The Envelope Insulation Design Regarding Material Alteration Compatibility in Blast-Resistant Modular Buildings
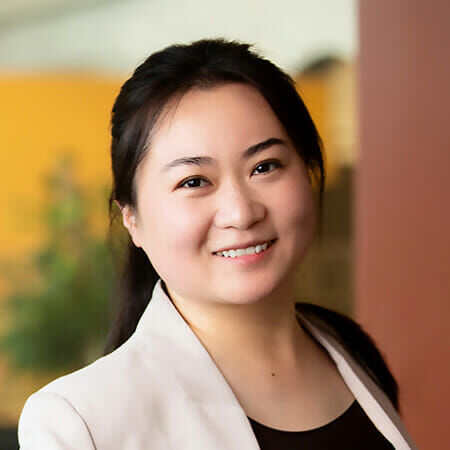
Ran Yu is an arcitect with GLMV Architecture
Blast-resistant modular buildings (BRM buildings) are designed with strong steel exterior wall structure and thick steel skins to withstand blast events and to protect people and equipment from explosions. They are commonly used in oil refineries, chemical processing plants, laboratories, and similar operations.
However, the intrinsic high thermal conductivity of the steel skin and structure in exterior walls acts as the cold bridge reducing the efficiency of building envelope insulation. This results in the need for more insulation material and thicker insulation layers for BRM buildings to comply with building energy code. As energy code and energy-saving standards are adopted by more and more jurisdictions, the requirements for energy code compliant building envelope insulation design have increased.
Meanwhile, the module dimension of modular buildings adopts the inherent limitation of transportation. The prevailing transport limit is 12 feet wide and 40 feet long. A modular unit exceeding this limitation will result in a significant increase in shipping costs.
The third challenge of BRM insulation design is the suddenly derailed global supply chain with price and availability uncertainty. Following the pandemic, the existing global supply chain developed over the past decades was challenged and forced to reshuffle within a few years. The construction industry is experiencing insulation material shortages and incredible price increases. This leads to three possible results: spending extra time and money to redesign and revise drawings with alternative insulation materials; increased construction budgets; postponement or cancellation of projects.
Thus, BRM envelope insulation configuration has impacts on construction schedule time, potential redesign workload, and market competitiveness, which are all critical to the success of a BRM project. One must ask then, how to design an envelope insulation fitting in BRM exterior wall, being compatible with material alteration without wall thickness increasing?
The Envelope Insulation Design Regarding Material Alteration Compatibility
Design for material alteration compatibility aims to reduce redesign, project postponement and cancellation by thinking ahead. At the outset of a project design, consider various insulation material options and thicknesses available
and their impact to energy code compliance. This allows better coordination with blast-resistant structural design requirements. Different than using determined insulation material, design for material alternation compatibility requires the study of various insulation material properties, unit price, and their compatibility with current factory equipment and worker’s skill. The design process is below:
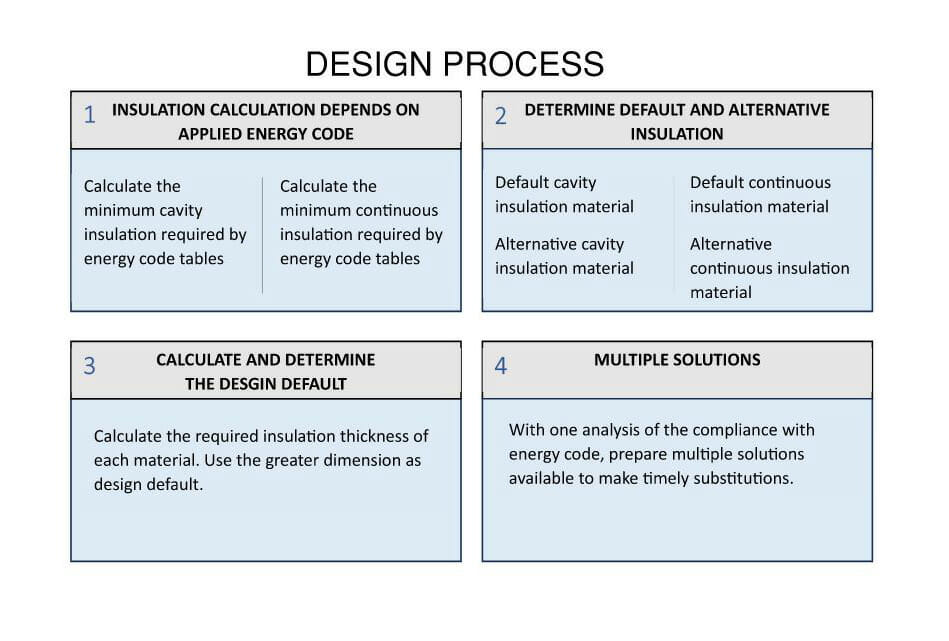
- Insulation calculation depends on applied energy code.
(1) Calculate the minimum inorganic cavity insulation between steel framing required by energy code tables.
(2) Calculate the minimum continuous insulation required by energy code tables. - Determine default and alternative insulation materials.
In BRM buildings, to achieve energy code compliance, cavity insulation is needed in between steel framing, and continuous insulation is needed to be attached to the inner side of steel structure. All these are done without changing BRM’s inherent structural characteristics. At least two materials each for the cavity and the continuous insulation shall be selected.As an example of material selection, one may use close-cell spray foam or mineral wool as cavity insulation, while using polyisocyanurate rigid board or extruded polystyrene board as continuous insulation.
- Calculate the required insulation thickness of each alternative material. Use the greater dimension as design default.
- Now with only one analysis of the compliance with energy code, we have multiple solutions available to make timely substitutions.
Conclusion
In conclusion, design BRM building envelop insulation with compatible to alterative materials supports the success of BRM projects by reducing postponement and cancellations due to redesign work and time, controlling project budget and time.
These advantages will benefit all stockholders including building owners, contractors, manufacturers, and designers.
More from Modular Advantage
Oregon’s Prevailing Wage Proposal: A Wake-Up Call for Modular Construction
In early February, 2024, the Massachusetts Board of Building Regulations and Standards (BBRS) released its proposed 10th Edition building codes. This draft included several amendments targeting modular construction that would have created an extremely difficult environment for the entire modular industry and could have eliminated the industry entirely in the state.
Behind the Design of Bethany Senior Terraces, NYC’s First Modular Passive House Senior Housing Project
As more developers seek to meet new regulations for energy efficiency, the team at Murray Engineering has set a new record. With the Bethany Senior Terraces project, Murray Engineering has helped to develop NYC’s first modular structure that fully encompasses passive house principles — introducing a new era of energy efficiency in the energy-conscious city that never sleeps.
How LAMOD is Using Modular to Address Inefficiency, Sustainability, and the Future of Construction
As developers, designers, and contractors seek to understand the evolving needs of the modular industry, no one is as well-versed in the benefits of going modular as Mārcis Kreičmanis. As the co-founder and CBDO of LAMOD in Riga, Latvia, Mārcis has made it his ultimate goal to address the inefficiencies of traditional construction.
From Furniture Builder to ‘Activist Architect’: Stuart Emmons’ Unique Journey
Stuart Emmons was fascinated by buildings at a young age. He remembers building sand cities with his brother during trips to the Jersey shore. His father gave him his first drawing table at the age of ten. Today, he is an experienced architect who received his FAIA in June 2025. The road he took is unique, to say the least.
Forge Craft Architecture + Design: Codes, Contracts, and Intellectual Property
Founding Principal and Director of Modular Practice for Forge Craft Architecture + Design, Rommel Sulit, discusses the implications of codes, contracts, and intellectual property on
modular construction.
Eisa Lee, the “Bilingual” Architect
Now as the founder of XL
Architecture and Modular Design in Ontario, Canada, she applies not just her education as a traditional architect but an entire holistic view on modular design. It’s this expansive view that guides her work on being a true partner that bridges the gap between architects and modular factories as they collaborate on the design process.
Tamarack Grove Engineering: Designing for the Modular Sector
The role of a structural engineer is crucial to the success of a modular project, from initial analysis to construction administration. Tamarack Grove offers structural engineering services — project analysis, plan creation, design creation, and construction administration — for commercial, manufacturing, facilities, public services, and modular. Modular is only one market sector the company serves but it is an increasingly popular one.
Engineer Masters the Art of Listening to His Customers
Since founding Modular Structural Consultants, LLC. in 2014, Yurianto has established a steady following of modular and container-based construction clients, primarily manufacturers. His services often include providing engineering calculations, reviewing drawings, and engineering certification
Inside College Road: Engineering the Modules of One of the World’s Tallest Modular Buildings
College Road is a groundbreaking modular residential development in East Croydon, South London by offsite developer and contractor, Tide, its modular company Vision Volumetric (VV), and engineered by MJH Structural Engineers.
Design for Flow: The Overlooked Power of DfMA in Modular Construction
Unlocking higher throughput, lower costs, and fewer redesigns by aligning Lean production flow with design for manufacturing and assembly.