A Construction Journey from Conventional to Modular
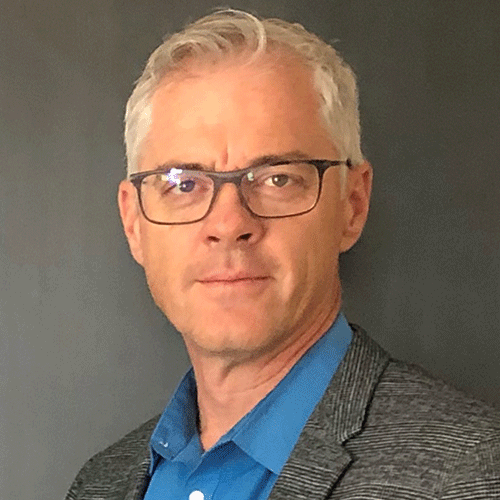
Scott Bridger is the co-founder and Vice President of Proset.
Started by Scott Bridger and Matt Mitchell in 2014, ProSet has grown from a single crew to multiple crews and about 50 installation workers across the country. Though they didn’t know each other previously, both Bridger and Mitchell were from Telluride, Colorado, and were working in the Bakken area of North Dakota and it made sense to commute from Colorado together. An opportunity for a modular construction project came to Mitchell, which he described to Bridger as a “set” project. “I really didn’t know much about modular at the time,” Bridger said, “but he (Mitchell) said the industry is growing as far as commercial modular, meaning multifamily modular and modular hospitality. And there was a sense of interest or maybe a need for a company to just simply do the modular installation scope on these commercial projects. And it was a new enough industry that there really weren’t very many companies out there who really understood how to do this kind of work, but Matt did. He had a lot of experience with it because, as a general contractor building modular apartment buildings, he was self-performing the installation work with his own crew so he knew it very well,” Bridger added.
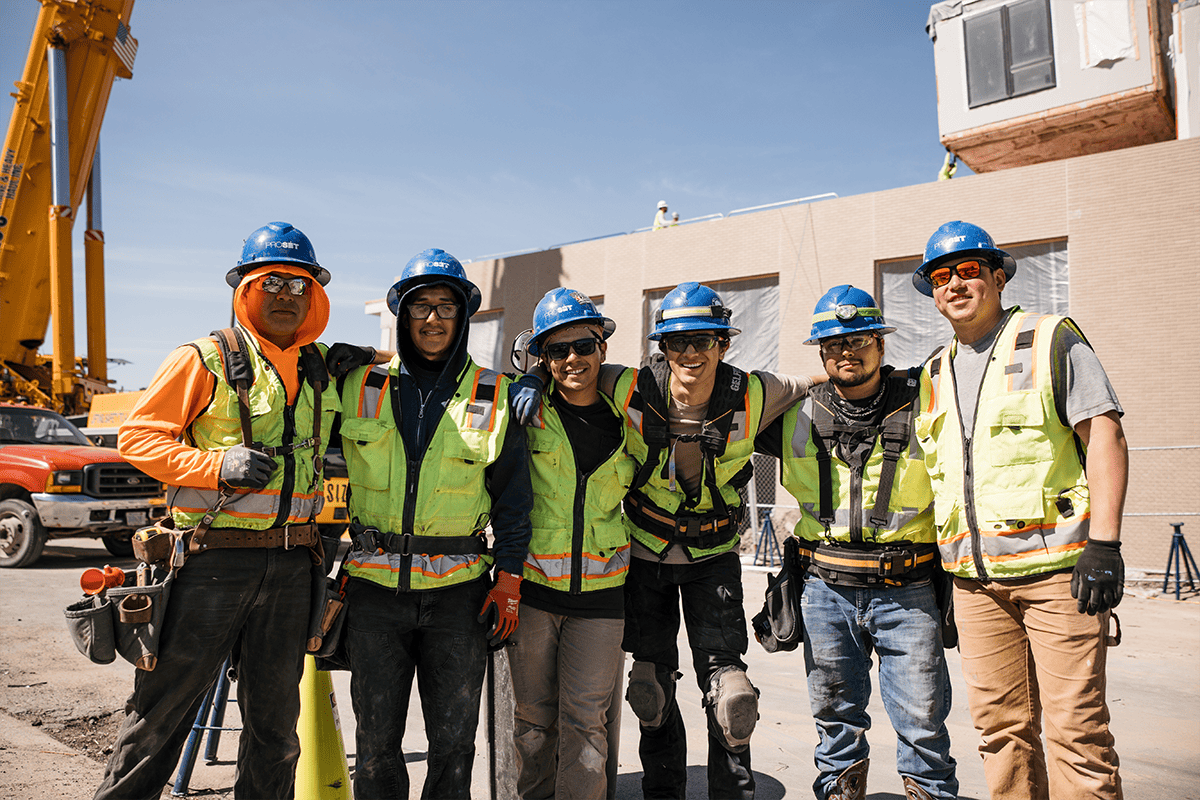
Photo by RISE Modular and Russell Heeter Photography
At that time, though, Mitchell didn’t have the crews in North Dakota to handle the project and proposed combining crews with Bridger. The idea was to create a specialty modular installation or set crew, which they did for that North Dakota Project. When that job wrapped up, the modular builder, Guerdon Enterprises, then hired Bridger’s and Mitchell’s company, which by then was officially ProSet, Inc., to work on their first Marriott Corporation project in Folsom, California, which was a Fairfield Inn. That project appears to have been a turning point for the industry. “In a lot of ways the industry took off at that point,” Bridger said. Until then, Bridger said, the consistent demand wasn’t quite there for the company’s services. It’s a specific niche of multifamily, hospitality, and assisted living. “At the time when we started this company, there was very little activity. There were very few projects anywhere in the country that were in that modular multifamily or hospitality space. There just weren’t very many manufacturers building that product yet,” he said
“So we were just maintaining one single crew going from one job to another, and to be honest, sometimes having some fairly big gaps in between our projects because there, again, weren’t that many projects out there,” he noted.
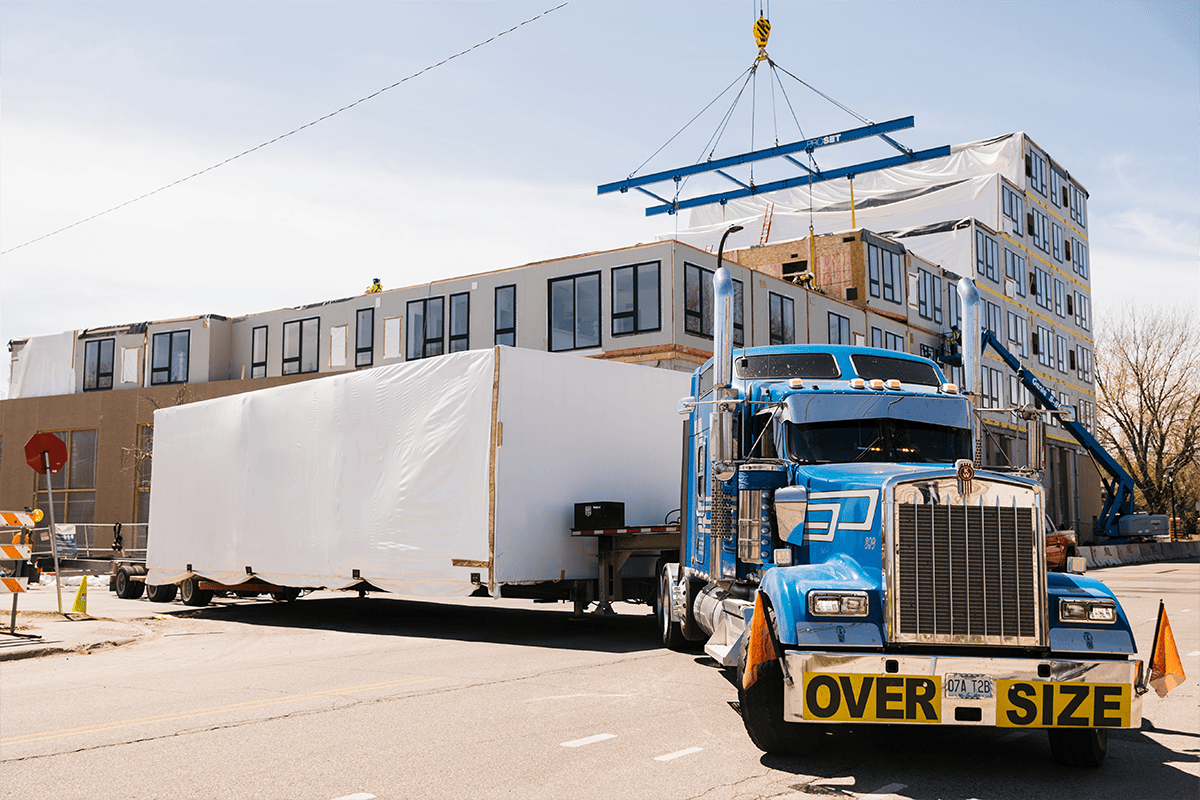
Photo by RISE Modular and Russell Heeter Photography
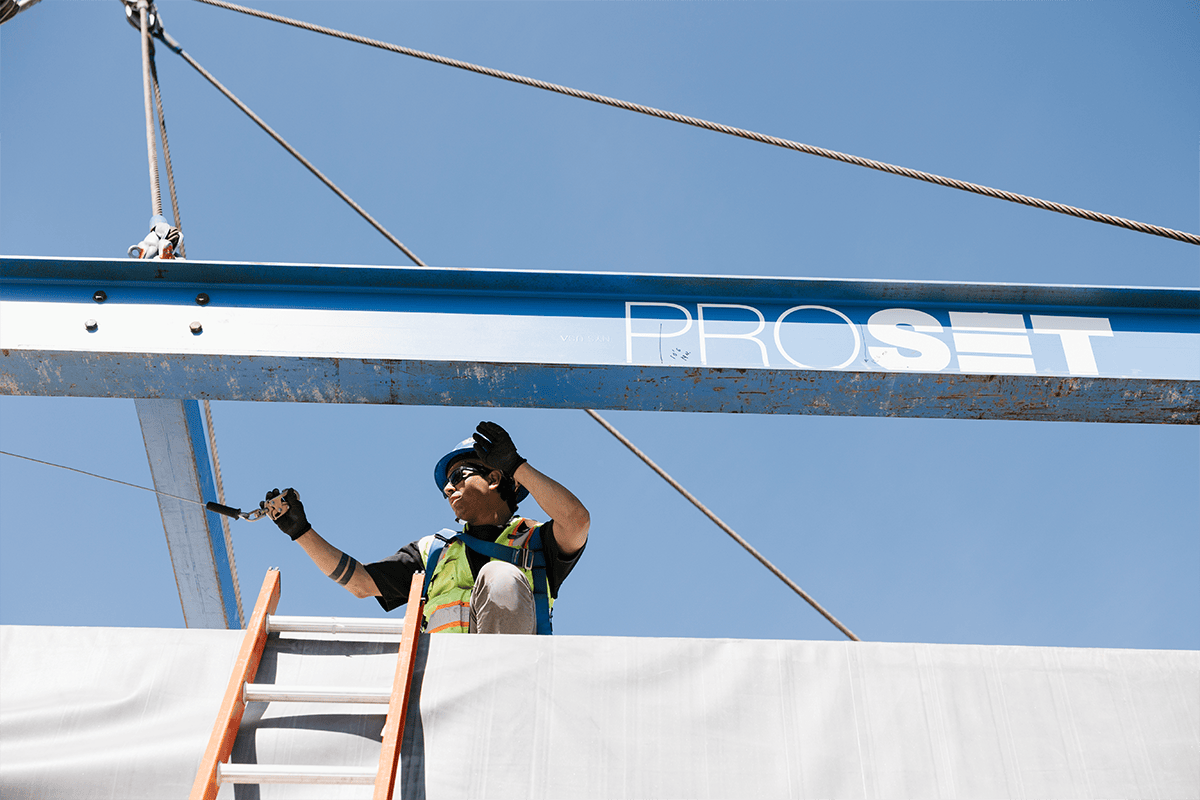
Photo by RISE Modular and Russell Heeter Photography
A Turning Point for Modular
The Fairfield Inn project for Marriott was the start of a new phase for the company, and for the commercial modular industry. “When a company like Marriott, the largest hospitality company in the world, says modular is a great way to build…it really delivered a lot of credibility to modular technology,” Bridger said. Since then, both the industry as a whole and ProSet have grown substantially, he said, and the company now has four full-time crews. “Today we’re setting for many more factories. In fact, in 2023 alone we’ll set for about 20 factories. So that just demonstrates where the growth is coming from and we see that continuing,” he noted. As an example, ProSet will install roughly 500 modular units this year for Rise Modular, a newer modular manufacturer in Minneapolis, Minnesota.
ProSet’s internal team is a major factor in the company’s continued success. Led by industry veteran and minority shareholder Chris Rimes, the company depends on traveling crews. Finding and retaining team leaders has been crucial and a building block for attracting complementary team members, he said. “Those of us who work in this industry today are going to look back years from now and say that we were part of a very significant change in how buildings get built in the United States,” Bridger said. “And so I think just by the nature of our being part of a young, dynamic industry, we are able to attract some really good talent, some forwardthinking people who are interested in being part of something exciting,” he noted.
A large part of the industry’s growth curve is due to the industry maturing and improving the product, so that a company like Marriott would become a client. And another key factor, Bridger said, is how well the key players work together in getting the projects built. The manufacturer, architect, engineer, general contractor, and developer all play crucial roles in a successful project, and it’s helpful for those professionals to have modular experience. It’s also productive when ProSet gets involved early in the project, he said.
Getting in Early Is Key
“It really helps to have experienced modular architect and engineering firms, particularly the structural engineer. And if the general contractor doesn’t have modular experience, it’s important that they have studied the process and have the right attitude about performing on a modular project,” Bridger noted. “If those stakeholders and those key players are brought together early and have a good depth of experience, that is likely going to result in a good project,” he said.
ProSet, Bridger noted, works on a variety of project types and of varying complexity, so coming in early in the process is always a benefit. single-family home with one or two modules doesn’t require much planning compared to a multi-family project. “Let’s look at a large-scale modular project where let’s say you have 100 modular units, which is kind of average for our projects. So instead of one modular box or two modular units in a single-family modular home, you’ve got maybe 100. And there’s a very specific order that those need to be installed. And so there’s going to be some pretty serious logistics planning with that process,” he said.
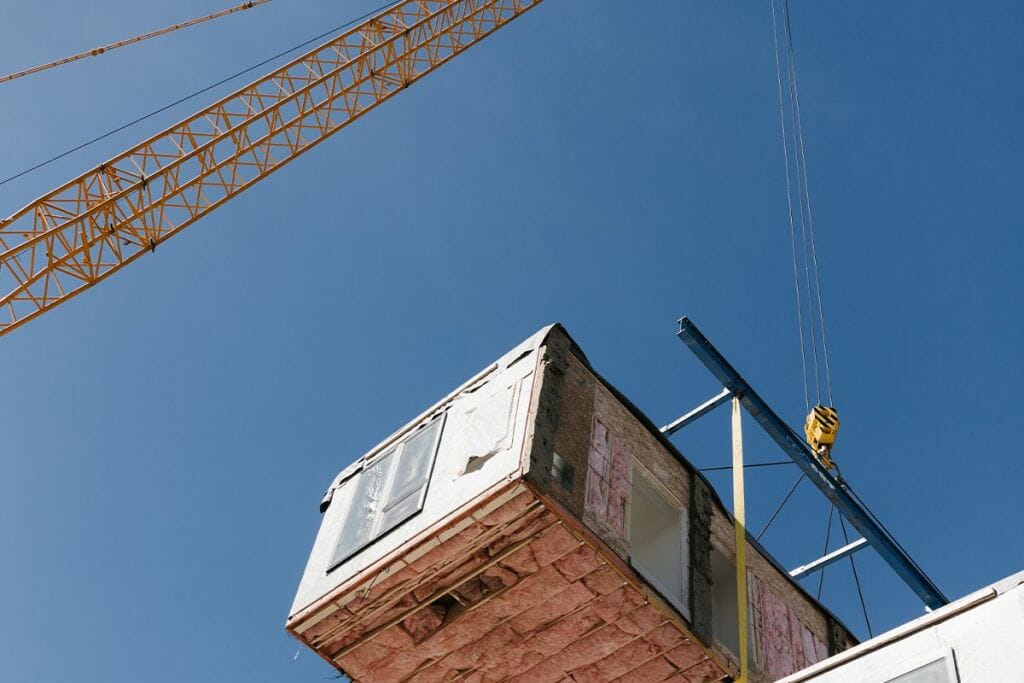
Photo by RISE Modular and Russell Heeter Photography
A big part of the planning involves determining the order of installation on the foundation at the job site, which means directing the order of manufacturing the modules at the factory, and also the order of transporting the modules to the job site or storage yard for the modules so that the erection process goes as efficiently as possible. For that reason, Bridger said, ProSet can have more impact when they’re brought in early on a project. “There’s a symphony that can be coordinated very well if we’re involved early,” he said. “We have less impact the farther into the project or later into the project we get engaged."
A Bright Future for Modular Construction
The challenges facing conventional building and the housing market are well known. A shortage of construction labor seems to be intractable, as is housing affordability in many markets across the country. Modular construction offers an alternative approach that addresses the well-known, decades-old problems of conventional construction. “Modular can really provide a lot of predictability on schedule and cost, but also can, in most cases, reduce construction durations considerably,” Bridger said. “And depending on where that particular project is, it can probably also save some money on construction costs,” he added.
Those attributes can be a major benefit in creating attainable housing all across the country, Bridger said. “Modular is not a silver bullet, but it certainly provides the opportunity to move the needle where conventional construction is just not able to keep up and certainly not able to catch up in terms of the number of modular housing units that we need across the country,” he noted. “So long story short, the industry has, I think, a very, very bright future and much as it’s grown in the last few years, I think we’ll see a considerably faster pace of growth in the modular commercial industry in years to come,” he added.
About the Author: Steve Hansen is a Colorado-based writer with a focus on the built environment—architecture, construction, renewable energy, and transportation. He can be reached on LinkedIn.
More from Modular Advantage
Oregon’s Prevailing Wage Proposal: A Wake-Up Call for Modular Construction
In early February, 2024, the Massachusetts Board of Building Regulations and Standards (BBRS) released its proposed 10th Edition building codes. This draft included several amendments targeting modular construction that would have created an extremely difficult environment for the entire modular industry and could have eliminated the industry entirely in the state.
Behind the Design of Bethany Senior Terraces, NYC’s First Modular Passive House Senior Housing Project
As more developers seek to meet new regulations for energy efficiency, the team at Murray Engineering has set a new record. With the Bethany Senior Terraces project, Murray Engineering has helped to develop NYC’s first modular structure that fully encompasses passive house principles — introducing a new era of energy efficiency in the energy-conscious city that never sleeps.
How LAMOD is Using Modular to Address Inefficiency, Sustainability, and the Future of Construction
As developers, designers, and contractors seek to understand the evolving needs of the modular industry, no one is as well-versed in the benefits of going modular as Mārcis Kreičmanis. As the co-founder and CBDO of LAMOD in Riga, Latvia, Mārcis has made it his ultimate goal to address the inefficiencies of traditional construction.
From Furniture Builder to ‘Activist Architect’: Stuart Emmons’ Unique Journey
Stuart Emmons was fascinated by buildings at a young age. He remembers building sand cities with his brother during trips to the Jersey shore. His father gave him his first drawing table at the age of ten. Today, he is an experienced architect who received his FAIA in June 2025. The road he took is unique, to say the least.
Forge Craft Architecture + Design: Codes, Contracts, and Intellectual Property
Founding Principal and Director of Modular Practice for Forge Craft Architecture + Design, Rommel Sulit, discusses the implications of codes, contracts, and intellectual property on
modular construction.
Eisa Lee, the “Bilingual” Architect
Now as the founder of XL
Architecture and Modular Design in Ontario, Canada, she applies not just her education as a traditional architect but an entire holistic view on modular design. It’s this expansive view that guides her work on being a true partner that bridges the gap between architects and modular factories as they collaborate on the design process.
Tamarack Grove Engineering: Designing for the Modular Sector
The role of a structural engineer is crucial to the success of a modular project, from initial analysis to construction administration. Tamarack Grove offers structural engineering services — project analysis, plan creation, design creation, and construction administration — for commercial, manufacturing, facilities, public services, and modular. Modular is only one market sector the company serves but it is an increasingly popular one.
Engineer Masters the Art of Listening to His Customers
Since founding Modular Structural Consultants, LLC. in 2014, Yurianto has established a steady following of modular and container-based construction clients, primarily manufacturers. His services often include providing engineering calculations, reviewing drawings, and engineering certification
Inside College Road: Engineering the Modules of One of the World’s Tallest Modular Buildings
College Road is a groundbreaking modular residential development in East Croydon, South London by offsite developer and contractor, Tide, its modular company Vision Volumetric (VV), and engineered by MJH Structural Engineers.
Design for Flow: The Overlooked Power of DfMA in Modular Construction
Unlocking higher throughput, lower costs, and fewer redesigns by aligning Lean production flow with design for manufacturing and assembly.