Building Green, Living Clean
How Modular Construction Paves the Way for Zero-Waste and Eco-Efficiency
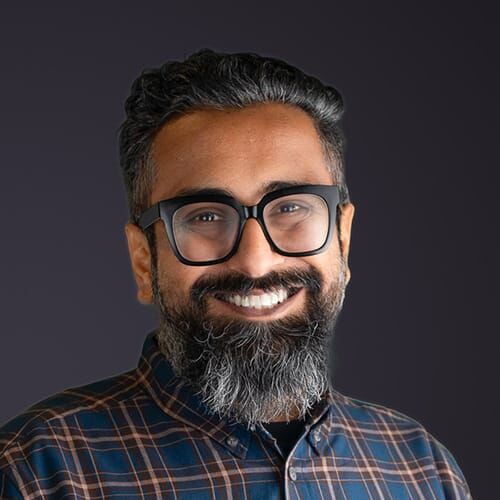
Ali Salman is the Director of Sales and Marketing for Northgate Industries
This Northern project consisted of 54 modular units making up duplexes and fourplexes with a combination of studio suites and one-bedroom suites. These units were 665 sq ft and 446 sq ft. Triodetic foundations with chain link skirting were used because of permafrost. These units were placed in 13 First Nations communities in the Northwest Territories. They were built to withstand the harshest climates, with temperatures reach down to -65 Fahrenheit, often for weeks at a time.
Modular construction, an innovative building method where structures are prefabricated off-site and then assembled on-site, is making significant strides in sustainable building practices. The method is increasingly recognized for its potential in achieving zero waste and superior environmental efficiency compared to traditional on-site construction. This article delves into the mechanisms through which modular construction achieves these environmental milestones, backed by statistics and research references.
Zero Waste through Precision and Recycling
Modular construction significantly reduces waste generation due to its precision and the controlled environment in which the modules are constructed. According to a report by Waste & Resources Action Program (WRAP), modular construction can reduce waste materials like timber, cardboard, plastics, and concrete by up to 90% compared to traditional construction methods. The precision of factory settings minimizes off-cuts and excess usage of materials. Additionally, any waste generated can be more efficiently sorted and recycled in a factory setting, unlike on a construction site where waste segregation and recycling can be more challenging.
Reduced Material Usage
The manufacturing process for modular buildings allows for more accurate material estimates, reducing over-ordering and excess use. This careful management of resources contributes to a reduction in the environmental impact associated with material extraction and processing. The Modular Building Institute reported that this process results in a material savings of up to 20%.
Lower Energy Consumption
Modular construction sites typically have a smaller carbon footprint. The bulk of construction activity takes place in a factory, which usually has better energy management systems than a traditional construction site. A study from the Journal of Building Engineering indicated that modular construction could lead to an average reduction in energy consumption of about 67% during the building phase. Moreover, transporting fully constructed modules to a site often requires fewer trips compared to the transportation of raw materials for on-site building, leading to reduced emissions from transportation.
Enhanced Building Efficiency
Modular buildings are often more energy-efficient than traditional buildings. The controlled environment of a factory allows for better insulation and airtightness, leading to reduced energy consumption in heating and cooling. Furthermore, research suggests that modular buildings can be up to 15% more energy-efficient than conventional buildings.
Sustainability in Material Choices
Modular construction provides an opportunity to use sustainable and recycled materials. The controlled environment of a factory allows for more experimentation and utilization of eco-friendly materials that might not be feasible in traditional construction settings.
Reduced Site Disturbance
Since most of the construction is done off-site, modular construction significantly reduces the environmental impact on the construction site. This approach leads to less soil erosion, less damage to the local ecosystem, and a reduction in the site’s carbon footprint.
Challenges and Future Directions
Despite its advantages, modular construction faces challenges such as transportation logistics, the need for standardization in design for more effective recycling, and perception issues in the market. However, with technological advancements and increasing awareness of environmental issues, modular construction is poised to play a crucial role in sustainable building practices.
In conclusion, modular construction presents a promising path towards zero waste and enhanced environmental efficiency in the building industry. By leveraging precision manufacturing, reduced material usage, and improved energy efficiency, this method aligns with the growing global emphasis on sustainability and environmental responsibility. As the industry evolves, modular construction is likely to become a standard bearer for eco-friendly building practices.
More from Modular Advantage
Oregon’s Prevailing Wage Proposal: A Wake-Up Call for Modular Construction
In early February, 2024, the Massachusetts Board of Building Regulations and Standards (BBRS) released its proposed 10th Edition building codes. This draft included several amendments targeting modular construction that would have created an extremely difficult environment for the entire modular industry and could have eliminated the industry entirely in the state.
Behind the Design of Bethany Senior Terraces, NYC’s First Modular Passive House Senior Housing Project
As more developers seek to meet new regulations for energy efficiency, the team at Murray Engineering has set a new record. With the Bethany Senior Terraces project, Murray Engineering has helped to develop NYC’s first modular structure that fully encompasses passive house principles — introducing a new era of energy efficiency in the energy-conscious city that never sleeps.
How LAMOD is Using Modular to Address Inefficiency, Sustainability, and the Future of Construction
As developers, designers, and contractors seek to understand the evolving needs of the modular industry, no one is as well-versed in the benefits of going modular as Mārcis Kreičmanis. As the co-founder and CBDO of LAMOD in Riga, Latvia, Mārcis has made it his ultimate goal to address the inefficiencies of traditional construction.
From Furniture Builder to ‘Activist Architect’: Stuart Emmons’ Unique Journey
Stuart Emmons was fascinated by buildings at a young age. He remembers building sand cities with his brother during trips to the Jersey shore. His father gave him his first drawing table at the age of ten. Today, he is an experienced architect who received his FAIA in June 2025. The road he took is unique, to say the least.
Forge Craft Architecture + Design: Codes, Contracts, and Intellectual Property
Founding Principal and Director of Modular Practice for Forge Craft Architecture + Design, Rommel Sulit, discusses the implications of codes, contracts, and intellectual property on
modular construction.
Eisa Lee, the “Bilingual” Architect
Now as the founder of XL
Architecture and Modular Design in Ontario, Canada, she applies not just her education as a traditional architect but an entire holistic view on modular design. It’s this expansive view that guides her work on being a true partner that bridges the gap between architects and modular factories as they collaborate on the design process.
Tamarack Grove Engineering: Designing for the Modular Sector
The role of a structural engineer is crucial to the success of a modular project, from initial analysis to construction administration. Tamarack Grove offers structural engineering services — project analysis, plan creation, design creation, and construction administration — for commercial, manufacturing, facilities, public services, and modular. Modular is only one market sector the company serves but it is an increasingly popular one.
Engineer Masters the Art of Listening to His Customers
Since founding Modular Structural Consultants, LLC. in 2014, Yurianto has established a steady following of modular and container-based construction clients, primarily manufacturers. His services often include providing engineering calculations, reviewing drawings, and engineering certification
Inside College Road: Engineering the Modules of One of the World’s Tallest Modular Buildings
College Road is a groundbreaking modular residential development in East Croydon, South London by offsite developer and contractor, Tide, its modular company Vision Volumetric (VV), and engineered by MJH Structural Engineers.
Design for Flow: The Overlooked Power of DfMA in Modular Construction
Unlocking higher throughput, lower costs, and fewer redesigns by aligning Lean production flow with design for manufacturing and assembly.