FullStack Modular’s Bicoastal Moves Are Making Waves
A New HQ in CT and a Project With Starwood Capital in CA
As Founder and President of FullStack Modular, Roger Krulak has overseen the company’s growth since its inception in 2016. The firm has moved from its first factory in the Brooklyn Navy Yard to a new home in Hamden, Connecticut—all while establishing a flourishing factory in Portland, Oregon.
FullStack Modular has been in Connecticut since late April 2023, getting set up portside at Gateway Terminal. The company has been quick to establish contracts with the state government, providing design and manufacturing options for affordable housing and a myriad of other projects.
“Connecticut is very pro-development and have been great partners since our arrival in Hamden,” said Roger. “The business environment there is very proactive in encouraging new ways to meet their housing needs. So that’s super exciting, and our participation in that is growing.”
In Portland, FullStack Modular is collaborating with the city’s public transportation agency, TriMet, in an effort to develop housing near its rail lines. Roger says it’s all part of his bigger vision to optimize and improve the construction process to propel the industry forward.
“Manufacturing is a process of continuous improvement. The first time we build something, it’s never as efficient as the fifth time we build it. Industrialized construction embraces this approach and we are happy to see that the built environment is finally open to utilizing industrialization and offsite construction to help solve for what seems like an unrelenting demand,” he said.
“Is there a better way to do this? Over the years, I have become very fond of that mindset and process. And I think that the industry as a whole is finally starting to embrace change in order to move the industry forward.”
All the changes and expansions to the business have given Roger a better understanding of the value of continuous improvement, especially as factories adopt robots and automation to increase their speed and efficiency.
Know Your Process Before Introducing Automation
Having been in the business for over 15 years, Roger has seen a lot of successes and failures in the industry. These days, he says, anyone looking to expand or work in modular manufacturing needs to focus on owning their design and process before introducing automation.
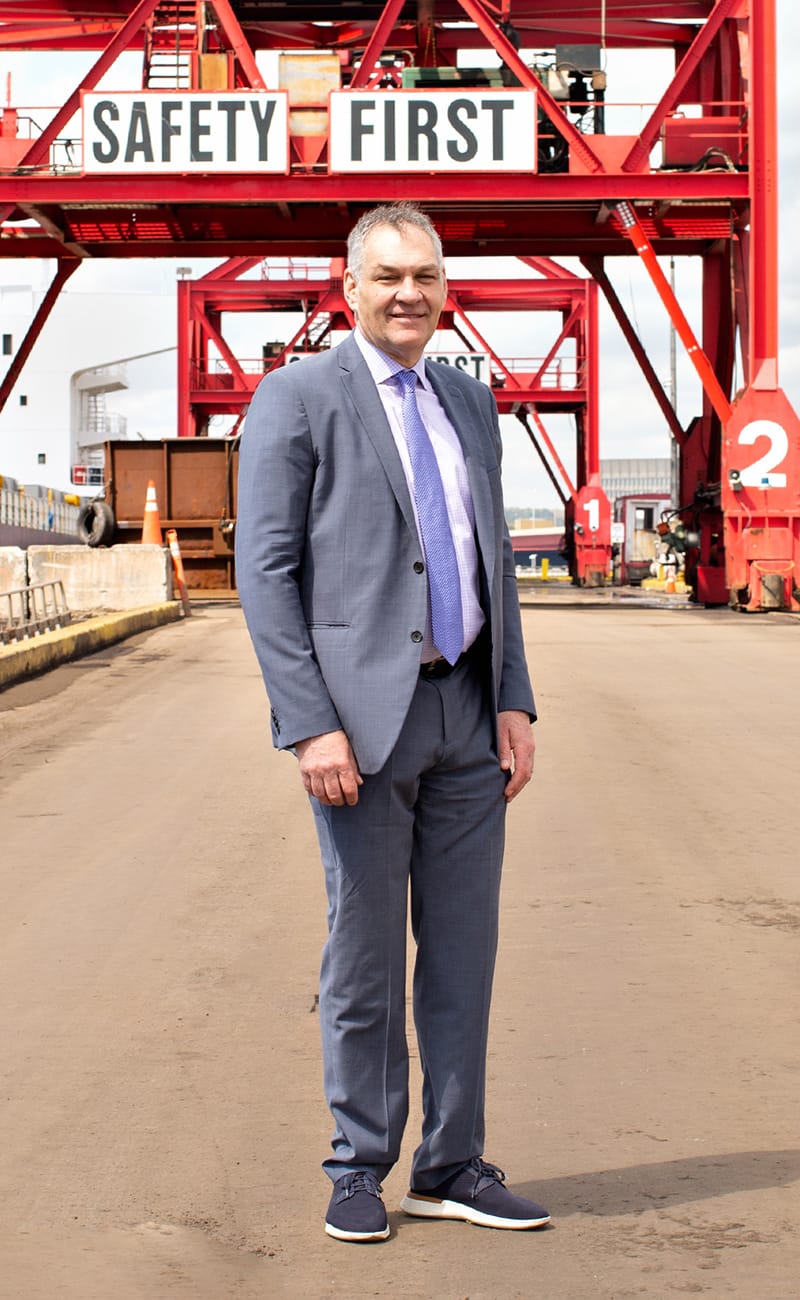
Roger Krulak, founder and president of FullStack Modular. Photo credit: Riverstone Images Studio.
“First, know what your product is and know how you’re going to build it effectively,” he says. “Second, make sure that your factory can accommodate the needs of your product and your process.”
Roger notes that automation—without knowing your process inside and out—could lead to larger financial mistakes down the line. While mistakes are unavoidable, there are some costly ones that manufacturers can and should be wary of.
“I see that mistake made literally every day of the week. They buy a bunch of robots, and they build a window plant that can make 8,000 windows a week, but you can’t even use 8,000 windows in three months,” he says. “Nothing’s going to be perfect, and continuous improvement is imperative. One thing I’ve heard too many times is, ‘I’m buying a bunch of robots, and then I’m going to figure out how to use them.’ Do not do that!”
With these experiences and lessons learned, FullStack Modular’s dedication to sustainability and process yielded their latest project for the Portland factory: a sustainable hotel for Starwood Capital Group in Sunnyvale, California.
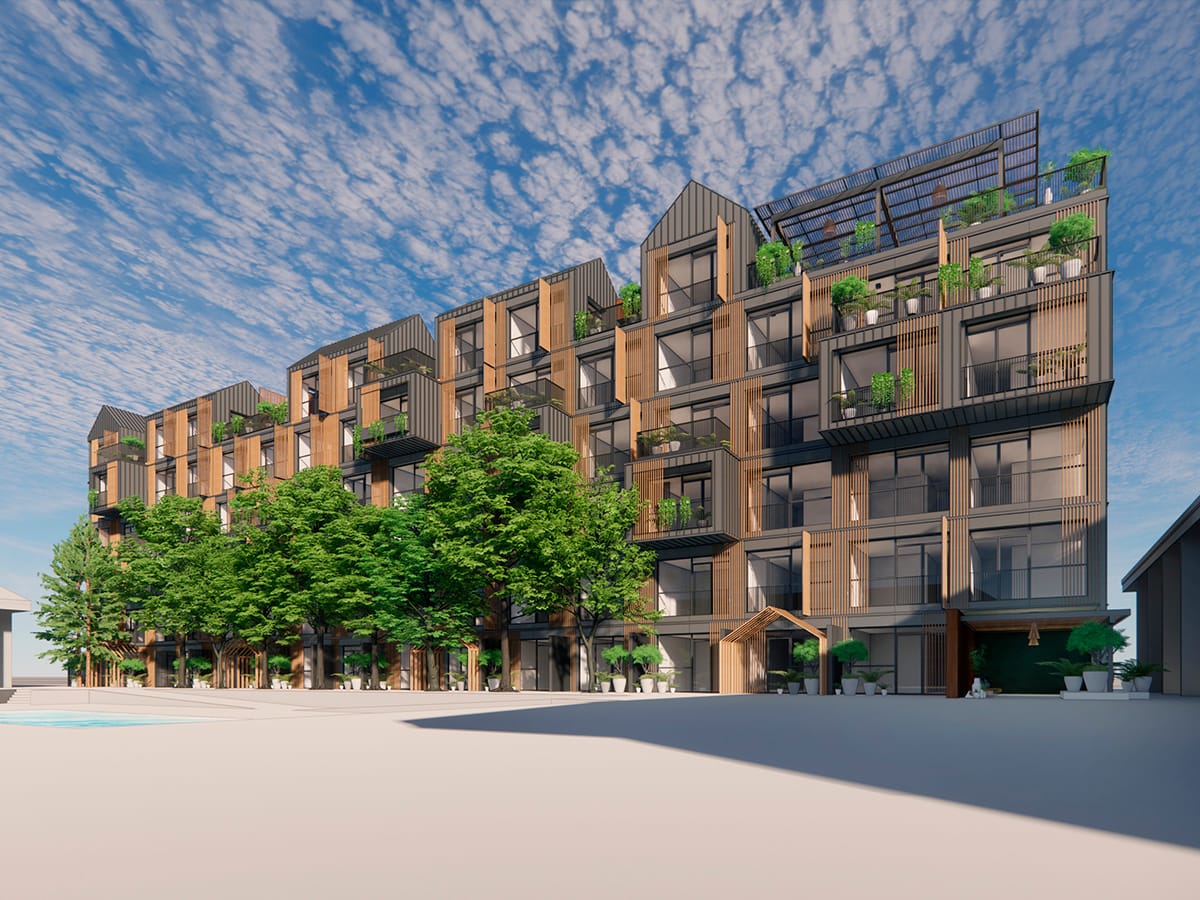
A rendering of Starwood Capital Group's first modular Treehouse hotel in Sunnyvale, CA, manufactured by FullStack Modular. Opening is scheduled for late 2024.
Related Listening:
Notes From a Growing Manufacturer: New Projects and Lessons Learned w/ FullStack Modular
Roger Krulak, founder of FullStack Modular, joins the podcast to talk about the growth of his modular manufacturing company and the exciting projects FullStack and its partners have in the pipeline.
Roger also shares some of the lessons learned from his career in modular and gives advice to up and coming modular manufacturers.
Chasing Sustainability Highs in California
The six-story Treehouse hotel features 200 modules and 143 rooms, all done in coordination with Starwood Capital Group, who, as Roger says, has embraced many of the tenets that make modular work better. The private investment company was looking for a firm that could build in California not just with sustainability in mind, but also climate resiliency in a high seismic zone.
In fact, FullStack Modular’s focus as a mid-to-high-rise all-steel construction modular company resonated with Starwood Capital Group’s plans to create the first Treehouse hotel in the U.S.
“They interviewed every modular company in the world,” said Roger. “It sounds funny, but I’m totally serious. They felt like our unique approach to offsite construction provided them a long-term solution.”
“Our system is seismically responsive, wind responsive, and adaptable to almost every condition,” said Roger. “From whatever our mods sit on all the way through the parapet, it’s all mods, stairwells, elevator shafts, [and] there are no concrete cores in FullStack Modular’s system. It’s all steel and cement floors. Then, it’s all bolted together on-site.”
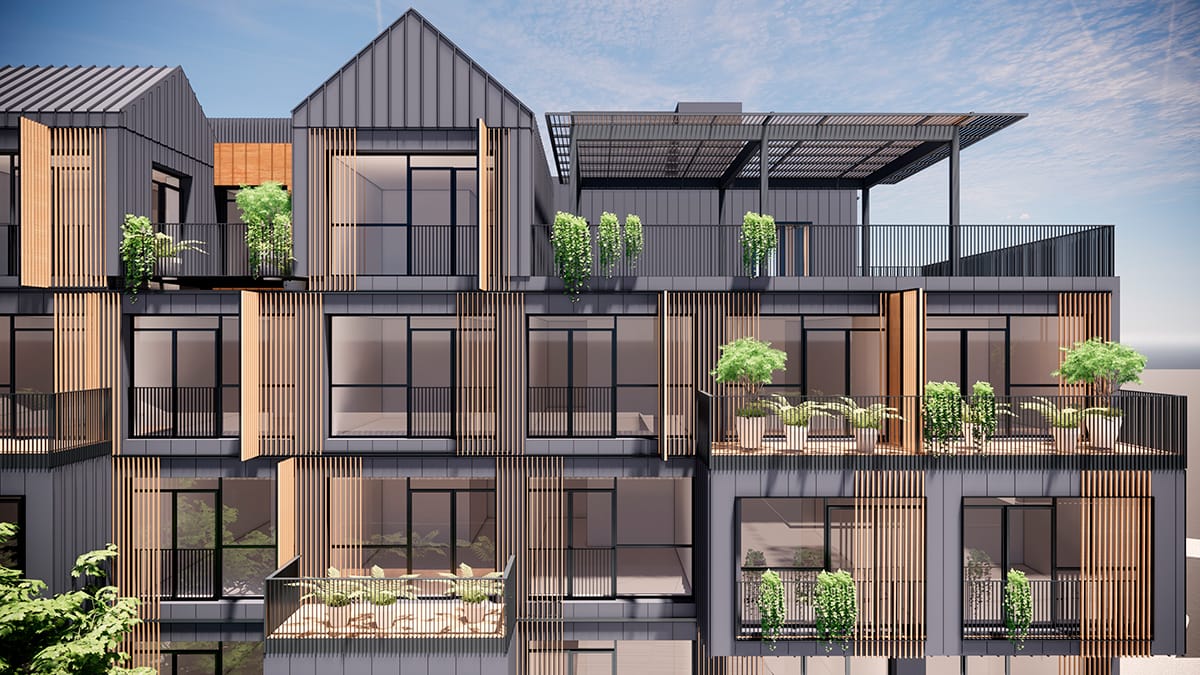
Manufacturing Modules in Portland Bound for California
After working with Starwood Capital Group on the overall design and goal, the Portland factory set to work on developing six different varieties of modules. With FullStack Modular’s system of building with double-loaded corridors, the construction and building process looks to be quick. Roger says the company is aiming to assemble the six-story building over the course of one month once all the modules have arrived via truck from Portland to Sunnyvale.
While the Portland factory is working on these modules, the project took a bit to get started. COVID delays related to the hotel business—namely financing and knowing when to officially start—plagued the manufacturer, on top of supply chain delays.
In all, the timeline is now set to deliver the modules in April or May of 2024. The goal is to have the hotel open by the end of 2024.
About the Author: Karen P. Rivera is a freelance writer and editor with a passion for storytelling. She is a former United Nations-based reporter, with experience covering international breaking news, venture capital, emerging healthcare tech, and the video game industry.
More from Modular Advantage
Oregon’s Prevailing Wage Proposal: A Wake-Up Call for Modular Construction
Should House Bill 2688A become law, building projects would increase in price, face longer completion timelines, and produce significantly more waste. The bill also incentivizes contract awards to out of state businesses who would not reinvest their earnings into the local Oregon economy.
Behind the Design of Bethany Senior Terraces, NYC’s First Modular Passive House Senior Housing Project
As more developers seek to meet new regulations for energy efficiency, the team at Murray Engineering has set a new record. With the Bethany Senior Terraces project, Murray Engineering has helped to develop NYC’s first modular structure that fully encompasses passive house principles — introducing a new era of energy efficiency in the energy-conscious city that never sleeps.
How LAMOD is Using Modular to Address Inefficiency, Sustainability, and the Future of Construction
As developers, designers, and contractors seek to understand the evolving needs of the modular industry, no one is as well-versed in the benefits of going modular as Mārcis Kreičmanis. As the co-founder and CBDO of LAMOD in Riga, Latvia, Mārcis has made it his ultimate goal to address the inefficiencies of traditional construction.
From Furniture Builder to ‘Activist Architect’: Stuart Emmons’ Unique Journey
Stuart Emmons was fascinated by buildings at a young age. He remembers building sand cities with his brother during trips to the Jersey shore. His father gave him his first drawing table at the age of ten. Today, he is an experienced architect who received his FAIA in June 2025. The road he took is unique, to say the least.
Forge Craft Architecture + Design: Codes, Contracts, and Intellectual Property
Founding Principal and Director of Modular Practice for Forge Craft Architecture + Design, Rommel Sulit, discusses the implications of codes, contracts, and intellectual property on
modular construction.
Eisa Lee, the “Bilingual” Architect
Now as the founder of XL
Architecture and Modular Design in Ontario, Canada, she applies not just her education as a traditional architect but an entire holistic view on modular design. It’s this expansive view that guides her work on being a true partner that bridges the gap between architects and modular factories as they collaborate on the design process.
Tamarack Grove Engineering: Designing for the Modular Sector
The role of a structural engineer is crucial to the success of a modular project, from initial analysis to construction administration. Tamarack Grove offers structural engineering services — project analysis, plan creation, design creation, and construction administration — for commercial, manufacturing, facilities, public services, and modular. Modular is only one market sector the company serves but it is an increasingly popular one.
Engineer Masters the Art of Listening to His Customers
Since founding Modular Structural Consultants, LLC. in 2014, Yurianto has established a steady following of modular and container-based construction clients, primarily manufacturers. His services often include providing engineering calculations, reviewing drawings, and engineering certification
Inside College Road: Engineering the Modules of One of the World’s Tallest Modular Buildings
College Road is a groundbreaking modular residential development in East Croydon, South London by offsite developer and contractor, Tide, its modular company Vision Volumetric (VV), and engineered by MJH Structural Engineers.
Design for Flow: The Overlooked Power of DfMA in Modular Construction
Unlocking higher throughput, lower costs, and fewer redesigns by aligning Lean production flow with design for manufacturing and assembly.