages production across thousands of modular bath pods for major healthcare projects, through Offsight.
More from Modular Advantage
AI, Faster Sets, and Automation: The Future of Modular is at World of Modular
While the modular building industry has long known that it can be an effective solution to increase affordable housing, the word is slowly spreading to more mainstream audiences. Three presentations at this year’s World of Modular in Las Vegas hope to provide insight and direction for those seeking a real solution to the crisis.
An Insider’s Guide to the 2025 World of Modular
The Modular Building Institute is bringing its global World of Modular (WOM) event back to Las Vegas, and with it comes some of the industry’s best opportunities for networking, business development, and education. Over the course of the conference’s four days, there will be numerous opportunities for attendees to connect, learn, and leverage event resources to get the most out of the conference.
Affordable Housing Now: The Industry’s Best Bring New Solutions to World of Modular
While the modular building industry has long known that it can be an effective solution to increase affordable housing, the word is slowly spreading to more mainstream audiences. Three presentations at this year’s World of Modular in Las Vegas hope to provide insight and direction for those seeking a real solution to the crisis.
Opportunities for Innovation in Modular Offsite Construction
Modular Offsite Construction has already shattered the myth that it only produces uninspired, box-like designs. Architectural innovations in module geometry, configurations, materials, and products make it possible to create visually stunning buildings without sacrificing functionality or efficiency.
Safe Modular Construction with Aerofilm Air Caster Transport
In collaboration with Aerofilm Systems, Heijmans developed innovative skids using air caster technology for moving modules easily and safely. These pallets are equipped with an auto-flow system, making operation extremely simple.
Miles, Modules, and Memes: Building a Modular Network One Flight at a Time
At the end of the day, social media is just another tool for building connections, and like any other tool, needs to be used skillfully to work properly. Use social media thoughtfully, and it will open doors to real opportunities and relationships you didn’t even see coming.
Falcon Structures: Thinking Inside the Box
Some of Falcon’s latest projects include creating container solutions for New York’s Central Park and an East Coast professional baseball team. More and more, Falcon is shipping out container bathrooms and locker rooms to improve traditionally difficult work environments, like those in oil and gas or construction.
UrbanBloc—From Passion to Industry Leader
UrbanBloc specializes in three main categories or markets – what they call “Phase 0” projects, amenities, and urban infill. Clients are often attracted to shipping containers because from a real estate perspective they are considered an asset. Having the flexibility to move and transport these assets allows owners to respond to different circumstances in a fluid manner that they can’t get with standard construction.
The Hospitality Game-Changer
“Hospitality is about more than just providing a service – it’s about delivering an experience,” says Anthony Halsch, CEO of ROXBOX. “And that’s where containers thrive. They allow us to create spaces that are unique, efficient, and sustainable.”
Container Conversions Counts on Simplicity to Provide Critical Solutions
Container Conversions has fabricated and developed thousands of containers for varied projects, including rental refrigeration options, offices, kitchens, temporary workplace housing, and mobile health clinics.