What the Inflation Reduction Act Means for Modular Builders
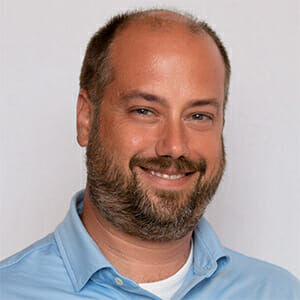
John Tienken is the regional sales manager for vertical markets at Mitsubishi Electric Trane HVAC US
Signed into law last August, the Inflation Reduction Act (IRA) is the country’s largest climate investment initiative. Hundreds of millions of dollars will be funneled into rebates and tax credits for greener and more energy-efficient building upgrades.
With space heating, air conditioning and water heating accounting for significant percentages of a building’s energy consumption, modular builders who want to take advantage of the IRA incentives should look closely at their HVAC and water heater technology and explore more energy-efficient options.
How Modular Builders Can Take Advantage of the IRA
Depending on the types of buildings they develop, modular builders can take advantage of IRA initiatives including:
- The updated 179D commercial buildings energy-efficiency tax deduction, which now offers base tax deductions to commercial building owners and designers of buildings meeting certain energy-efficiency standards.
Using a sliding scale, tax deduction levels are being increased to $.50 per square foot for energy savings of 25% and up to $1 per square foot for energy savings of 50% or greater. If a building meets certain prevailing wage requirements, bonus deductions are also available. These are determined based on a sliding scale of $2.50 per square foot for energy savings of 25% and up to $5 per square foot of energy savings of 50% or greater.
- The 45L investment tax credit (ITC), targeted towards single-family and multifamily building contractors who meet specified energy-efficiency requirements.
- For single-family residences, contractors can receive $2,500 for homes that meet ENERGY STAR standards and $5,000 for zero energy ready homes.
- For multifamily dwellings, contractors can receive $500 per unit that meets ENERGY STAR standards and $1,000 per unit for zero energy ready units. Modular builders meeting certain labor requirements can increase that amount.
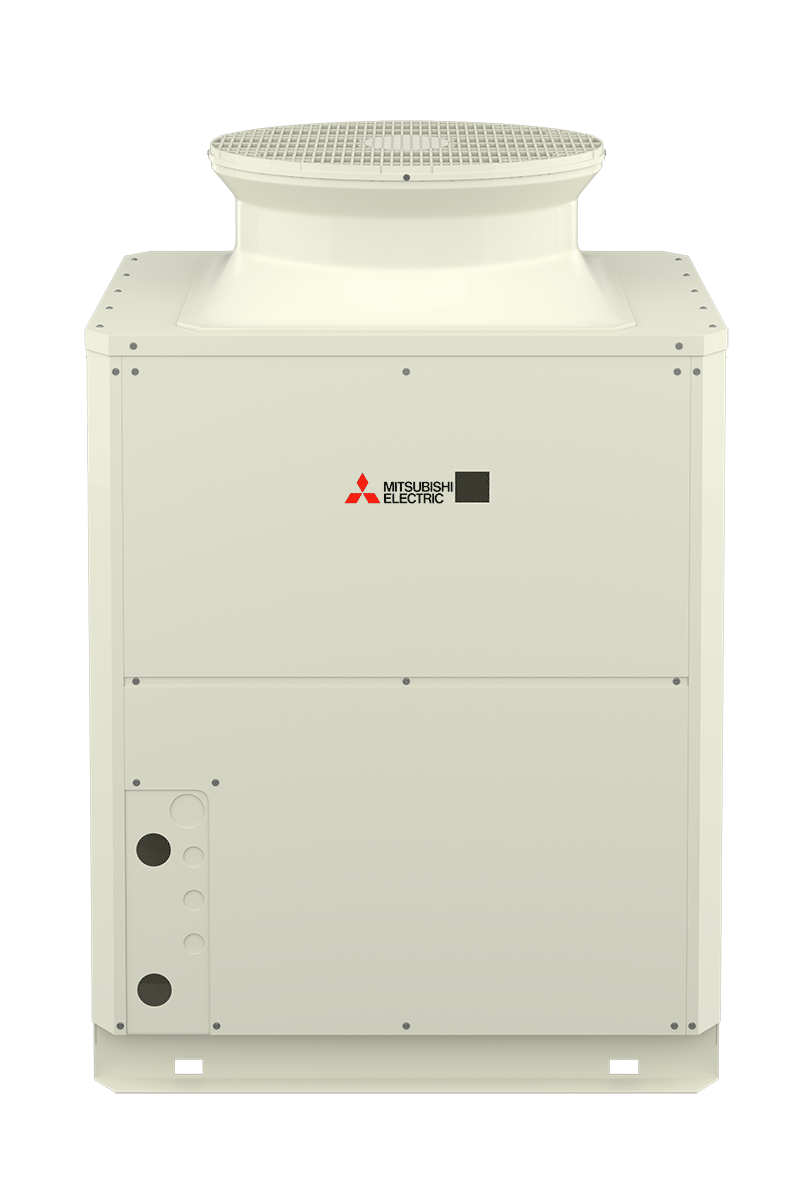
Issa Nesheiwat and Apex Modular Solutions participate in the “Tiny Home Experience” Event with Ulster Saving Bank.
Energy efficiency is clearly key to qualifying for 179D tax deductions and 45L ITCs. A joint 2022 report from the National Renewable Energy Laboratory, Oregon State University, Momentum Innovation Group and the U.S. Department of Energy laid out five key strategies for how modular builders can improve energy efficiency.
Modular builders can reach peak efficiency by focusing on envelope thermal control, envelope infiltration control, mechanical, electrical and plumbing (MEP) systems, smart controls and solar-plus-storage services.
HVAC & Water Heating Technology Plays a Crucial Energy-Usage Role
Next, we explore energy-efficient MEP system technology, such as HVAC and water heaters, and smart controls available for modular builders.
Space heating, air conditioning and water heating comprise the most significant percentages of buildings’ energy consumption. Seventy percent of energy consumption in single-family and multifamily residential buildings goes toward space heating, air conditioning and water heating. In multifamily buildings, domestic hot water accounts for roughly 25% of annual energy usage.
Natural gas continues to play a big role in powering these systems, but electric solutions are becoming more popular. The U.S. Energy Information Administration reports that 31% of commercial buildings use electricity as their primary space-heating source, while 35% of single-family and multifamily homes use electricity for space-heating.
To help reduce reliance on fossil fuels, electrification initiatives in the United States are starting to heat up. For instance, New York is the first state to ban natural gas and other fossil fuels in many new buildings. The state will prohibit gas-powered stoves, furnaces and propane heating and encourage climate-friendly, all-electric heat pumps, stoves and ovens in new structures less than seven stories by 2026 and for taller buildings by 2029. Washington and California have rules restricting the use of natural gas in commercial buildings, while several cities have similar rules – for new commercial and residential construction. Others are expected to follow suit.
The push for electrification extends beyond new construction. For instance, the Department of Energy’s Building Technologies Office in 2022 announced the Home Electrification Prize to fund innovative solutions to retrofit homes to eliminate using fossil fuels and accelerate electrification, including the installation of energy-efficient heat pumps.
A popular conventional electric system used by many modular builders is a relatively inexpensive packaged terminal air conditioner (PTAC). However, PTACs are no longer the most energy-efficient option as they are usually fixed speed, constantly cycle on and off to reach a desired set point and require 30 to 40-amp electrical strip circuits.
Newer tech, like all-electric heat pumps, use more energy-efficient compressors that greatly reduce the amount of energy needed to keep a space comfortable. With features like zoned heating and cooling and smart controls, heat pumps can make a world of difference in a modular building’s energy consumption.
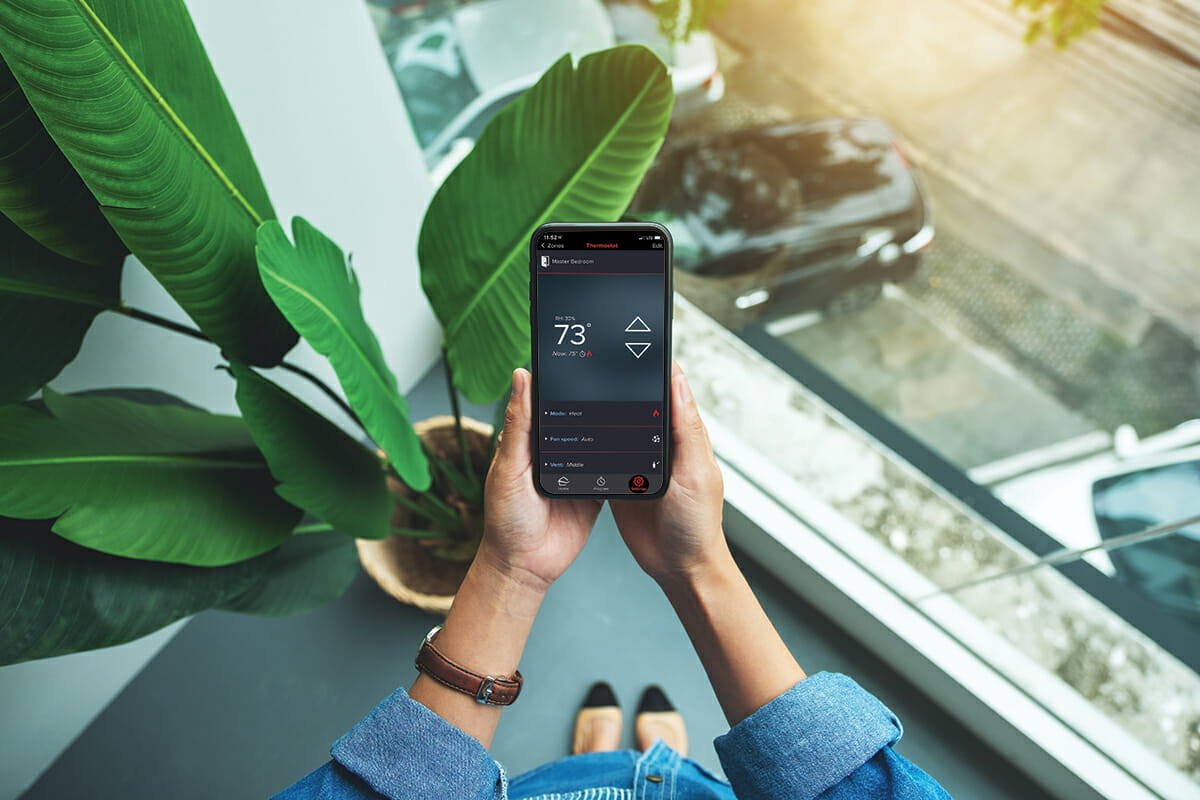
Smart controls allow users to monitor and control their HVAC systems remotely, through a building control panel, wireless controllers, or smartphones.
Why Heat Pumps Are Energy Efficient
Heat pumps are somewhat of a misnomer since they heat and air-condition spaces efficiently. For warmth, the outdoor heat pump absorbs heat energy from the outside air and transfers it to the inside unit via the refrigerant. The refrigerant is compressed, increasing its temperature significantly when it reaches the indoor coil. A fan blows air over the heated coil to deliver warm air to the room. To provide cooling, the process reverses.
Commercial and multifamily modular buildings are implementing all-electric heat pump technology called Variable Refrigerant Flow (VRF), the fastest-growing segment of the commercial HVAC industry. VRF compressors eliminate the wasteful start-and-stop cycle of conventional systems. The compressor motor varies its speed, regulating the amount of refrigerant delivered to the indoor units to match demand.
Through continuous operation, indoor unit fans help maintain an even, constant flow of filtered and conditioned air. VRF technology also divides a building into zones customized for comfort and energy efficiency, allowing the air to be easily turned off in certain spaces when unoccupied.
The compressors in single-family modular heat pumps work similarly.
For domestic hot water, multifamily modular builders should look at tech like electric heat pump water heaters since they offer energy savings of up to 70% compared to electric-resistance water heaters. Consider options with compressors that modulate refrigerant flow and heating capacity to match loads, thus improving energy efficiency.
How Smart Controls Improve Energy Efficiency
To better monitor and manage the energy usage of HVAC systems, modular builders should consider integrating energy-efficient smart thermostat controls in their buildings. Doing so makes it easier for building staff and tenants to maintain comfort settings in high-traffic spaces while conserving energy in unused spaces.
Smart controls allow users to monitor and control their HVAC systems remotely, through a building control panel, wireless controllers, or smartphones. Smart controls are even integrable with Amazon Alexa or Google Home smart home devices for a seamless, unified experience
Energy-Efficient Building Systems Are the Future
Energy-efficient buildings are now table stakes for savvy modular builders looking to attract investors, buyers and tenants. Energy efficiency means end-user cost savings, greener buildings, and IRA tax incentives for builders.
Savvy modular builders across commercial, multifamily, and single-family sectors who revamp their HVAC and water heating systems with more energy-efficient technology like heat pumps, zoning and smart controls will be well-positioned for a sustainable future.
More from Modular Advantage
AI, Faster Sets, and Automation: The Future of Modular is at World of Modular
While the modular building industry has long known that it can be an effective solution to increase affordable housing, the word is slowly spreading to more mainstream audiences. Three presentations at this year’s World of Modular in Las Vegas hope to provide insight and direction for those seeking a real solution to the crisis.
An Insider’s Guide to the 2025 World of Modular
The Modular Building Institute is bringing its global World of Modular (WOM) event back to Las Vegas, and with it comes some of the industry’s best opportunities for networking, business development, and education. Over the course of the conference’s four days, there will be numerous opportunities for attendees to connect, learn, and leverage event resources to get the most out of the conference.
Affordable Housing Now: The Industry’s Best Bring New Solutions to World of Modular
While the modular building industry has long known that it can be an effective solution to increase affordable housing, the word is slowly spreading to more mainstream audiences. Three presentations at this year’s World of Modular in Las Vegas hope to provide insight and direction for those seeking a real solution to the crisis.
Opportunities for Innovation in Modular Offsite Construction
Modular Offsite Construction has already shattered the myth that it only produces uninspired, box-like designs. Architectural innovations in module geometry, configurations, materials, and products make it possible to create visually stunning buildings without sacrificing functionality or efficiency.
Safe Modular Construction with Aerofilm Air Caster Transport
In collaboration with Aerofilm Systems, Heijmans developed innovative skids using air caster technology for moving modules easily and safely. These pallets are equipped with an auto-flow system, making operation extremely simple.
Miles, Modules, and Memes: Building a Modular Network One Flight at a Time
At the end of the day, social media is just another tool for building connections, and like any other tool, needs to be used skillfully to work properly. Use social media thoughtfully, and it will open doors to real opportunities and relationships you didn’t even see coming.
Falcon Structures: Thinking Inside the Box
Some of Falcon’s latest projects include creating container solutions for New York’s Central Park and an East Coast professional baseball team. More and more, Falcon is shipping out container bathrooms and locker rooms to improve traditionally difficult work environments, like those in oil and gas or construction.
UrbanBloc—From Passion to Industry Leader
UrbanBloc specializes in three main categories or markets – what they call “Phase 0” projects, amenities, and urban infill. Clients are often attracted to shipping containers because from a real estate perspective they are considered an asset. Having the flexibility to move and transport these assets allows owners to respond to different circumstances in a fluid manner that they can’t get with standard construction.
The Hospitality Game-Changer
“Hospitality is about more than just providing a service – it’s about delivering an experience,” says Anthony Halsch, CEO of ROXBOX. “And that’s where containers thrive. They allow us to create spaces that are unique, efficient, and sustainable.”
Container Conversions Counts on Simplicity to Provide Critical Solutions
Container Conversions has fabricated and developed thousands of containers for varied projects, including rental refrigeration options, offices, kitchens, temporary workplace housing, and mobile health clinics.