Part I: Valuing Levels of Innovation
Valuing Levels of Innovation in the Modular Construction Industry
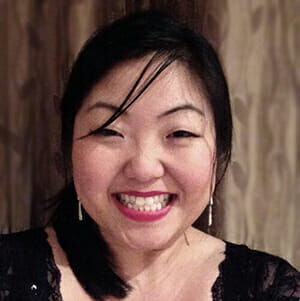
Heather Wallace is the Director of Communications and Project Manager at the Momentum Innovations Group.
What Exactly is Innovation?
One of the best ways to determine whether or not something is innovative is if it creates new value. Innovation is when a product, service, or knowledge is renewed, modernized, or improved by the application of new processes, the introduction of new techniques, or establishing successful ideas…to create new value in the market. And there are multiple levels of innovation.
Incremental innovation creates feature improvements on an existing product or service. It requires continuous improvement - something that must be built into the culture of a company where employees at all levels feel empowered and equipped to explore and share new ideas.
Site-built stick framing has been incrementally improving over many decades - from timber framing to platform framing - including an improvement of tools and some materials - from plywood to OSB to MDF and fire-rated wood. But images of framing from 100 years ago look eerily similar to images of framing today.
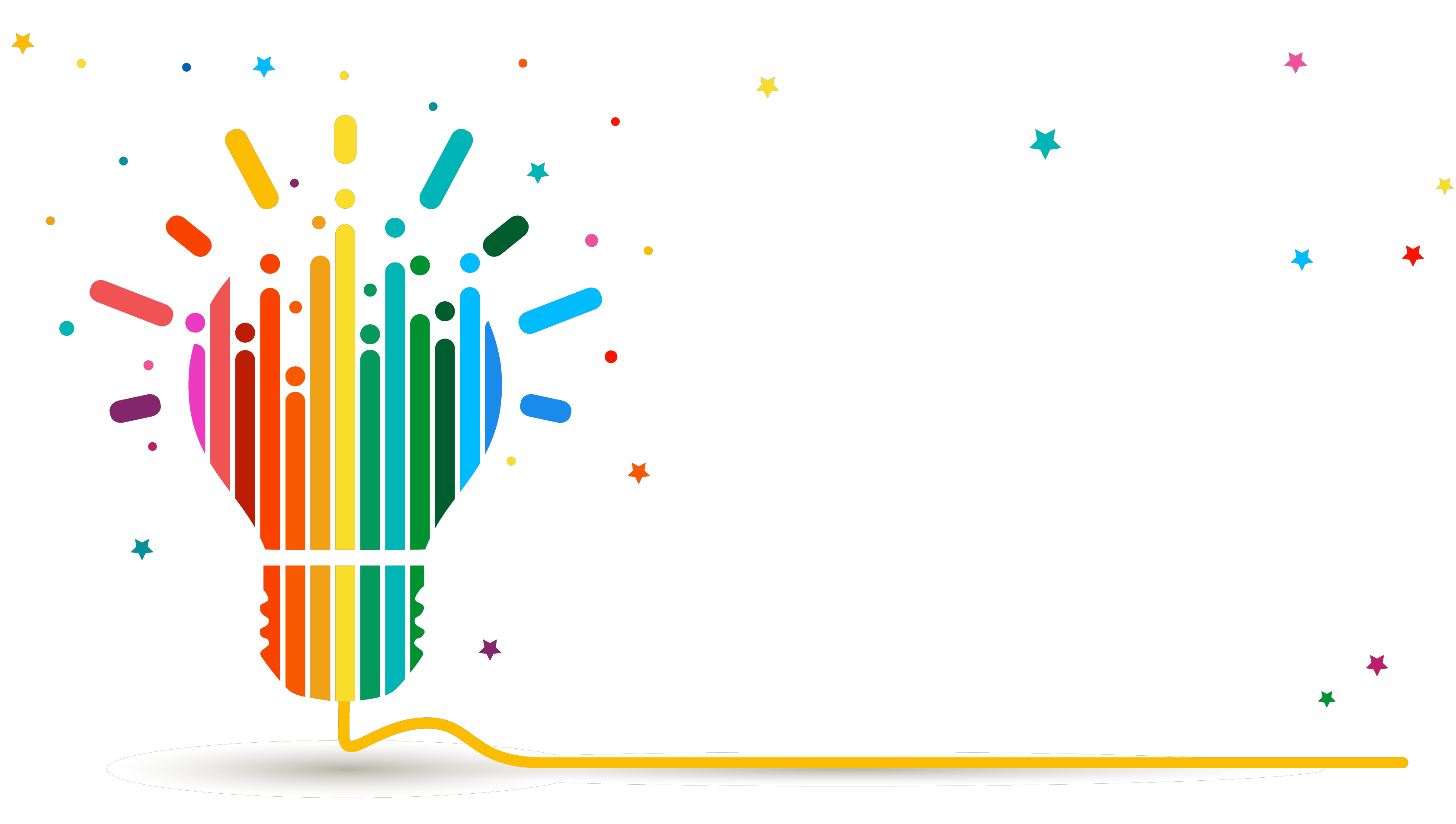
Adjacent innovation utilizes existing knowledge with the application of technology to gain new audiences.
The Modular Mobilization Coalition is a good example of adjacent innovation. When Covid-19 patients began filling-up healthcare facilities around the country, sixteen independent modular companies banded together to help solve this challenge. All of the companies had an existing knowledge of modular construction - they were all building somewhat similar products for the residential, commercial, and educational spaces. The adjacent innovation happened when all of these companies agreed to manufacture a standardized healthcare product based on a modular platform that allowed the emergency healthcare product to be moved and then converted to permanent residential units when the emergency ended.
Although MMC never got to fully deploy their standardized and configurable modular platform, the concept spawned a number of new initiatives.
Disruptive innovation is the most exciting type of innovation. It shakes up an industry and has the potential to take over market share of existing business from larger, legacy companies. Many times this type of innovation is fueled by the desire to solve a nagging specific industry challenge.
Back in 2007 the founders of Airbnb, Brian Chesky and Joe Gebbia, were living in San Francisco with no money and rented out air mattresses in their apartment to conference attendees because they could not find a hotel. A study from the National Bureau of Economic Research found that in 10 US cities with the largest Airbnb market share, “the entry of Airbnb resulted in 1.3 percent fewer hotel nights booked and a 1.5 percent loss in hotel revenue”. Airbnb not only disrupted the hospitality sector, but the travel sector, as well. They democratized the travel industry - creating more affordable or diverse options for everyone.
3D printing buildings in the construction industry has the potential to be both an adjacent and disruptive innovation. Companies like Mighty Buildings and ICON are utilizing an existing building material - concrete - albeit in a slightly different format, and combining it with a technology already being successfully used in other industries. Creating buildings using 3D printing technology still has a ways to go but does have the potential to offer end users an alternative building method and take business from traditional site built construction.
Why is There So Much Failure?
Only a small amount of innovative ideas actually become successful in the marketplace. Why is it so difficult for companies to innovate successfully?
First and foremost, most legacy companies actively resist innovation, this is especially true in the fragmented construction industry. This is a major challenge as there are hundreds of thousands of independent trades, builders, distributors, and building material companies who work hard but generally maintain the status quo. It’s often said people are scared of change, but a more nuanced perspective is they fear loss, whether it is profits, time or familiarity.
Secondly, early traction and scaling is important but this is very difficult in our industry, exacerbated by combative contracts, little transparency and low-bid transactional relationships. Innovating one part of the process or within a particular geographical area often does not result in another area of the industry moving any faster.
One of the most famous disruptive innovators in the construction industry was Katerra. Whatever your viewpoint of Katerra was, their goals of mass manufacturing + technology positioned them to create efficiencies rarely seen in the construction industry. Their problems were rooted in unrealistic growth and forgetting they were a manufacturing company. Although their failure was highly public and predicted by many, it does not change the fact that they had the potential to be disruptive.
It is unfortunate that hard-tech construction innovation requires a 10+ year commercialization timeline but this means that patient capital is essential for success.
Ultimately, meaningful innovation creates new value whether it’s through incremental, adjacent or disruptive innovation. And we can (hopefully) all agree we need more!
Stay tuned for Part II of this series in a future issue of Modular Advantage as we dive deeper into the topic of innovation.
More from Modular Advantage
Oregon’s Prevailing Wage Proposal: A Wake-Up Call for Modular Construction
In early February, 2024, the Massachusetts Board of Building Regulations and Standards (BBRS) released its proposed 10th Edition building codes. This draft included several amendments targeting modular construction that would have created an extremely difficult environment for the entire modular industry and could have eliminated the industry entirely in the state.
Behind the Design of Bethany Senior Terraces, NYC’s First Modular Passive House Senior Housing Project
As more developers seek to meet new regulations for energy efficiency, the team at Murray Engineering has set a new record. With the Bethany Senior Terraces project, Murray Engineering has helped to develop NYC’s first modular structure that fully encompasses passive house principles — introducing a new era of energy efficiency in the energy-conscious city that never sleeps.
How LAMOD is Using Modular to Address Inefficiency, Sustainability, and the Future of Construction
As developers, designers, and contractors seek to understand the evolving needs of the modular industry, no one is as well-versed in the benefits of going modular as Mārcis Kreičmanis. As the co-founder and CBDO of LAMOD in Riga, Latvia, Mārcis has made it his ultimate goal to address the inefficiencies of traditional construction.
From Furniture Builder to ‘Activist Architect’: Stuart Emmons’ Unique Journey
Stuart Emmons was fascinated by buildings at a young age. He remembers building sand cities with his brother during trips to the Jersey shore. His father gave him his first drawing table at the age of ten. Today, he is an experienced architect who received his FAIA in June 2025. The road he took is unique, to say the least.
Forge Craft Architecture + Design: Codes, Contracts, and Intellectual Property
Founding Principal and Director of Modular Practice for Forge Craft Architecture + Design, Rommel Sulit, discusses the implications of codes, contracts, and intellectual property on
modular construction.
Eisa Lee, the “Bilingual” Architect
Now as the founder of XL
Architecture and Modular Design in Ontario, Canada, she applies not just her education as a traditional architect but an entire holistic view on modular design. It’s this expansive view that guides her work on being a true partner that bridges the gap between architects and modular factories as they collaborate on the design process.
Tamarack Grove Engineering: Designing for the Modular Sector
The role of a structural engineer is crucial to the success of a modular project, from initial analysis to construction administration. Tamarack Grove offers structural engineering services — project analysis, plan creation, design creation, and construction administration — for commercial, manufacturing, facilities, public services, and modular. Modular is only one market sector the company serves but it is an increasingly popular one.
Engineer Masters the Art of Listening to His Customers
Since founding Modular Structural Consultants, LLC. in 2014, Yurianto has established a steady following of modular and container-based construction clients, primarily manufacturers. His services often include providing engineering calculations, reviewing drawings, and engineering certification
Inside College Road: Engineering the Modules of One of the World’s Tallest Modular Buildings
College Road is a groundbreaking modular residential development in East Croydon, South London by offsite developer and contractor, Tide, its modular company Vision Volumetric (VV), and engineered by MJH Structural Engineers.
Design for Flow: The Overlooked Power of DfMA in Modular Construction
Unlocking higher throughput, lower costs, and fewer redesigns by aligning Lean production flow with design for manufacturing and assembly.