26 Stories in 5 Days - How BROAD Sustainable Building is Redefining the Speed of Modular
On January 7, 2024, BROAD Sustainable Building began assembling the new 26-story mixed-use Jindu Residential Tower. On January 11, just five days later, construction was completed.
But for BROAD, this was just another day at the office.
In fact, the Jindu Residential Tower represents the 16th generation of BROAD’s Holon Building concept, a modular construction design that uses foldable, container-sized units that BROAD first started developing nearly 15 years ago.
“BROAD Sustainable Building was founded in 2009,” said Jeremy Zimman, Director of Marketing, Holon Modular Building Systems at New Jersey-based BROAD USA, “in response to a large earthquake that happened in China in 2008, close to where our parent company, BROAD Group, is based. There were tens of thousands of people who lost their lives. Our chairman and founder saw that these buildings made of concrete were falling like dominoes, so he resolved to make more durable steel buildings.”
And while the use of steel wasn’t exactly revolutionary, BROAD’s embrace of stainless steel is.
“We transitioned to stainless steel about five years ago,” said Zimman, “because we realized the mechanical properties of stainless included not only non-corrosion, which is good for facades, but stainless steel also has a great ductility—the ability to withstand tensile stress. That's the reason we chose stainless for our load-bearing members. We're the first to do that.
“So now,” continued Zimman, “even though our volumetric product is just two years old, we’ve been in a continuous state of innovation. For instance, in the first Holon building that we built two years ago, the beams had to be put in on site. And now, when we lower the modules, the flooring system of those modules have the beams built in. So, there's no welding on site. It's only bolting. We have the cranes ready; we just pick and place, stack, bolt, connect utilities, and we're good to go.”
“Our building is turnkey,” said Zimman. “When construction is over, it's move-in ready. It includes all the fixtures like air conditioning, our own ventilation system—energy-recovery ventilation, which is a principle of Passive House—that’s included. Even water tanks are in place.
“The only thing not included is movable appliances. Refrigerators, washers, dryers, dishwashers, microwaves; other than those appliances, the building is ready to occupy.”
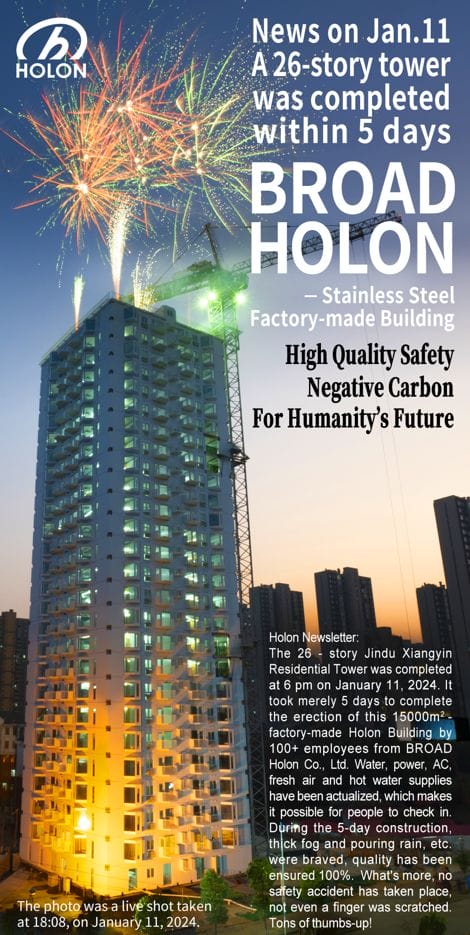
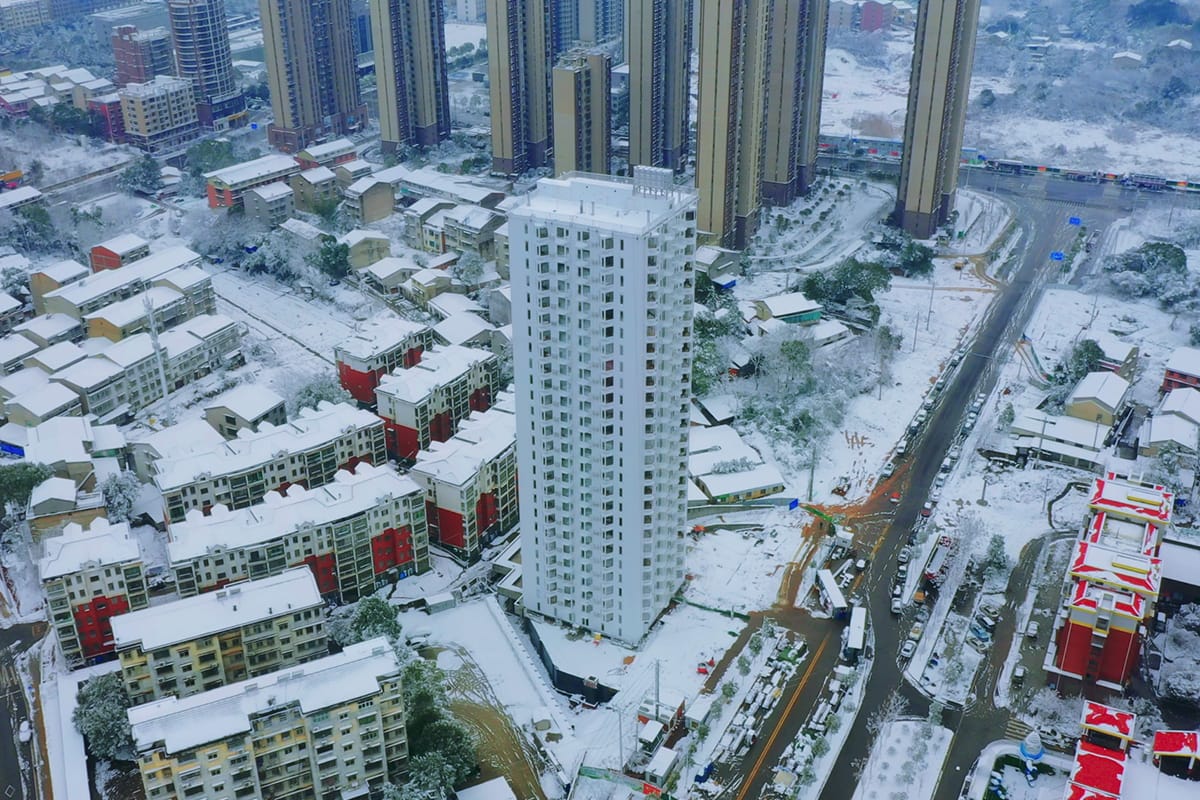
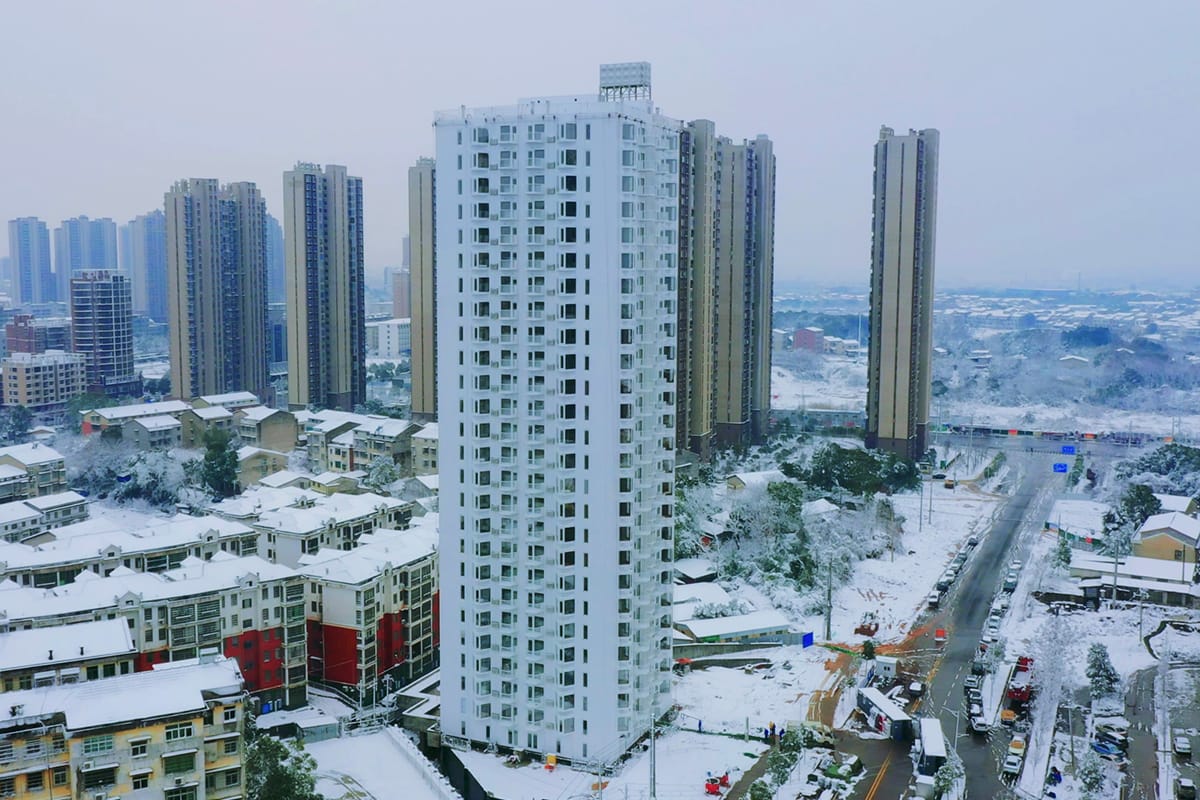
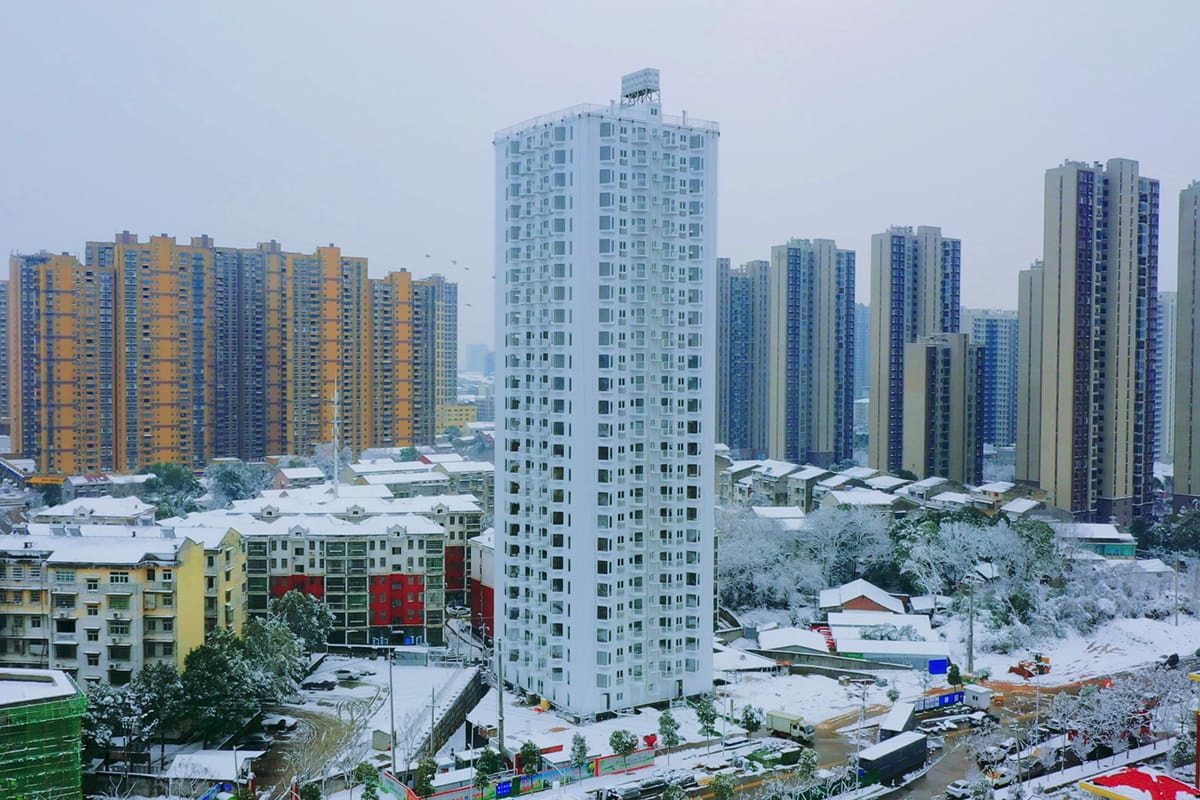
The Jindu Residential Tower was assembled in just 5 days by BROAD Sustainable Building.
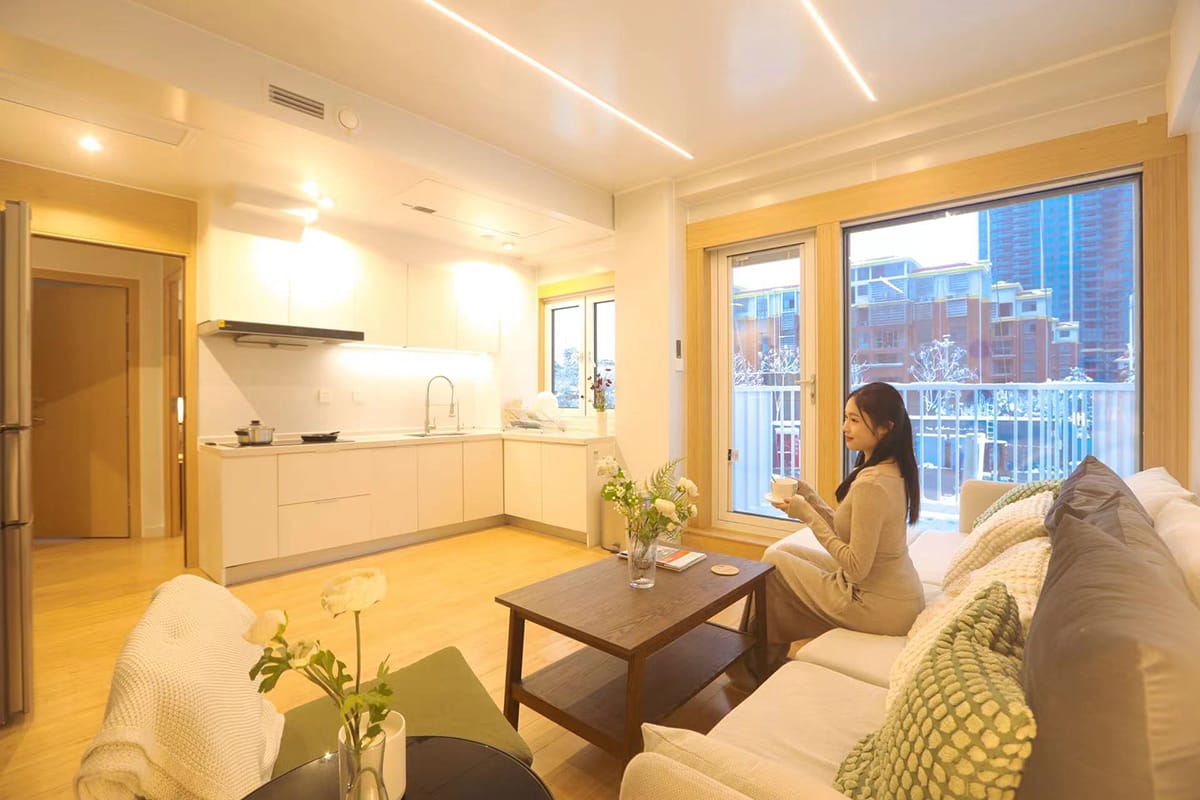
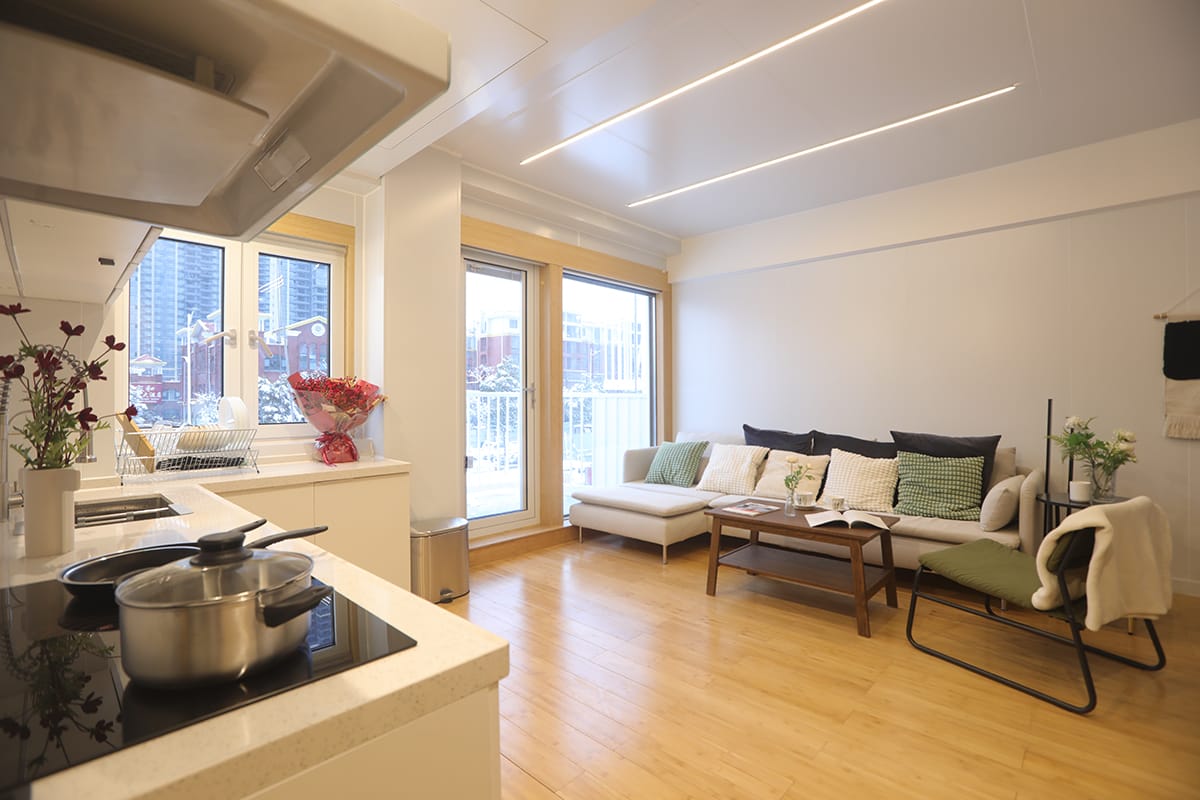
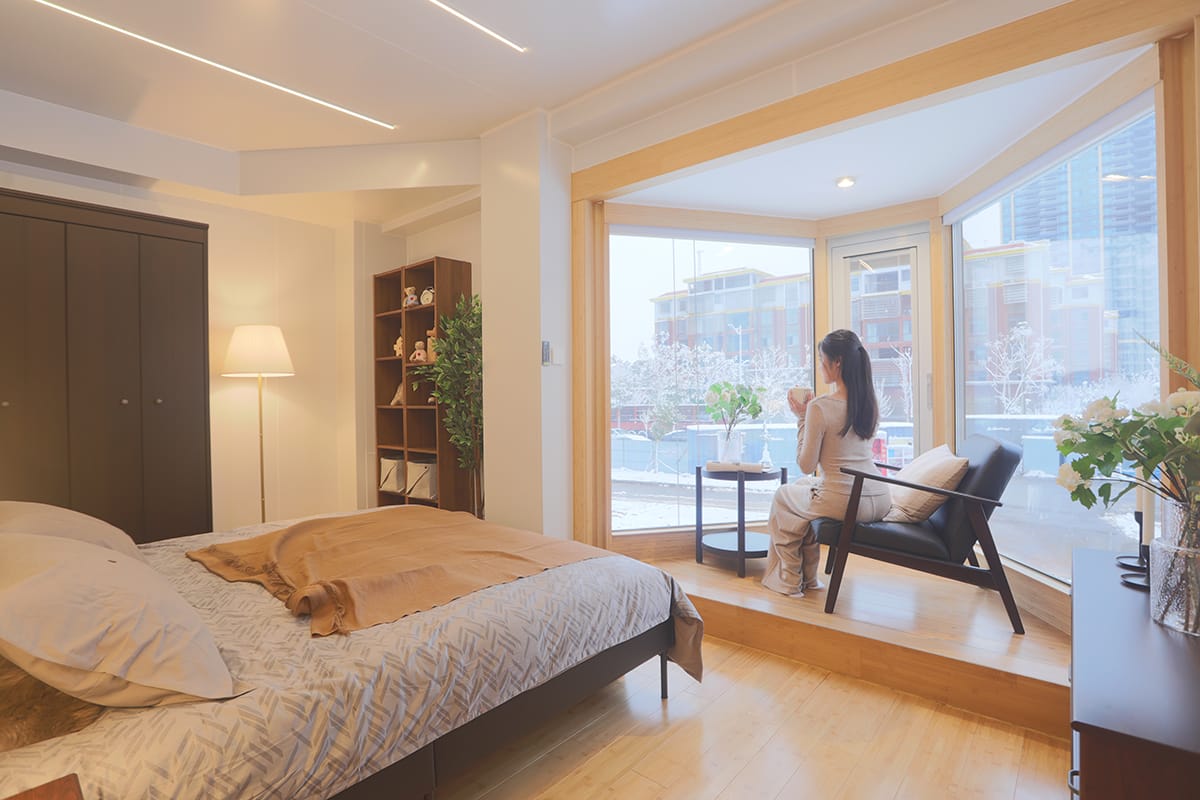
After the 5-day assembly was complete, the building was move-in ready; the only things missing were the appliances.
The Importance of B-CORE
BROAD’s patented B-CORE flooring system is the key to these efficiencies. It is a sandwich structure brazed in a special oven at 2000 degrees, which enhances the inherent mechanical properties of stainless steel. One 40x8 B-CORE "slab” can be produced every two minutes.
“The Jindu Residential Tower has 264 modules, which are all either a room module or a lift module. And because the walls in the Holon Building aren’t load-bearing, we’re able to configure the room modules flexibly. That enables us to produce a very small number of physical module types, and to crank them out at high volume. And that keeps our costs relatively low. So, even though we're using stainless—which is not the lowest cost material—we gain economy of scale through very high volume production.”
Related Reading:
B-CORE: The Modern Material from BROAD
“B-CORE is composed of two stainless steel plates with an array of stainless steel tubes fused between them,” says Sunny Wang, General Manager at BROAD USA. “Copper foil is fused to the stainless steel base material during brazing. Because the metals have different melting points, they can stick together very strongly. It looks very simple, but it’s super-light and super-strong.”
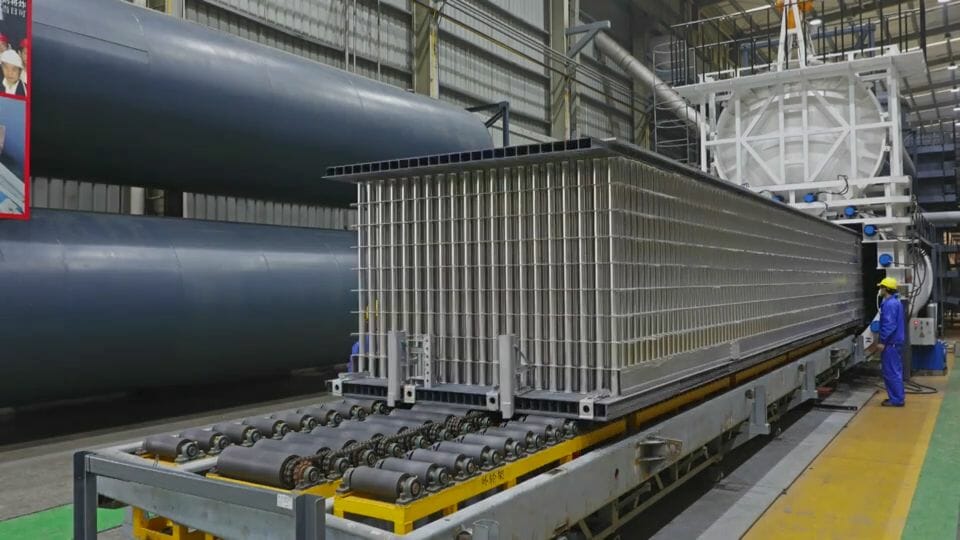
Production, Construction, and Logistics
BROAD’s latest project utilized 100 individual builders working alternating shifts, plus one mobile crane and one tower crane. But despite the constant onsite activity, BROAD’s Holon builds go up quickly and smoothly thanks to the predictable, standardized nature of the building’s components and the efficiency of their production.
“For this project,” said Zimman, “the logistics were relatively simple because the building is going up not far from our factory. But wherever we build, we can utilize a standard flatbed truck. We designed the modules to the size of a standard 40-foot-long shipping container for easy global transport, maritime and on land. So, we can go across any jurisdiction in the US, for instance, on a flatbed.
“Another critical factor in our logistics is the capacity of our factories. We’ve streamlined our production to the point where we can easily produce each module in 21 minutes.”
BROAD livestreamed the building's complete onsite assembly on YouTube.
Looking Ahead
Twenty-six stories may seem like a lot for a modular building, but the plan, eventually, is to go much higher. “There is actually no limitation for the height,” says Sunny Wang, President of BROAD USA, “because we take advantage of the stainless steel. It's strong enough that we can go as high as we can design it.”
With the proverbial wind at its back, it’s only a matter of time before BROAD’s Holon buildings are seen far and wide. And besides their upcoming projects in China, the Philippines, and the UAE, plans are also in place for Holon Buildings in the Unites States.
“The Holon modular system enables the construction of tall residential buildings at great speed, and we look forward to deploying this technology to shorten the construction cycle and alleviate the severe housing shortage in the U.S. and Canada,” concluded Zimman. “Right now, we’ve got plans in place for Ohio, Texas, and California. As soon as we can say more, we absolutely will.”
About the Author: John McMullen, PCM, is the marketing director for the Modular Building Institute. You can reach him directly at mcmullen@modular.org or on LinkedIn.
More from Modular Advantage
AI, Faster Sets, and Automation: The Future of Modular is at World of Modular
While the modular building industry has long known that it can be an effective solution to increase affordable housing, the word is slowly spreading to more mainstream audiences. Three presentations at this year’s World of Modular in Las Vegas hope to provide insight and direction for those seeking a real solution to the crisis.
An Insider’s Guide to the 2025 World of Modular
The Modular Building Institute is bringing its global World of Modular (WOM) event back to Las Vegas, and with it comes some of the industry’s best opportunities for networking, business development, and education. Over the course of the conference’s four days, there will be numerous opportunities for attendees to connect, learn, and leverage event resources to get the most out of the conference.
Affordable Housing Now: The Industry’s Best Bring New Solutions to World of Modular
While the modular building industry has long known that it can be an effective solution to increase affordable housing, the word is slowly spreading to more mainstream audiences. Three presentations at this year’s World of Modular in Las Vegas hope to provide insight and direction for those seeking a real solution to the crisis.
Opportunities for Innovation in Modular Offsite Construction
Modular Offsite Construction has already shattered the myth that it only produces uninspired, box-like designs. Architectural innovations in module geometry, configurations, materials, and products make it possible to create visually stunning buildings without sacrificing functionality or efficiency.
Safe Modular Construction with Aerofilm Air Caster Transport
In collaboration with Aerofilm Systems, Heijmans developed innovative skids using air caster technology for moving modules easily and safely. These pallets are equipped with an auto-flow system, making operation extremely simple.
Miles, Modules, and Memes: Building a Modular Network One Flight at a Time
At the end of the day, social media is just another tool for building connections, and like any other tool, needs to be used skillfully to work properly. Use social media thoughtfully, and it will open doors to real opportunities and relationships you didn’t even see coming.
Falcon Structures: Thinking Inside the Box
Some of Falcon’s latest projects include creating container solutions for New York’s Central Park and an East Coast professional baseball team. More and more, Falcon is shipping out container bathrooms and locker rooms to improve traditionally difficult work environments, like those in oil and gas or construction.
UrbanBloc—From Passion to Industry Leader
UrbanBloc specializes in three main categories or markets – what they call “Phase 0” projects, amenities, and urban infill. Clients are often attracted to shipping containers because from a real estate perspective they are considered an asset. Having the flexibility to move and transport these assets allows owners to respond to different circumstances in a fluid manner that they can’t get with standard construction.
The Hospitality Game-Changer
“Hospitality is about more than just providing a service – it’s about delivering an experience,” says Anthony Halsch, CEO of ROXBOX. “And that’s where containers thrive. They allow us to create spaces that are unique, efficient, and sustainable.”
Container Conversions Counts on Simplicity to Provide Critical Solutions
Container Conversions has fabricated and developed thousands of containers for varied projects, including rental refrigeration options, offices, kitchens, temporary workplace housing, and mobile health clinics.