Customized & Complex: Inside the Construction of the Nation's Largest Modular Hospital
Some people love a challenge, and some companies grow to specialize in tackling challenging projects. MODLOGIQ, located in New Holland, Pennsylvania, has developed expertise in building healthcare facilities, a demanding enterprise for any builder. With roots going back to the 1970s in Canadian manufacturer NRB with owners Bob and Craig McNeil, MODLOGIQ was spun-off from NRB as a result of the sale of the Grimsby operation in 2019 with Jim Gabriel as President and CEO.
The company continues today in taking a problem-solving approach to applying the benefits of off-site modular construction, Gabriel said, to a number of current challenging projects. “Our philosophy has always been that we’re not necessarily modular builders, we’re problem solvers. We take a collaborative approach to that,” he added.
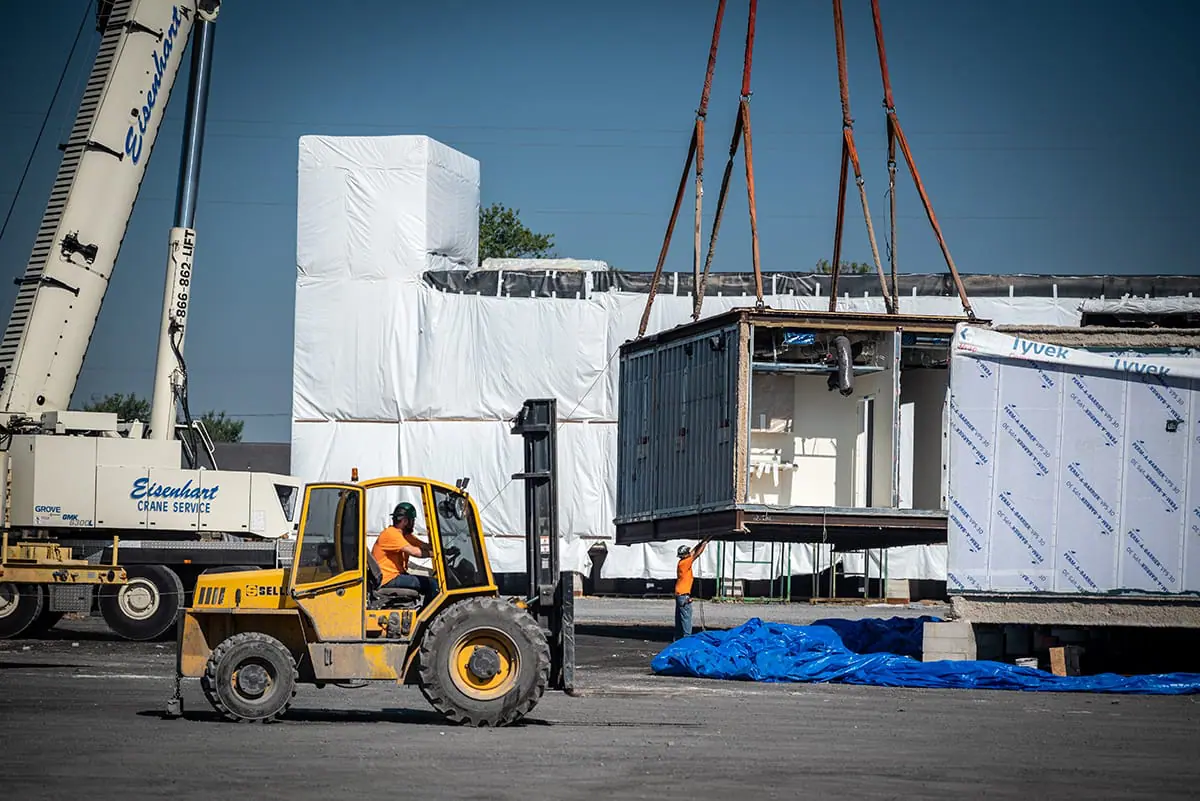
Modules intended for the Athens Medical Campus in Athens, OH, are craned into position during its offsite construction.
A Unique Focus On Modular Healthcare Facilities
MODLOGIQ has a long history of building modular healthcare facilities, such as their recent hospital project in Athens, Ohio. Compared to other types of modular projects, such as hotels, for example, healthcare facilities tend to be more complex projects, Gabriel said.
“We’re low volume, high custom, and high level of complexity, and so we’re the company that takes on all the other types of more complex projects. And so healthcare became a natural fit,” he added.
All building projects involve layers of complexity, especially when working with clients and their expectations, but some projects are at different levels. “It’s not easy, but it’s easier to modularize a hotel. It’s easier to modularize single family and multifamily. It’s easier to take what modular is and apply it to those applications,” he noted.
“It’s pretty difficult to do that with the health care and the patient-care environment,” he said. “And so whether it’s patient care, whether it’s laboratories, health science-type applications, it’s highly complex, not just in what’s performed in those, but how do you get to an efficient level of constructability when it comes to the design and execution? And can you provide a suitable alternative to conventional construction?” he continued.
Obviously modular can provide a suitable alternative to conventional construction, and two factors stand out as major benefits, Gabriel noted. Modular construction can overcome the schedule problem, which matters a lot to a revenue-generating organization such as a healthcare group. Getting the new facility operational in the shortest possible timeframe means, basically, less time in cash outflow before moving on to cash inflow.
Addressing the labor challenge is another advantage for modular construction. When traditional contractors are facing labor shortages, they may be running a team of mid-level competence and may be running shorthanded. A healthcare facility is a complex project that requires high competence, and many contractors don’t want to bid that work based on concerns over their ability to execute.
“You don’t want to position yourself to fail,” Gabriel said, “so you’re going after the work that’s easier to execute. So what healthcare providers, administrators, and owners are finding is that they’ve got fewer qualified contractors who have less labor to apply to their projects, and so the cost per square foot is going up and so is the time to completion.” In contrast, Gabriel noted, “With our focus on healthcare, we bring speed to market. We’re able to provide clients with a more efficient path to getting to a complete turnkey solution.”
Of course, the modular industry is not immune from labor challenges, but adapting to current market conditions is crucial. “Everyone has the same challenge with labor,” he added. “The question is: how efficiently are you using your labor? And as an industry, modular construction generally has used that more efficiently.”
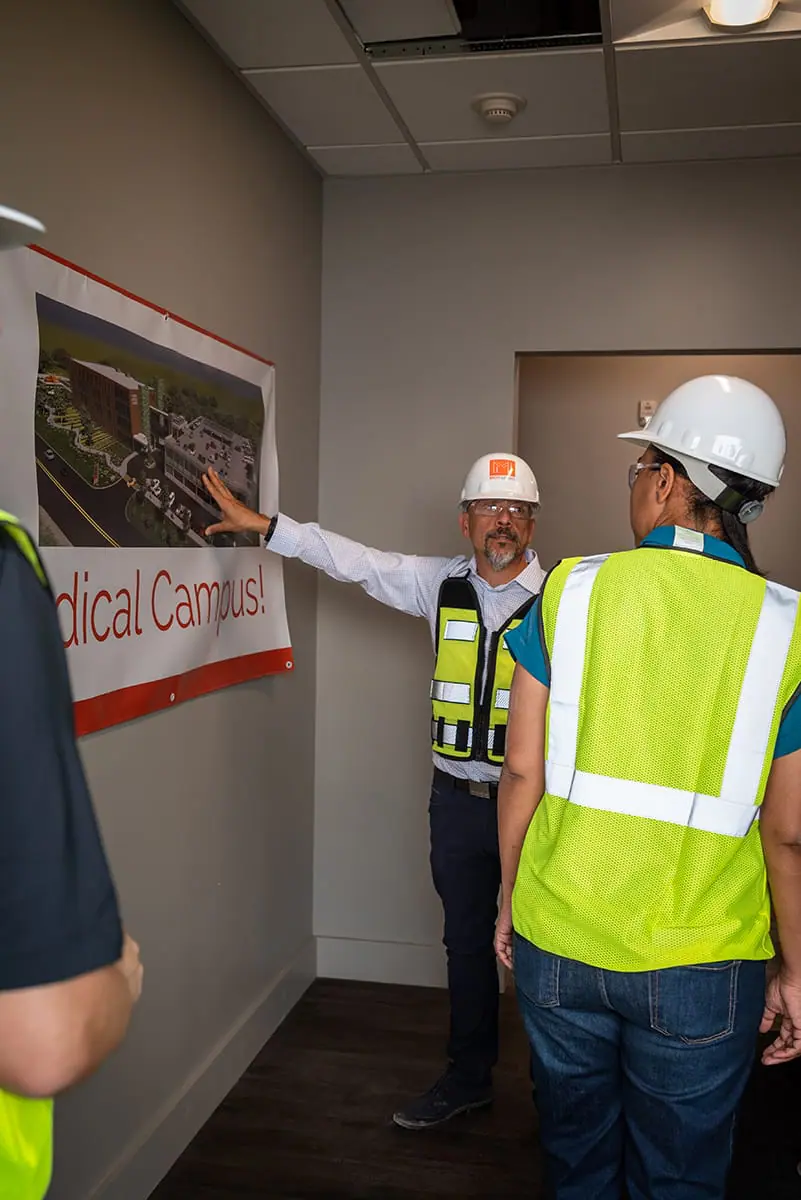
Jim Gabriel shows a mock-up of the completed Memorial Health System hospital currently being built at MODLOGIQ.
Building the Largest Modular Hospital Yet
Athens, Ohio, is a small town of just under 25,000 population located a bit more than an hour away from Columbus, Ohio. It’s the site of the Athens Medical Campus project for Memorial Health System that Gabriel calls a “prototype hospital” for the company.
With about 100,000 square feet of space on four levels, it’s considered a “micro-hospital,” he said, and MODLOGIQ is producing 100% of the space off-site in their factory. That includes everything from mechanical, electrical, and plumbing to interior finishes and casework to about an 85% level of completion.
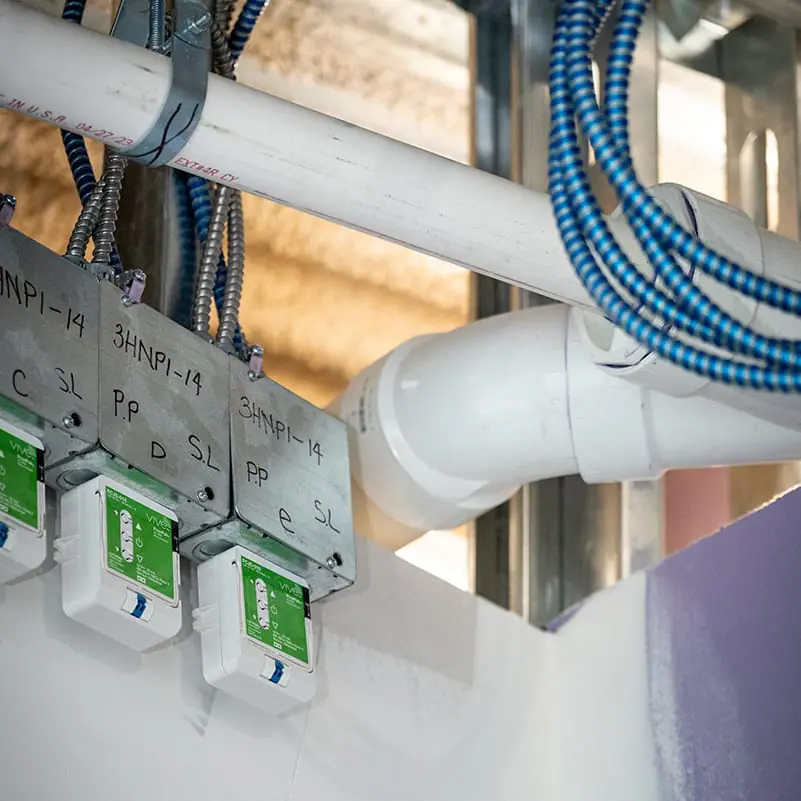
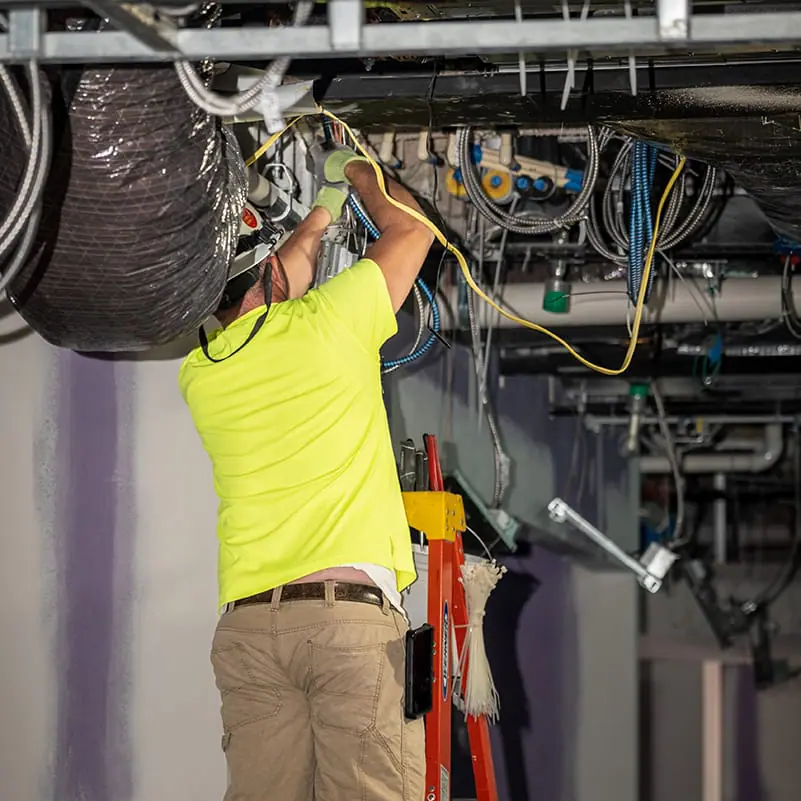
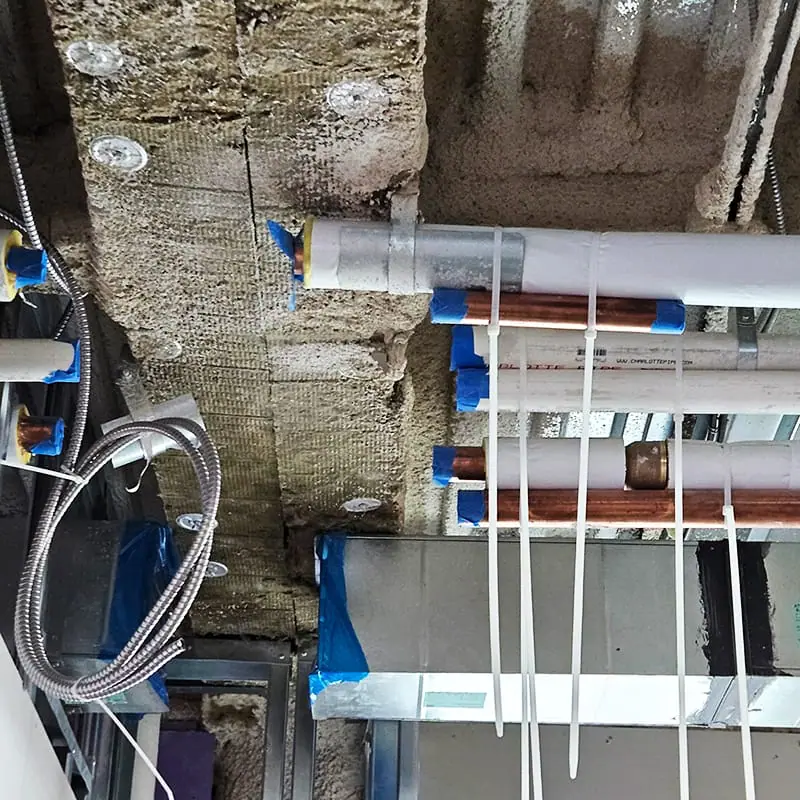
All mechanical, electrical, and plumbing work was completed to about 85%. The remaining connections between modules will be completed onsite.
Working with developers Medical Innovations Development (MIND) and representatives Bob Guessing and Mark Molen, MODLOGIQ started in December of 2021 to design and get approval for the structural steel. As the process moved ahead to site work, finding a general contractor proved to be challenging due to heavy competition from other local construction projects.
“What we learned over the course of this is that there’s a ton of new projects going on in nearby Columbus Ohio, like the Intel chip-manufacturing facility, and Amazon’s got some new facilities that they’re building there. And so it’s really a tight demand for that labor,” he added. “It took some time to find the right contractor on site, but it all came together with the addition of Robertson Construction. And we’ve got what we believe is a really strong team,” he noted.
The Challenge of Adapting Modular to Healthcare
The client’s vision for the project was clear from the start, Gabriel said, but the challenge for MODLOGIQ was to modularize it.
“They knew what they wanted to build, but they didn’t exactly know how they were going to build it. And I think our expertise is really taking that vision and then understanding their programming requirements to achieve something we can build efficiently in our factory,” he noted.
Working with the client through the design process required a series of design modifications, he said. “Can we change the dimension of this area? How can we support this open area without columns everywhere?” he added. “It was a design that was literally happening as we were building, and that’s not typical for modular construction. But because we had the structural done, which started roughly in late summer, we were working through all the other design decisions and gyrations but it was all taking place within that structural framework,” he noted.
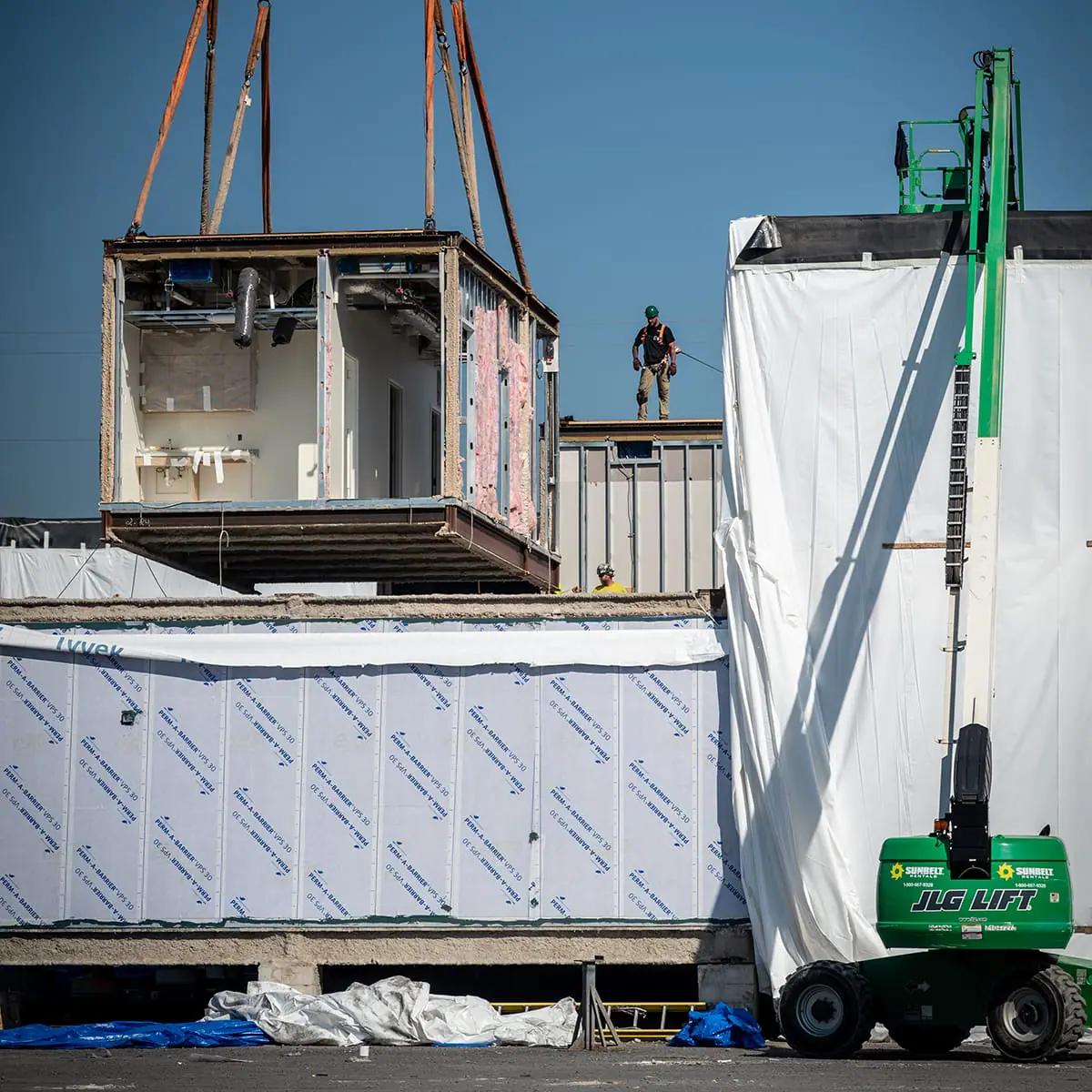
With the structural steel in place, it acted as a sort of guardrail or design constraint that everyone had to work around, which can save time and help to keep the process moving along.
The project used 204 modules with 12 different variations of length and width at a consistent height. Those sizes were driven by the client’s programming requirements for the building, Gabriel said. “The module sizes and configurations are a little less traditional than what would be typical for a modular build,” he added.
What is traditional, though, is meeting all standard codes and other requirements for a commercial building. “There’s no modular hospital design standards; there’s nothing different because we’re modularizing it or fabricating that in the factory,” Gabriel said. “We just have a more efficient way to build it. And it is consistent with all hospital requirements for the state of Ohio and all other AHJs,” he added.
Adding A New Team for the Project
Due to the size and speed requirements of this project, Gabriel said the team knew they couldn’t take the project on at the expense of their other clients or upcoming projects. They decided to move some key staff members to the Athens project, hire some new staff, and create a completely new and separate team for the project.
“We approached this as a separate business unit so that we were making decisions not just from a project standpoint, but from an operational standpoint,” he mentioned. “This is a $65 or $70 million project. How do we need to approach that differently from an operational standpoint?” he added.
Large and challenging projects like this one will always offer some twists and turns, and this one was no exception. As the team moved rapidly through design and then broke ground for construction, some design elements were unfinished. “You don’t like to have those design decisions lingering. There were still some components of the design that weren’t directly related to the building but could have an impact. What was going to happen around the helicopter pad, the parking garage? The adjacency of those structures and how they impact the design,” he noted. Even with those challenges, the MODLOGIQ team brought the project 12 months ahead of a conventional construction schedule, Gabriel said.
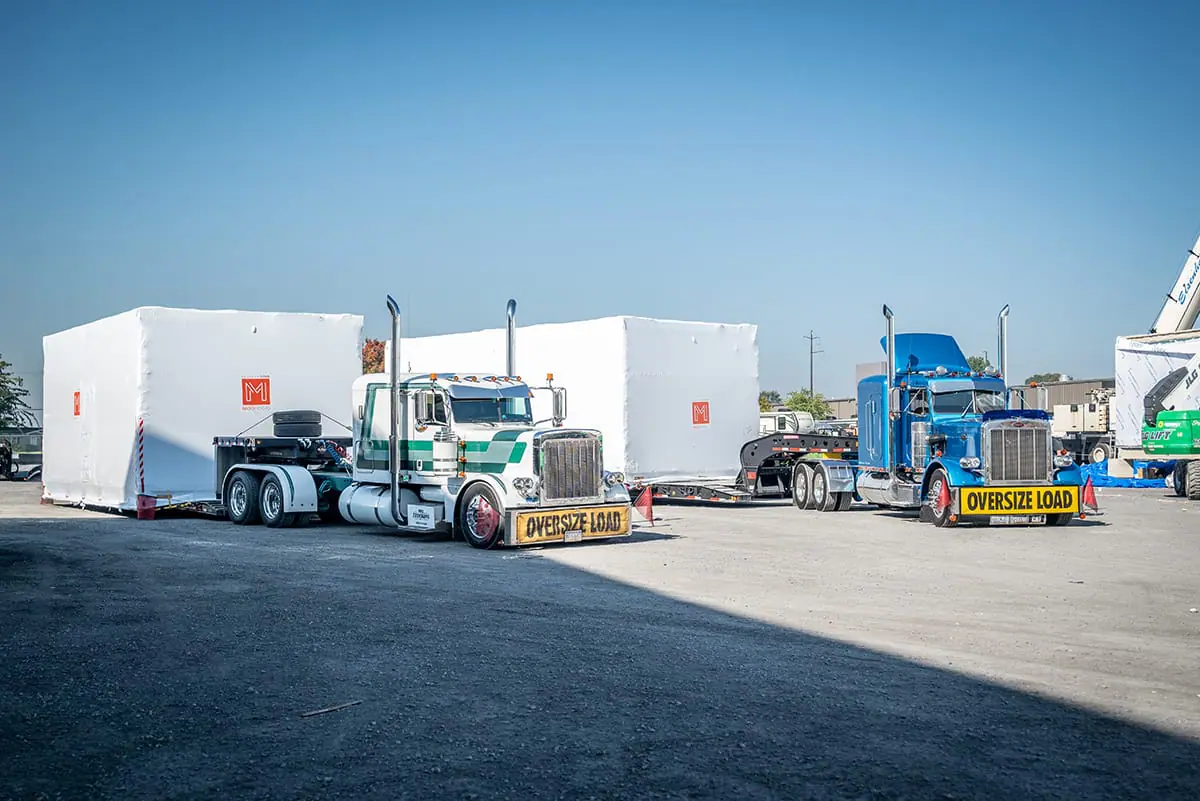
What’s Next for MODLOGIQ?
According to Gabriel, the company’s core value is servant leadership. “I would say that our culture is characterized by and led by a group that is some of the best that I’ve ever worked with in this industry, and I’ve been at it for 30 years,” he said.
To that end, the company is already in discussions on a series of prototype hospital projects, and he’s also interested in looking beyond the hospital environment to leveraging the strengths of modular construction to address the affordable housing shortage and support rapid disaster rebuilding efforts.
“This project demonstrates what we and modular can do. It’s important that we find ways to apply our knowledge and experience in more significant ways,” he said. “How can the modular industry and MODLOGIQ be more relevant in applying the value of offsite modular prefab construction in the rebuilding of our infrastructure?” he asked. “It takes collaborative design and innovative thinking. It cannot be done in a vacuum.”