For True Modular Building, Sustainability is Part of Yesterday, Today, and Tomorrow
You can’t deny it. Sustainability is built into the bones of this company. For Carel van Duuren, the 71-year-old CEO of True Modular Building, it’s more than just his legacy—he’s thinking about the future of society at large. How do you make things infinitely repeatable and simple? How can you make sure you’re contributing to the economy without adding extra waste or using increasingly precious resources? And how can you do this, and quickly?
These are just some of the questions that Carel thinks about every day. And he wants his Netherlands-based company to answer all of them. True Modular Building is the next stage in Carel’s evolution as an entrepreneur, which started with the volumetric modular and manufacturing industry. His first foray with modular started with developing kitchens for universities, businesses, conventions, and any hosted events in large spaces with his companies NxtGen Industrial and NxtGen Kitchens building systems.
Soon that evolved into demountable professional container kitchens and restaurants for event spaces, which then led Carel to wonder, ‘how can I make this system repeatable for other structures?’ Namely, residential buildings or affordable housing, which remain in huge demand in the Netherlands and elsewhere around the globe.
The amount of CO2 and waste created by construction pushed Carel to envision a new system that deviated from volumetric modular. He wanted to start fresh with a new idea of building residential housing that focused on sustainability, efficiency, affordability, and quasi-vertical control. Over three years of research and iterating led him to develop an entirely new basic building block for modular design, changing his outlook on what residential housing could be.
“I think the future in building is ‘componentized buildings’ and not volumetric buildings,” he said.
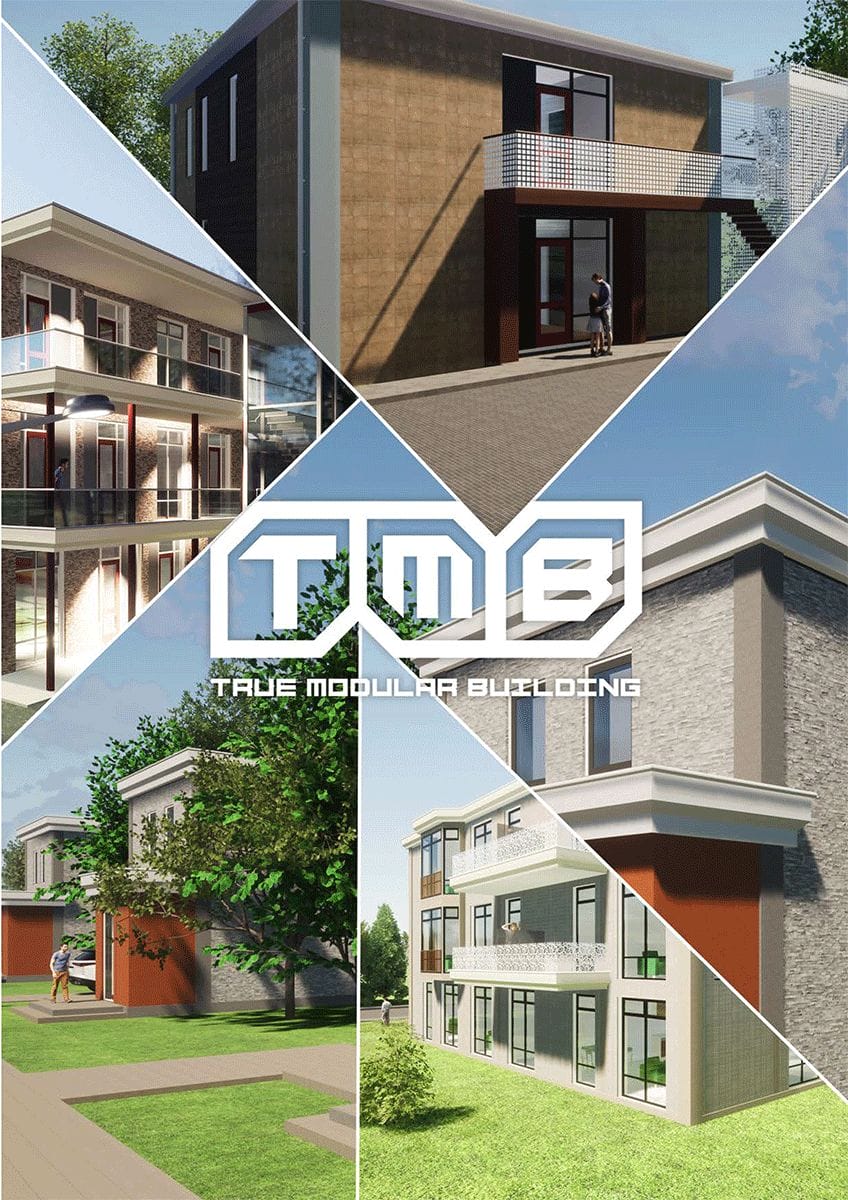
Protecting the Future with TRUE Modular Building
Shifting away from volumetric modular is not just an ideological choice, but a practical application and interpretation of the industry’s future, says Carel. So much so that the word TRUE represents more than its dictionary definition for the company name. With the title True Modular Building (or TMB for short), True stands for “Traceable and Transparent; Resilient and Regenerative; Unique and Universal; Economic and Eco-friendly.”
“I think true modular is the opposite of volumetric modular because modular in itself is also a word that nobody really knows what it means,” said Carel. “And with true modular, let’s say it’s componentized modular. It is not all rocket science, it’s just how you connect all the dots so to say. For instance, look at the evolution of Volkswagen. They have these configurable platforms and they have one chassis and they make a lot of different cars out of it.”
Taking inspiration from car manufacturers, the “Shearing Layers of Change” concept from Steward Brand, and John Habraken’s principles of “Open Building,” TMB created their own adaptable chassis, a skeleton or superstructure, that is load bearing as well. Using this as the base, they have created a structured, sustainable cladding system that can change any number of ways to meet residential housing codes and environmental concerns all around the world.
The cladding system is integral to the building’s resilience, as TMB uses sustainable bio-based insulation to keep buildings warm and soundproof. Additionally, it helps with carbon sequestering, a major concern for any new construction projects.
This insulation also meets the goals of being “resilient” and “eco-friendly.” The construction system is also closed-loop, which means they are also not creating any additional waste.
While modular aims to be efficient, cost-cutting, and easy to build, Carel’s system goes a step further by addressing manufacturing costs and the value of sustainable materials. Which starts with the components.
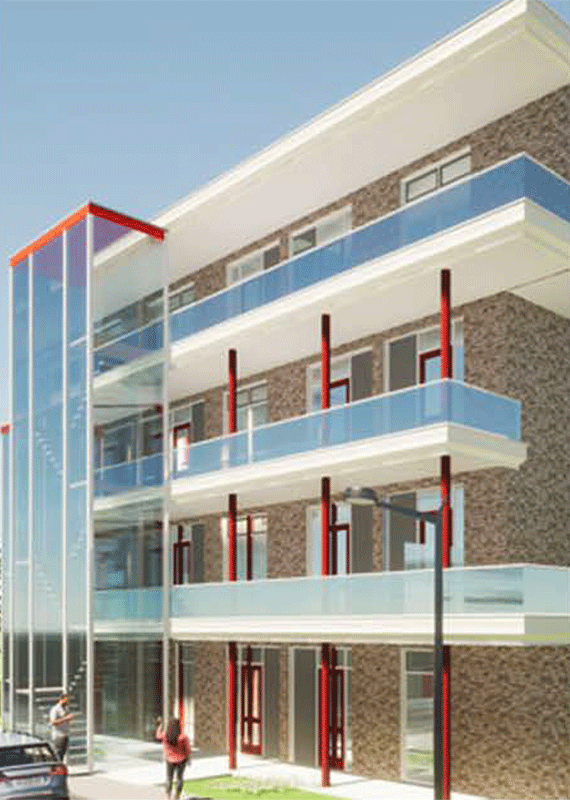
TMB100 - Low- and mid-rise buildings
Low- and mid-rise apartments have studios and 1 to 3-bedroom apartments. They are popular with students, couples, roommates and young families. The size of the apartments varies from 190 to 870 sq ft (approx. 18 - 80m2).
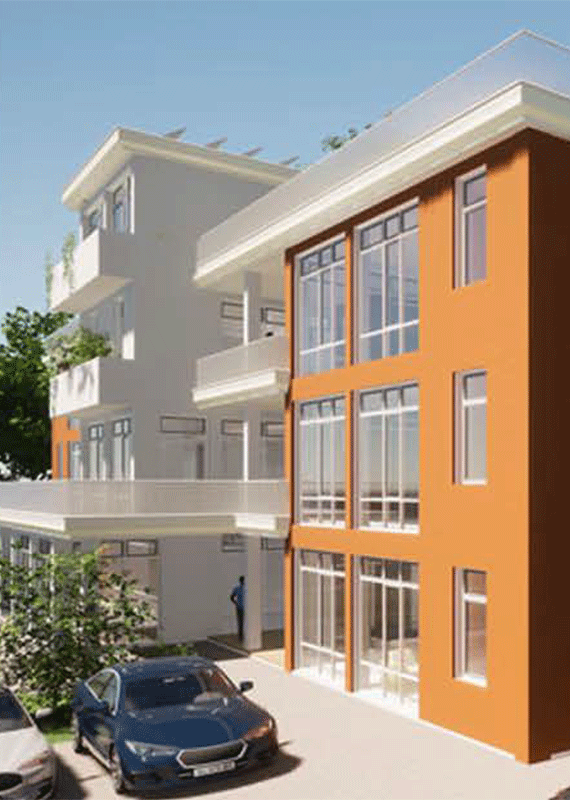
TMB200 - Mixed-use apartments
Mixed apartments consist of studios and 1 to 3-bedroom apartments. They are multifunctional and combine the needs of urban target groups in the areas of living, working, shopping, recreation, and possibly social services.
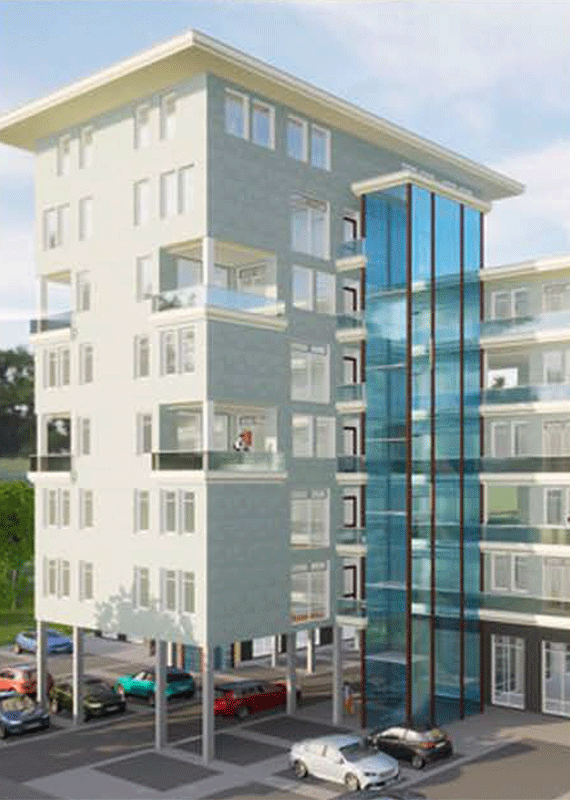
TMB300 - Cluster apartments
Cluster buildings with or without a commercial plint, residents share amenities. The buildings have studios and 1 to 2-bedroom apartments and size from 290 to 680 sq ft (about 27 - 63m2).
Controlling the Quality of the Entire Building Process
So what is “componentized building?” It differs from volumetric building through the creation of joints, compositions, combined parts, built from something even smaller, called primitives, in the TMB system. Once the part is created, it becomes a component. Then design the housing construction with said component through the TMB system.
The closest comparison would be a LEGO block. This block could be manufactured using any type of durable material like steel, bio-based plastics, and anything else that might be usable in the future.
It all depends on the construction location and cost. Clients can choose the most sustainable material that appeals to them and TMB for longevity and ease of repair.
This system relies heavily on “co-makers” as Carel calls them, or partner companies that can help manufacture the primitives. This cuts down on any transportation costs required to build the structure. That is, there are no boats or trucks necessary to move the final project, unlike in other modular building scenarios.
“People build these large factories for volumetric building, but the large factory needs [to receive] a lot of work because otherwise you can’t work efficiently,” said Carel. “So you have a lot of overhead, you have a lot of costs, but if you don’t produce a lot of items, then you never can be profitable.”
Carel wants to address as many pain points as possible when building a residential structure. That means analyzing potential problems related to manufacturing overhead, material costs, construction costs, transportation, ease of repair, climate resilience, and long-term sustainability.
It also makes materials and the whole sourcing process traceable—another core tenet for True Modular Building.
“It’s crucial to control the value chain but also the production chain because a lot of things happen in between,” he said. “I don’t want to own a factory, but I use co-makers who produce our components. It’s like an OEM-type of thinking, so to say.”
It’s also about reducing manufacturing cost through repetition and expansion.
“We can build a lot of different type of houses, but all with the same system, all with the same components,” he said. “So if I order for instance, let’s say a hundred components, I pay one price, but if I order a thousand components, I have a different price. So that is how I think we can lower the price also by having better purchase prices.”
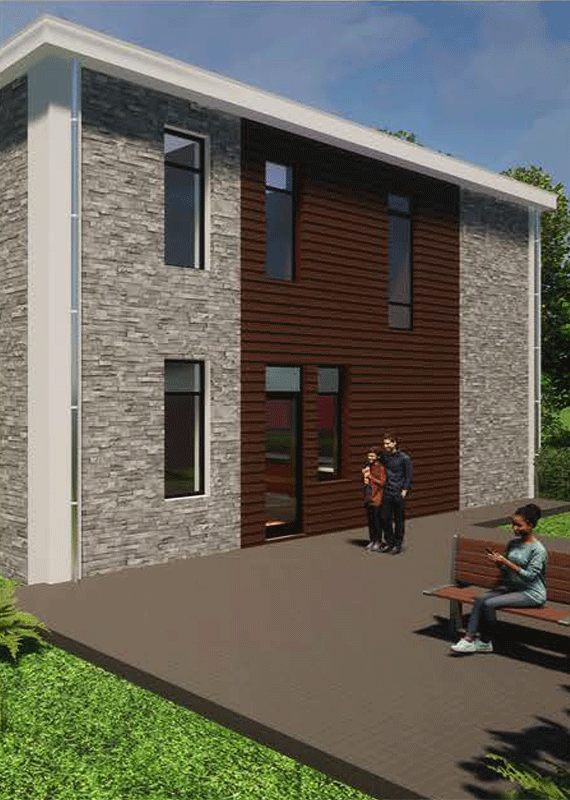
TMB400 - Co-living apartments
TMB offers a range of co-living designs (a student way of living). From 7-unit micro apartments (85 to 160 sq ft/ 8m2 -15m2 ) in which each resident has an own bedroom supplemented by shared amenities like kitchen, toilets, bathroom and living room, to apartment buildings with 20 units (160 to 225 sq ft / 15m2 -21m2) per story with a private bathroom and kitchen where residents share amenities such as living room, garden, laundry room and fitness/entertainment.
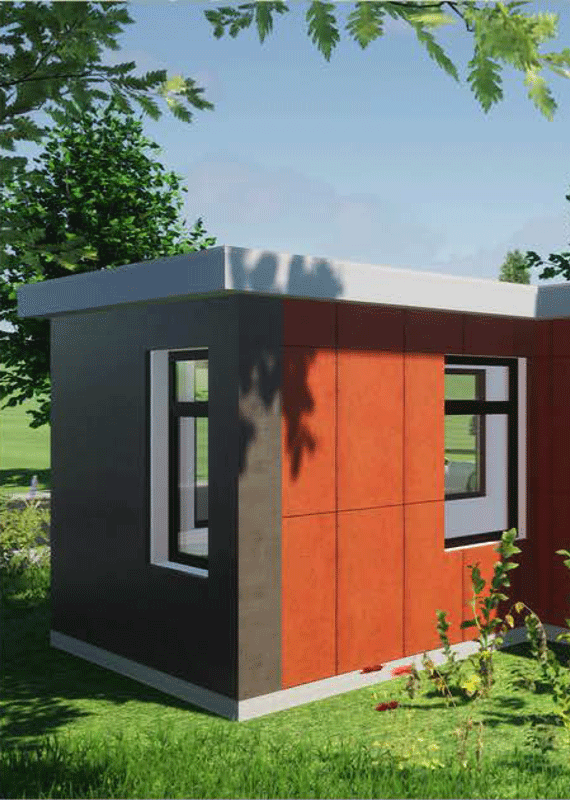
TMB500 - Care homes and apartments
Accessory Dwelling Units (ADUs) and care home apartments are a comprehensive housing solution tailored to cater to the needs of individuals requiring (intensive) care.
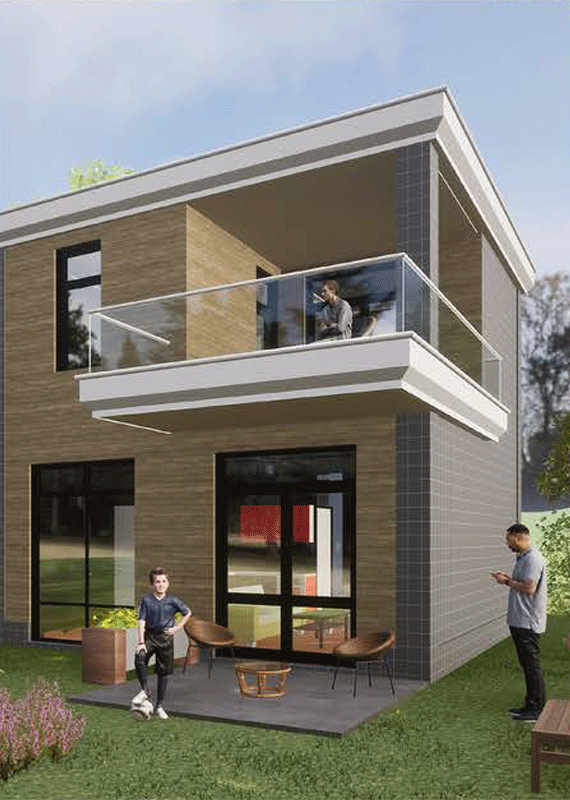
TMB600 - Single and two-story homes
TMB offers a range of 1 and 2-story single-family homes varying in size and number of bedrooms, all with adequate storage space provide flexibility for new couples, (first) families, and retirees. Detached, semi-detached and terraced, optional with balcony or garage. The size of the homes varies between 580 to 1.170 sq ft (about 54 -110m2).
True Sustainability Met Through the “Orange Kit”
As part of TMB’s goal to be repeatable and efficient, they have launched what they call the “Orange Kit,” which is traditional pre-manufactured modular construction but even more simplified. Imagine IKEA but for buildings.
The Orange Kit provides agility and flexibility for those who want to make changes to the residential structure down the line. With TMB providing co-ownership, Carel makes sure that these houses continue to meet sustainability and affordability values. Currently, with the use of the Orange Kit, TMB has created a product catalog of at least 60 different configurations—all using the same skeleton. The only differences? The floor plans and materials in components and cladding.
Building codes are still a little ways behind. Carel has already seen the future of modular using other construction materials, such as bio-based plastics made from potatoes. It’s a far cry from chopping down large forests.
“I am calling this my legacy project and I am much into creating affordable living, but also into making planet friendly buildings,” said Carel. “I use all bio-based insulation, not because I have to, but because I want to, because I’m convinced that’s good for our planet.”
A Sustainable Future is Here
TMB’s Orange Kit and componentized buildings are not just things on paper or on a screen. Carel is busy making TMB globally known, launching projects in South Africa, the U.K., and Ireland. So far, the appetite and interest has been high; TMB received a 2023 BUILD Award for Most Innovative Modular Building Company 2023 - Netherlands & Best Sustainable Componentized Building System 2023: Orange Kit.
But it’s not about industry domination for Carel and TMB.
With his contacts around the world, his goal is to start joint ventures to not only establish oversight on the process, but to give partners on the ground “a real stake in what is happening.” A lot of it is just plain business sense, as having eyes and ears on the ground helps with smoothing over any wrinkles and making sure things work according to Carel’s vision. But at its core, TMB is laying out the foundation for residential housing with the local community in mind.
“Three years of testing prototypes of the components resulted in making a live prototype in May 2023. Based on these results I’m sure that we will succeed,” he says. “And of course I have colleagues and I have the younger generation who will follow into my footsteps.”
This also means that by sticking to his values, TMB cannot accept funding from any and all financial institutions. Carel thinks of funding as more of a marriage, rather than a short-term infusion of cash and quick return on investment.
“They only think in terms of five years, in profit, and in return of investment. But I think in wealth creation, in value creation,” he said.
South Africa, U.K., and Ireland are only the first few stops. In 2024, Carel and True Modular Building hope to start building in other countries like Nigeria, Kenya, India, and the U.S. He’s targeted the “Texas Triangle” and Georgia as places to develop new residential buildings.
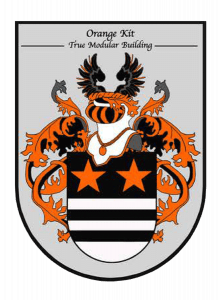
TMB's Orange Kit
“Plug and Play”
Orange Kit (-of-Parts) is a collection of standardized building components that can be arranged and assembled in various ways to create buildings. By breaking down the design into a small number of components, TMB is able to create a repeatable and scalable delivery method for housing. Pluggable connection systems are ideal for sustainable building components that conserve resources. Color coding, further simplifies installation, making the process reliable and error-free.
Simplicity is the future
Modularization enables us to easily assemble, disassemble, expand and adapt components to changing needs. Orange Kit allows reusable and demountable structures to be built, promoting more efficient use of materials and reducing environmental impact.
TMB focuses on efficiency, flexibility and sequestering carbon in design and construction. By delivering prefabricated, easy-to-install “plug and play” components (flat pack) to the construction sites, we created a flexible easy to transport and assemble system to cope with the increasing cost and industry’s labor shortage.
About the Author: Karen P. Rivera is a freelance writer and editor with a passion for storytelling. She is a former United Nations-based reporter, with experience covering international breaking news, venture capital, emerging healthcare tech, and the video game industry.
More from Modular Advantage
Oregon’s Prevailing Wage Proposal: A Wake-Up Call for Modular Construction
In early February, 2024, the Massachusetts Board of Building Regulations and Standards (BBRS) released its proposed 10th Edition building codes. This draft included several amendments targeting modular construction that would have created an extremely difficult environment for the entire modular industry and could have eliminated the industry entirely in the state.
Behind the Design of Bethany Senior Terraces, NYC’s First Modular Passive House Senior Housing Project
As more developers seek to meet new regulations for energy efficiency, the team at Murray Engineering has set a new record. With the Bethany Senior Terraces project, Murray Engineering has helped to develop NYC’s first modular structure that fully encompasses passive house principles — introducing a new era of energy efficiency in the energy-conscious city that never sleeps.
How LAMOD is Using Modular to Address Inefficiency, Sustainability, and the Future of Construction
As developers, designers, and contractors seek to understand the evolving needs of the modular industry, no one is as well-versed in the benefits of going modular as Mārcis Kreičmanis. As the co-founder and CBDO of LAMOD in Riga, Latvia, Mārcis has made it his ultimate goal to address the inefficiencies of traditional construction.
From Furniture Builder to ‘Activist Architect’: Stuart Emmons’ Unique Journey
Stuart Emmons was fascinated by buildings at a young age. He remembers building sand cities with his brother during trips to the Jersey shore. His father gave him his first drawing table at the age of ten. Today, he is an experienced architect who received his FAIA in June 2025. The road he took is unique, to say the least.
Forge Craft Architecture + Design: Codes, Contracts, and Intellectual Property
Founding Principal and Director of Modular Practice for Forge Craft Architecture + Design, Rommel Sulit, discusses the implications of codes, contracts, and intellectual property on
modular construction.
Eisa Lee, the “Bilingual” Architect
Now as the founder of XL
Architecture and Modular Design in Ontario, Canada, she applies not just her education as a traditional architect but an entire holistic view on modular design. It’s this expansive view that guides her work on being a true partner that bridges the gap between architects and modular factories as they collaborate on the design process.
Tamarack Grove Engineering: Designing for the Modular Sector
The role of a structural engineer is crucial to the success of a modular project, from initial analysis to construction administration. Tamarack Grove offers structural engineering services — project analysis, plan creation, design creation, and construction administration — for commercial, manufacturing, facilities, public services, and modular. Modular is only one market sector the company serves but it is an increasingly popular one.
Engineer Masters the Art of Listening to His Customers
Since founding Modular Structural Consultants, LLC. in 2014, Yurianto has established a steady following of modular and container-based construction clients, primarily manufacturers. His services often include providing engineering calculations, reviewing drawings, and engineering certification
Inside College Road: Engineering the Modules of One of the World’s Tallest Modular Buildings
College Road is a groundbreaking modular residential development in East Croydon, South London by offsite developer and contractor, Tide, its modular company Vision Volumetric (VV), and engineered by MJH Structural Engineers.
Design for Flow: The Overlooked Power of DfMA in Modular Construction
Unlocking higher throughput, lower costs, and fewer redesigns by aligning Lean production flow with design for manufacturing and assembly.